Significant saving on maintenance costs
Mr. Heiko Engelke, General Manager, Lubricant Consult GmbH
A global research conducted by a bearing manufacturer shows that more than 50 per cent of premature bearing failures are due to over-lubrication, under-lubrication, mixing of incompatible lubricants, wrong lubricant and lubricant contamination. This has its significant impact on the country’s economy, says Mr. Roland Metelmann, President, LUBCON Lubricants Asia Pacific Inc.
India is undoubtedly one of the most mature market in textile manufacturing. The industry is investing in state-of-the-art, high quality, high performance machines from all over the world. These machines perform 24/7, 365 days a year, but they require the right level of lubrication to ensure that they operate at the optimum levels. The new generation of high speed machines are highly demanding when it comes to lubrication systems. Excess lubrication and under-lubrication can lead to serious failures in machines, the cost of which might run to thousands of dollars for millowners.
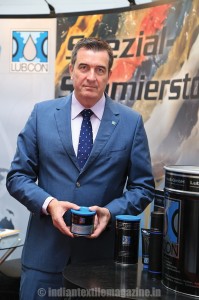
With an intention to sharing its global expertise and serving the Indian market, LUBRICANT CONSULT GmbH (LUBCON), a global leader in manufacture of lubricants for industrial applications, has entered the Indian market. It has partnered with the Coimbatore-based Star Industrial Products to cater to the growing requirement for lubrication systems for the industrial market in India.
Founded in 1980, LUBCON has established an extensive network of subsidiaries and sales representatives around the globe. “India is one of the world’s leading destinations for textile manufacturing. There are many modern manufacturing facilities equipped with the latest machines. There is a definite need to engage with customers and educate them on the need for right lubrication. Some customers do not understand the importance of using lubricant of the right quality and specification and they end up paying a heavy price. We at LUBCON have global expertise and understanding of the textile industry. We are confident that through continuous engagement with the industry we will be able to help our customers adopt best practices and save significantly on maintenance costs and breakdown”, says Mr. Metelmann.
LUBCON caters to a range of industries within which textiles is a very important vertical for the company. From raw cotton processing to finished product, textiles is a long manufacturing process that depends on reliability and performance of different machines. Whether in cotton and synthetic fibre yarn production, fabric knitting and weaving or in textile finishing, machine elements are constantly subject to high loads and have to operate efficiently. High speeds, wide temperature ranges and chemical influences are factors that impede an optimum manufacturing process on a daily basis.
LUBCON lubricants for the textile industry are specifically designed to withstand various loads, even at maximum machine operation. They protect friction points from wear and corrosion for a low maintenance operation over a long period.
Spinning machines
Speed and temperature are important factors in production as well as processing of cotton/synthetic fibres. In sliver processing, e.g., drawing frame needle bearings or twin disc bearings can reach speeds of up to 3.0 million mm/min. The use of the inappropriate lubricant can cause overheating and premature bearing failure. Especially in the spinning process, selection of the proper and application tailored lubricant is thus of great importance.
LUBCON has a product assortment particularly designed to meet the requirements in spoolers and spinning machines manufactured by Grossenhainer Textilmaschinenbau Ltd., Marzoli spa, Rieter Holding AG, Saurer AG, Trützschler GmbH & Co. KG, etc. The lubricants consistently protect against friction and wear and reduce operating costs by extending maintenance intervals.
Synthetic fibre
Synthetic fibre production allows incredibly broad product varieties and is indispensable in the modern textile market. Yet, it is a complex production process from polymer melt to the finished synthetic yarn. Various machine elements in filament spinning are subject to aggressive chemicals as well as extreme temperatures and speeds. For instance, in synthetic fibre processing where hot polymer pushes through the spinnerets at high pressure or where hot godets distribute filaments to the winding section at highest speeds. Such demanding processes in synthetic fibre manufacturing are major challenges for the machine and lubricant.
LUBCON offers high-performance lubricants protecting machine components from chemical and mechanical impacts, facilitating maintenance and extending operating time as well as machine service life. LUBCON works with Barmag in the segment.
Knitting and weaving
Mr. Roland Metelmann, Mr. Heiko Engelke, Mr. Mahesh Krishnamurthy, Country Manager, LUBCON India, Mr. B. Vaidyanathan, GM – Sales & Tech Services, Star Industrial Products (Cbe), and Mr. Anand Ramanathan, GM – Sales & Tech Services, Star Engineering Services, and the team from Star Industrial Products
Modern circular knitting machines, flat beds and weaving machines manufactured by Groz-Beckert KG, Mayer & Cie. GmbH & Co. KG, Stäubli International AG and Lindauer Dornier GmbH daily process several hundred kilograms of knitted material at maximum speeds. Hundreds of fine needles and sinkers turn colourful threads into socks, sweaters, skirts, coats, wool bed covers and comforters with finest patterns in a blink of an eye.
An accurate knitting and weaving image requires good yarn tension as well as the reliable operation of bearings, gears, sliding elements and needles. Even the smallest machinery discrepancy reflects immediately on the knitted or weaved fabric and increases thus the percentage of sub-standard fabric as well as the associated manufacturing expenses.
LUBCON offers tailored high performance lubricants for the reliability of machines, particularly geared towards machine component precision and long service life. Scouring, friction and wear minimising LUBCON needle, running-in and cleaning oils enable clean and low-maintenance production processes, while saving costs.
Finishing
One of the most important manufacturing segments in the textile industry is yarn, fabric and textile finishing. The desired fabric/fabric fibre properties such as stiffness, smoothness, softness, protection or colour can only be accomplished through finishing.
Machine components, especially in the textile finishing process, are incessantly exposed to mechanical, chemical and thermal challenges. Textile finishing machines have to perform at highest levels and withstand daily operating conditions such as extremely high loads, high temperatures as well as contamination with water, chemicals, detergents and hot steam.
Due to the latest additive technologies, LUBCON special greases for the textile industry protect machine components such as chains, roller bearings, adjusting spindles and gears against those detrimental influences. Furthermore, they prevent friction and wear-related failures and thus enable long service life and maximum operation reliability.
LUBCON greases, oils and pastes can be utilised in textile finishing machines manufactured by industry majors like Benninger AG, Brückner Group GmbH, J. Zimmer Maschinenbau GmbH, Monforts Textilmaschinen GmbH & Co. KG, etc.
Mr. Metelmann adds: “We have also developed a mapping tool, LUBCON Asset Optimisation System, to help customers optimise on consumption of lubricant. It also ensures that the matching lubricant for the lubrication point is used in the right amount and at the right time. Our experts go to the customer location, map the individual lubrication points in the machines, optimise and implement it. We are planning to organise a series of workshops and seminars and explain to customers through constant education on the importance of lubrication. We are entering the Indian market with high confidence and big expectation along with a very good professional partner. India is the second largest textile market, next to China. We are confident that 2015 will be a good year for LUBCON in the Indian market”.