Creates new benchmarks in the processing and finishing technology
Kusters Calico is a one-stop source for textile processing and finishing machinery for various woven and knitted fabrics. The company designs and manufacture machines for de-sizing and singeing, bleaching both in single and double-stage steamer, mercerizing, washing, dyeing in cold pad batch, pad steam and also dewatering in its wide product portfolio
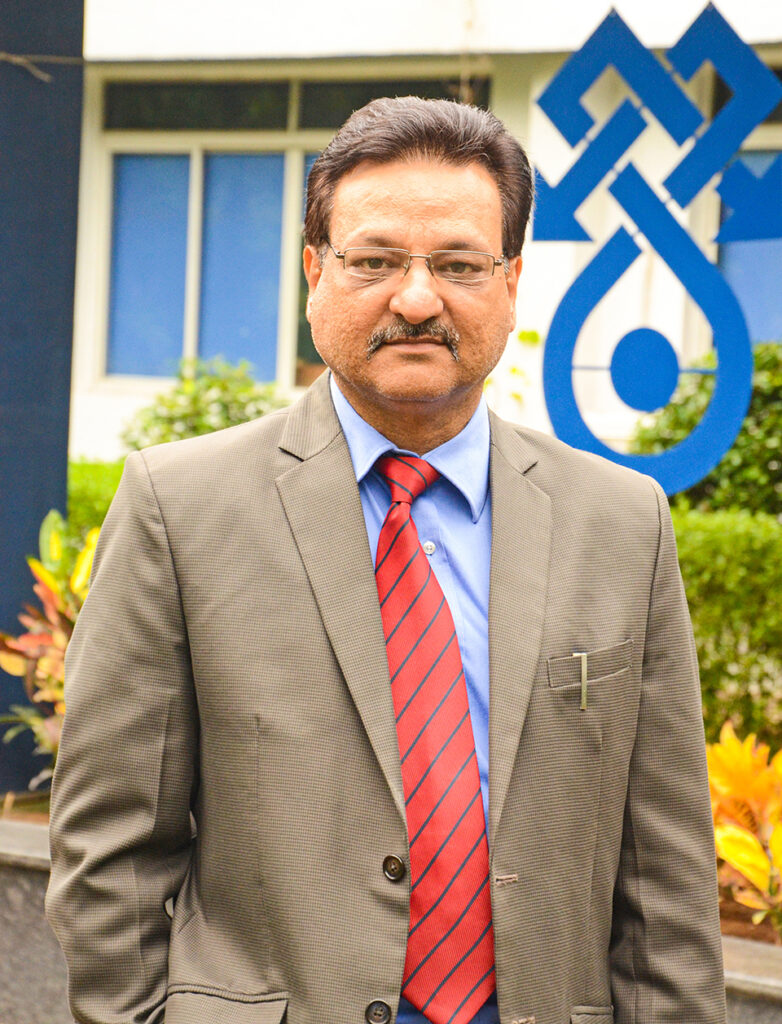
The eventful journey of Kusters Calico started in 1996 as a joint venture company between Eduard Kusters Maschinenfabrik GmbH & Co. KG (EKK) of Germany and Calico Industrial Engineers (Calico) of India with Kusters holding 70% shares and the balance by Calico. Kusters, Germany wanted to start manufacturing of textile wet processing machinery in India for the Indian industry and for exports. The company purchased 42 acres of land and established one of the best machinery manufacturing workshops in India with all machines imported from Germany. This year the company has completed 25 years of its manufacturing activity in India and is celebrating its Silver Jubilee Year 2021.
In an exclusive chat, Sushil Verma, Managing Director, Kusters Calico, revealed that while the company had to face certain challenges due to the ongoing pandemic in FY 2021, the overall performance was good. “The year 2020-21 was full of challenges. By February 2020 we had booked enough orders that could have been executed in 2020-21 but suddenly the corona virus pandemic in March 2020 disrupted the production for nearly 2-3 months. Many customers wanted us to delay the machine production but slowly all orders were revived with revised delivery schedule,” he says.
“We had to gear up and managed to complete the revenue target by running all three shifts and additional manpower. Overall, the performance was good in terms of top-line and bottom-line achievement,” he adds. Speaking about the solutions it offers to the market, Verma mentions that Kusters Calico is a one-stop source for textile processing and finishing machinery for various woven and knitted fabrics. The company designs and manufacture machines for de-sizing and singeing, bleaching both in single and double-stage steamer, mercerizing, washing, dyeing in cold pad batch, pad steam and also dewatering in its wide product portfolio. It can supply all machines from 1,800 mm to 3,200 mm working width.
Significant Inroads
The company has made significant inroads into the Indian market apart from expanding its export markets. “In India our market share is continuously increasing. Recently we supplied three lines in the Bhilwara market apart from entry in the Dombivli market. Kusters Calico has very good export market and we export nearly 65-70% of textile machines produced by us. Recently we have taken orders from Turkmenistan, Uzbekistan and Pakistan. Turkey, Egypt and Germany as usual are our big markets since years,” Verma informs.
Going into details regarding the company’s Indian installations, Verma states that although it had supplied a number of continuous ranges and almost 20 cold pad batch machines to various customers in the last one year in India, the notable among them are the three continuous washing and bleaching ranges to the Bhilwara market, one washing and bleaching range to the Dombivli market, one continuous mercerizing range and one continuous pad steam range to the Surat market. Given that the processing or finishing industry was always considered a weak link in the Indian textile industry, how is this segment evolving post the pandemic? Responding to this question, Verma says, “Textile processors still do not give due importance to processing and continue to use old technology.”
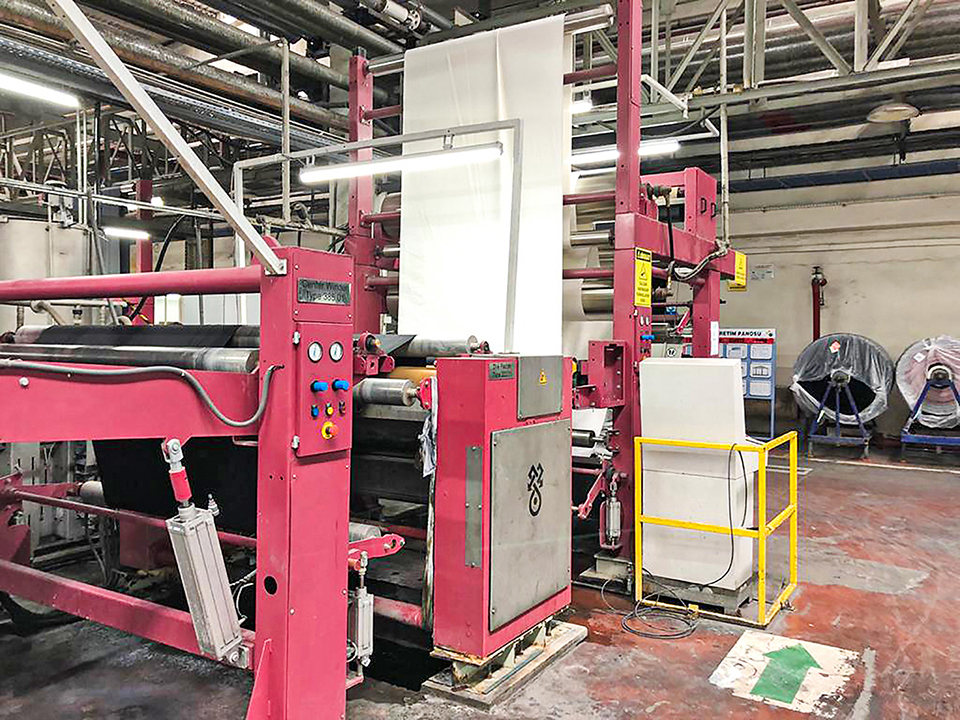
“For example, for dyeing and bleaching many processors still use jiggers. But time is changing and competition itself is forcing them to shift to continuous process technology so that over the years many process houses have shown interest and have installed machines with new technologies. Going forward this will get better as more and more process houses will understand the environmental issues related to water and energy and move towards quality continuous processing machines,” he adds. The textile finishing business is a niche segment with many global players aggressively competing for a share of business in India. Given this scenario, why should a buyer consider sourcing from Kusters Calico? “The Kusters technology in wet textile processing is well known worldwide,” Verma says.
“And Kusters Calico has further done many improvements in designs for cost reduction and better results. We have developed anti-deflection S-roll technology which reduces the residual moisture up to 15% after squeezing as compared to ordinary squeezers so that this leads to lesser steam consumption while the ‘Super Flush’ and ‘Flush Master’ concepts are already proven for efficient washing with lesser water consumption due to innovative washing concepts,” he adds. “Our swimming roll padders technology has no match even today. We use IE3 energy-efficient motors. We are going towards Industry 4.0 digitisation in our machines and soon customers will find high level digitisation in all our machines. No competitor can beat us in technology and our motto is ‘affordable excellence’. We aim to give the best machines and technology at competitive prices,” he continues.
Modern Infrastructure
The company is known for its infrastructure focus and the factory is spread across 42 acres of lush green land with 1,00,000 sq. feet covered area divided into four sheds. It has in-house design, fabrication, machining, blasting, painting, electrical panel wiring and assembly. The company started upgradation of manufacturing facilities in 2017 when a new assembly shed was constructed, new painting and blasting booths were constructed, and a new double column machine was added apart from addition and upgradation of many other machines. With the current set-up the company can manufacture machines of up to Rs 110 crore a year.
It has planned to buy a new 4 MT CNC turning this year to meet high accuracy requirements in roll manufacturing and will also obtain a 4 MT grinding machine next year. When asked to list some of the biggest achievements of the company under his stewardship, Verma says that since the time he joined the company in 2015 he has worked on many projects to improve efficiency, workmanship and quality and also upgrade manufacturing infrastructure, provide training, etc. “We have set up our own research and development unit to continuously upgrade the designs. A separate SBU of converting business was started in 2016 to give a boost to coating and lamination machines’ business,” he says.
Upgradation of manufacturing activities started in 2017. Jagenberg AG purchased 100% stake in Kusters Calico and it became a 100% subsidiary of Jagenberg AG, Germany in the year 2018. Kusters Calico added manufacturing of slitting machines in 2020 under license from Kampf, Germany a Jagenberg Group company. “Currently we are working to create a separate SBU of lifecycle services for the customers and work has started on this, which we hope will be in operation by this year-end. We would be able to offer much more to our customers like 3D view of spare parts with SAP code in machine HMI, SCADA to enable production managers to see complete machine and production data on his computer or mobile phone, machine maintenance alarms at set intervals, digital operational and maintenance manuals, remote access of machine for online service support, to name a few,” he adds.
Two-Fold Revenue by 2025
Sharing his views about the textile finishing market in 2021 and beyond, Verma mentions that textile is one of the basic needs of humans to cover the body and for fashion. The growth is definitely going to be there but in the range of a maximum of 5-8% year on year. Slowly old process houses are realising the need for shifting from old processes to new continuous ranges for less power and water consumption as environmental controls are getting more and more stringent day by day. “Today the government does not allow a process house to function if effluent treatment facility is not provided,” Verma points out. The company has clear-cut future growth plans. According to Verma, in 2020 Jagenberg AG stated the vision for the next five years i.e. from 2021 to 2025. It includes targeted improvements in the areas of company weaknesses, technology upgrade, infrastructure upgrade, new product development, skill development, supply chain strengthening, exploring markets, digitisation and sustainability. “We are also working to prepare 3D drawings for all the identified standard modules and write standard operating procedures for all the activities we do in our company, right from taxi booking to machine manufacturing. Both these activities when completed will definitely take us to the next level of manufacturing where we can deliver cost-effectively, in time and with the same quality every time. The target is to double our revenue by 2025,” he says on a parting note.