In the fast-paced world of industrial machinery, the backbone of efficiency lies in the hands of skilled service technicians. This is a compelling narrative that underscores the pivotal role skilled service technicians play in the efficiency of industrial machinery. The journey of Pralay and Ankur, two dedicated technicians from India, reflects the commitment to excellence and continuous improvement in the dynamic field of digital textile and carpet printing machinery services.
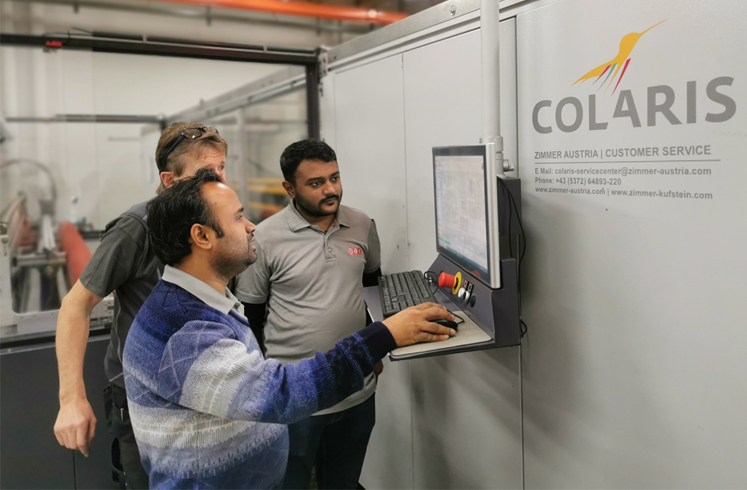
The initiative taken by ZIMMER AUSTRIA Digital Printing Systems and A.T.E. Enterprises Private Limited to enroll these technicians in comprehensive training programs demonstrates a proactive approach to staying ahead in the industry. The programs not only equip Pralay and Ankur with theoretical knowledge but also provide hands-on experience and exposure to cutting-edge technologies, setting the stage for their mastery of machine installation, maintenance, and troubleshooting.
The precision in machine installation, as emphasized in the narrative, showcases the technicians’ ability to decipher complex schematics, assess spatial requirements, and execute installations with meticulous attention to detail. Their training prepares them to handle a diverse range of machines, from CHROMOJET electromagnetic jet-based carpet printers to high-resolution inkjet printers like COLARIS used in textile and carpet printing mills.
The story also highlights the shift towards preventive maintenance as a key focus for Pralay and Ankur. Armed with their newfound knowledge, they plan to develop proactive maintenance schedules to ensure machines operate at peak efficiency, reducing downtime and prolonging machinery lifespan.
Troubleshooting emerges as an art form for Pralay and Ankur, as they learn to diagnose and resolve issues swiftly, minimizing disruptions to production lines. The real-world application of their skills in their respective workplaces results in tangible improvements – decreased machinery downtime, increased productivity, and a downward trend in operational costs. Their ability to handle complex installations, conduct proactive maintenance, and troubleshoot with precision positions them as indispensable assets within their organizations.
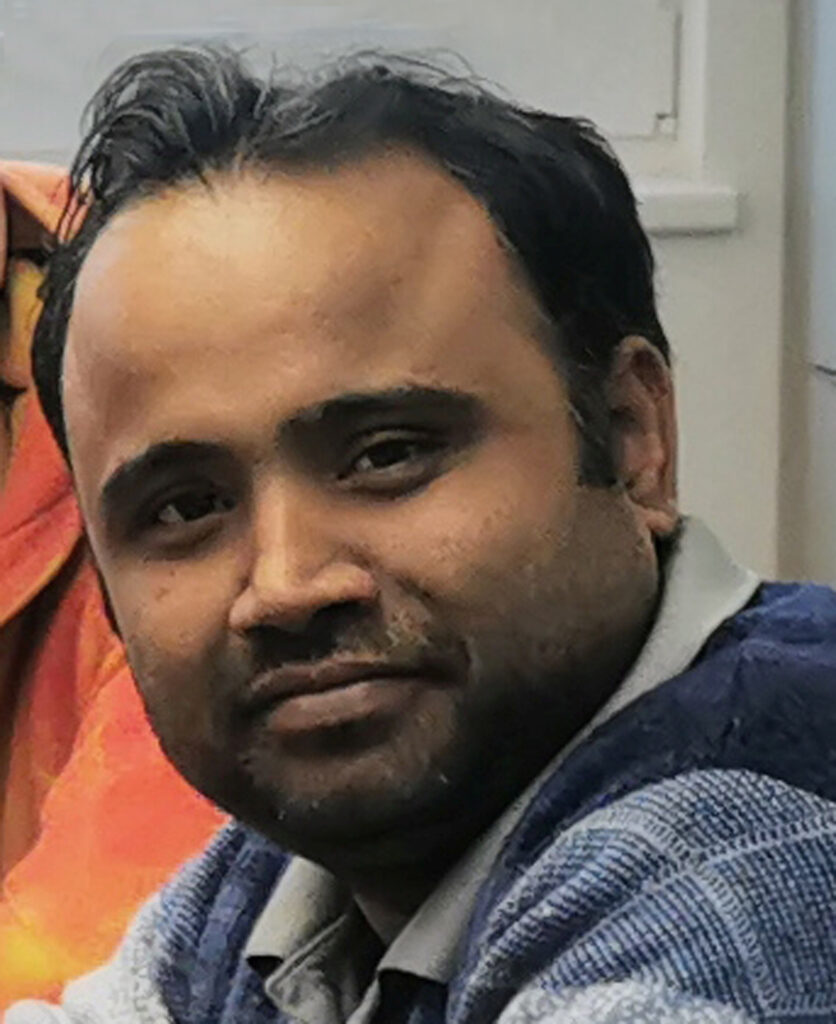
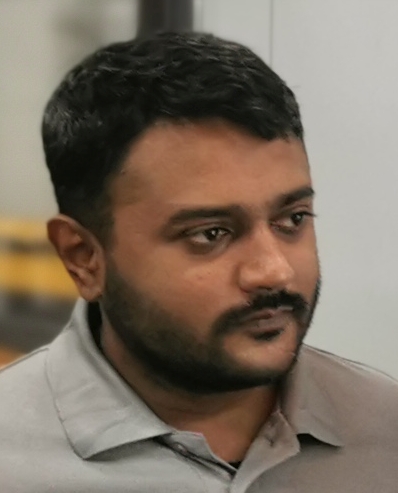
The ripple effect of Pralay and Ankur’s commitment to continuous improvement is emphasized in the narrative. Their colleagues are expected to adopt a similar mindset, leading to an overall enhancement in the quality of machine services within the organizations. Beyond the workplace, the ripple effect extends to positively impact client satisfaction and the companies’ bottom lines.
In conclusion, the story of Pralay and Ankur serves as a powerful illustration of the transformative power of investing in training for service technicians. It underscores the idea that in the realm of machine installation, maintenance, and troubleshooting, knowledge is not only power but also a catalyst for progress and innovation in the world of machinery services. As industries evolve, technicians like Pralay and Ankur become beacons of inspiration, showcasing that a commitment to mastering the intricacies of their craft can lead to remarkable success.
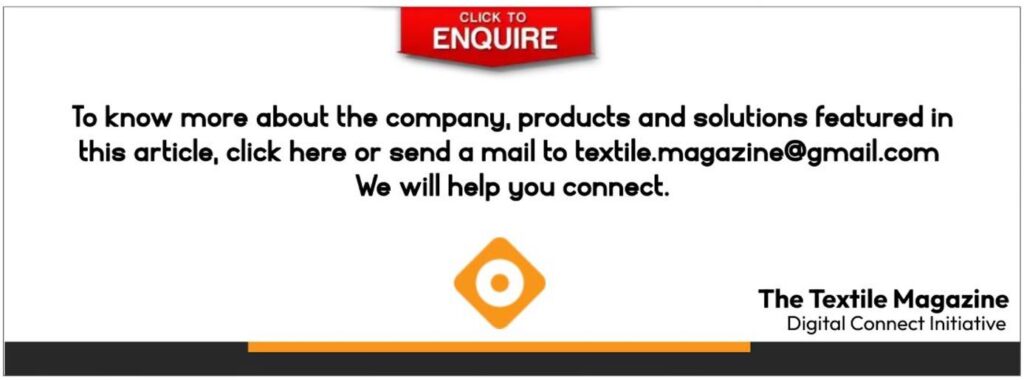