Increased focus on automation and energy efficiency
Lakshmi Machine Works Ltd. (LMW) is a name that needs no introduction. One of the top global manufacturers of textile machinery, it has consistently been raising the bar higher. The company has been catering to the domestic and export markets with its range of world-class products.
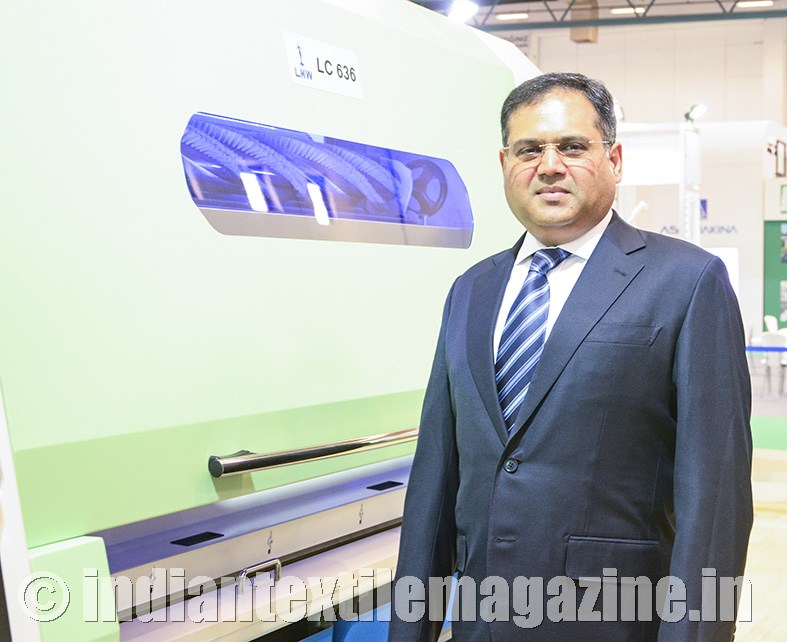
The bedrock of LMW’s success story has been its strong focus on research and innovation. State-of-the-art manufacturing processes and attention to detail, ensuring adherence to stringent quality standards, coupled with excellent aftersales support services, have seen the company grow from strength to strength.
In an exclusive interview, Mr. Sanjay Jayavarthanavelu, Chairman and Managing Director of LMW, under whose leadership the company has initiated a slew of new initiatives, spoke at length about the recent performance of the company, its new launches, what makes its products special, steps to enhance customer experience and in general about the health of the textile industry.
Here are the edited excerpts.
Expressing his satisfaction over LMW’s performance in 2017-18, Mr. Sanjay stated the year was a successful one for LMW and that the company has lived upto the expectations of the market. Going into the reasons for the good performance, he explained: “Being one of the few manufacturers of the complete range of spinning machinery, LMW was able to cope up with the market fluctuations and changes. Spares and other add-on services too saw higher growth. In 2017-18 LMW has contributed to the market to a great extent in terms of sophisticated technology too.”
Mr. Sanjay felt that in spite of the volatility of the textile market in 2017-18, LMW was in a position to serve its customers in a better way, thanks to its strong R&D and market-driven approach.
“We have successfully launched a new model auto-leveller draw frame LDF3 which caters to all segments, including OE applications. Also, LMW introduced new model Speed Frame LF4280 with maximum 280 spindles. Both these products which were well received in the market contributed for a major portion of the sales,” he said.
Happy on the export front too, Mr. Sanjay said that LMW has shown a growing trend in exports in 2017-18 as compared to the previous years. The highest revenue was obtained from exports to Bangladesh, followed by those to Indonesia, Pakistan and Vietnam, where the company’s current focus is on.
Continuing on exports, LMW had been in the news recently with the Rivatex project in Kenya where it has helped modernize a spinning mill. Asked about the project, Mr. Sanjay said: “The project is both of expansion and modernization in nature for its upstream machines. We are partnering Rivatex in expanding its product range. The turnkey project is viewed from the employment generation and imports reduction perspective. We are looking forward for installation of 16,800 spindles in this project. Yes, there are similar projects lined up and engagements will start in due course of time.”
New products
Highlighting the key new developments and innovations, at the product level last year, Mr. Sanjay observed: “We as a company have strengthened our R&D activities and the new products and innovations rolling out of our factories each year testify to the same.”
The new products include:
LDF3 Draw Frame: The gearless drive system equipped with duo digital, high accuracy auto levelling system, auto piecing, less maintenance mechanism, etc., which contribute to higher production and high sliver quality output
LF4280 AX: The world’s largest speed frame with auto doffer with a maximum capacity of 280 spindles supported by its unique dual drive mechanism
LRJ9SX: The smart ring frame driven by motor directly eliminating change gears and capable of producing a variety of yarns like compact, slub, multi count and multi twist.
New compact system: The company has also released a new model suction compact system which caters to the requirements of top-end spinners to process top-notch quality compact yarn with less energy requirements.
Sometime back LMW had unveiled solar-powered ring frames. When queried on the update on the project and whether there have been any commercial installations, Mr. Sanjay said that the solar-powered ring frames developed are for Government projects. “We have still not taken it to the commercial space. We are looking forward and the decision will be taken for further development post analysing the market demand.”
Industry 4.0
The global engineering industry is moving towards Industry 4.0 which is primarily focused on automation and data transfer. Responding to LMW’s preparedness to meet the Industry 4.0 standards, Mr. Sanjay explained: “Industry 4.0 creates what has been called a ‘Smart Factory’. These are the technological digitized solutions that ensure productivity and optimization of the resources. The growing market trend is to adopt Industry 4.0, and our global outlook has enabled LMW to synthesize the technological needs of the spinning industry. During the year we have focused mainly on automation and energy saving solutions. Some of the offsprings of our Industry 4.0 initiatives include the following.”
Spin Connect
This is a web-based monitoring and control application where the data can be accessed remotely. A data alerting mechanism is also incorporated in it. Data regarding the specific parameters and health monitoring of the machines in running conditions can be obtained and appropriate action taken accordingly. This real-time information obtained could be used for various analysis purposes. The notification-enabled dashboard lets enables customers to have a complete control over the machines.
Yarn Breakage Sensor (YBS): Individual monitoring of spindles provides signals to the operator in case of breakage. The YBS helps in improving performance of the ring frame by providing timely details of sick spindles.
Roving Stop Motion (RSM): This, along with YBS, will ensure smooth working of the machine. RSM sensors will stop the roving feed in case of any yarn breakage sensed by YBS, thus avoiding lapping of rollers and reducing pneumafil/roving waste.
Roving Transport System (RTS): Automatic transportation of bobbin from speed frame to ring frame based on the requirement. This saves a lot of manpower and delivers consistent quality due to less manual handling of bobbins.
Lap Transport System (LTS): Lap being produced by lap former is automatically transported to the comber based on its demand. This reduces manpower, inventory cost (since lap trolleys can be avoided) and improves the quality of the lap.
The company has executed some major projects in recent times. Going into details, Mr. Sanjay commented: “A number of projects have been executed in the Gujarat and Maharashtra region. Apart from the complete projects, we also have executed modernization/expansion projects for many major customers in South India, Delhi and Ludhiana zones.”
Spinning industry
There have been voices being raised within the industry that there should be a cap on further investments in new capacities. Sharing his views on the topic, Mr. Sanjay remarked: “Yarn production, its requirement in the market and its profitability are historically cyclical in nature. It depends on many factors, starting from raw material to trade policies between countries or regions. Hence we cannot attribute the subject of profitability only to capacity of spindles in India.”
He added: “The subject of spindle excess capacity in India to be viewed in conjunction with the yarn demand for the domestic and global markets. India with self-dependent on raw material and with strong capability and expertise on yarn spinning, needs to cater to the global requirements of yarn. Also, with the recent development of the post-spinning industry bolstered by the support of Government policies, yarn demand for domestic consumption will increase steeply. The phenomena of looking at the current situation as due to excess spindle capacity will soon change and India will take a lead role in catering to the global requirements.”
Competitive edge
India has become a hub for manufacturing spinning machinery with all major global players well entrenched with their local manufacturing and component supply base. Given this scenario will LMW continue to remain competitive and stay ahead? To this Mr. Sanjay replied: “It is true that the competition is getting stiffer with many foreign players entering the market. With a huge volume being handled as a market leader and with the kind of ecosystem that the company has created over a period of five decades, LMW is always in an advantageous position to supply the industry with superior technology machines at an affordable cost. Adding to this, the focus we maintain on aftersales, technical support, spare parts, service and other value-added support have always helped LMW to be a preferred supplier.”
Continuing on the subject and adding an extension to the earlier point, his views on the fact that with the spinning industry becoming so competitive and yarn margins dwindling, how does LMW ensure profitability for its customers? Mr. Sanjay responded saying: “With technology being the core value we offer to the customers, LMW machines are engineered to perform with lesser moving mechanical parts. Also, highly efficient electrical drives and superior technological parts have enabled the customer to produce quality yarn with lesser price and maintain the operation with lesser running costs. This unique value proposition offered by LMW to its customers has always kept the spinners ahead of their competition to meet their market needs.”
Focus on allied solutions
One of the recent strategies adopted by LMW to stay ahead of the curve has been to position itself as a one-stop solution for its customers by offering allied solutions like OHTC, BTS, etc. Pointing out the key reasons behind the strategy he said: “As you have already mentioned, LMW wants to provide the entire range of machinery and equipment to the customer. Advanced technologies are being adopted in the modern-day textile machinery, which in turn leads to higher production rates, greater perfection in quality and stringent delivery standards. Apart from the textile machinery with higher standards, the quality of the allied equipment too plays a major role in practical operation and customer satisfaction. These allied solutions from LMW offer enormous confidence and comfort to the customers. We are in the process of providing 100% in-house solutions for these allied services.”
In recent times, with acute shortage of labour, automation has assumed greater significance. Mr. Sanjay said: “Automation is no more a choice for the manufacturers of the Industry 4.0 generation. Being a technology adept company, we have engineered automation to a greater extent. Some of the solutions we offer include RTS (Roving Transport System), LTS (Lap Transport System), YBS (Yarn Breakage System), RSM (Roving Stop Motion), etc.”
Innovation-driven growth
LMW has launched an e-portal for online ordering of spares. Going into details of the service, Mr. Sanjay pointed out that LMW wants to support its customers in every possible way. The e-spares portal launched enables the customer to have direct access to the LMW spares team. This includes round-the-clock 24X7 login facility that ensures immediate and automated booking of the spares required. Also provided is the order tracking mechanism. Additional customer support comes with upgradation kits that enhance machinery technology for achieving higher productivity/quality.
There are also some other initiatives taken by LMW in making customer service more effective. Highlighting these initiatives, Mr. Sanjay said: “LMW has recently established a direct connect with customers to meet their service requirements in time. In this connection, LMW has created a web-enabled app to register the customer needs and technical queries directly. A technical support centre with a team of experts has also been formed exclusively to handle all the queries and to respond with action. At the field level we have more than 250 trained service professionals placed region wise to ensure maximum uptime of the machines.”
LMW has also been working on innovations in spinning different types of yarn in their machines. Elaborating on the innovations, Mr. Sanjay stated: “Our R&D has worked immensely hard to produce machines that will cater to wide range of applications, incorporating total flexibility in the yarn manufacturing process. The yarn types which can be produced by our machines include compact yarn, SIRO yarn, slub yarn, short slub yarn, multi twist yarn, multi count yarn, core yarn, etc.”
Crystal ball gazing
Mr. Sanjay sounded positive about the prospects of the Indian textile industry in 2018-19. He said: “The year 2018-19 will witness a major transformation in downstream industries like weaving, knitting and processing. This is evident from the rate at which the addition and modernization of the post-spinning machines is happening in the Indian textile industry. Many State Governments have encouraged investments in the post-spinning industry with the intention of entire value chain development. They are also viewing investment from the employment creation perspective. This trend will help in increasing the domestic yarn requirement, and hence we expect more fresh investments in spinning to continue.”