Future-ready with IE4 motors: the ESD series rotary screw compressors from Kaeser are now equipped as standard with energy-saving motors and high-efficiency Sigma air ends. The prime benefit is even lower energy consumption for significant energy cost savings.
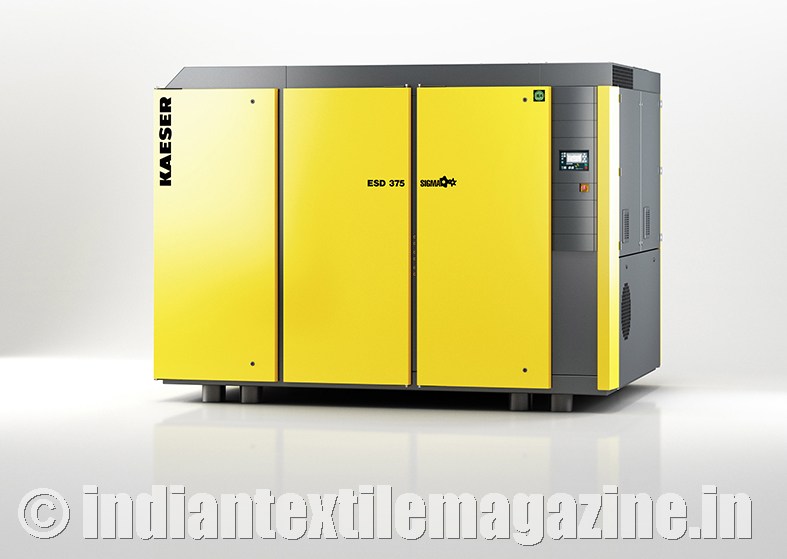
The latest generation ESD series rotary screw compressors consume up to 8 per cent less energy than the previous models, yet deliver 6.5 per cent higher flow rates. Numerous optimisation measures, such as further-improved Sigma Profile air ends and the use of IE4 motors significantly improve the overall energy profile. With drive powers of 200 and 250 kW, these highly efficient compressors produce flow rates from 8.6 to 44.5 m³/min and are designed for pressures up to 15 bar.
The exceptional performance of ESD series compressors is due in large part to Kaeser’s refined technical concept. At the heart of every ESD system lies a flow-optimised rotary screw air end with energy-saving Sigma Profile rotors that allows ESD compressors to set the new standard when it comes to specific power.
The use of IE4 Premium Efficiency motors underlines Kaeser’s continued commitment to providing maximum efficiency, not only to save energy but also to assure compressor competitiveness well into the future. IE4 motors are the technology of tomorrow, as current regulations introduced in January 2015 simply require the use of IE3 class motors.
Moreover, the electronic thermo management system delivers additional energy advantages, as do the environment-friendly fluid filter and integrated Sigma Control 2 controller.
Electronic thermo management consistently controls the oil temperature within a constant, safe differential relative to the dew point (condensation temperature), which also helps avoid unnecessarily high air end discharge temperatures, thereby contributing to higher overall energy savings.
Kaeser’s engineers have also equipped the new ESD series compressors with another small, but clever, detail to aid heat recovery. Amazingly, a compressor converts 100 per cent of its input drive energy into heat, of which 96 per cent can be recovered and used for heating purposes. The associated savings benefit is therefore huge.
With optional heat recovery equipment, a second electronic Thermo management system ensures optimum use of the heat energy that arises from the compression process. For example, when all of the heat energy has been fed into the heat recovery system, the intelligent Sigma Control 2 controller recognises that cooling is no longer required from the system cooler – so it simply deactivates the fan at the fluid cooler, which in turn leads to further energy cost savings.
Environment-friendly fluid filter
The principles of resource conservation are also consistently applied inside the compressor unit: the environment-friendly fluid filter elements now simply sit in an aluminium housing, with no need for a sheet metal enclosure. The filter elements themselves are completely free of metal, making disposal straightforward: at the end of their service life, they can be thermally disposed of without additional pre-treatment.
The advanced “Sigma Control 2” compressor controller provides comprehensive monitoring of the compressor and, if equipped, the frequency converter (SFC variable speed control option). It also enables the compressor to utilise powerful networking solutions and allows straightforward connection to a master control system, such as the Sigma Air Manager 4.0, or to a control centre.
Kaeser’s new ESD compressors are therefore perfectly equipped to benefit from all of the advantages that true Industrie 4.0 production environments have to offer.