In a rapidly evolving world in which logistics will play a decisive role, the 60 years of experience behind Salmoiraghi will be useful to project the company into the future with ideas, production capabilities and openness to continuous innovation
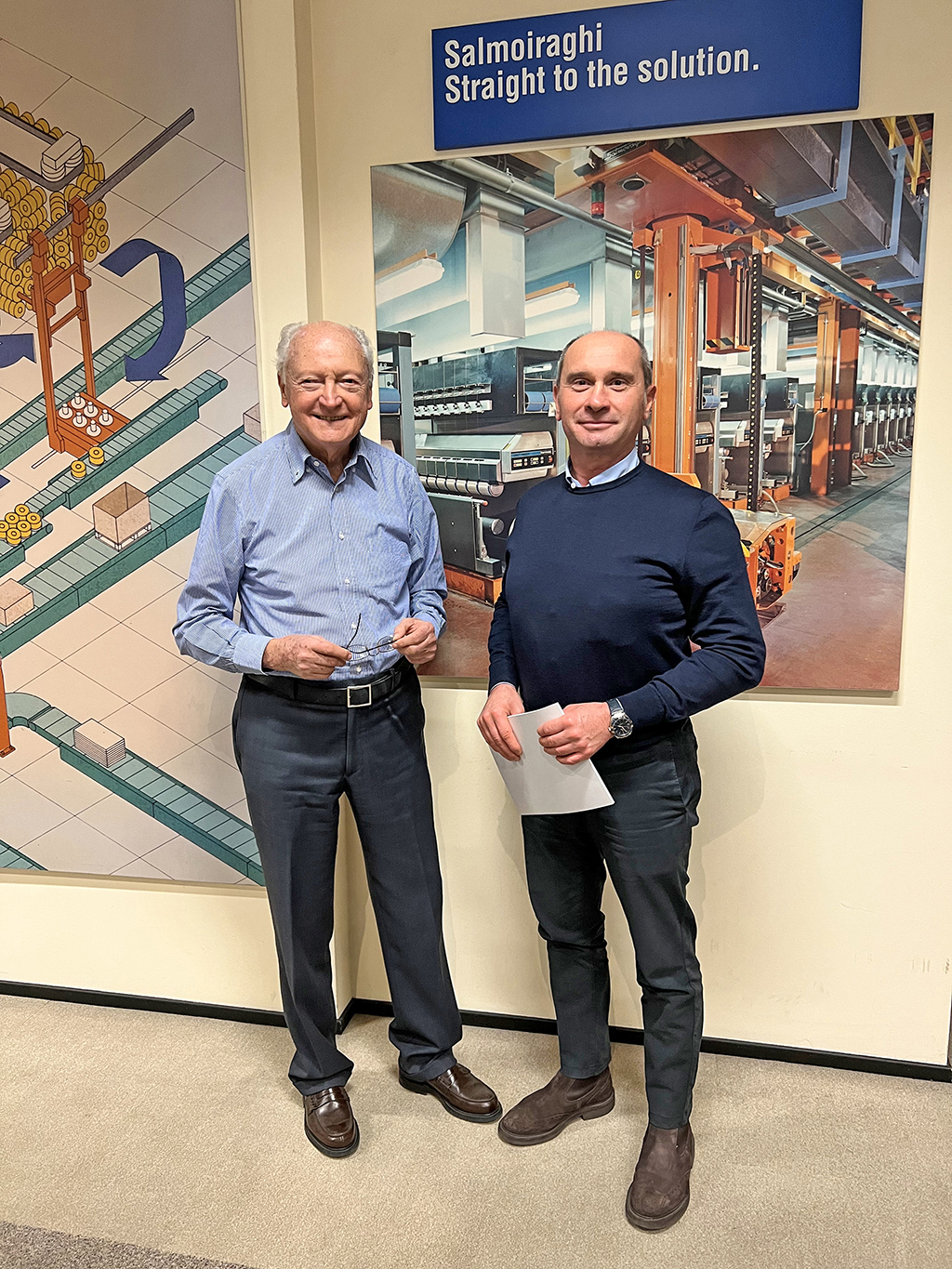
Coming from a family with solid roots in the textile industry, in 1963 the Salmoiraghi brothers Angelo and Sandro put to good use the knowledge acquired from their father and uncle – managers of important cotton mills in Northern Italy – combining it with the new technologies and engineering solutions. They already had significant design and business experience and decided to join their skills for starting a new activity in the textile machinery sector. After several years of specialisation in auxiliary equipment for the emerging synthetic fibre industry, the company started a close collaboration with the main chemical-textile Italian groups of the time such as Chatillon, SNIA, ANIC and Montefibre.
The first ‘Made in Italy’ quench cabinet lines were manufactured by Salmoiraghi, representing the start of a continuously developed product line featuring various customised solutions for the spinning of NYL, POY, BCF, tyre cord and microfibre. The activities of the company, which gradually evolved from a limited partnership entity to Salmoiraghi Ltd., and finally into the modern Salmoiraghi shareholder company, are not limited to Italy but spread over the international market in a world where borders seem to get ever larger. The years that followed were exciting and the company grew to gain a solid market reputation. Together with President Sandro Salmoiraghi, the new generation with sons Antonella and Giorgio, has carried on the family tradition, ensuring continuity and growth, assisted by a dedicated and highly motivated team.
Infrastructure and Products
Salmoiraghi is an integrated group in which each department is specialises in a specific automation sector. This allows the firm to have complete control of the engineering and manufacturing process while the customers benefit by obtaining fully integrated systems from a single source. The machines and integrated systems are developed through a sophisticated procedure of prototyping, operational simulation and shop testing. Advanced CAD stations are used for project and engineering development. A special section is dedicated to technical documentation and training of the client’s staff.
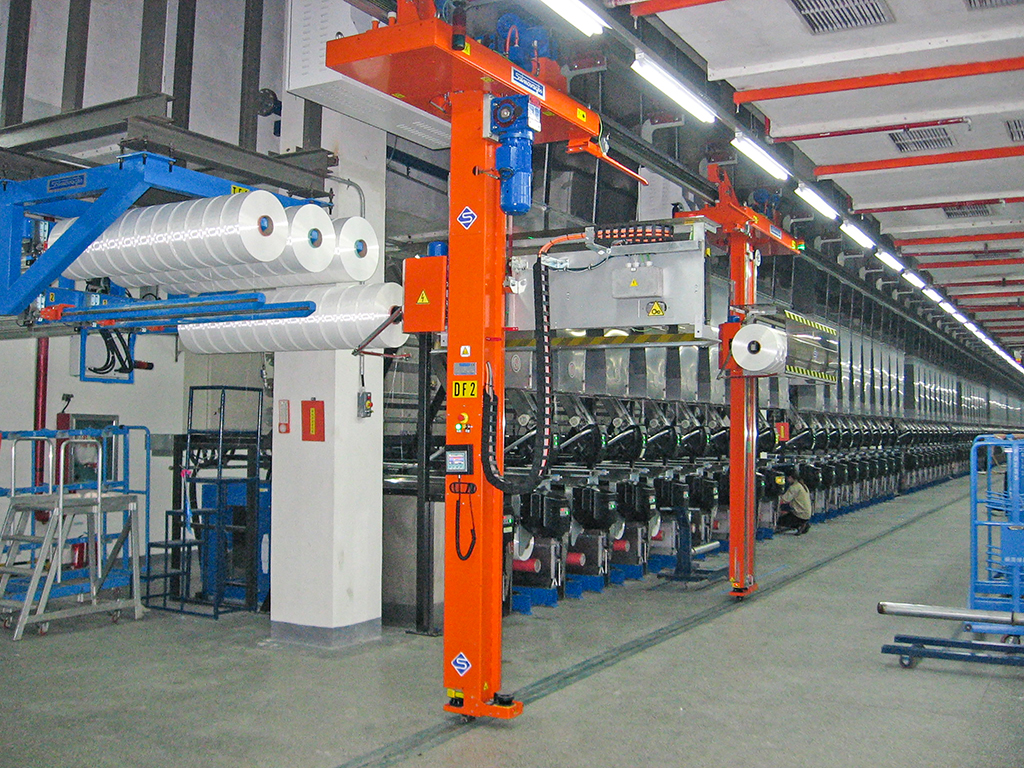
Salmoiraghi designs, manufactures and installs a wide range of integrated systems and special equipment for automated handling and warehousing of industrial products. The key application fields are factory in-house handling and transport systems for raw materials, components, and finished products, packing systems, auto warehouses and logistic distribution centres. From the original specialisation in textile automation systems, Salmoiraghi has evolved and diversified by applying the gained experience and know-how of automated handling and warehousing systems for other manufacturing sectors such as automotive, food, glass and carbon fibre, industrial components, healthcare facilities, etc.
Major Milestones
Due to the development of POY and larger bobbin sizes, manufacturers started encountering product-handling problems. A fortunate intuition led to the development of a system for loading and unloading of creel carts on draw twisters. This solution was an immediate success and has been adopted by leading machinery manufacturers such as Rieter, Barmag, Zinser, Marzoli, Ishikawa, etc. and also directly acquired by fibre manufacturers. From 1966 to 1972, over 500 of these systems and 12,000 creel carts were manufactured. Many of these systems are still fully functional and in operation today. The first concept of automated handling for continuous yarn plants emerged. Salmoiraghi developed solutions for automatic doffing and transport of cops produced by draw twisters.
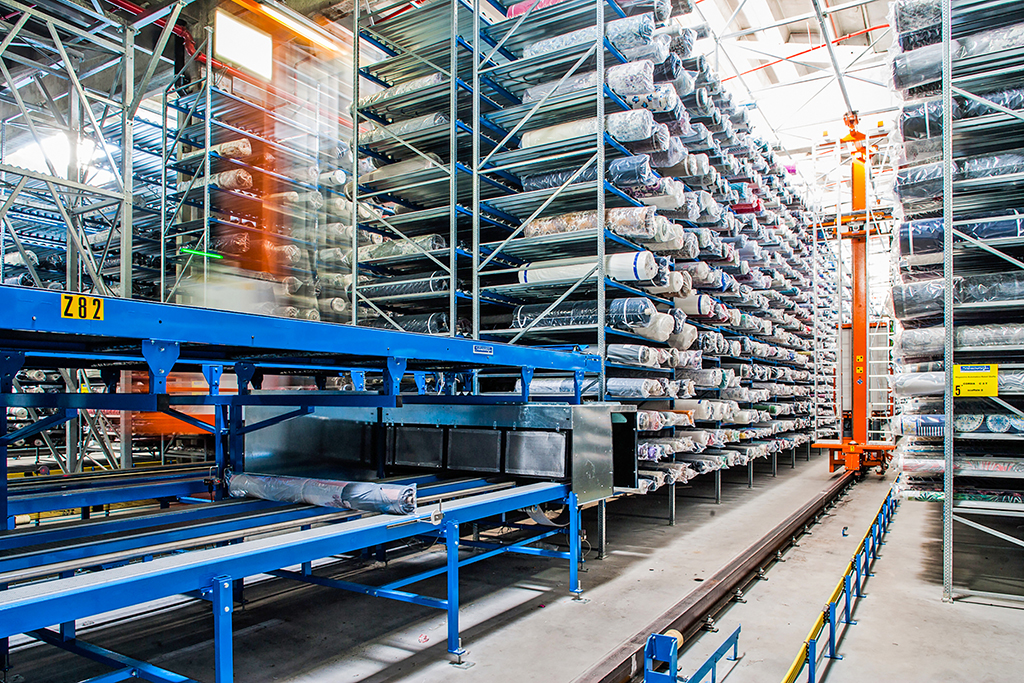
This led to the implementation of the SNIA Viscosa Villacidro System (1974), serving 48 draw twisters and featuring an integrated process, including doffing, inspection and sorting, automatic packing and box transport to the warehouse – all controlled by one of the very first computerised management systems applied to yarn handling processes. The advent of POY and the decline of draw twisting, superseded by the continuous process, led to new requirements concerning the doffing of bigger and heavier bobbins from the winders.
The doffer with its different variants was born in 1976. For the development of this important machine, Salmoiraghi actively collaborated with the main winder manufacturers, including Rieter, Barmag, Teijin and Toray. Following the doffer project, Salmoiraghi developed the bobbin overhead transport concept, featuring electrically powered shuttles travelling on elevated monorail circuits that follow the plant layout. At the ITMA 1983 show in Milan, Salmoiraghi exhibited the industrial doffer which, after many modifications and improvements, today remains the absolute market leader.
Export Scenario
Over the years Salmoiraghi has built more than 180 technologically performing fully automatic plants in Europe, Asia and America. In recent years, with the progressive concentration of the production of synthetic fibres in China, Salmoiraghi has gradually successfully introduced itself into this market. To date, Salmoiraghi has built more than 35 automatic handling systems in China. There is therefore a great possibility of further development for the realisation of full automatic systems in a 4.0 perspective for this large market.
The other developing markets are Turkey, India, Vietnam, USA and EU. In India the company has a well-established relationship with the Reliance Group since 1994 and to date has supplied 15 fully automatic systems for their various POY, FDY and DTY plants. It has also installed a large plant for Rajashree Polyfil. “We believe that today India represents a very interesting market for us not only in the handling of yarn bobbins but also for automatic warehouses for fabric rolls and carpets for which we have negotiations underway,” says President Sandro Salmoiraghi.
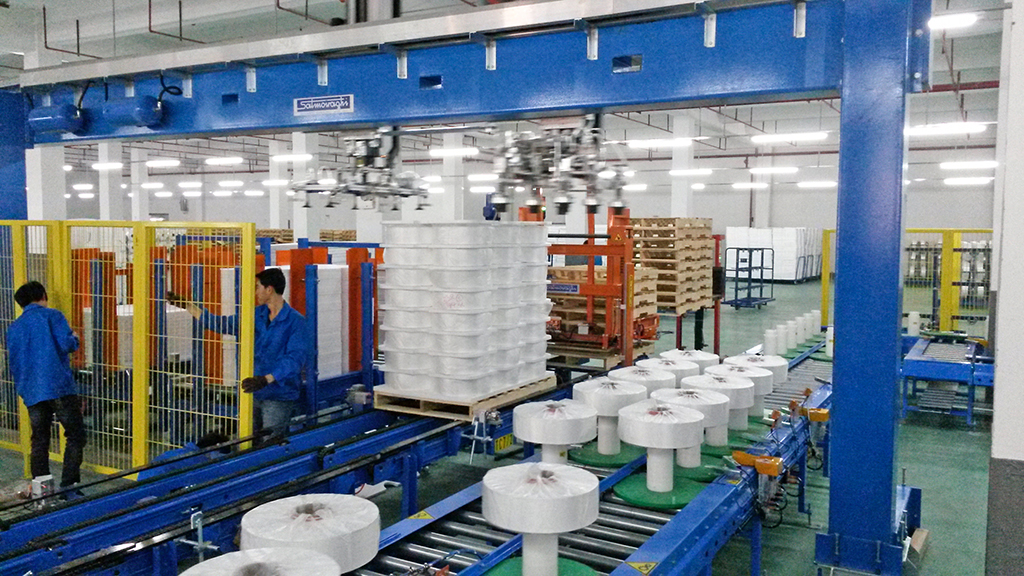
Innovative Approach
Alongside the fabrication of plants in the fibre sector (core business), there is the whole sector of generic handling for various applications and the auto warehouse sector, always integrated in solutions of complex handling. In recent years, as part of advanced specialisation concerning the design and fabrication of automatic warehouses for fabric rolls, a special device has been developed for picking up the single roll. There is also the sector of overhead transport systems through shuttles for which the company has great experience having realised many systems for handling loads from 10 to 1,000 kg. “In the auto warehouse sector we have carried out projects for stacker cranes up to 35 meters in height. Another area of specialisation concerns the inertia-guided vehicles used in special applications enslaved to machines and production processes for which we already have industrial installations in India and China, and which represent the current line of development for new applications,” informs CEO Giorgio Salmoiraghi.
The company currently holds several valid international patents regarding original solutions in its areas of competence. “A significant part of the design processes is reserved to research and development activities which we can undoubtedly summarise in a value equal to 15% of the annual costs of the personnel,” Sandro states. In the Salmoiraghi concept, automation is much more than a means for reduction of labour costs. The final aim is to eliminate product damage and handling errors often caused by manual handling. “By ensuring safe and efficient product flow in a compact and fluid system configuration, we enable our clients to achieve true total quality. Thanks to these concepts, Salmoiraghi systems have always achieved success with various manufacturers worldwide through significant quality improvement, sharp reduction of labour costs and prompt return on investment,” Giorgio says.
Technology Advantages
The ongoing research and development of innovative solutions allows the company to continuously augment the acquired engineering experience and integrate it with in-house developed core technology, machinery, devices and control software. “We carefully analyse any requirement, ensure comprehensive support all the way from the project concept phase to the commissioning of the fully operational system and guarantee after-sale assistance throughout the system lifetime. Thanks to close teamwork with our clients, we can offer customised solutions for any kind of application. Therefore, the client benefits by obtaining a personalised and flexible solution designed for specific needs and budget,” Sandro elaborates.
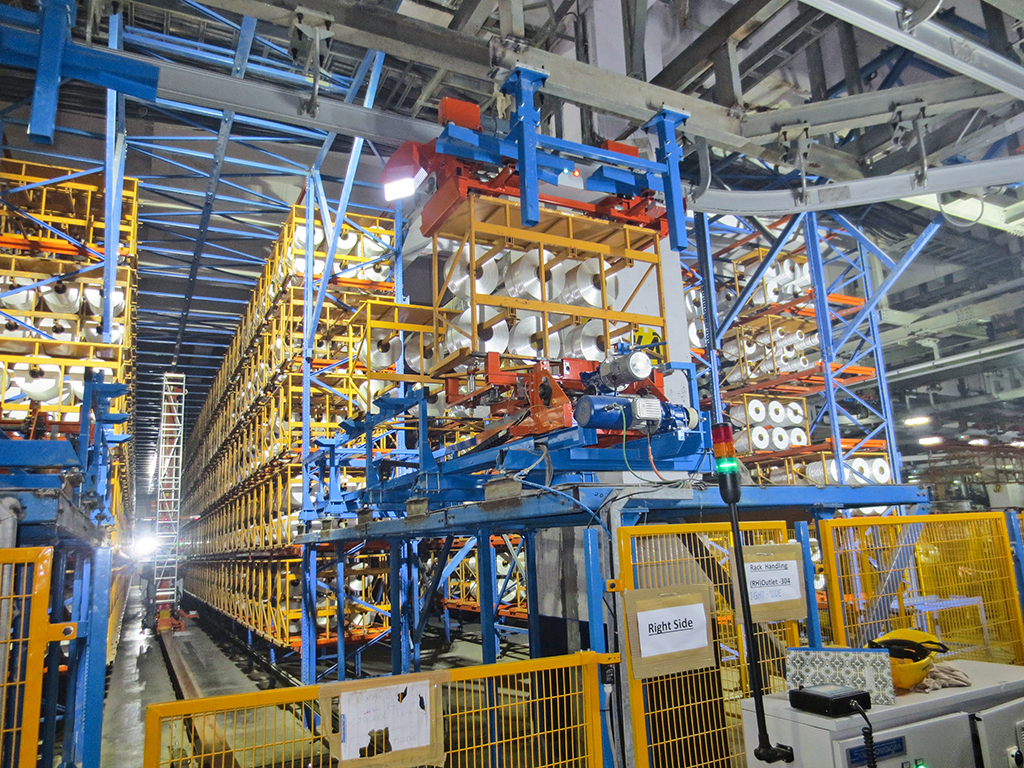
Sales and Service
Salmoiraghi’s systems are installed in continuous cycle production lines (24 hours a day) and each customer is prepared to manage the maintenance in real time. Remote assistance, in particular with regard to the software, has been used by the company for over 20 years and basing the construction of machinery on very solid foundations and supporting the customer with maintenance plans, it has managed to still have in operation systems completed in the eighties and nineties. “Today, due to the pandemic and despite all the restrictions associated with travel, we compensate it with our teams of local staff and resident technicians with sophisticated remote technical support managed directly from our headquarters in Monza,” Sandro states.
The Pandemic Experience
The pandemic-related experience was undoubtedly devastating and created enormous difficulties for everyone. However, despite the seriousness of the situation, the company’s reaction was rapid and effective, allowing activities to be carried out partly in presence, partly in smart working so as to minimise delays in the delivery of the plants. “We have also learned to remotely manage commercial activities and technical meetings and our customers have appreciated the support and collaboration, confirming their trust in us. There has been no increase in demand for our products typically linked to long-term investment plans, but there has been an incentive to make our systems more and more remotely controllable with the application of new technologies available today such as artificial vision and intelligence, data analytics, Internet of Things and augmented reality,” Giorgio says.