State-of-the-art plant with machines from leading global suppliers
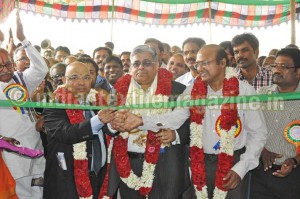
With China’s increasing labour cost, the world is looking to India as an alternate destination for increasing their sourcing of fabrics, home textiles and garments. Identifying an opportunity, many Indian textile manufacturers are moving forward from traditional spinning into weaving and dyeing, and several others into garmenting. The Government has also been offering a lot of support for the textile industry, particularly boosting the weaving segment by offering nil duties on import of machines and the TUFS which further incentivises investments in the textile industry.
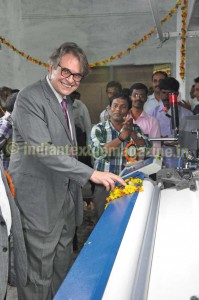
In the recent past, many textile mills are seen moving their comfort zone of being spinners to expand their capabilities in the area of weaving and dyeing. One such classic example is Kallam Spinning Mills Ltd. (KSML) of Andhra Pradesh.
Kallam Spinning has taken a major step forward by setting up a state-of-the-art weaving and dyeing plant. The company recently inaugurated its new plant in Andhra Pradesh comprising with 250 weaving machines with a capacity of one lakh metres of fabric per day and a yarn dyeing plant with a capacity of 5,000 kg per day. The new facility was inaugurated by Mr. T.M. Bhasin, Chairman & Managing Director of Indian Bank, in the presence of Mr. K. Haranadha Reddy, Chairman, Kallam Group, Mr. P. Srinivas, Executive Director, Bank of Baroda, Mr. Ajeya Kallam, Principal Secretary to the Andhra Pradesh Chief Minister, and senior executives from all major companies who have supplied machinery for this project, including Picanol, Toyota, Karl Mayer, Staubli, the Prashanth Group and others.
Kallam Spinning Mills started as a spinning unit in March 1995 with 12,096 spindles. The company today operates 56,400 spindles of ring spinning, out of which 31,488 spindles are compact. It also established its open end unit in 2009-10 with an initial capacity of 1,248 rotors. The total rotors capacity of the open end unit was increased to 2912. In March 2011, KSML started its Ginning Division with 24 ginning machines. These number of machines has now been increased to 28. KSML is an ISO 9001-2000 certified company by TUV since 2000.
The premium quality yarn is exported to a number of customers across the world. The company relies on consistent supply of international standard quality yarn. Having a clear vision and well placed systems, guided by a team of professionals and steered by an enterprising management, KSML continues diversifying its products and extending its customer reach. It is targeting a turnover of Rs. 250 crores for the current financial year.
Weaving expansion
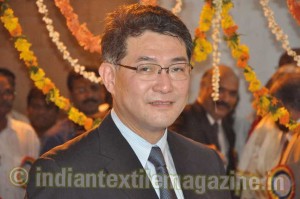
KSML had conceived the weaving and dyeing project two years back at a project cost of Rs. 150 crores. The weaving project has been funded by Indian Bank. The company has established a state-of-the-art weaving plant with 250 looms of Picanol and Toyota machines with a total production capacity of one lakh metres per day of woven fabric, including 70 per cent yarn-dyed shirting and 30 per cent of bottom weight fabric. The company has invested in state-of-art machineries in weaving preparatory, weaving loom shed and sophisticated testing equipment and instruments. It will offer through this plant dobby yarn dyed shirting, fabrics with cotton 100 per cent and blended with lycra stretch, polyester, nylon, linen and viscose fabrics.
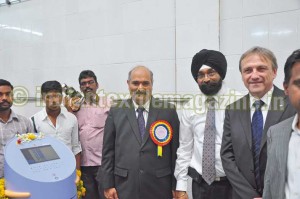
As part of the weaving and dyeing expansion project, KSML has partnered Picanol and Toyota for its weaving machines and Fongs for its dyeing machine range. The company has installed two direct warping machines from Karlmayer with 784 creel and Prashanth West Point India with 690 creel. The company has also installed two sectional warping machines from Prashanth Gamma Tex with fully automatic microprocessor control and lasertonic system. Sizing machines have been sourced from Karlmayer of Germany.
For weaving preparatory section, KSML has installed automatic drawing machines from Staubli Delta-110, which is fully automatic with camera control and 100 per cent fault-free machine. This world No.1 machine for auto drawing helps save a lot of manpower and timings.
Picanol
Kallam Spinning has invested in 102 Picanol Omniplus Summum high speed air jet loom to produce 300 mtrs to 650 mtrs in a loom per day as per pick density. These are state of art machine for producing 100% cotton and blended with polyester, viscose, linen and Lycra fabric. The loom working width is 190 cm and it has 800mm & 1000mm beam flanges. The machine will have very sturdy side frames and back rest systems to match with its requirements for producing bottom weight and yam dyed shirting. OMNIplus Summum is the most advance loom with sumo motor and ELSY motion, cramming motion, multiple weft insertion and Lycra Stretch Systems. SUMO motor is patent righted for Picanol, since the sumo motor will work with software control to increase and decrease the RPM within a fraction of a minute compared to the old system which takes minimum half an hour to reduce or increase the speed changing the pulleys. ELSY motion is the electronic selvedge motion with separate control of selvedge of ends to bring more designs in selvedge alone.
Rapier Looms
Kallam has invested in 42 rapier looms with 20 shaft dobby made by Staubli. This machine is more suitable rapier technology to produce endless colors in warp way and 8 colors in weft way. 20 shaft dobby motions is suitable for any critical dobby yarn dyed shirting fabrics. The rapier technology comes with flexible drive system to ensure near zero breaks down and to increase the utilization. Picanol OptiMax rapier looms are most sophisticated looms of rapier weft insertion followed by their earlier types of Picanol, GTM, GTX, GTMAS, GAMMA and GAMMAX. This machine is also having Sumo motor, ELSY selvedge crank motion, multiple weft insertion and many other features like touch screen software for the settings according to the qualities. The machine has three set cards to transfer the settings from one loom to another loom and preserve the settings exclusively. All dobby weave fabrics as well normal yarn dyed products.
Toyota
KSML has installed 104 Toyota JAT 810 air jet looms is suitable for yarn dyed shirting, bottom weight and suiting with 100 per cent cotton and blended with polyester, linen, nylon, viscose and lycra stretch fabrics. These looms can produce 380 to 700 mtrs per day in one machine. This machine is having special feature of crank to non-plain fabric separately. The seven shafts and 1681 type Staubli cam box attachment help run various weave designs like twill, drill, sateen, matt & oxford, etc. These are fault-free looms capable of producing zero-defect fabric with minimum maintenance cost and maximum utilization.
The Toyota air jet has earlier models like JAT 610 and JAT 710. The model JAT 810 is more beneficial with regard to air consumption control with its P monitor attachment.
Also the machine has very friendly software for monitoring the loom’s mechanical setting and fabric settings. The machine has other facilities to arrest fabric damage like bumping mark, starting mark, etc. The special Lycra stretch system will be suitable for producing Lycra weft fabric which is most popular in the market.
Dyeing unit from Fongs
KSML is setting up an advanced state-of-the-art yarn dyeing plant with a capacity to produce 5,000 kg per day. This project is being funded by Bank of Baroda. KSML has partnered with Fongs for the entire dyeing machine range. It will have 11 dyeing machines with a capacity ranging from three kg to 500 kg per machine. The project is catering to yarn dyed shirting in weaving and will require small to large quantities of dyed yarn in various shades, depending upon the customer order. KSML has the facility to run the dyeing vessel from 100 per cent to 50 per cent capacity without change in the MCR ratio with the air pad technology.
Each machine has two carriers, each one with several spindles with a maximum of 10 cones/spindle can be loaded based on the machine capacity. The maximum capacity of the plant is 5,275 kg.
Hydro extractor from Dettin
Cotton yarn after wet dyeing usually has moisture and has to be squeezed or extracted by centrifugal rotation of the material. The earlier technology was to dump all cones into a perforated basket and rotate at high speed, thus removing around 50 per cent moisture and retaining 50 per cent to be dried on the radio frequency drier. The cones are loaded onto individual cone spindle, and each cone rotates at high speed on its own axis, thus achieving the same earlier results, but without de-shaping the cones as it is not manually handled. The capacity of Dettin BERTA 36 model matches the dyeing capacity of 275 kg/hr. The machine operates continuously.
Radio frequency drying from Stallam
Subsequent to dyeing and extraction on dyeing machine, the moisture content is to be brought down from 50 per cent to 10 per cent to dry the yarns. Earlier, drying was done by passing steam through the cheeses, which was very expensive and time consuming.
KSML has adopted the latest radio frequency system, wherein the drying is carried out by acting only on moisture at a particular frequency. Although this consumes high power (105 Kw), the yarn strength does not reduce as in older technology, and the process is continuous and instantaneous. The company has gone for STALLAM R.F. DRIER which has various safety features. The capacity matches its dyeing requirement of 275 kg/hour.
Auto dye weigh & auto liquid chemical dispensing
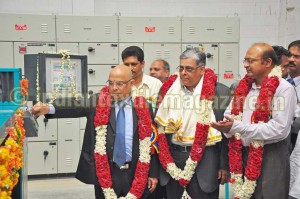
Until recently all dyes and chemicals were manually weighed, prepared and dispensed. This manual activity gave scope for errors and thus added one more variable for shade differences between lots. Over the last few years there has been a lot of work on auto dispensing, and it has been observed that in addition to reducing costly errors in weighing, there is atleast 10 to 15 per cent savings in chemicals by avoiding spilling and excess use due to approximations.
Also the auto system is connected to the online system, indicating real time stock, consumption, re-order levels highlighting, etc., reducing clerical work and consequent errors. By going for bulk dispensing the company also saves a lot by getting chemicals in larger containers instead of smaller cans manually.
Subsequent to the R.F. drying, the yarn cones are unloaded, weighed, checked for evenness of dyeing and are rewound as soft packages on Schlafhorst auto-coners, so that it is ready for warping or for weft insertion in the weaving section. KSML has planned for five machines of 60 spindles each based on its requirement and needs segregation of each machine, to avoid fluff contamination of one shade into the other. It is helpful if humidification air changes are provided so that the fluff is going into the return trench and not flying around in the winding area.
Effluent treatment of dyed liquours
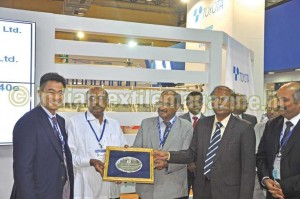
KSML has accorded high priority for protecting the environment, and believes in a more responsible and sustainable business. Effluent discharge from the dyeing plant is an important area where the company has made considerable investment. With the introduction of zero liquid discharge (ZLD), no water is allowed to be discharged into the ground even without proper treatment. In other words there is need to excessively treat the effluent such that it is almost like fresh water and fit to be reused into the process again.
KSML has set up an advanced ETP plant in partnership with Confident Engineering of Coimbatore for treating the 180 m3/day partially by biological treatment and filtration for use for our plantations at site. The remaining HTDS effluent [high total dissolved solids] stream of 150 m3/day will be further treated by ultra-filtration, reverse osmosis -2 stages, nano-filtration, etc., to basically recover good water at each of these stages and bring down the water requirement to the bare minimum for the very expensive multistage evaporation [MEE].
Thus from 150 m3/day is narrowed down to only 20 m3/day for evaporation. After a lot of deliberation with some of the best Italian and Indian effluent plant suppliers the company has finally decided to go with Confident Engineering Pvt. Ltd. [CEPL]. They are also responsible for achieving the final results as per the norms of APPCB. KSML has also entered into an operations/maintenance contract for five years.
Multi-stage evaporator
As mentioned earlier, subsequent to reducing the effluent volume to 20 m3/day, there is need to evaporate the same by going through three stages of evaporation. Since this is a high steam consuming process, KSML has gone for a MEE from Ketav Consultants, wherein they use fresh steam only at first stage evaporation and reuse the steam. Additionally the company has installed the thermo vapour recompressor (TVR) and has gone for total automation and PLC to reduce labour and manual intervention. The MEE is located between the boiler and ETP so that it minimizes the pipelines and enables handling all aspects economically.
KSML has embarked on a major step forward by expanding into weaving dyeing. The company has also plans to enter the garmenting segment in the future. It clearly shows the willingness of Indian companies to move from the comfort zone of pure spinning to becoming a more integrated textile manufacturers.
With China’s increasing cost and focus on its domestic market, Indian textile manufacturers see a larger opportunity to cater to the global market requirements.
Stäubli, a strong technology partner for Kallam Group
Stäubli has been a key partner for the Kallam Group in its foray into weaving. Staubli has supplied warp preparation equipment DELTA D110 enabling it to automatically draw in warps into drop wires, healds and reeds, thus facilitating and improving the gating process and the quality of weaving operations. Furthermore, the company has supplied shed forming technologies (dobbies and cam motions) to Kallam which are used on their weaving machines.
Mr. Fritz LEGLER, Vice President, Staubli Sargans AG, says: “We have reached a high level of co-operation and understanding on either side. This forms a very good and effective basis for future cooperation. We thank the Kallam Management for having chosen Stäubli as one of their key suppliers”.
“Kallam requires utmost flexibility and quick response capabilities in their respective business dealings with their customers. Our automation technology (quick warp preparation through automatic drawing-in) as well as shed forming technologies enable quick turn arounds in their weaving operation”, adds Mr. LEGLER.
With the Indian Government’s incentive for the weaving segment, Staubli expects many more Indian spinning mills to move up the value chain and foray into weaving.
Complete air engineering solutions from Luwa
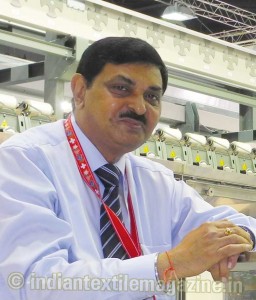
Luwa has been associated with the Kallam Group since 2004, providing humidification and ventilation systems for their Ring Spinning, Open end Spinning, Laboratory Precision Control Unit and Weaving Unit. The comany has provided the complete air engineering solutions for the new weaving plant as well. Luwa engineers worked very closely with the KSML on various design and engineering aspects for the new plant. Luwa has provided the humidification plants for the complete weaving line and also for their weaving preparatory department consisting of warping machines.
Mr. K.K. Malhotra, Vice President Sales, Luwa India, says: “The requirement from the customer was to have energy efficient systems hence Luwa has supplied its patented Loom sphere system for their weaving machines, which provides high humidity level at the warp with laminar low speed air flow without turbulences. The main advantage of Luwa Loom Sphere system is higher productivity at reduced energy consumption. This provides ambient conditions at comfortable 65% humidity and around 80% humidity on warp which helps in increasing the production output and quality with increased loom efficiency”.
The Luwa team works very closely with Kallam engineers, extending all its technological inputs to them in implementing air engineering solutions for their Spinning and Weaving plants. In fact, the Jt M.D. of Kallam Spinning Mills Mr. G.V. Krishna Reddy always takes lot of interest in design and engineering and had personally visited our Works and office in Bangalore for quality check, design and engineering discussions. In future also Luwa will definitely be working very closely with the engineering team of Kallam and provide tailor made and customized solutions for their various projects. Luwa will also be helping them with energy and efficiency audits of their various plants, training of their technical and maintenance team so as to maximize the operation efficiency of Luwa plants.
Mr. Malhotra says: “We are already observing this trend of forward integration and going up on value chain by some existing Spinning Mills in India. With fluctuating rate of yarns, integrating forward by Indian Spinning mills will be a more viable solution and many existing Luwa customers are already going for value additions. We hope that Luwa with its maintenance friendly high efficiency Humidification system will get good opportunity for partnering with future investors and see good prospects for its business”.
K.H. Reddy
Kallam Group Founder & Chairman
A saga of success
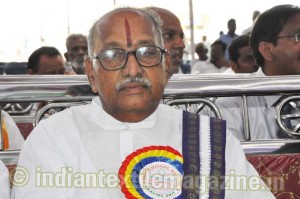
Born in a small village called Ramanayapalem in Prakasam district of Andhra Pradesh in 1936, Mr. Kallam Haranadha Reddy hails from a poor family of farmers. Being the youngest of all in the family, he had to discontinue his studies due to financial constraints and join his father in the fields. In Initial days, he struggled a lot, but due to his determination, hard work, broad vision and leadership qualities, he slowly and steadily built up his business empire.
During 1962-1985, Mr. Reddy started 18 firms, with the help of his friends and colleagues. In 1988, he constructed an oil mill and in 1995 forayed into the textile industry by setting up a spinning unit which went for public issue and got five times oversubscribed.
In 1996, Kallam Agro Products and Oils Ltd. started construction of its solvent and oil refinery plant, which was another landmark in Mr. Reddy’s career. The company has the second highest domestic sale of DOC in India and has been awarded the second highest crusher from 1999-2000 till date.
As for the spinning unit, Mr. Reddy established Kallam Spinning Mills Ltd. with an initial investment of Rs. 16.70 crores for installing 12,096 spindles, and an additional amount of Rs. 8 crores was invested later towards expansion of spindles, totalling 18,144 spindles in 2000. The spindlage was further increased stage by stage, and today it stands at 56,400 spindles with a capital investment of Rs. 120 crores. lt is worth mentioning here that the spinning mill was awarded ISO 9000 by TUV India and is an ISO 9000 unit for the last one decade.
Kallam Spinning Mill has been expanded further at Kunkupadu village, Addanki Mandal, by constructing a weaving project having 250 airjet and rapier looms with a capacity of one lakh metres of cloth per day, and a yarn dyeing project to process 5,000 kg of yarn per day for yarn dyed shirting.
Thanks to his strong willpower, determination and the urge to be one step ahead of others, Mr. Reddy further ventured into constructing four mini-hydel power projects, one at Janapadu and three at Nelakondapalli, with a total capacity of 5.0 mw at a cost of Rs. 35 crores, with financial assistance from IREDA and Andhra Bank.
Mr. Reddy observes that Andhra Bank has played a vital role by providing him loans for all his expansion plans. Today the Kallam Group is being financed by five banks, namely, Andhra Bank, Indian Bank, State Bank of Hyderabad, Bank of Baroda and Axis Bank, having a total exposure of Rs. 400 crores to the group. With a turnover of less than Rs. 150 crores in 2004, today the group has achieved Rs. 600 crores, four times within a short span of 10 years. Discharging his duties to the younger generation at the right time, Mr. Reddy retired from active participation from his group companies and handed over the reins to the respective managing directors in 2004.
With great perseverance and hard work, Mr. Kallam Haranadha Reddy pursued his education in 1968 at the age of 42 and was able to accomplish a Master’s degree in Arts and Bachelor’s degree in Law. He has started an engineering college for the economically backward students, irrespective of the caste or creed.
In recognition of Mr. Reddy’s contribution to the society and the nation at large, Andhra Bank suggested his name for the prestigious UDYOGA PATRA Award for self-made industrialist in the country. For his expertise in business and yeoman service rendered to the cotton trade, he was given the Life Time Achievement Award in 2002 by East India Cotton Association, Mumbai.
Mr. Reddy also actively takes part in social service and occupies an important position as the President of the Viswa Hindu Parishat of Purva Andhra and as Vice President of the Gosamrakshana Sangam.
Thus, throughout his career, Mr. Reddy has had great determination to be one step ahead of others. He strongly believes that the reason for his self-made development in business, trade and education is his devotion to hard work, discipline, quality, strong will, determination, patience, courtesy, moral values, loyalty, broad vision, high ambition and cordial relationship with workers and his customers.
Year Name of the firm
1958 Sri Venkateswara manure depot
1960 Sri Sambasiva Rao Mill, Karamsetty Sambasiva Rao Son Alla Satyanarayana Reddy & Co.,
1960 LIC agency with code, 1099688 General Insurance (new – india assurance) as agent
1963 Kallam Haranadha Reddy, Thummapudi Nageswara Rao. Whole-sale rice business.
1965 Sri Venkateswara General Commission Merchants, Kallam Haranadha Reddy & Co.,
1967 Sri Venkataramana Commission Merchant Kallam Haranadha Reddy & Co.,
1968 Jyothi Chits & Finance company
1969 Sri Navodaya Trading Company (chillies and corianders export)
1973 Sri Chandrasekhara Ginning Mills
1974 Sri Ramakrishna Rice Mill, Allasatyanarayana Reddy, Kallam Haranadha Reddy & company
1975 Sri Ramakrishna Poultry Firm
1976 Sri Ramakrishna Fertilizers & Pesticides
1977 Sri Ramakrishna Fertilizers & Ginning section
1978 Siva Ramakrishna Rice Mill, Alla Satyanarayana Reddy, Kallam Haranadha Reddy & Co.,
1979 Ramakrishna Refinery (oil mill) AIla Satyanarayana Reddy, Kalam Haranadha Reddy & Co.,
1980 Sri Ramakrishna Ginning Mill, Kallam Chalama Reddy Sons & co.,
1983 Sree Traders & co., (a broker office)
1984 Sri Sidhardha Cotton Press
1985 Chandra Sekhara Ginning Mill, Bellary branch, Kallam Chalama Reddy & Co.,
1988 Kallam Agro Products & Oils Ltd., Cotton & Oil Division at Guntur Dist, AP
1988 Kallam Agro Products & Oils Ltd., Rajapalayam in Tamil Nadu
1995 Kallam Spinning Mills Ltd., Commercial production and public issue
1996 Kallam Agro Products & Oils Ltd., Solvent & Refinery Division
1996 Sri Venkata Sainadha Traders, KHN Reddy & co.
1999 Kallam Housing & Real Estate Pvt. Ltd.
2000 Kallam Brothers, Cotton Division
2001 Janapadu Hydro Power Project Pvt. Ltd., Nereducharla, Nalgonda dist.
2002 Kallam Spinning Mills Ltd., Power Division (1.6 MW), Nelakondapalli, Khammam dist.
2002 Kallam Spinning Mills Ltd., Power Division (0.80 MW), Nelakondapalli, Khammam dist.
2002 Kallam Brothers Cotton Ltd., Spinning Division at Annavaram.
2004 Registered in Bar Counsil of India & started practice as Advocate
2007 Kallam Spinning Mills Ltd., Spindileage increased to 44,000
2008 Kallam Spinning Mills Ltd., OE plant commencement
2008 Commissioning of 1.5 MW wind mill by Kallam Agro Products and Oils Ltd. in Tamil Nadu
2010 Kallam Spinning Mills Ltd., Spindleage increased to 52,000
2010 Kallam Spinning Mills Ltd., Ginning Plant Commencement
2010 Commencement of Kallam Haranadha Reddy Institute of Technology, Chowdavaram
2011 Commissioning of third KSML 1.6 MW hydel power project
2012 Laying Foundation Stone for Weaving and Dyeing Project at Kallam Spinning Mill at Kunkupadu, Prakasam Dist.
2013 Commissioning of India’s First Cotton Seed storage plant at Kallam Agro Products and Oils Ltd., Dokiparru.
2014 Commissioning of Weaving plant at Kunkupadu with 250 looms capacity
A.T.E. provides Kallam warp preparation and dyeing solutions
A.T.E. has been associated with the Kallam Group since the early 90s for their first spinning project. Since then A.T.E. has been partnering the Kallam Group in all its new projects and expansions. The company started by supplying Trumac blowrooms and DK740 cards, for which it has received repeat orders subsequently. For another expansion project of Kallam Brothers, part of the Kallam Group, the company had supplied Trützschler blowroom, cards and Zinser speed frame 51M.
A.T.E. was a key partner in the Kallam Group’s weaving and dyeing expansion project. The company has supplied Karl Mayer’s warp preparation machines and the complete dyeing plant from Fongs. “Kallam is a very professionally managed group, headed by the Chairman Mr. Haranadha Reddy, who is passionate about his business and has a great drive for excellence. We have been partnering Kallam group in spinning, weaving and processing in most of the projects and I am confident that we will continue to partner them in future as well”, says Mr. G.V. Aras, Director – Textile Engineering Group, A.T.E Enterprises Ltd.
A.T.E. has installed the state-of-the-art warp preparation machines from Karl Mayer. In the first phase of the weaving project of Kallam Group, the company has supplied Karl Mayer high speed direct warping machine type – WARPDIRECT and high performance sizing machine type – “Size-O-Matic”.
The WARPDIRECT produces high quality of warp beams for sizing machine and is the most productive because of its V creel executions. The high quality of warp beams are achieved due its unique feature of no cross threads, fewer rolled-in ends as machine stops instantly during stoppages. Highest productivity speed in practice of up to 1200 m/min and with V creel it ensures the warping with the lowest thread tension. Ergonomic design and operator friendly for universal applications – coarser to finer staple yarns.
The KARL MAYER ROTAL “Siz-O-Matic” machine is characterized by highly-convenient operation and a perfect process control. Warp beams sized by KARL MAYER ROTAL stand for highest efficiency in weaving. The compact size boxes guarantee short yarn paths with an ergonomic design for easy access, maintenance and cleaning of a size box having liquor volume of 60 per cent lower than in conventional technique and bound warp sheet transport during wet application. The KAMCOS is an ideal tool for customer-oriented process monitoring for regulating yarn tension and controlling sizing process parameters.
The latest technology emphasis is on the economic aspects of the process, greatly increases efficiency in both the weaving and weaving preparation processes. High-tech sizing operation produces high-quality, perfectly uniform, reproducible warp beams, which are needed to fully exploit the high-speed Airjet and Rapier weaving machines.
Kallam has partnered Fongs for the complete dyeing range. Kallam has set-up a 5000 kgs productivity per day yarn dyeing plant. A.T.E. representing Fongs in India has supplied the complete range of “LABWIN”, “ALLWIN” with capacities ranging from 5 kgs to 500 kgs/charge.
With spinning mills increasingly moving forward by setting up weaving and process houses, Mr. Aras says: “There will certainly be more mills venturing into weaving and processing and grow vertically for the sake of higher value addition. Since yarn business is fast becoming highly competitive and dependence on imports by China has made it quite vulnerable. In this backdrop, many mills will go for weaving, knitting and dyeing for value addition”.