L.S. Spinning Mills Private Limited has emerged as a leader in the highly competitive textile manufacturing industry, and is well known for producing premium-quality yarn. Their long-standing partnership with LMW for spinning machinery has been key to their sustained growth and innovation. Over the decades, this collaboration has not only overcome challenges but also continuously evolved to create value and reach significant milestones.
With this technologically advanced and highly automated mill, L.S. Spinning Mills Ltd. is able to maintain the same high-quality output while increasing production and reducing manpower requirements. Their yarn realization has improved by 2.5%, and they have achieved significant power savings, positively impacting operational efficiency and setting new benchmark standards.
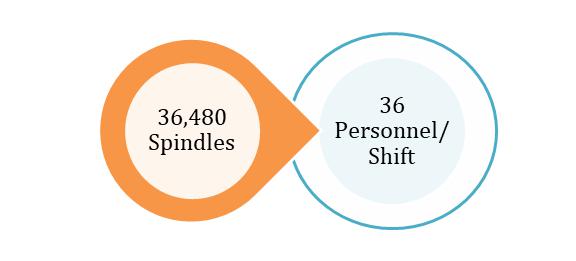
This fruitful collaboration has significantly boosted LSS Mills production capabilities while setting new industry benchmarks in efficiency, automation, and sustainable practices.
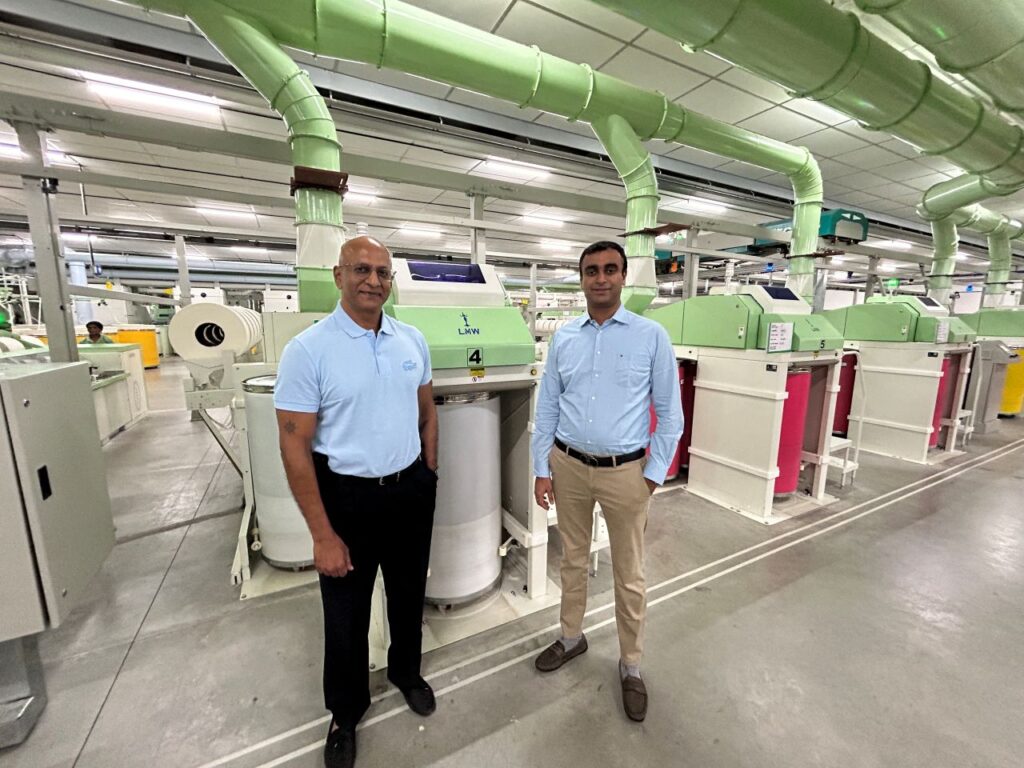
LMW’s Cutting-Edge Technology
LMW’s extensive range of machinery, from blow room equipment to ring spinning frames, has empowered LSS Mills to reach impressive productivity and quality standards. By integrating LMW machines across the entire production process, they ensure consistency and efficiency, reinforcing their position as a preferred supplier to high-end textile manufacturers.
A key highlight of LMW’s machinery is its capability to run at high speeds without compromising the exceptional quality of the yarn. Mr. Harshavardanaa Prabhakaran, Executive Director, LSS Mills, states that they were able “to attain top quality by operating their ring frames at maximum speeds of 26,000 RPM, which enabled them to achieve the highest grams.” This combination of high-speed operation and advanced automation has streamlined LSS Mills workforce, reducing the need to just one operator for every thousand spindles in their newest state-of-the-art facility. As Mr L.S. Prabhakaran states with pride, “there are just 36 people running the complete unit of 36,480 spindles.” LSS Mills is truly a testament to the remarkable levels of automation achieved through LMW’s technology.
Benchmarking Efficiency—36 Personnel for 36,480 Spindles
The LMW Advantage
LMW’s dedication to innovation shines through in their latest solutions, including the Spin Pact compact spinning system. Recently implemented at LSS Mills, this technology has greatly enhanced yarn quality and consistency. The compact spinning system plays a vital role in producing the superfine yarns that LSS Mills specializes in, ranging from 50s count to 160s count.
Benchmarking productivity and quality –
With the introduction of next-gen smart machines from LMW, LS Spinning Mills Private Limited has achieved a benchmarking productivity of up to 92 GPSS in 60s Ne CC, maintaining the highest quality levels.
- 10% increase in productivity at an average spindle speed of 24,300 rpm (0.1 TM reduction, 4.0 from 4.1).
- 11% increase in productivity at an average spindle speed of 24,300 rpm (0.1 TM reduction, 3.9 from 3.8).
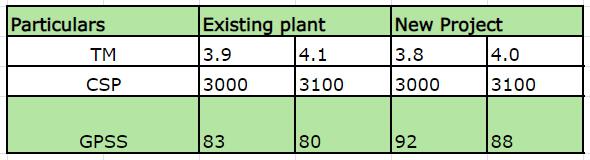
Yarn realization
Thanks to LMW’s smart and advanced carding and combing systems, yarn realization has improved by 2.5%, reaching a rate of 72%.
Particulars | Existing plant | |
Count | Ne 60s | |
IPI Level | 110-130 | |
Waste % | BR + Card + Others | 11.5% |
CBR Noil | 19% | |
Total | 30.5% | |
Yarn Realization | 69.5% |
LMW’s after-sales service has played a vital role in their partnership with LSS Mills. Mr. L.S. Prabhakaran remarks, “Their service is exceptional—they’re just a call away. Within a day, they send their team to resolve any issues.” This level of responsiveness is critical in an industry where production delays can result in significant financial losses.
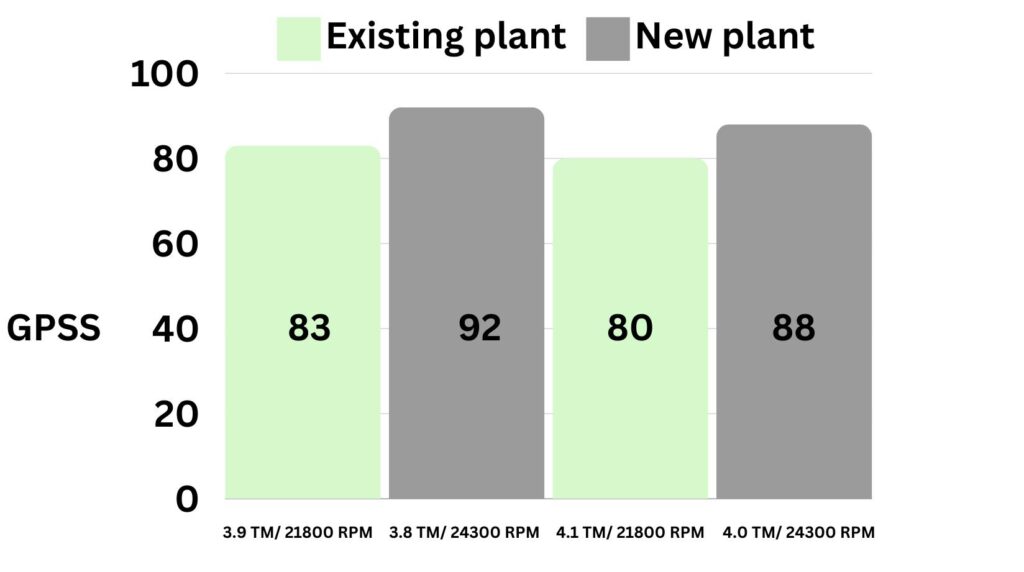
LSS Mills trust in LMW extends to their future expansion plans. Mr. Harshavardanaa confirms that LMW will be their preferred choice in their future projects. With over 1,06,000 spindles in operation, LSS Mills has positioned itself as a key player in the superfine yarn category. Their ability to cater to premium clients is largely attributed to the consistent high quality of yarn produced on LMW machines. “Our USP pivots on providing the best quality for all our customers,” says Mr. Harshavardanaa. “We have a dedicated team of technicians who focus on providing the best quality.”

Sustainable Practices and Future Growth
LSS Mills does not compromise when it comes to quality. They opt for premium raw materials sourced from the US and Egypt for their super fine category of yarn. This focus on top-tier inputs combined with LMW’s advanced machinery allows LSS Mills to produce yarns that meet the stringent standards of the world’s leading textile manufacturers.
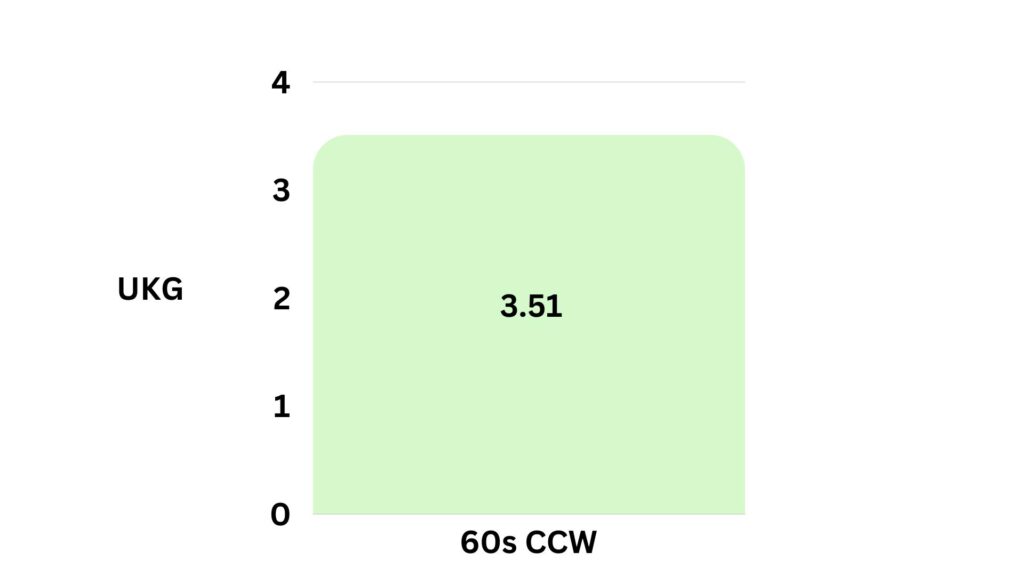
Moreover, LMW’s technology has enabled LSS Mills to pursue sustainable manufacturing practices. The energy-efficient machines align with LSS Mills commitment to renewable energy that take the form of investments in wind and solar power. This synergy between machinery efficiency and sustainable energy sources has helped LSS Mills to reduce its carbon footprint while maintaining high productivity.
The association between the two companies goes beyond a typical supplier–customer relationship. Described as a family bond, this strong relationship has fostered trust and collaboration, leading to continuous innovation and enhancement in both LMW’s machinery solutions and LSS Mills operations.
LSS Mills success with LMW machinery has placed them in the limelight in the industry. The company frequently hosts visitors who come to witness their world-class quality and efficiency as well as to see firsthand the level of automation they have implemented. This recognition serves as a testament to the effectiveness of LMW’s solutions.
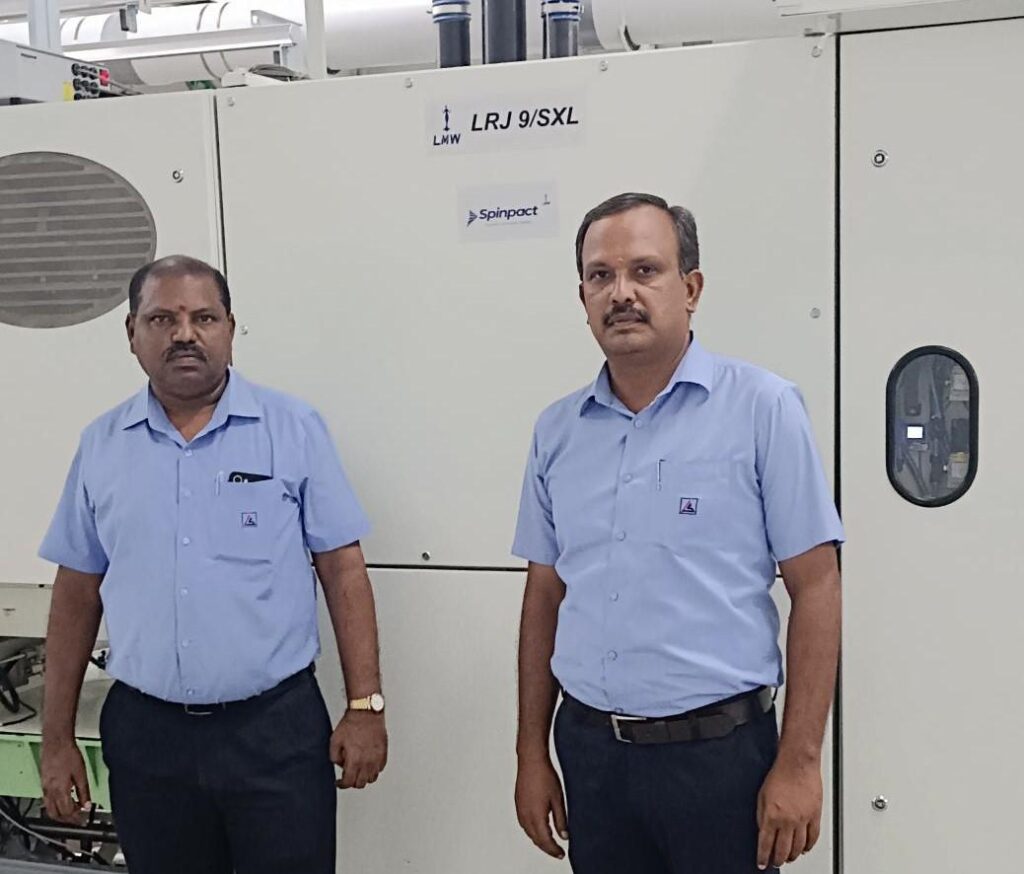
Mr. K. Nagaraj, GM, and Mr. S. Kesavamurthy, DGM, LSS Mills, vouch for the efficacy of LMW machines and affirm that they “have significantly boosted productivity with their advanced technology and reliability.” They assert that “the automation features have streamlined operations, reducing manpower and maintenance needs. Their support and innovation make them an invaluable partner for our mill.”
In conclusion, the partnership between LMW and LSS Mills exemplifies how cutting-edge textile machinery can drive a manufacturer’s success. LMW’s comprehensive range of equipment, coupled with their exceptional service, has empowered LSS Mills to achieve world-class quality, optimize their operations, and set new benchmarks in the textile industry. As both companies continue to innovate and grow, their collaboration serves as a model for success in the evolving landscape of textile manufacturing.