Klübermatic – speciality lubricants in “intelligent packages”
To attain optimum production efficiency in the textile industry, it is not only essential to select the right lubricant, but it is equally important that the right lubricant quantity is applied to the right lubrication point. Excessive or insufficient lubrication of components and installations are among the most common errors occurring in lubricant use.
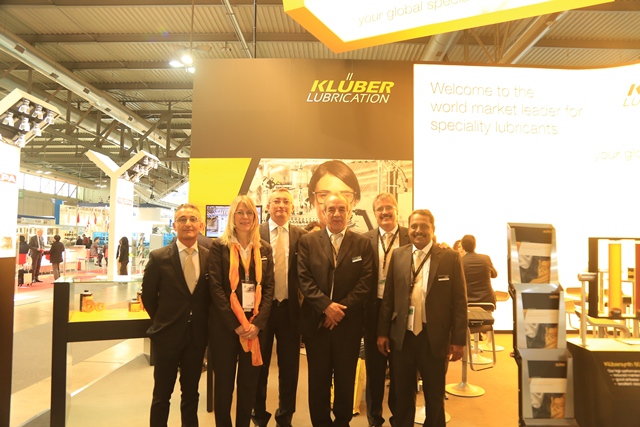
Klüber Lubrication’s automatic lubricant dispensers of the Klübermatic series solve this problem by enabling reliable and precise lubrication of friction points. The Klübermatic range, which is already well established in many industries, is now complemented by the Klübermatic Flex dispenser, a flexible lubrication unit in compact design.
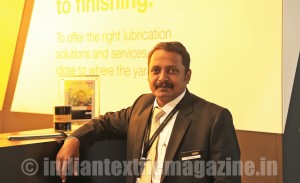
“Klübermatic Flex is clean to use and very economical. The automatic lubrication system does not only prevent overlubrication of components and hence minimise the risk of fabric contamination, but it also counteracts premature wear of machine parts due to insufficient lubrication while extending maintenance intervals and reducing production losses” explains Mr. Christian Forster, Market Manager Textile Industry Klüber Lubrication.
Automatic lubrication also provides advantages over manual lubrication when it comes to lubrication points that are difficult to access or at high temperatures and also for lubrication points that are far apart from each other. The automatic dispensing system is available in several designs which facilitate variable lubrication interval settings. Klübermatic can be used for single-point lubrication of rolling and plain bearings, slideways, open gears, toothed racks, threaded spindles, shaft seals and chains.
Higher reliability in weaving machines with less downtime
Synthetic high-performance gear oil for wear protection and higher efficiency
Weaving machines are today operated constantly under a maximum of stress. To offer the highest possible productivity under these conditions, they have to function with utmost reliability and downtime has to be reduced to a minimum. Lubricants play a decisive role in this context as they reduce friction wear to protect components against premature wear and tear. It is especially for the long-term or lifetime lubrication of sliding friction points in weaving machines that the tribology expert Klüber Lubrication has developed the new high-performance gear oil Klübersynth 80 KV.
“Utmost functional reliability, maximum efficiency and dependable machine availability contribute to a reduction of production costs in the textile industry of today. Being a vital component of any weaving machine, the gearbox must be optimally protected against wear and scuffing damage. Klüber Lubrication has developed its new polyglycol-based special oil with good ageing resistance to match this kind of application” explains Mr. Forster.
Besides its outstanding wear protection and load-carrying capacity, the high-performance gear oil Klübersynth 80 KV shows an excellent viscosity temperature behaviour supporting the formation of sufficient lubricant film even at high temperatures. Lower friction coefficients enable higher application efficiency, leading to lower energy consumption. Moreover, the excellent ageing and oxidation stability of the synthetic base oil can lead to a significantly longer service life than mineral oil-based products. This enables service intervals to be extended. Even for-life lubrication is possible in some cases.
Klübersynth 80 KV is recommended by the Italian textile machine manufacturer ITEMA for the lubrication of gears, plain bearings, needle cams and other sliding friction points in type R 9500 weaving machines made by ITEMA.
High-performance bearing lubrication for stenter frames and steamers
Versatile long-term grease with excellent corrosion protection at high temperature
The bearings in stenter frames and textile finishing machines are subject to particular high stresses arising from the operating environment. While stenter frame bearings are exposed to extreme heat over a long period, they are additionally subjected to steam and aggressive media in the finishing steamers. The new speciality lubricant Klübertemp GR AR 555 was developed to match precisely these applications. It excels not only in high-temperature applications due to its evaporation stability, but offers high-performance corrosion protection as well.
“Bearing failures are a frequent cause of costly downtime in the textile industry,” says Mr. Forster. “With Klübertemp GR AR 555, we have succeeded in developing a versatile speciality lubricant which considerably reduces bearing failure risk and significantly extends relubrication intervals.”
Klübertemp GR AR 555 is designed for use at operating temperatures up to 250 degrees Celsius and resistant to aggressive media. The white, synthetic long-term grease is based on a perfluorinated polyether oil (PFPE) and polytetrafluoroethylene (PTFE) and is neutral to most elastomers and plastics used for seals.
New special oil for high-speed knitting machines
Less residues and wear for higher production efficiency
Together with a leading manufacturer of large circular knitting machines, Klüber Lubrication has developed the new needle and sinker oil Klüber Silvertex HS 68. The new special oil significantly reduces wear and deposits on the heavily loaded, sensitive needles and sinkers. As a consequence, operation is much less liable to disruption and the need for maintenance is reduced, contributing to higher efficiency in production.
“With Klüber Silvertex HS 68, speed factors of 2100 or higher can be attained, which in a 30-inch machine means 70 revolutions per minute. Thus, a daily output of more than 1500 kilogrammes of single knit fabric is possible with this product, leading to significantly higher plant economy” says Mr. Forster.
Klüber Silvertex HS 68 for modern circular and flat-bed knitting machines is compatible with elastane fibres and commonly used synthetic fibres as well as neutral towards conventional sealing materials and plastics. The high-speed oil protects needles, sinkers, couplings, needle cams and cylinders, dials and sinker rings reliable against wear. It has been tested and approved by a leading high-speed knitting machine manufacturer.
Competence and experience – added value for customers
KlüberEfficiencySupport helps increase process efficiency and protect valuable resources
Next to a lubricant that is optimally suited for the respective application, its proper handling is also essential for efficient production. Therefore, Klüber Lubrication offers a wide range of speciality lubricants and services for the textile industry. In addition, KlüberEfficiencySupport can help protect valuable resources such as energy and water, thus helping to reduce operating costs.
“Klüber Lubrication is more than just a manufacturer of speciality lubricants. We as the specialist offer our customers a comprehensive lubrication package. Lubricant users benefit from our experience and tribological know-how and do not have to worry about finding the optimum solution for their particular application themselves” says Mr. Forster.
The services and consulting services combined under the keyword KlüberEfficiencySupport are precisely tailored to the requirements and challenges of the respective customers, far exceeding the actual lubrication issue. In close cooperation with lubricant users, the tribology experts of Klüber work on the systematic optimisation of lubrication processes in the plant. This includes services such as the development of lubrication schedules, cleaning and relubrication, general inspections as well as lubricant and component analyses. All this is aimed at the optimal utilisation of the machines and know-how of the staff.
Another important offering from Klüber Lubrication is training tailored to the textile industry sector. Besides tribology basics and the properties of oils and greases, the lubrication of machine elements operating in the textile industry is at the focus of these KlüberCollege trainings. Participants learn about the optimisation of lubrication processes, inspections and maintenance, correct lubricant application and the prevention of typical errors such as excessive lubrication or lubricant starvation.
A cooperation that benefits also others
A strong cooperation between the producers of textile machines and speciality lubricants is beneficial also for textile manufacturers
Textile production worldwide is challenged more and more by a rising need to produce as efficiently and cost-saving as possible. Key factor herein are textile machines and other production equipment running smoothly and with as few downtime as possible. To achieve this aim, besides other things, it is crucial to select the right lubricant, for the initial lubrication of a component as well as for relubrication during operation. The lubricant itself constitutes only a minor investment, but its effects can be tremendous. The lubricants used are expected to offer reliable performance over a long service life and a wide temperature range as well as good resistance to loads. For the operators, these characteristics mean long relubrication intervals for greases and long lubricant life for oils.
The OEM on the other hand can offer its customers optimum solutions when considering the impact of high-quality lubricants from the design stage. Thus, a close and intense relationship between OEM and speciality lubricant producer is beneficial for all production stages of textile production.
Partnership with ITEMA
One example for such a relationship is the 25 year-long cooperation between Klüber Lubrication and Itema, the Italian-based global leader for textile machinery, which has been showered with success in recent and distant times and for whom high performance oils have been developed. A recent successful launch was the R9500, a textile machine which is the jewel in the crown of the Colzate-based company. On its own, the machine brings in half of the companies’ total earnings. In 2014 it enabled the sales volume to leap by 60 per cent worldwide, particularly in the Far-East, China, the Middle-East, Turkey, and South America. Never has its partnership with Klüber Lubrication been so crucial.
One of the features making the R9500 such a good performer for international textile manufacturers, is its centralised force-feed lubrication system with a reservoir and double filter. This provides maximum lubrication yield and minimum energy dissipation, resulting in at least a 10-degree temperature reduction compared to the previous models.
Gears, cams, bearings and the rapier and belt kinematic system, to keep beating, the hi-tech heart of the sophisticated loom required a viscous agent capable to ensure the best gear performance. After months of testing and development, the chemists and the engineers from Klüber Lubrication, together with the colleagues from Itema, identified the ideal personalized lubricant which could guarantee uninterrupted high-speed operation. The Klübersynth KV – specifically the Klübersynth 80 KV, was the series of high performance oils for centralised lubrication designed to meet the needs of the R9500 weaving machine. With a modified viscosity, Klübersynth 80 KV keeps the operational temperature to a minimum.
By changing the oil after every 20,000 hours of operation (it has a two year warranty) and replacing the filters, Klüber Lubrication makes sure the client does not need other lubrication maintenance. Its global distribution network makes the Munich company’s lubricants an easy and profitable choice anywhere in the world, as shown by the extensive feedback obtained from the technicians of the Italian production plants and the rest of the world. The laboratories are in Munich, but the commercial services and support network of Klüber Lubrication is ready to assist in case of particular needs and customized solutions in more than sixty countries. Only balanced team work brings certified excellence.