Digital textile specialist Kornit Digital showcased a broad range of applications and live system demos at FESPA Digital in Amsterdam. Two industrial-grade direct-to-garment printing systems formed the core of the company’s presence at the show. Both of them emphasized the company’s policy of a one-step multi-fabric process without pre-treatment using its NeoPigment Pure ink.
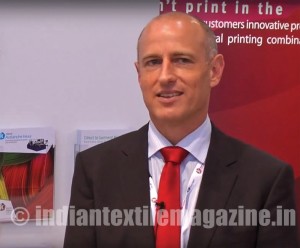
Guy Zimmerman, Kornit’s VP of Marketing and Business Development, commented: “As the textile printing market moves towards online business models and fast fashion, our customers are requesting powerful industrial systems in flexible configurations. The new systems have launched are designed for higher effective throughput and an even more attractive ROI while offering first-class print quality and process efficiency.”
Also demonstrating Kornit Digital’s improved efficiency and industry-leading color and quality, the proven Kornit Avalanche 1000 is considered its flagship model. Its 24 Spectra Polaris heads, together with all other Avalanche efficiency features, make it the ‘productivity’ configuration of the Avalanche platform which is also available in a six-color and in a digital discharge version.
Kornit also demonstrated large-format cut piece printing and optimized prints made with the recently launched NeoPigment Pure ink.
Kornit’s presence was completed with a host of high-quality samples produced on Kornit’s systems, be it garments made from a variety of fabrics or Allegro prints that were turned into home textile or fashion examples.
Oliver Luedtke, Director, Marketing EMEA at Kornit, observed: “FESPA Textile is the largest and most significant event for digital textile printing today, and we’re delighted to be Corporate Textile Partner once again. One area where FESPA excels is in educating other print sectors – be that digital or analogue – on the opportunities digital textile printing presents.”
He added: “In today’s market, vendors are still making progress in expanding the range of potential applications for digital textile, and at FESPA Textile we were fortunate in seeing solutions providing end users with expanded colourgamuts and more flexibility in terms of garments, for example, as well as the very important integration into the workflow, enabling more automation and the possibilities of e-commerce applications.”
Last year, Israel-based Kornit, which has customers in more than 100 countries, put up performance of another of its machines, the Allegro roll-to-roll textile printing system, with recirculating print heads from Fuji Dimatix to improve reliability.
Kornit Digital has been a long-standing sponsoring partner of FESPA.
Introduces Storm Hexa, Storm 1000
Kornit’s most popular product family for mid-size businesses receives major upgrade, features recirculating print heads, flexible ink configurations and significantly reduced ink consumption.
The new systems are members of Kornit’s best-selling platform of Storm systems, which, in more than 10 years, have earned a reputation as solid, robust and reliable industrial systems with high effective throughput.
The new Kornit Storm Hexa and Kornit Storm 1000 have been equipped with state-of-the-art inkjet technology to turn them into the most advanced industrial direct-to-garment printing systems for medium-size businesses. Their features include a recirculating ink system to reduce ink consumption and to further optimize reliability, as well as a doubled number of nozzles to increase productivity of up to 40 per cent over the previous Storm configurations.
The Storm 1000 is the standard configuration of the new product family and features 12 print heads in a CMYK and White configuration. It produces up to 170 garments per hour in high productivity mode, including inline pre-treatment. It covers a print area of up to 50 x 70 cm / 20 x 28 in.
The new Storm Hexa is equipped with 16 print heads and two additional colors for full CMYK, Red, Green and White support. It is the system of choice for color conscious applications such as production of promotional and brand related garments. It also can produce up to 170 garments per hour in high productivity mode.
Both systems are based on Kornit’s unique NeoPigmentTM printing process. They have advanced productivity features such as a built-in pretreatment system, a quick replace pallet mechanism, a 4 liter bulk ink system, an integrated humidity system and a back-up power system for a quick and easy system start. All Kornit printing systems are compatible with a variety of fabrics (cotton, polyester, blends, denim, silk wool, etc.) and are geared towards industrial mass-customization applications.
Guy Zimmerman, Kornit’s Vice President of Marketing Business Development, comments: “The Storm series of direct-to-garment systems have been Kornit’s signature products for more than a decade. The Storm II is the best-selling industrial direct-to-garment printing system in the market. Launching a new and improved generation of it is an important milestone for us and a great opportunity to further improve the efficiency and performance of our industrial systems. The new Storm configurations show drastically improved throughput and further reductions in ink consumption, as well as excellent print quality. They are perfect production tools for a broad range of applications.”