The Albstadt-based circular knitting machine manufacturer Mayer & Cie. (MCT) generated sales of around EUR 105 million in 2017, on a level with the previous year. The family-owned company also sold roughly the same number of machines as in 2016. The reason for the result, which fell short of the company’s expectations, was a complex in-house ERP-system changeover.
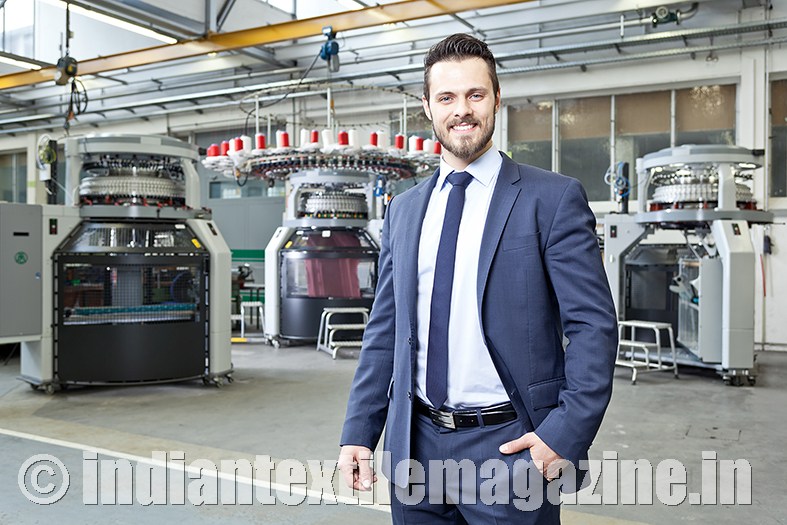
For the current year, Mayer & Cie.’s target is a significant increase in group sales once more. Preparations are also scheduled to start this year for the integration of a sister company and its products.
2017 results: Satisfactory with reservations
The Mayer Group – the Albstadt headquarters and the Czech and Chinese subsidiaries – generated sales totalling around EUR 105 million, which was almost identical to the 2016 result. That this figure fell short of the company’s expectations was due to neither the market situation nor the order position, both of which continue to be positive. It was the result of an ERP system changeover that went into operation in the summer of 2017 after several years of preparation. That led to problems in the production flow, with almost completed machines could not be delivered to the customers because parts were not available at the required time.
“We are dozens of machines behindhand,” says Benjamin Mayer, Managing Director of Mayer & Cie. “That naturally has an effect on the result, which would otherwise have been significantly better. We did, after all, have the capacities and the orders. Fortunately, system changeovers of this kind are not a daily occurrence, and we are confident that we have now largely put the initial difficulties behind us. We are sure that we will be able to work better and more efficiently than with our old system.”
In addition to its ERP-system update, Mayer & Cie. invested millions last year in other modernisation projects, especially at the headquarters location in Albstadt. The company constantly and regularly upgrades its machinery, last year including, for example, 10 new production machines. Work on the automated storage system has also progressed and is nearing completion.
Outlook for 2018 continues to be positive
Benjamin Mayer has now set himself last year’s EUR 110 million sales target for 2018 and is confident that it can be achieved. “2018,” he says, “has got off to a good start. Our order intake is stable and we expect to be back in calmer waters after our system changeover and to be able slowly but surely to work off our backlog of machines.”
Mayer & Cie. is therefore able to tackle new challenges in 2018. One of them is braiding machines, a successful product of the US sister company Mayer Industries in Orangeburg, South Carolina. Founded in the early 1970s as a Mayer & Cie. subsidiary and a circular knitting machine production site, the company is to be wound up in the medium term.
Mayer Industries’ products are braiding machines for the manufacture of hose tubing. They are to be made from about 2019 in Albstadt-Tailfingen. Preparations are under way for integrating this new product. The necessary infrastructure, above all the personnel capacities and production line, is to be in place next year.
“For us the integration of this technically related product is a good opportunity to develop an additional mainstay that is independent of our core business,” Benjamin Mayer says, explaining the decision. “We have repeatedly opted for diversification in the past decades and had good experiences with it.”
Mayer & Cie. spinitsystems receives IKU Award
The Albstadt-based circular knitting machine manufacturer Mayer & Cie. has received an IKU Award. The SME won a Climate and Environment Innovation Prize (IKU) for its spinitsystems spinning and knitting technology.
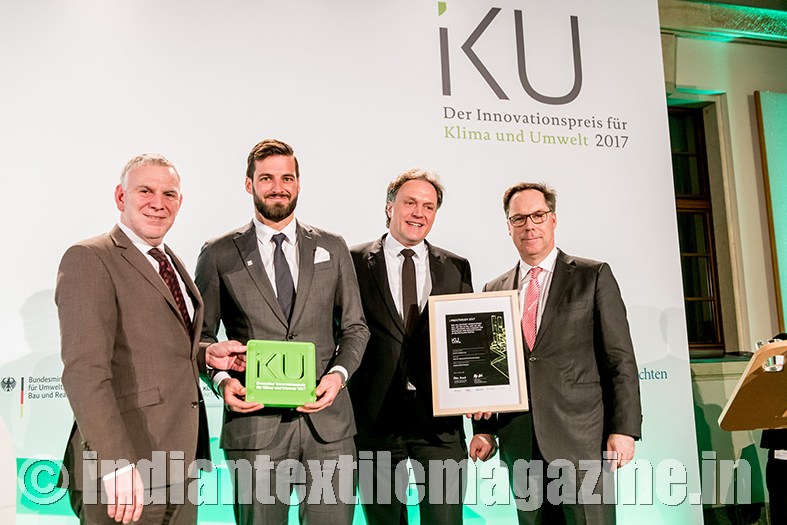
The Federal Environment Ministry (BMUB) and the Federation of German Industries (BDI) Award IKU prizes every other year for innovations “that mark new departures in climate and environmental protection”. The IKU jury felt that spinitsystems did just that. By combining spinning and knitting in one machine, it saves energy, resources, space and time in the production of Single Jersey fabrics.
“We are the first manufacturer to have dared to merge these two processes that have previously been separate both technically and ideologically,” says Michael A. Tuschak, in charge of spinitsystems marketing and sales. “We are delighted that the staying power required to see an innovation of this kind through has been rewarded with this prize.”
Less CO2, less energy, fewer resources
Normally, yarn is processed into a textile fabric on the circular knitting machines of Mayer & Cie. The yarn comes from a spinning mill, where it is manufactured in a complex and energy-intensive process. The new Mayer & Cie. spinning and knitting machine, in contrast, does not wait for the finished yarn to arrive from the spinning mill; it uses roving and is thereby able to combine in one machine, the Spinit 3.0 E, the previously strictly separate processes of spinning and knitting. Several other machines are no longer required, reducing the space required by about a third.
The process takes less time, reducing the amount of energy required to about two-thirds of what the conventional manufacturing process uses, with a positive effect on the carbon dioxide balance. The spinning and knitting machine also helps to save valuable cotton. Leftover roving on the spools is not waste; it can be sent straight back to the spinning mill.
These were the points that the IKU jury specially mentioned in its appraisal. The organisers were also impressed by the market potential and the number of machines envisaged over a five-year period.
The jury further felt that the 30 active spinitsystems patents and the long development time testified to the entrepreneurial performance that lay behind this innovation.
Sebastian Mayer, Mayer & Cie.’s director in charge of corporate development, is particularly proud of this achievement. “In combining the spinning and knitting processes we have created an interface that did not previously exist. Nobody other than us is conversant with it yet, so that, in addition to the technological lead, we have established a valuable knowledge lead.”
Along with the Award, the prize-winners in the five IKU categories each receive EUR 25,000 in cash to support their climate and environmental activities. In selecting the prize-winners, the IKU jury relied on the recommendations of the Fraunhofer Institute for Systems and Innovation Research (ISI), which checked the applications in detail and in some cases called on the applicants to submit further, in-depth information.