Leading with Vision, Precision, and Integration
Since its inception in 1979, Khosla Profil has transformed from a modest polypropylene filtration fabric unit into one of Asia’s leading names in technical textiles. Founded by Mr. Pramod Khosla, a visionary first-generation entrepreneur, the company has relentlessly pursued technological excellence, vertical integration, and global outreach. With four manufacturing plants across Wada, Daman, and Ghaziabad, Khosla Profil today commands recognition for its world-class capabilities—right from chips and yarns to finished technical textile solutions.
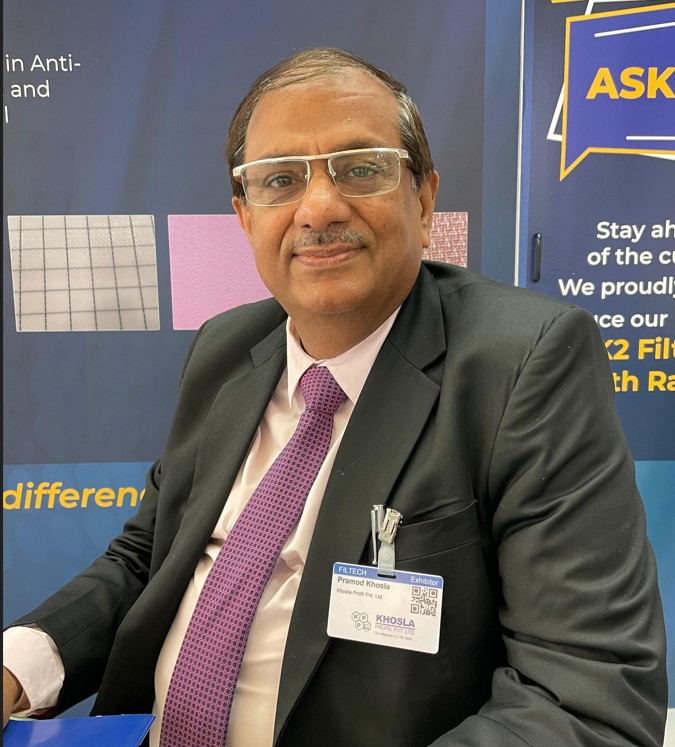
With over four decades of industry leadership, the group has continued to scale new heights by integrating backward and forward across its value chain. In a recent milestone, the company has taken a transformative step by investing in its own spinning unit, a move aimed at enhancing control over quality, ensuring timely delivery, and supporting product innovation in critical textile applications. In an exclusive interview, Mr. Pramod Khosla shares the thought process behind this decision and reflects on a year of consolidation, expansion, and renewed ambition.
A Landmark Year: Strategic Expansion and Deeper Integration
Reflecting on the past financial year, Mr. Khosla describes it as “an important year,” one in which the company took decisive steps to multiply its future growth while also strengthening its production foundation. At the heart of this transformation is the new spinning facility—a long-awaited step that gives the company greater control over raw material inputs, particularly fiber-based yarns used in high-performance filtration and technical fabrics.
“For decades, we’ve aspired to bring fiber-based yarn production in-house,” explains Mr. Khosla. “While we have been producing monofilament yarns internally for over ten years, fiber-based yarns, especially high-temperature and specialty fibers, were always sourced externally. Unfortunately, these yarns often lacked the consistency and timely availability we required, especially for critical applications.”
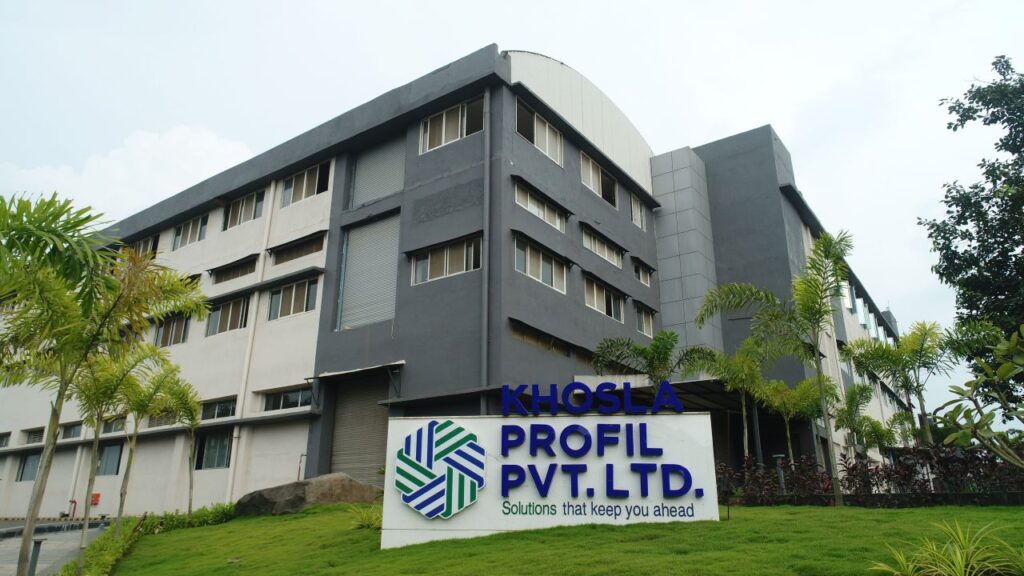
The decision to establish a spinning unit, located adjacent to their existing weaving operations, was thus both strategic and essential. Construction is well underway, machinery has begun arriving, and the first phase—featuring ring spinning systems—is expected to commence production by July. This will be followed by the addition of open-end spinning, cotton, and poly-cotton segments, backed by state-of-the-art machinery including autocorners, TFOs, combers, and high-end carding systems.
While the spindle capacity is not the central metric—since the focus is not on volume but on specialization—Mr. Khosla notes that the plant will focus exclusively on high-technology, technical yarns, with over half of the output used for in-house requirements and the rest primarily for exports.
End-to-End Control for Technical Superiority
The new spinning capability is designed to serve the group’s vast requirements in both woven and nonwoven fabrics. The company’s nonwoven lines, for instance, require specialty scrims—high-strength base fabrics—that were previously dependent on external suppliers.
“This backward integration will significantly reduce lead times and allow us to produce scrims and high-performance nonwovens with better quality control,” says Mr. Khosla. “We can now source the fibers, spin the yarns, weave or needle them, and complete the finishing—entirely in-house. For technical textiles, where quality consistency is everything, this is a game-changer.”
Additionally, the group is also investing in balancing and de-bottlenecking across its existing manufacturing units. This includes the addition of a new warper, advanced weaving looms, and numerous supporting systems to ensure seamless expansion of capacity without operational delays. These recurring investments are part of the group’s continuous effort to enhance productivity and efficiency.
New Growth Verticals: Coated Fabrics and Protective Clothing
While the spinning investment is a significant milestone, 2023-24 also marked another major strategic leap for the Khosla Group—the acquisition of a coated fabrics division, previously part of Texport Syndicate Ltd. This acquisition adds a new dimension to the group’s outdoor and industrial fabric portfolio. Mr. Khosla emphasizes that the coating facility stands out due to its capability to process fabric widths up to 3.3 meters—a size that remains uncommon in India.
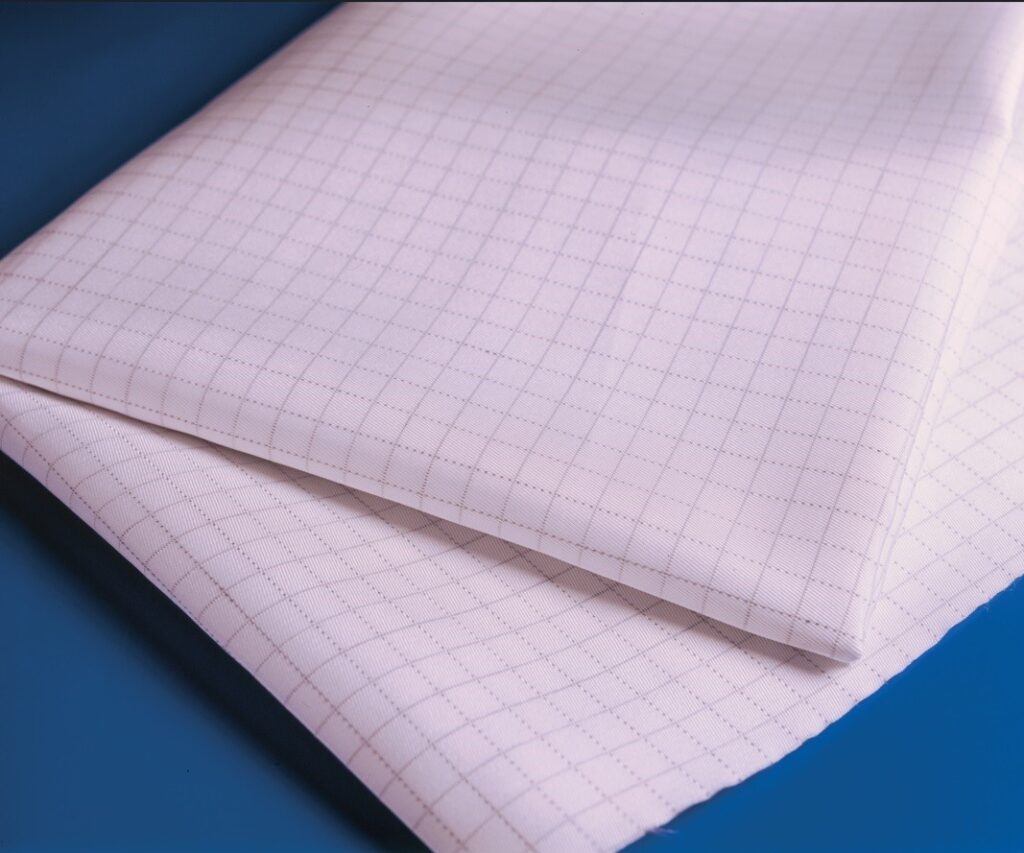
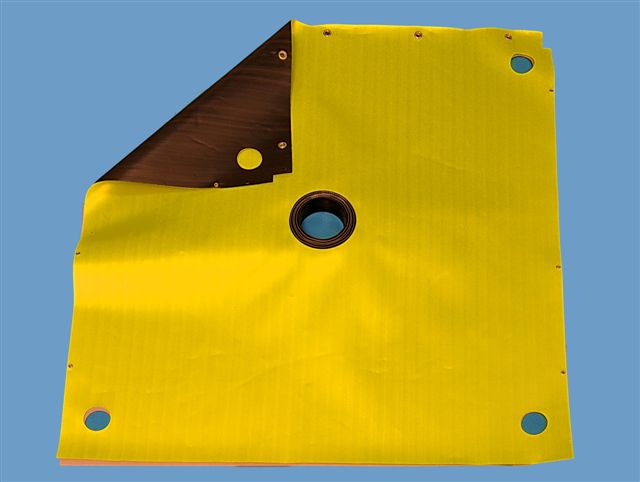
“Today, the market increasingly demands wider-width coated fabrics for Tensile & Semi Tensile, tents, structures, awnings, tarpaulins, and similar applications. With this new acquisition, we’re equipped to deliver on that demand efficiently and with superior quality,” he explains.
Khosla Group has a clear strategy for this new vertical transforming the category into a specialty segment, much like it has done with filtration textiles. “We intend to produce high-performance coated fabrics that are currently being imported, especially from Europe and China,” says Mr. Khosla. “With the technology and vision we have, we can make India self-reliant in this space too.”
In parallel, the group is actively working on launching a third vertical—protective clothing, a logical extension of their integrated value chain. The groundwork is already underway to incorporate specialized dyeing and finishing capabilities for protective textiles. With strong in-house stitching facilities, the company is poised to produce end-to-end protective fabric solutions—from spinning and weaving to dyeing, coating, and garmenting.
An Expanding Product Portfolio and Global Reach
Khosla Profil has long been a trusted name in filtration—both liquid and dry—and its current offerings include a wide range of high-performance filter fabrics and made-ups for industries like pharmaceuticals, chemicals, food processing, mining, and more. With the backward integration into spinning and the forward expansion into coating and protective wear, the company’s product basket is becoming even more varied, robust and balanced.
In terms of revenue contribution, exports account for over 60 percent of the group’s turnover, with the balance coming from the domestic market. Major export markets include the United States, Europe, Latin America and GCC. However, Mr. Khosla is pragmatic about future expectations, acknowledging the uncertainties in global trade. “It’s a very fluid environment. One must be agile, adaptable, and prepared to pivot based on how the situation unfolds,” he remarks.
A Journey of Grit, Innovation, and Continuous Milestones
Mr. Khosla’s own journey into technical textiles is a story of passion and perseverance. Recalling his early days, he credits Rajasthan Spinning & Weaving Mills (RSWM)—where he began as a management trainee—for introducing him to the world of polypropylene, a fiber largely unknown in India at the time. Driven by curiosity and an appetite for challenge, Mr. Khosla was quick to see the potential for industrial applications of polypropylene fabrics, even as his then-employer remained focused on more traditional segments.
That divergence led to the birth of Khosla Profil—a bold entrepreneurial leap taken in an era when the term “startup” didn’t even exist. “I had no money, no family in Bombay, no connections,” he says. “But I was determined. And whatever I earned, I reinvested in the best technology available.”
From four power looms in 1982 to today’s state-of-the-art vertically integrated facilities, Khosla Group has grown through decades of milestones—adding polyester, cotton, multi-filament, nonwoven, monofilament, and now, its own spinning, coating, and technical garmenting capabilities. Mr. Khosla proudly notes that each year has marked a turning point. “We started from zero. So, every year we added something. Every year became a milestone.”
Today, Khosla Group is globally recognized among the top three filtration fabric manufacturers in the world, with one of the most modern setups anywhere. Many global OEMs not only source from Khosla but proudly use the company’s products in their own high-performance systems, underscoring the trust and credibility Khosla Profil has built over time.
A Vision for the Next Five Years
Looking ahead, Mr. Khosla envisions a focused transformation of the group’s operations into high-CAGR verticals, particularly nonwovens and high-value woven fabrics. “We plan to establish each manufacturing activity—be it nonwoven or woven—as an independent, fully capable unit. We’ll expand our nonwoven portfolio and also reinvent our woven segment by focusing on at least half a dozen specialty fabrics that are currently not produced in India,” he shares.
There is also a clear shift in the company’s marketing strategy focusing internally on high-performance, value-added products for both domestic and international markets. This will allow Khosla Group to better utilize its world-class infrastructure and ensure continued leadership in innovation and quality.
Conclusion: A Future Defined by Control, Quality, and Customer-Centric Innovation
As the global demand for performance-driven textiles rises, Khosla Group’s investment in infrastructure, technology, and vertical integration is setting the stage for its next phase of growth. The group’s move into in-house spinning is not just about capacity; it is about precision, reliability, and flexibility—critical elements in serving both domestic and global clients with high-grade technical textiles.
“This was a long-standing need,” concludes Mr. Khosla. “By bringing spinning, weaving, dyeing, finishing, coating, and stitching all under one umbrella, we are now in full control of the quality chain. That’s essential for technical textiles, and it reflects our commitment to deliver the very best to our customers—on time, every time.”
Mr. Rajkumar Khosla a younger brother of Mr. Pramod Khosla and Mr. Rahul Bajaj & Mr. Sagar Khanna his son in laws are other family members of the leadership group of this strong Technical Textile company well known for its prowess in India and World over.