Millionth spindle handed over to Pallava Group
KTTM recently achieved a milestone of selling one million spindles of its ring spinning model RX 300. The one million spindles of RX 300 have been manufactured at its facility in Bengaluru. The machinery, with the one millionth spindle, was delivered to the Pallava Group that has recently invested in 15,000 spindles of RX 300 ring frame.
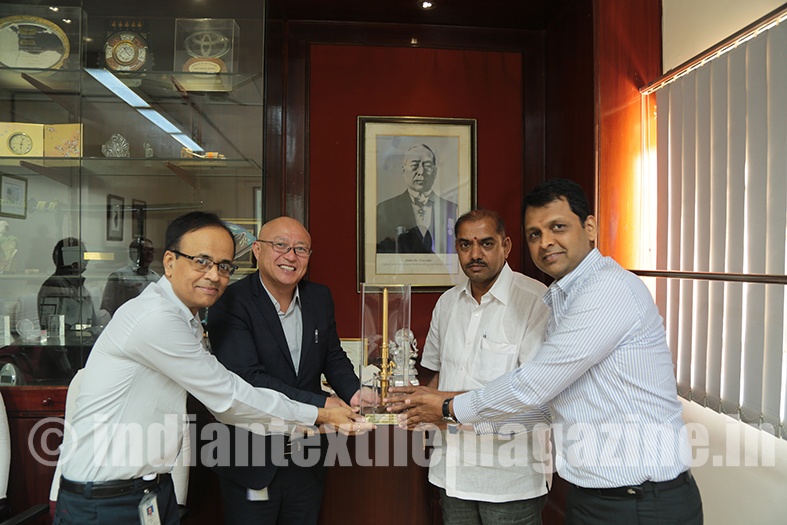
Mr. Toshihiko Shimizu, KTTM Managing Director, and his team felicitated Mr. Durai Palaniswamy and Mr. M.P. Devarajan, Directors of the Pallava Group.
The RX 300 ring frame model was launched in 2014, and within a span of less than 30 months the company has sold and installed over a million spindles worldwide. India is currently the global manufacturing hub of Toyota for ring frames. The company has exported a significant number of machines to Pakistan, Bangladesh, Vietnam, Turkey, Thailand, Brazil and many other countries.
Talking about the Pallava’s strong relationship with the Toyota Group, Mr. Durai Palanisamy said: “In 2016 we started working with KTTM. We are one of the biggest customers for Toyota Weaving machines and forklifts. Toyota being a pioneer in innovation, we wanted to explore their technology in ring spinning also. Last year we did some initial trials which were very positive and then decided to go for the first set of 10 machines. Its been good experience so far and we are working together to get the best out of the machine.
The Erode-based Pallava Group has been in the textile industry for many decades. The group has established capacity of 200,000 spindles, 50 vortex machines and 500 airjet looms. The company has manufacturing capacity of close to 150 tonnes per day of yarn production, out of which one-third goes for captive consumption, another one-third for exports and the balance one-third for the domestic market. The company has also added knitting capacity recently.
“Toyota has always been at the forefront of innovation hence our expectations are very high. We are expecting higher productivity and lower manufacturing cost, particularly power cost. Toyota has one of the best doffing systems which reduces the downtime of the machines. All these we hope will enhance our competitiveness”, said Mr. Durai Palanisamy.
Speaking to Mr. Toshihiko Shimizu, he said: “We currently have capacity to manufacturer 60,000 spindles per month. India is now the global manufacturing hub of Toyota for spinning machines. Currently nearly 75% of the machines manufactured in India is going for export market and the balance 25% sold in India. We are witnessing a growth of 8 to 10% year on year”.
Toyota’s RX Series of high-performance ring spinning frames have been very successful worldwide. The RX300 was developed in response to many customer requests for saving energy in spinning mills. The adoption of new high-efficiency motors and new pneumatic equipment ensures excellent energy-saving performance. The new long-frame design – which supports up to 1,824 spindles – employs Toyota’s proprietary technology to ensure high reliability and high performance, as well as space saving and cost-saving effects.
In addition, the RX300 also comes with options such as a compact yarn spinning device and a fancy yarn spinning device, which can be used with any number of spindles on the long frame. The RX300 MOSAIC YARN device, which is called e-Draft, creates designs by alternating one colour and the other evenly with a combination of various slub pattern. The outstanding uniqueness of the so-called “MOSAIC YARN” effect will enable the customers to create a completely new market for highly value-added spinning products. Mosaic yarn is manufactured using injection slub yarn attachment. It is double-color yarn manufactured in a single process.
Excess capacity
On excess capacity in spinning in India, Mr. Durai Palanisamy said: “Yes, there is some amount of excess capacity, But if we look at the current capacity in the industry that is modern, which can cater to current needs of high-end segment machines or customers who are looking for high quality yarns for high speed weaving/knitting applications then, I would say we are still short of capacity”.
“Today we are running our Toyota airjet loom at 1150 rpm. We cannot run any low quality yarn on these machines. To achieve 96% to 97% efficiency you need to have the best technology. In that scenario I feel we are still short of capacity. For sure, modernisation has to happen. More and more high speed machines are coming into the market. Over capacity will affect the industry in someways but an investment in modern technology will not be a wrong move”, he added.
“In spinning there is a huge technology gap between machines that are even 10 years old compared to the technology available today. Hence modernisation and upgradation has to be continuous. We have to be innovative in terms of product, finding new markets and embracing new growth opportunities”, concluded Mr. Durai Palanisamy.