Globalization has facilitated the entry of various industries that have over the years revolutionised the Indian markets. LACOM is a laminating and coating machines manufacturer known worldwide for its competence in the development and production of laminating and coating systems as well as robot-aided processing and processing solutions. It produces these machines for a variety of industries and applications. It had its humble beginning in a small village called Lauchheim in the southern part of Germany, with just five members almost 27 years ago. Now, the company runs most efficiently, thanks to the commitment of its 50 members who have taken the company profits from just one million Euros to a huge 15 million Euros today.
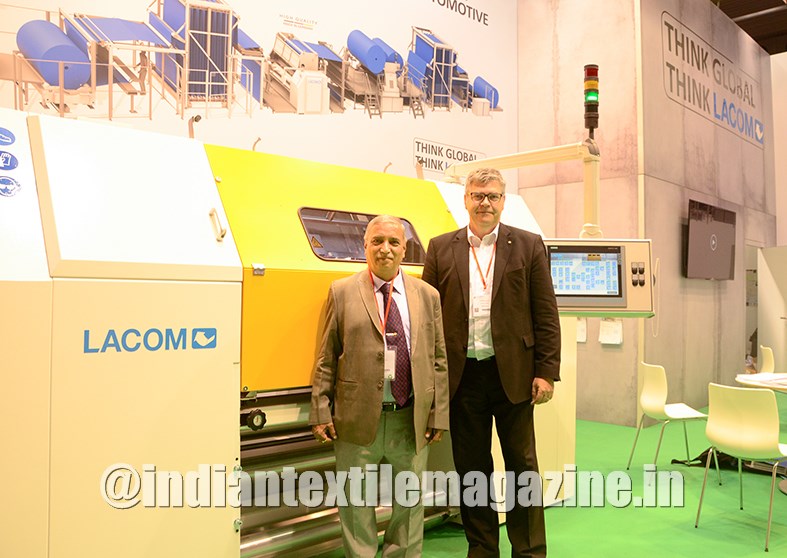
At Techtextil 19’ held in Frankfurt in May last, we met Achim Schaile, Sales Director at LACOM, who gave us an insight into the working of the company. The German manufacturer has an exceptional portfolio of products under its wing. It produces all kinds of lamination and coating machines used in different fields of coated and laminated products such as in Hometech, Sporttech, Packtech, Medtech, Indutech and, most important, technical textiles.
The LACOM multi-purpose laminating and coating machine is a most popular one sold across the globe. It is compact and economical with a design strongly based on research and feedback from customers. The Multi Roller System is used to hotmelt the back coating of carpets up to a whopping 5.2 mts. width. The Scatter Coating System is used to scatter powder adhesives evenly and with precision. The Dispersion Coating and Laminating System is strongly supported by the Doctor Blade and Bars, Slot Die and Multi Roller applicator. The machine releases no thermal effect while being used, which therefore leads to no shrinkage due to the heat produced, change in color or any other unwanted influences to the substance.
The minimum width of these machines is 500mm which can be easily adjusted in millimeters to the maximum working width, in just a couple of seconds. The machines do not make use water and solvent materials. This completely eliminates the need for using any dryers, and as a bonus, also has great environmental benefits. All these factors, along with a state-of-the-art control panel with precise settings and controls, makes human intervention limited and saves a lot of time and capital.
These machines are used for industrial applications such as nonwoven filters, abrasive papers, roof protections, and more. Such resources play an important role in textile processing. They even cater to the automotive industry by providing the machinery to make car carpets, headliners and side and front panels. Apart from this, they also deal with fission leather, natural leather and knitwear and are providers of all combinations for the nonwoven textiles market.
Asked how important LACOM thinks the Indian textile market is, Achim responded positively: “It’s always important. We head there every year since we started in India.”
The segment rapidly growing in the Indian technical textile sector is the coating and laminating textiles. In fact, an estimated growth of 8-12% has been forecast for technical and functional textiles in India, and this is something that LACOM as an industry leader has been observing. It has been in association with DN Associates in India since it saw the budding growth in the country’s textile industry. It has now been selling machines to the nation for more than a decade, successfully catering to the requirements of imported machine manufacturers, specifically the lamination coating industry. The reason behind this is simple. There is a big rise in demand for more profitable and value-added applications and products by the traditional textile producers.
The recent environmental conscious shift too contributes to the sale of more hotmelt machines as they do not use water and solvent-based substances to coat and laminate fabrics. In fact, this even removes the hassle of using dryers. So environmental reasons, focus on lower energy and the need for reduced labor costs are trends that LACOM has carefully observed and acted on, thus managing to make its own space in the local market. There are currently nine LACOM lines installed in the country, with their clients majorly being leading producers in the textile world and institutes.
To further prove how important the Indian market is to the lamination-coating manufacturer, LACOM gives top priority to aftersales services for customers. A service team is always ready at its German headquarters to solve any and all the problems of its users. An agency office has also been set up in India that immediately delivers spareparts if the need arises. Such careful precautions are indeed commendable and definitely a must when serving top businesses like Global Textile Alliance, PSG and Zen Linen (Chennai).
Like any other company, LACOM’s vision for the future is to step up the turnover, but along with that, it also wants to reach out to more areas such as the US. It also plans to remain a pioneer in advancing technological developments in the industry.