The cherished association between Aarti International Ltd. and LMW spans over 2 decades. The vertically integrated textile company located in Ludhiana (Punjab), India, manufactures 100% cotton compact, PC blended compact prima/fusion prima and fancy yarns.
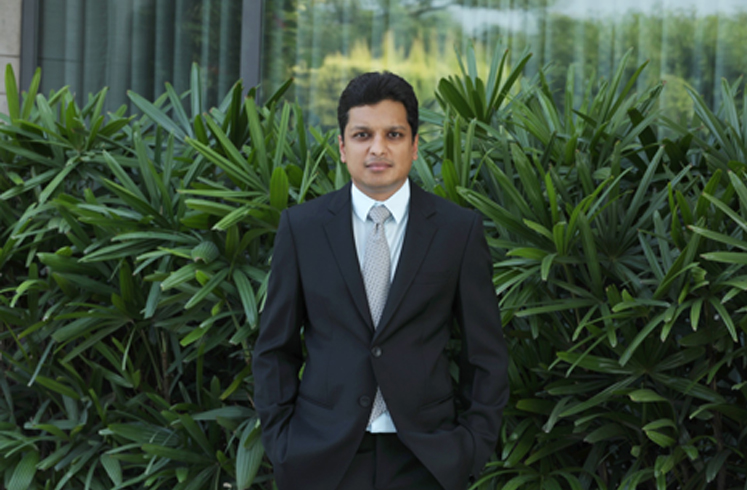
Established in the year 1996 with 28,000 spindles with 100% LMW machinery from Blowroom to Ring frame, the company has emerged as a global player with an installed capacity of 1,78,512 spindles. Aarti International Ltd. is a vertically integrated textile company with manufacturing facilities of 45000 tons Greige Yarns & 10000 tons knitted, Dyed & Printed Fabrics annually and serve both the domestic and major global markets. Some of the renowned customers include H&M, Ralph Lauren, Disney, Levis, Puma, Adidas, Tommy Hilfiger, etc.
Partnering the Technology Leader for Sustained Growth … Benchmark Productivity in Polyester / Cotton Compact application
“Our association with LMW is very long and dates back to the 1996’s. When we planned to put up a spinning plant, after thorough evaluation, we decided to go ahead with 100% A – Z, LMW project based on the deliverables it offers. The Unit 1 with 28,000 spindles was established in the year 1996 at Ludhiana,” shared Vinayak Mittal, Managing Director, Aarti.
With two years of endless efforts and several trials on compact machines and further extending the development to latest compact technology from LMW and Uster Quantum 4.0, we are able to benchmark the PC yarn quality and successfully launched Aarti branded product “Prima” PC compact yarn.
Achieving benchmark productivity through modernization of Ring frame
Unit No. 2 was with 28,704 spindles running 13 nos. LR6/AX and 13 nos. LR60/AX ring frames of 1104 spindles each producing 18 MT of 20s P/C, 24s P/c, 30s PCCH and 40s PC yarn. Mills planned to modernize their ring frames with higher spindleage and with link coners to improve the productivity and decided to replace the machines with the latest model Smart Ring frame LRJ 9/SXL machine with inbuilt suction compact spinning arrangement.
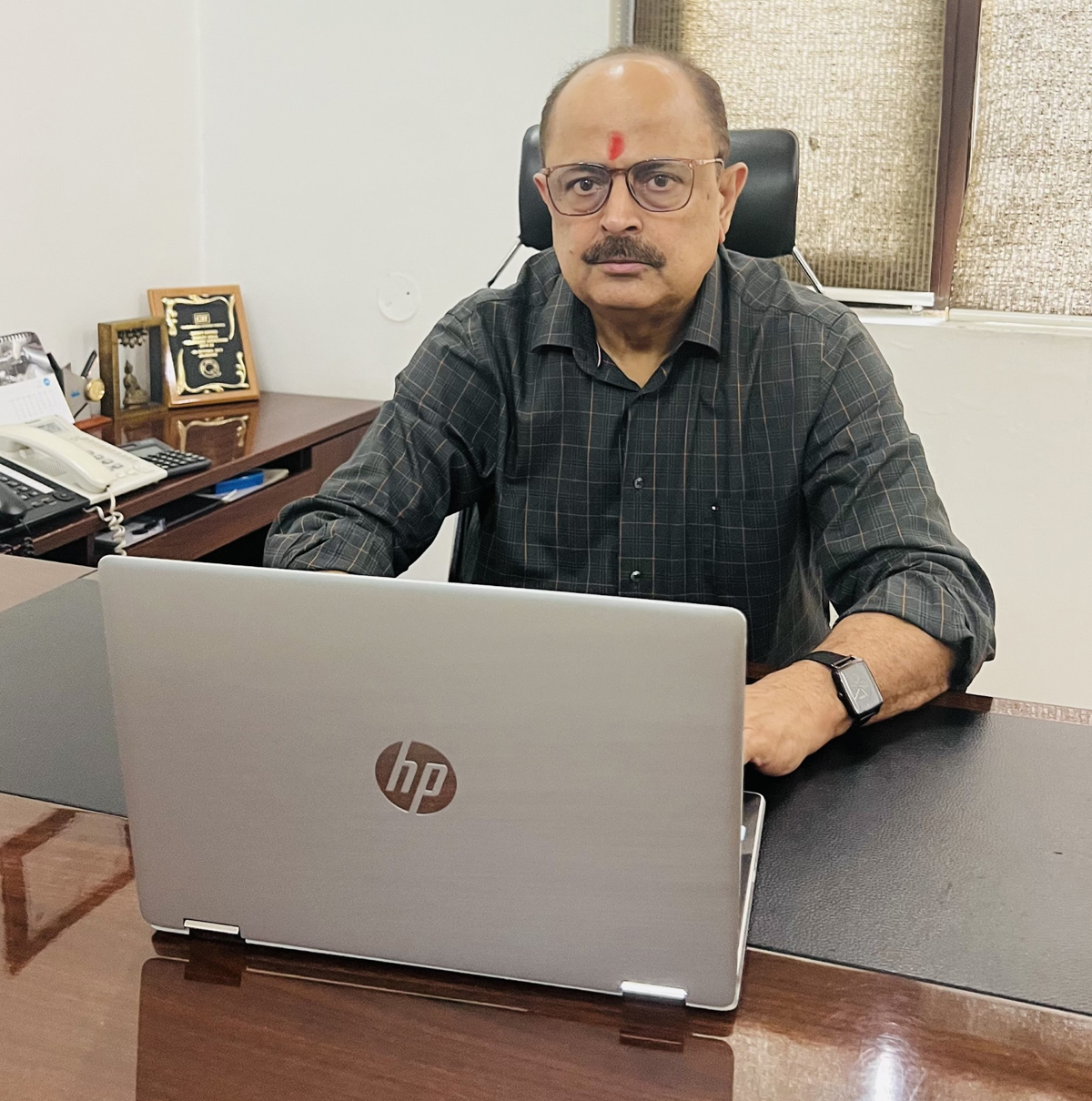
“When we decided to modernize our Ring frames at Unit 2, the only machinery that came into our mind was the latest state-of-the-art Ring frame LRJ 9/SXL model from LMW. The technology and the innovative features that were inbuilt in the Compact Ring frame LRJ 9 model were the best in the industry”, says Mr. Vinayak Mittal.
During Modernisation the 26 nos. existing Ring frames were replaced with 22 nos. Ring frame LRJ 9/SXL model of 1632 spindles each. The overall spindleage increased to 35,904 and the total output of the plant increased to 28 MT, an increase of 10 MT through increase in GPSS for various counts along with remarkable savings in Power, Manpower, Hard waste and Space, etc.
“Modernisation is the foremost factor for enhancing the global competitiveness and it is required to increase production, reduce cost, rationalize labour in various operations, reduce maintenance and adopt to energy efficient practices. In-depth analysis was carried out on the features and deliverables of Compact Ring frame LRJ 9/SXL. The machine was excellent on all the above parameters and our Unit 2 was modernized with the Smart Ring frame and all our expected deliverables were achieved with ease”, noted Mr. Surinder Kumar Mahajan, Director.
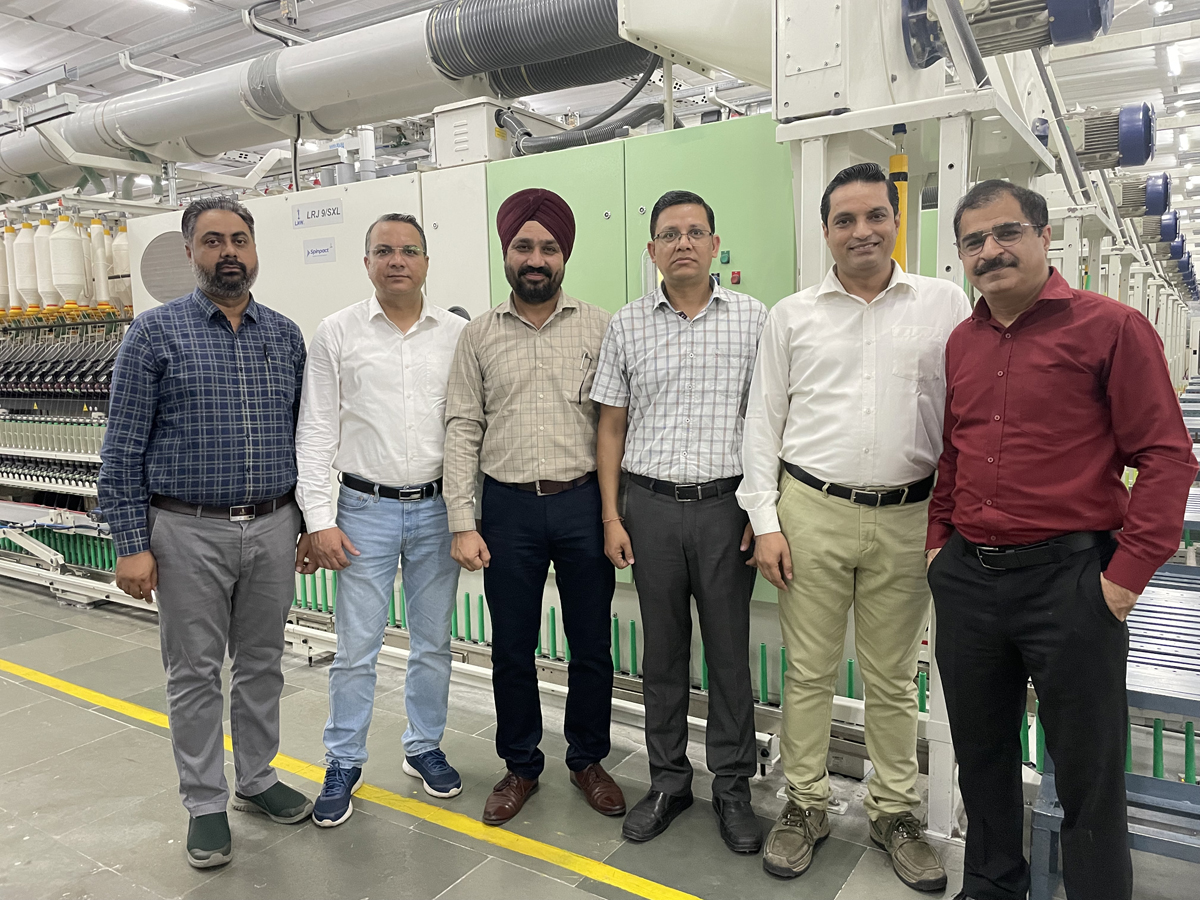
The versatile Ring Frame LRJ 9/SXL is with integrated Suction Compact Spinning and suitable to link with auto winding machinery. The machine is suitable to process a wide range of applications including recycled fibers ensures spinning success to customers. The benchmarking compact system ensures optimum spinning quality, while the compact roller’s simple drive system and the HPM (High Performance module) facilitate ease of operation. The Uni-compact nozzle made from a specially alloyed aluminium, the Direct Loading System (DLS) and unique top-suction arrangement ensure consistent quality.
The benefits derived out of this execution have been enormous:
- Productivity Improvement: With the state-of-the-art smart ring frame LRJ 9/SXL, the maximum spindle speed was at 21,000 rpm. This has led to increase in productivity (GPSS) across all counts from 18 to 22%, the maximum for Counts 40s PCCH @ 21.4%. The total productivity increased to 28 MT (higher by 10 MT) due to increase in total spindleage and GPSS.
The productivity levels achieved for various counts are:
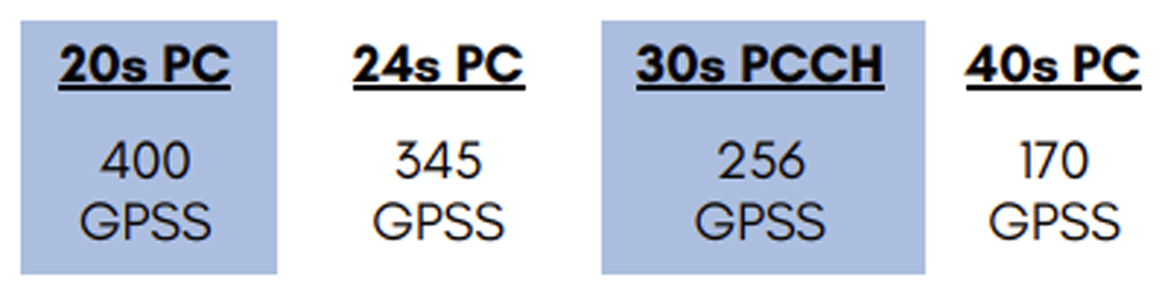
“The production levels achieved are the best in the industry and sets an example / standard for the industry”.
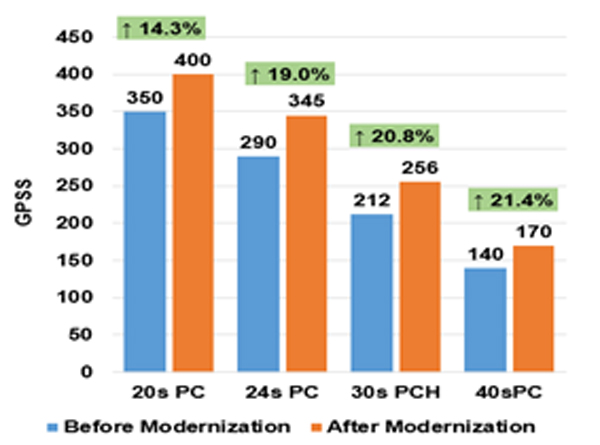
- Power Savings: For average Ne 30s P/C, at higher production rate the units consumed per kg of yarn delivered by the smart ring frame was only 1.3, a reduction of up to 15% from earlier consumption of 1.5. This has led to huge savings in the power cost.
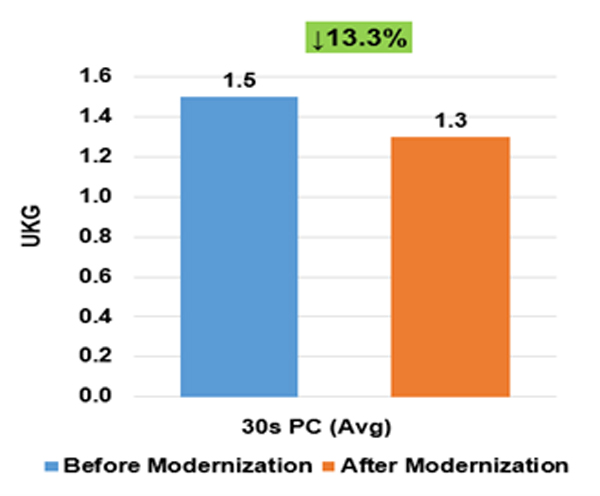
- Manpower Reduction: Manpower reduction of about 30% was achieved due to the modernization of the ring frames & Link Winders. The total personnel requirements were brought down to 157 from earlier employed levels of 223 even with production increase of 10 MT/Day leading to substantial reduction in manpower requirements and man power cost.
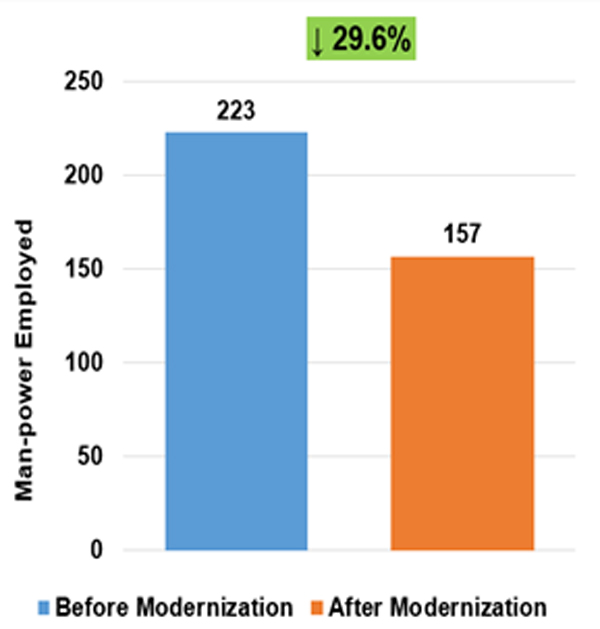
- Savings in Hard Waste: The design of the technological elements has led to the reduction in hard waste levels, thus improving the yarn realization. The hard waste generated has been reduced to 0.35% from 0.65%, thus resulting in hard waste reduction of up to 45% with the modernization of Ring Frames and Latest Winders.
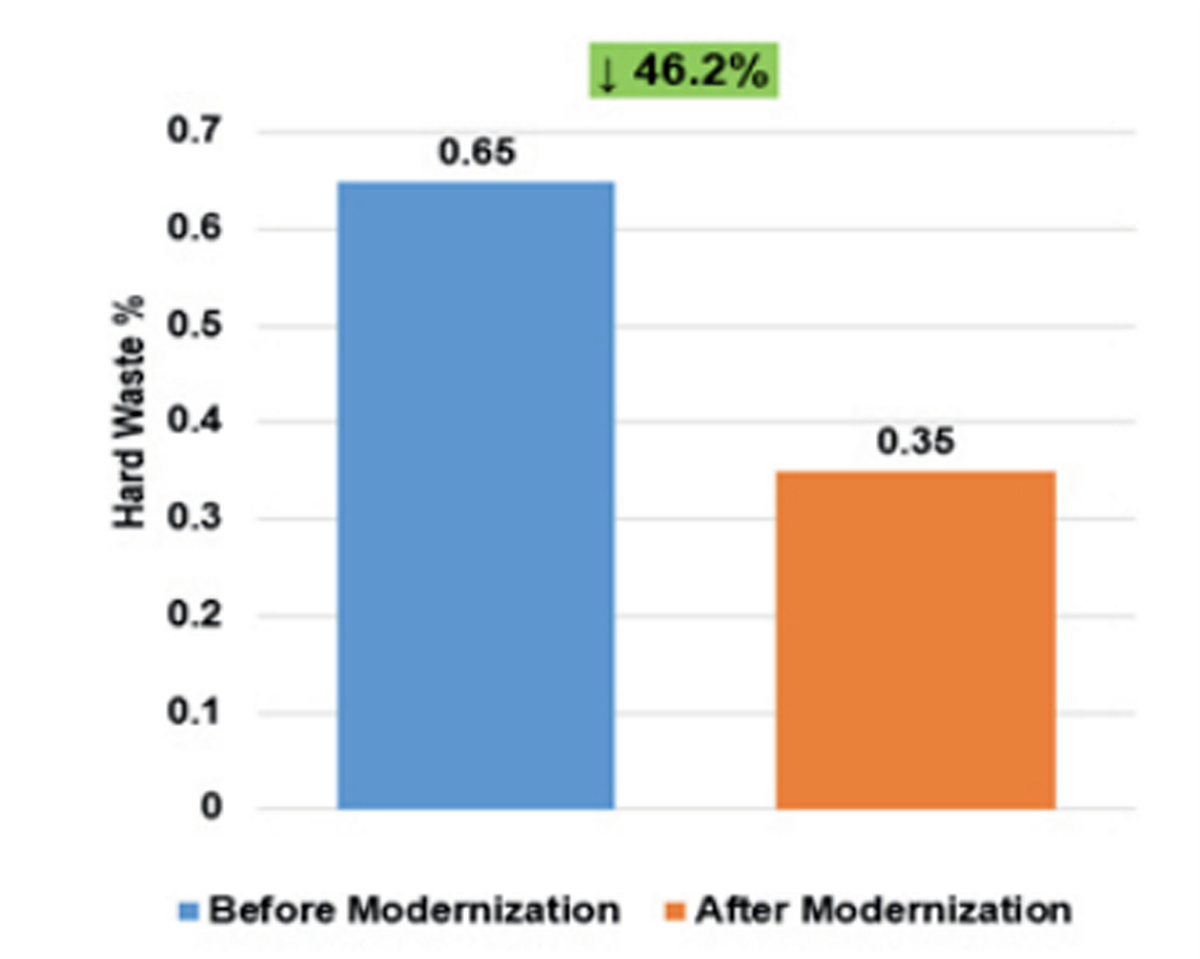
- Effective Space Utilization: The 26 nos. existing Ring frames with a spindleage capacity of 28,704 along with standalone auto winding machines has been replaced with 22 nos. Ring frame LRJ 9/SXL model of 1632 spindles each with link coner attachment. The overall spindleage has been increased to 35,904 under the same shed. An increase of 7200 spindleage. Also, the C-to-C distance has been placed at 2.4 mtrs in order to accommodate Ring frame Auto piecing (RAP) in the future.
The increased productivity with consistent quality, power savings, manpower reduction & manpower cost savings, reduced waste, and other benefits, ensure quicker Return on Investment (ROI) for the capital employed. The ROI is achieved within quickest span of time thus enabling the customer to spin success.