A 10% productivity boost and improved yarn quality – this is the success story of KPR Mill Limited after upgrading its Bräcker TITAN rings with ORBIT. In addition, the company profits from reduced machine downtime thanks to longer ring traveler lifetime. This has resulted in another win-win: increased machine utilization and enhanced operator availability.
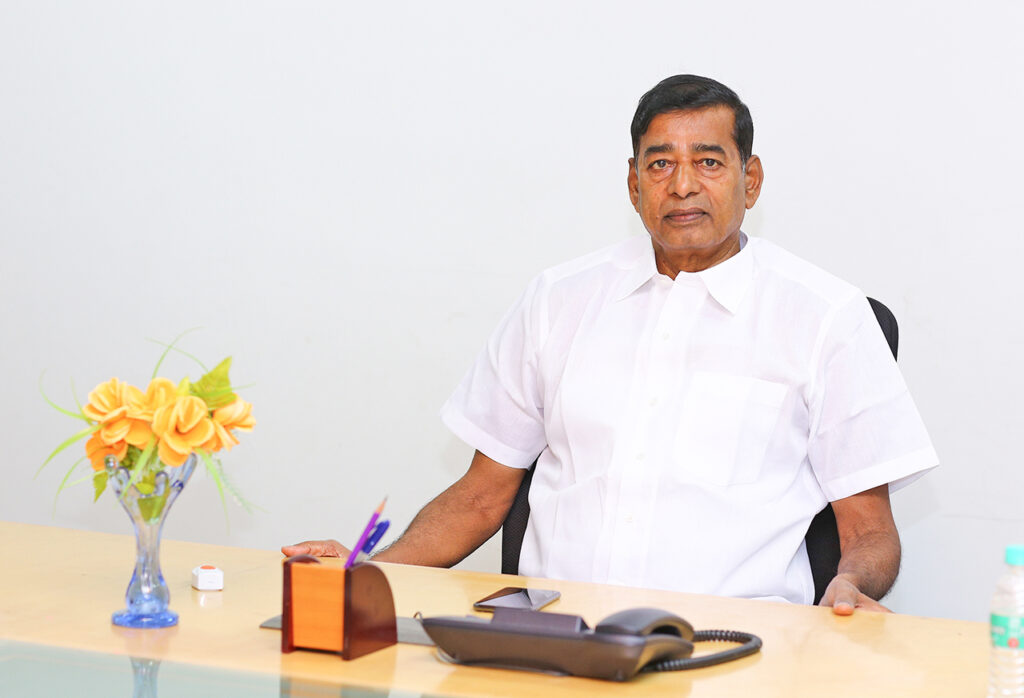
KPR Mill Limited (KPR), located near Coimbatore, is one of the largest vertically integrated public companies in India. For more than thirty years, KPR has been manufacturing an impressive range of textile varieties which are renowned for their quality among customers around the globe. Bräcker, the world’s leading supplier of rings and travelers for ring spinning systems, has helped the company upgrade their TITAN rings with ORBIT, increasing production by 10% while also achieving higher yarn quality in only six months.
The Challenge
KPR spinning mills feature high-quality equipment such as Rieter ring spinning machines G 32 equipped with the well-known EliTe compact-spinning system by Suessen and the TITAN T-flange rings by Bräcker. After ten years of service, KPR explored the option to upgrade the rings to boost productivity and yarn quality.
The Solution
KPR Mill Limited being a vertically integrated company, Bräcker saw a possibility of achieving more value for money with the ORBIT TITAN rings, by making the yarn more suitable for their downstream knitting process. The ORBIT ring is a technical marvel, firmly established in the spinning industry for more than three decades. With its large contact surface between ring and traveler, the ORBIT ring stands out from traditional T-flange rings and offers optimal heat conduction, stable yarn passage, consistent yarn quality and longer traveler life. KPR decided to test ORBIT rings for their knitting yarn application and began trials on one ring spinning machine.
The Customer’s Benefits
The original productivity and yarn quality were soon restored. To surpass them, Bräcker experts went further and optimized the shape and ISO weight of the SFB ring traveler. After six months of joint effort, production increased by 10% and a better yarn quality was achieved. In addition, machine downtime was reduced thanks to longer ring traveler lifetime. As a result, the machine utilization percentage for KPR increased and so did the operator availability.
Within 12 months, KPR changed 50% of their existing spinning capacity from T-flange to ORBIT rings. The company is now gradually replacing their balance rings with ORBIT TITAN rings. KPR Mill is one of India’s largest vertically integrated companies with diverse businesses spanning yarn, fabrics, garments, white crystal sugar, green energy and ethanol.
With a capacity of 370 000 spindles, KPR Mill Limited produces 100 000 metric tons of cotton yarn per year. The company also manufactures 40 000 metric tons of knitted fabrics, 157 million garments and has a processing capacity of 30 000 metric tons each year.
For more than 30 years, KPR has been manufacturing an impressive product range of textile varieties and delivering outstanding quality to its customers worldwide. With the recent launch of inner and athleisure wear under the brand FASO, KPR enters the retail business as well.
“As a market leader, KPR Mill Limited is constantly pushing the limits of operational efficiency to achieve higher productivity with better yarn quality. Bräcker’s innovative products such as ORBIT rings complement our efforts to pursue excellence” – K. P. Ramasamy, Chairman at KPR Mill Limited
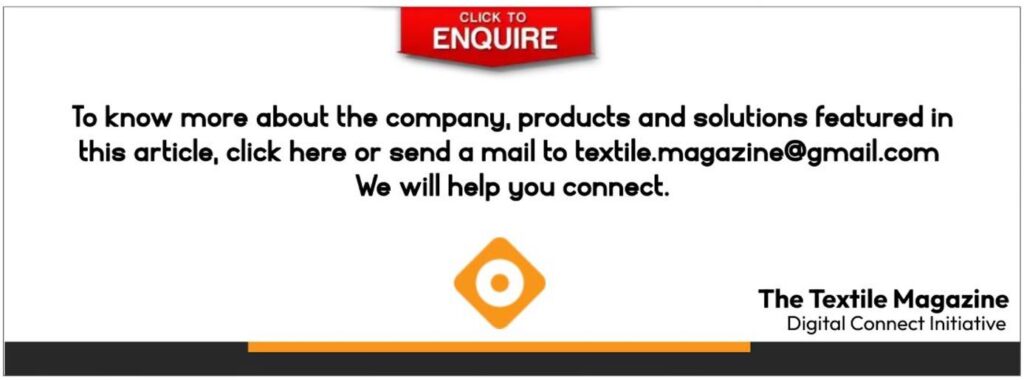