Kallam Spinning Mills Ltd. (KSML) producing spun yarns for knitting and weaving industries in India has announced completion of expansion and modernisation of its various divisions. The company registered a turnover of Rs. 21,464.04 lakhs in 2013-14 as compared to Rs. 18,302.65 lakhs in 2012-13, registering a growth of 117.27 percent. The net profit for the year under report increased to Rs. 1,466.90 lakhs from Rs. 615.49 lakhs.
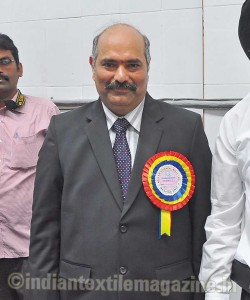
Commencing its operations on March 22, 1995, with 12,096 spindles, the company today operates 56,400 spindles of ring spinning, of which 31,488 spindles are compact.
The company established its open end unit in 2009-10 with an initial capacity of 1,248 rotors. The total rotors capacity of the unit was later raised to 2,912. The Ginning Division was set up in March 2011 with 24 ginning machines. The number of machines has now been raised to 28.
KSML has completed civil work for the 250-loom project at Kunkupadu village in Prakasam district of Andhra Pradesh at an outlay of Rs. 146 crores. The plant capacity is one lakh metrs per day of woven fabric, including 70 per cent yarn dyed shirting and 30 per cent bottom weight fabric. “We have state-of-art machineries in weaving preparatory, weaving loom shed, sophisticated testing equipment and instruments aimed at continuing to be a market leader in quality. Our possibilities of fabrics are boundless, such as dobby yarn dyed shirting, fabrics with 100 per cent cotton and blended with lycra stretch, polyester, nylon, linen and viscose fabrics. We have procured machines from Belgium, Japan, Swiss, Spain, German, China and Italy”, says Mr. P. Venkateswara Reddy, KSML Managing Director.
Dyeing unit
Kallam Spinning has taken up dyeing of 5,000 kg of cotton yarn per day. The project is being implemented at a cost of Rs. 12.5 crores. It includes 11 dyeing machines with a capacity of three to 500 kg per machine. The maximum capacity of the plant is 5,275 kg.
The company has adopted the latest radio frequency system, wherein drying is carried out by acting only on moisture at a particular frequency. Although this consumes high power, the yarn strength does not reduce as in older technology, and the process is continuous and instantaneous. An auto dye weigh and auto liquid chemical dispensing system has been installed to reduce errors in weighing.