Mafatlal Industries Ltd. (MIL) registered a total revenue of Rs. 935.49 crores on account of higher production levels during 2013-14 as against Rs. 840.38 crores in 2012-13, signifying a growth of 11.32 per cent. Its profit after tax for the same period amounted to Rs. 23.93 crores.
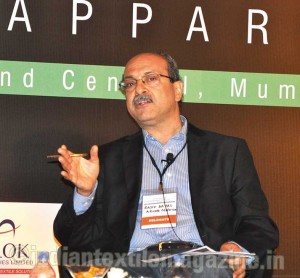
During the year, the company continued implementation of its business strategy objectives comprising of capital investments in contemporary processing equipment and other critical operational areas, across-the-board cost reduction and optimization initiatives, improvement in product mix and attaining synergy on account of the amalgamation concluded in the previous year.
An amount of Rs. 32 crores was spent on capital expenditure in the Nadiad and Navsari factories of the company. A captive power co-generation plant of 3 mw capacity will be commissioned this year. It plans to further undertake capital expenditure of around Rs. 38 crores in line with its long-term objective of modernizing its plants.
The Textile Division of the company has started generating profits during 2013-14. It also witnessed substantial increase in production levels, and with the installation of new capital equipment and increase in processing capacity the company expects to gradually increase the production level in 2014-15. The captive co-generation plant at Nadiad is expected to be commissioned by mid-2014.
The Denim Division of the company increased its capacity in 2013-14. Presently, the Indian denim industry is facing a situation of over capacity, which has led to demand and supply mismatch thereby causing pressure on price realizations and volume growth. This, coupled with high cotton prices throughout 2013-14, has led to severe erosion of profit margins in the denim segment. The situation is expected to improve in 2014-15.
The company plans to expand its marketing presence in export markets and also aims to align its marketing strategy towards having a judicious mix of domestic and export sales and introduce new value added denim fabrics for Indian and global brands.
Mafatlal still continues to be the market leader in supply of school uniform fabrics in India and tries hard to replicate the success of this business in the Middle-East countries through its joint venture, Al Fahim Mafatlal Textile LLC. The company also launched its designer collection of school uniforms with eco-friendly fibre dyed suiting for the coming season. Its corporate and institutional wear business also continues to show steady growth. During the year, MIL launched several new products including a premium linen range, bed and bath home furnishing collection and innovative white bleached and blended fabrics.
Energy conservation
The company has taken up several major initiatives to reduce its energy consumption. It has installed machines like Osthoff singeing machine, Goller combi range, Goller merceriser range, Fongs yarn dyeing machine (5 nos), Then air flow dyeing machine, 16 colour MHMS printing machines, Bruckner 7 field stenter machine, Monfort sanforiser machine and Thermax FBC thermic fluid heater 2000 BTU for better processing and low specific energy consumption.
R&D
In order to improve RFT in fabric and yarn dyeing various lab and bulk trials were conducted. RFT was improved from 60 to 80 per cent. Due to tremendous demand for linen fabric in domestic and export market, linen fabrics were developed in solid and yarn dyes. Being an eco-friendly process, bio scouring was introduced for bleaching at yarn stage. In order to provide speciality products for customers, Prema white fabrics were developed with 25 wash durability. Lycra fabric was developed in whites, dyed and yarn dyed. Modal and excel fibres being eco-friendly fabrics were developed in prints and solid dyed. As a result of these developments the company acquired a few new businesses and new customers.
Technology absorption
By adapting to the upcoming technology, the company installed new air flow dyeing machine and Fongs yarn dyed machine in its facility. This has resulted in a lower liquid ratio and in saving of water, power and effluent load. The quality of product has also improved. AGoller CBR and Merceriser was installed and commissioned to produce 1 lakh metres of fabric per day. Bruckner Stenter was installed leading to considerable saving in energy due to newly developed air circulation system. Printing quality and production was improved with the installation of new MHM printing machine.
Technorama Lab colour auto dosing has helped in reducing manual errors in the lab and contributed in improving RFT in sample development. Desk loom production increased due to installation of automatic sampling looms and warping machine thereby improving lead time in sample development. New Yarn Singeing Machine has been installed, which has resulted in a reduction of yarn breakages and improvement of loom efficiency by 11 per cent.
Efforts are on to enter new markets of the Middle East, Europe, Africa and the US. The company has been successful to some extent in increasing exports of processed fabrics to these countries.