By Arun Rao
Maruti Group’s Growth Journey: From Cotton Farming to Textile Excellence
Maruti Group, originally rooted in cotton farming, has evolved into a prominent player in the cotton ginning and textile industries. Based in Gujarat, the company started humbly with a small-scale cotton gin in 1996, founded by two brothers, who are first-generation entrepreneurs. Initially, the factory had 12 manual rollers, but the vision to produce high-quality ginned cotton and ensure maximum productivity laid the foundation for significant expansion.
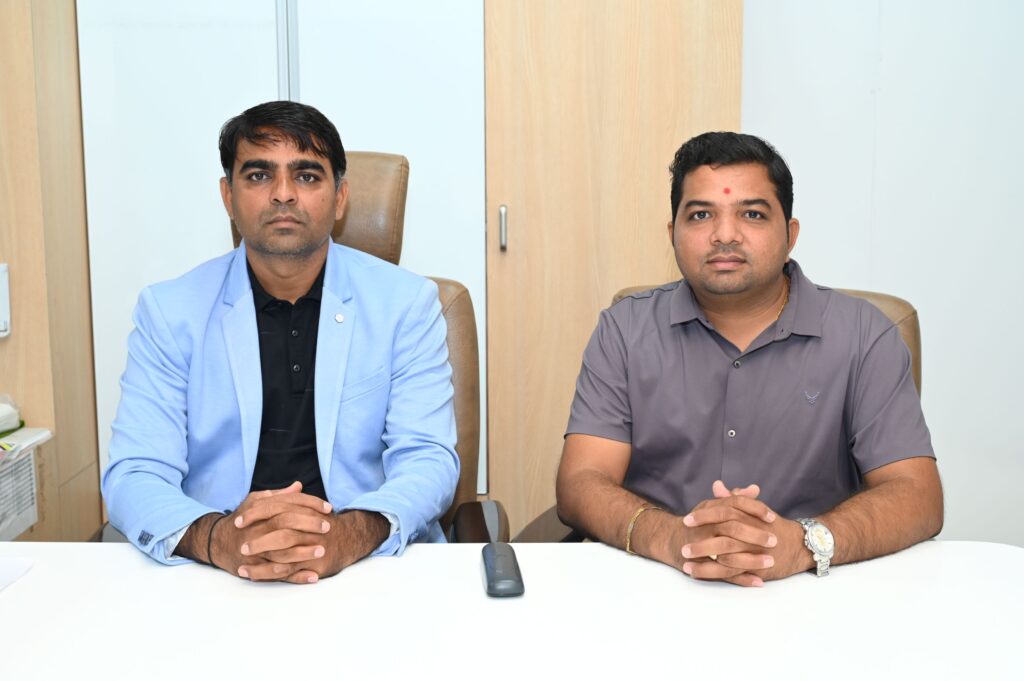
The Group has strategically partnered with Color Service from A.T.E. Enterprises, a leading-edge color kitchen solution, to meet the exacting standards of fashion brands for consistent and accurate dye shades in fabrics. This collaboration highlights Maruti Group’s dedication to innovation and quality across the printing and dyeing segments, ensuring superior results in every aspect of the manufacturing process.
With the increasing demand for their high-quality ginned cotton, the Maruti Group expanded its operations by setting up a new, automated ginning factory in 2005, which was later approved under the Government of India’s Technology Mission on Cotton (TMC). In 2008, they introduced a cotton seed crushing plant to manufacture cotton seed oil and cakes. The third cotton ginning factory came in 2012, further strengthening their position in the market with 24 automated rollers. As of now, their combined cotton ginning capacity stands at an impressive 600 bales of 170 kg each.
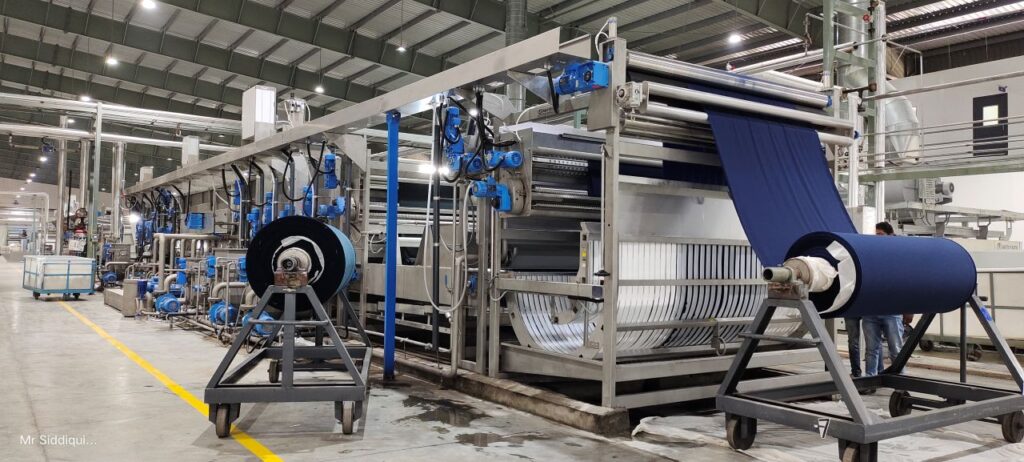
The Group’s consistent focus on high-quality production has allowed them to supply their cotton bales to prominent domestic customers in South India, such as KPR Mills, Shiva Texyarn, and Bannari Amman, and also export to several international markets. As Mr. Dhiru Kanetiya, Director of Maruti Group, stated, “Our journey in the cotton industry began with a simple vision, and now we are proud to see how it has grown into a much larger, successful business.”
Diversification into Spinning: Meeting the Demand for High-Quality Yarn
In 2012, with the introduction of Gujarat’s first Textile Policy, the Maruti Group expanded its horizons beyond cotton ginning and entered the spinning sector. The Group established an 18,000-spindle spinning unit equipped with cutting-edge technology. The spinning mill utilized blowroom and carding machines from Trützschler. This mill, which began its commercial production in 2015 mainly, produces compact cotton yarns.
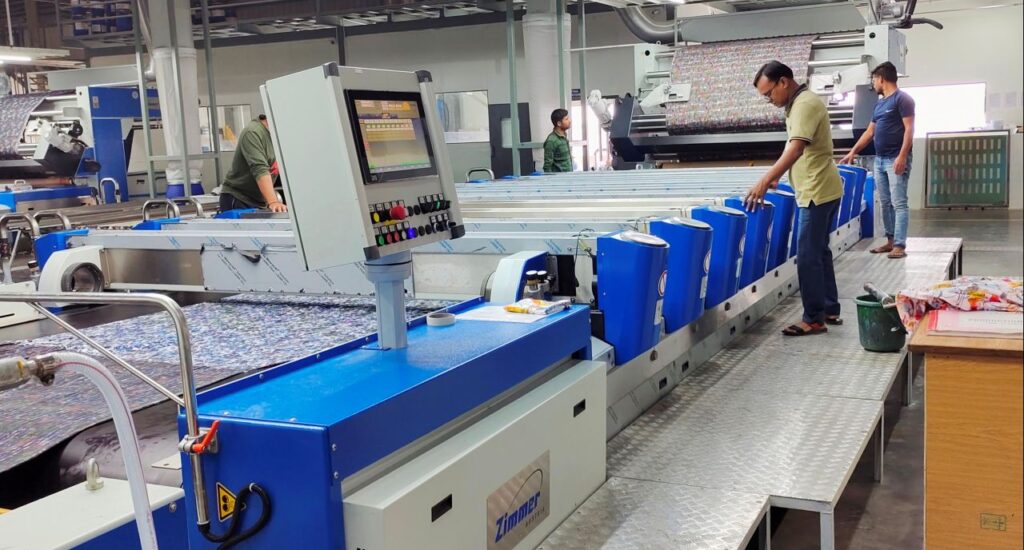
The Textile Policy extension in 2017 and market demand provided the Group with the confidence to further expand its operations. This led to the establishment of another spinning unit with 20,000 spindles, bringing the total to 38,000 spindles in just a year, ensuring the production of more high-quality compact yarns to meet the ever-growing demand.
Expanding into Knitting, Dyeing, and Printing: A Strategic Move for Value Addition
In 2020, Maruti Group decided to take a step forward in its expansion journey by setting up a knitting, dyeing, and printing unit. Instead of increasing spinning capacity, the company chose to add value to its cotton products by entering the knitting and fabric processing industry. After thorough evaluations of various knitting, dyeing, and printing technologies, Maruti Group chose the best available solutions.

Maruti set up a green field project for knitting and processing for the production capacity of 20 tons per day. The plant was set up with a state of machinery which includes rotary printing machine from Zimmer, Austria and fully automated dyes/chemicals storage, dissolution and distribution system from Color Service, Italy.
Maruti Group sources cotton from a select group of farmers known for their consistent high-quality cotton, which allows the company to maintain high standards in fabric production. This consistent quality is the key to their success in both the domestic and international markets. According to Mr. Paresh Kanetiya, Director at Maruti Group, “We supply our knitted fabrics to renowned brands like Jockey, Rupa, Amul, and Dollar in the domestic market, and export fabrics to Sri Lanka and Bangladesh for garment manufacturing, serving global brands in Europe and the US.”
The Role of A.T.E. Enterprises’ Color Service Technology in Ensuring Dyeing Precision
One of the key factors contributing to the Maruti Group’s success in fabric dyeing and printing is the integration of Color Service’s advanced color kitchen. The traditional dyeing process often led to inconsistencies in color shades, especially for complex colors like black. However, the Color Service system has provided the Group with a solution that ensures accuracy and consistency.
Mr. Dhiru Kanetiya explained, “In the conventional process, the dyeing shade is done manually, leading to inconsistency when repeating the same color. But Color Service ensures excellent accuracy. For example, black has many different shades, but with Color Service, we can achieve the exact shade as required by our customers, whether for dyeing or printing. The biggest advantage is that the recipe for any shade is stored and can be retrieved for future use.”
He also mentioned that the technology minimizes wastage of dyes and eliminates the risk of fabric rejection due to incorrect shades. “Color Service machines prepare the exact number of kilograms required, so there is no wastage, and the shade is as per the specification. 99% of the time, the machine delivers the correct shade on the first attempt,” he added.
The decision to choose Color Service was influenced by Maruti Group’s positive experiences after discussions with other mills that had already adopted the technology. These mills also expressed satisfaction with the system’s performance, leading Maruti to finalize the partnership with A.T.E. Enterprises.
Commitment to Sustainability and Eco-Friendly Practices
Maruti Group is also committed to sustainability and environmental responsibility. The company has installed a Zero Discharge Plant (ZLD), which ensures that 96-97% of water used in the textile process is recycled. Furthermore, the Group has invested in renewable energy, including a 2.70 MW wind energy plant and a 10 MW solar plant. With plans to add 5 MW more solar capacity, green energy will account for nearly half of the Group’s electricity needs.
“We aim to meet the government mandate of using 50% green energy and 50% conventional energy,” said Mr. Paresh Kanetiya. “Our dyeing process uses 50% less water and is chemical-free. Chemicals are only used during the washing stage of fabric production, and we do not use salts. Our boilers are equipped with advanced systems to reduce harmful emissions, ensuring minimal environmental impact.”
Additionally, Maruti Group offers traceability for its fabrics, providing customers with detailed information about the cotton’s origin, starting from the farms that supply the raw material. The company’s textile operations are certified under various compliance standards, such as the ISO 9001:2014 & 14001:2024, Regen Agri, Oeko-Tex Standard 100, SEDEX SMETA, GOTS, OCS, GRS, BCI, ZDHC, The BHive, Higg Index, Walt Disney FAMA certification.
The Success Formula: High Quality, Timely Delivery, and Transparent Practices
Maruti Group’s focus on delivering high and consistent quality fabrics on time has made it a leader in the fabric dyeing and printing sector in India. Mr. Paresh Kanetiya explained, “We are very particular about meeting our committed delivery dates, and if we believe the fabric quality will not meet customer expectations, we will not ship it. This commitment to quality and transparency has been the key to our success.”
The company’s current fabric dyeing and printing capacity stands at 600 tons per month, and it plans to double this capacity to 1,200 tons per month. Furthermore, Maruti Group has plans to set up a garment manufacturing unit with a capacity of 10-12 lakh pieces per month, which will further enhance the value addition to their products.
Future Plans and Continued Partnership with A.T.E. Enterprises
Looking ahead, Maruti Group aims to continue expanding its operations with a focus on maintaining high quality and adopting the latest technologies.
As Mr. Dhiru Kanetiya concluded, “A.T.E. Enterprises has been a trusted partner for us, providing reliable and top-quality machinery. We are pleased with the results and will continue to place repeat orders with them in the future.”
S Rajendran, Senior Vice President, A.T.E. Enterprises:
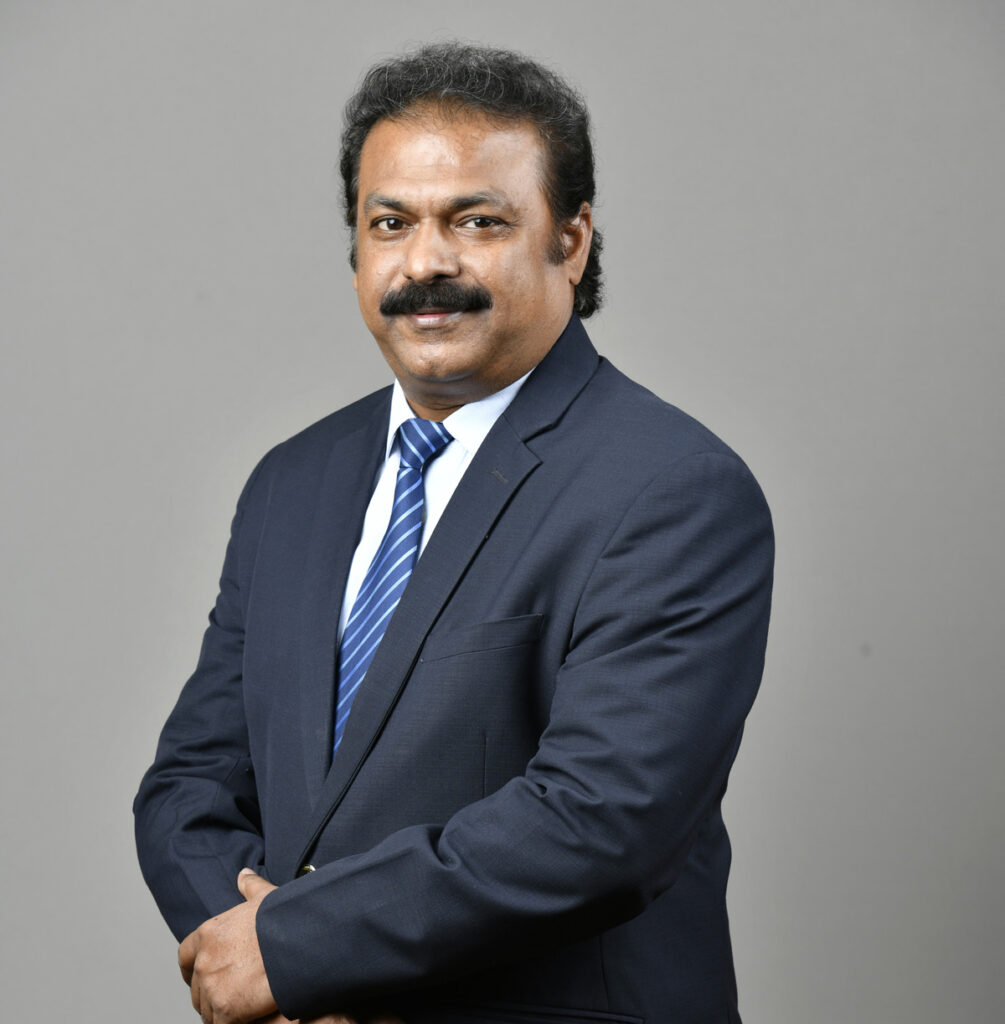
Maruti Group is our spinning customer, and we enjoy a good relationship with them which created a comfort for us to discuss with them in detail about their knitting and processing project. The customer had a goal to set up a modern processing plant with open width processing facility for knit fabrics. The main focus was to produce quality printed fabrics. We showed the working demonstration of Zimmer rotary printing machine as well as Color Service products for knit fabric application, and we finalized the specification based on their end products. It was a great teamwork between Maruti and A.T.E. for the smooth execution of two Zimmer rotary printing machines and fully automated dyes and chemicals dispensing system from Color Service. We are happy to mention that we have created one more good reference in India for knit fabric printing. Color Service products are helping the customer to achieve the quality, consistency and high productivity. The project of Maruti helped us to increase the market share of Color Service in India.