In view of the potential for global expansion, the Montex machinery range is constantly being upgraded to meet evolving customer needs for greater automation, ease of operation and, of course, energy optimisation and waste reduction
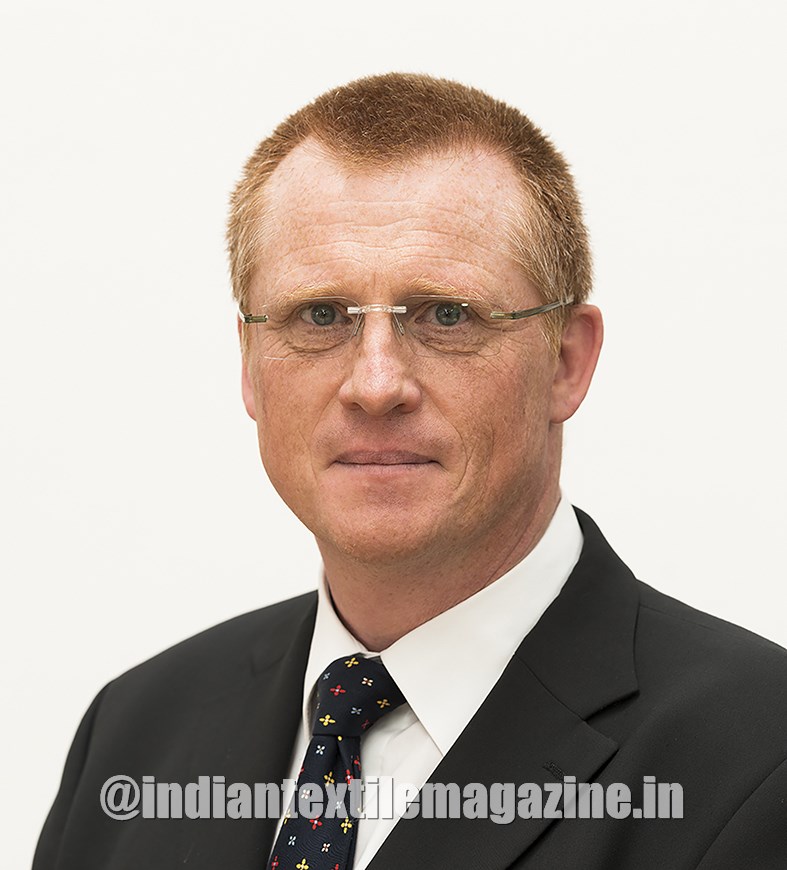
Monforts is a name that needs no introduction to anyone who is familiar with the world of textile machinery. One of the leading manufacturers of textile finishing machinery, the company has made significant inroads into the Indian market as well. In an exclusive chat, Hans Wroblowski, Head of Denim and Area Sales Director SEA of the company, mentions that though impacted by the pandemic situation, the worldwide demand for new machines remained healthy and significant investments are still being made. Elaborating about the key global markets which have been good for the company in recent times, he states: “We have a strong presence in all of the major markets for textile manufacturing such as Turkey, Pakistan, Bangladesh and India. Europe also remains a key market for us, notably for lines to produce technical and home textiles.”
Advantage Monforts
Elaborating on the strengths of Monforts and how the company’s textile machines help customers increase their efficiency, quality and profitability, Wroblowski points out that the Montex machinery range is constantly being upgraded to meet evolving customer needs for greater automation, ease of operation and, of course, energy optimisation and waste reduction. “With the latest Montex stenters for processes such as drying, stretching, heat-setting and coating, overall energy savings of up to 40% can now be achieved compared to a conventional stenter. The energy-optimised stenter offers different features to help save energy, including better insulation of the treatment chambers.”
“It also leads to a reduction of cold air intake at the inlet and outlet of the stenter chambers, new optimised gas burners and the use of preheated combustion air in combination with the MonforClean™ integrated heat recovery module,” he adds. “The waste heat from the drying process is used to pre-heat the drying air, resulting in a radical reduction in the conventional heat supply required compared to gas and thermal oil heating. The modular system for heat recovery can also be extended for exhaust air cleaning and odour elimination,” he further explains. Speaking about the new technologies introduced by the company in the recent past, Wroblowski says that Monforts partners with technical textiles manufacturers for value-added finishing of many products using the latest MontexCoat® multi-head coating system.
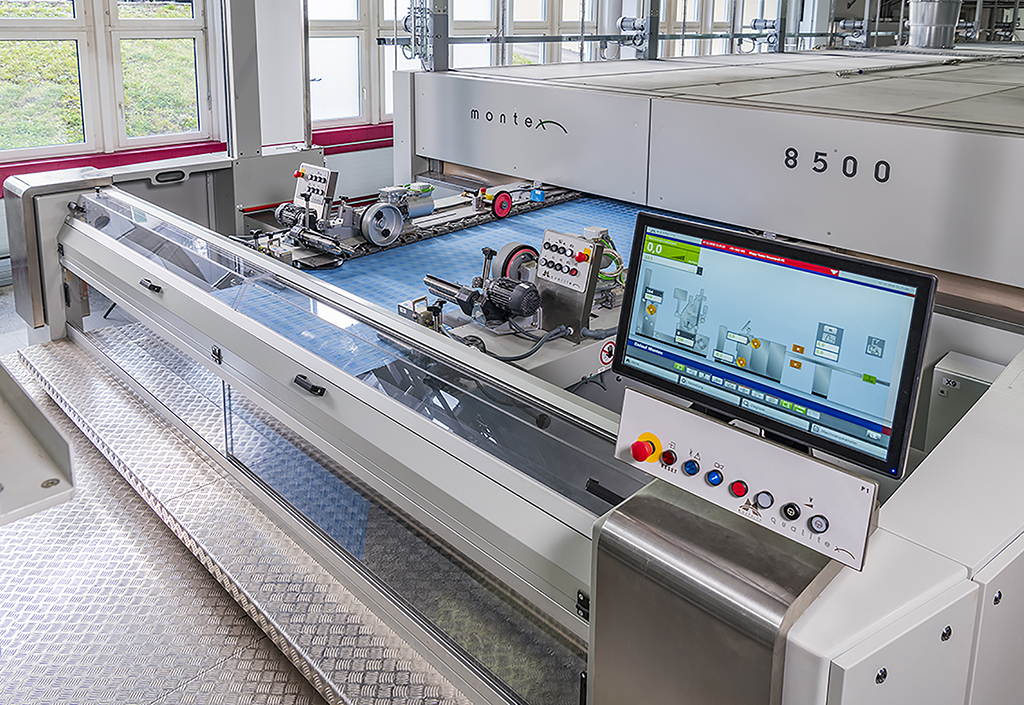
“Coated technical textiles are extremely diverse in their end-use applications and products already manufactured by Monforts’ customers range from substrates for digitally printed soft signage to those for high-performance composites. Others include airbags, automotive interior components, flame-retardant barriers, filter media, geo textiles, heavy-duty membranes, mattresses and even base liners for sensor-packed dye sensitive solar cells,” he says. According to him all of these very different materials require expert coating and finishing for maximum efficiency using Monforts’ technologies which provide the ultimate in flexibility and the ability to switch quickly from one fabric run to the next without compromising on the economical use of energy or raw materials.
“Since we acquired the technology that our coating units are based on in 2015, we have made a lot of refinements. All of these developments are reflected in higher coating accuracy and the resulting quality of the treated fabrics. At the same time, our latest multi-functional coating heads offer an unprecedented range of options with a wide range of modules available,” he adds. “Globally, technical textiles account for more than one-third of all textile consumption and currently India accounts for only a small proportion, but producers are investing in this sector and projections are that it will grow substantially in the coming years,” Wroblowski observes.
Overcoming Challenges
The entire textile industry has been passing through a tough phase for over two years now due to the pandemic situation. However, with the thrust on vaccination, things seem to be looking up now and there is widespread hope that the worst is behind us. How did Monforts use this period for improving the organisation and its objectives? What are the valuable lessons that it learnt from the pandemic? Responding to these questions, Wroblowski comments, “There have been noticeable changes in various textile sectors in terms of demand. There has, for instance, been a greater emphasis on leisure wear because many people have been working from home, with less demand for formal office wear.”
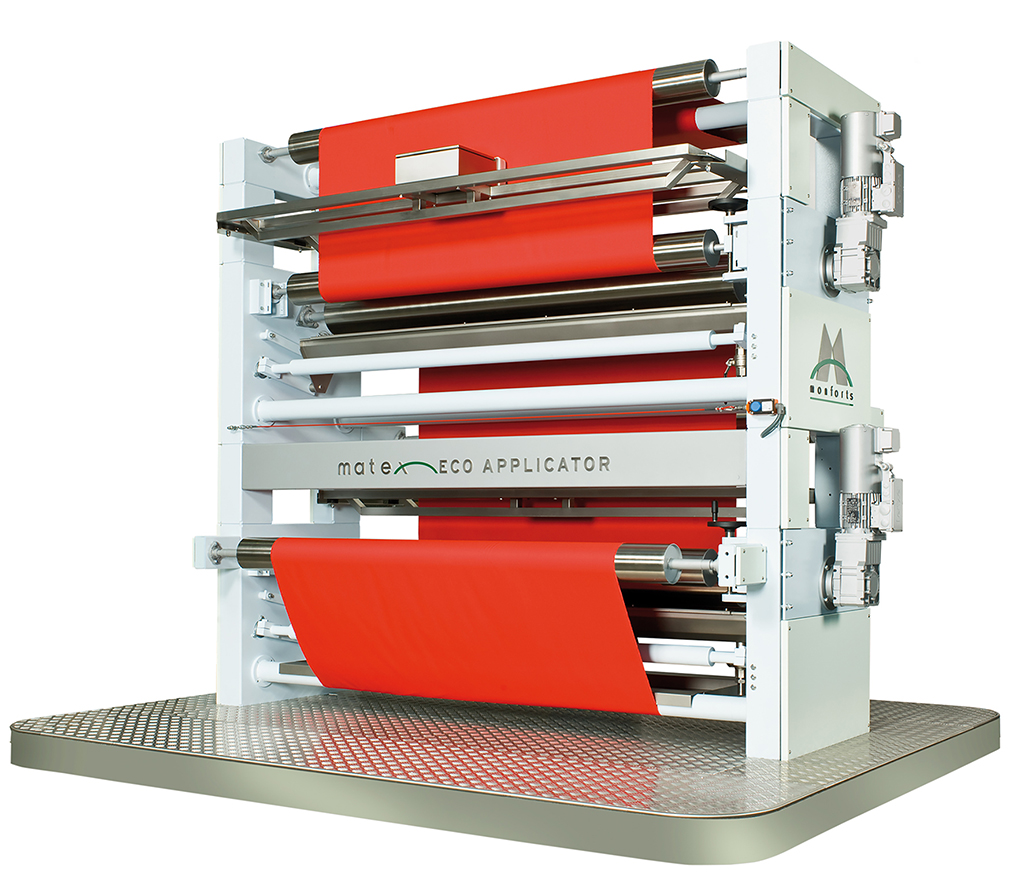
“For the same reason, the market for home textiles was very successful in 2021. Online shopping has benefited at the expense of the high street as a result of this too. On the positive side from our perspective as a technology supplier, we have always been able to meet customers’ demands for fast and reliable service thanks to our well-established and enhanced remote services as well as providing accurate and helpful onsite support with our local representative teams, such as with A.T.E. in India, for example. The demand for machinery for special textiles with added value has also risen in the past 18 months. Supply chain difficulties have demanded greater flexibility and happily led to a greater mutual understanding and trust between all parties, including with our customers,” he reveals.
Automation Initiatives
Automation and Industry 4.0 are no more optional. They are the fundamentals for an efficient manufacturing system. Giving an insight on Monfort’s initiatives on this front, Wroblowski remarks, “The latest Qualitex® visualisation software offers the operator reliability and ease of operation with its full HD monitor and slider function, dashboard function with individual adaptation to the operating states and faster access to the comprehensive recipe data management.” Adding further, he points out that the Monforts WebUI application provides live streaming of machine data and actual and historical alarms, as well as network camera feeds. Since the software is based on HTML 5 it can be used on any kind of mobile device.
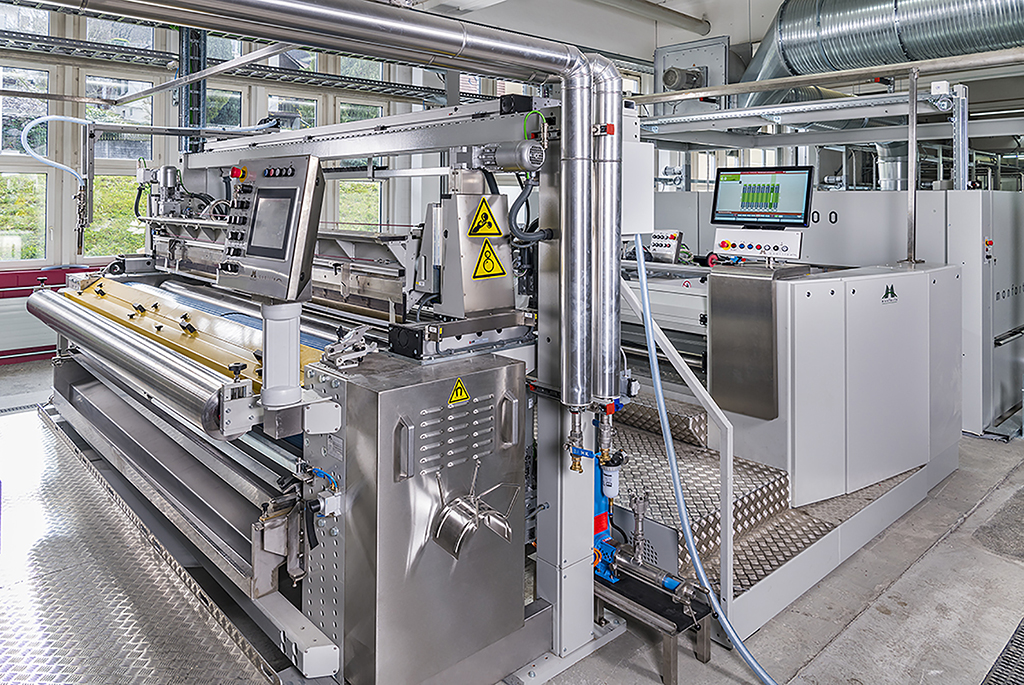
With the Monformatic™ control system, the exact maintenance of the dwell time in combined treatment processes (drying and heat-setting) is monitored. When the heat-setting point is reached the fan speed is automatically adjusted, keeping energy consumption fully under control. The Q-soft database is a central control system for production planning and documentation with a central interface. All process data can be stored in a standardised database where all set points and actual values are filed with read and write access for set points. Several machines can be connected simultaneously.
In combination with the Q-soft database, the customer can use additional systems including:
• Monforlogic® for the planning and management of batches and parameters or recipes with scheduling for up to nine machines.
• Operating Cost Overview for enhanced analysis of the machine processes by aggregating, analysing and displaying operational and process data, continuous monitoring and recording of meter data.
• Maintenance Manager which generates machine alarms at regular intervals to remind the operator to carry out necessary working steps.
Being Sustainable
Sustainable textile manufacturing has gained more importance in the post-pandemic world. Brands and retailers have set stringent sustainability goals and standards for their suppliers. Explaining how Monforts contributes towards its customers achieving these objectives, Wroblowski says: “The emphasis, more than ever now, is on sustainable production and achieving savings in energy, water and raw materials. New customers are showing a keen interest in heat recovery and energy optimisation achievable on the latest Montex stenters. In addition to the resource savings with our lines, the Monforts Eco Applicator® offers further potential for sustainably achieving perfect finishes via a precise direct application system.”
“This is as an alternative to conventional padding where fabrics are immersed in a bath of the required finishing chemicals. The Monforts Eco Applicator can significantly further reduce the energy and water required for achieving perfect finishes via a precise direct application system. Finishes can be applied on just one side of the fabric, or both, and even separately on each side, and sealed in place via different heating zones in the stenter. This allows endless differentiation possibilities,” he informs. Finally, Wroblowski is optimistic that the situation caused by the pandemic is on the mend and things should be back on track in the near future. “We expect a stable market for Monforts in 2022 and are hopeful that many of the obstacles caused by the pandemic in 2020 and 2021 will begin to recede,” he says on a parting note.