Jay Jay Mills India Private Ltd., Erode, is one of the most modern mills in India. Its state-of-the-art spinning plant has 32,832 spindles, with two Truetzschler blowroom lines feeding 18 Truetzschler TC 10 cards. The average count processed is Ne 38 combed compact.
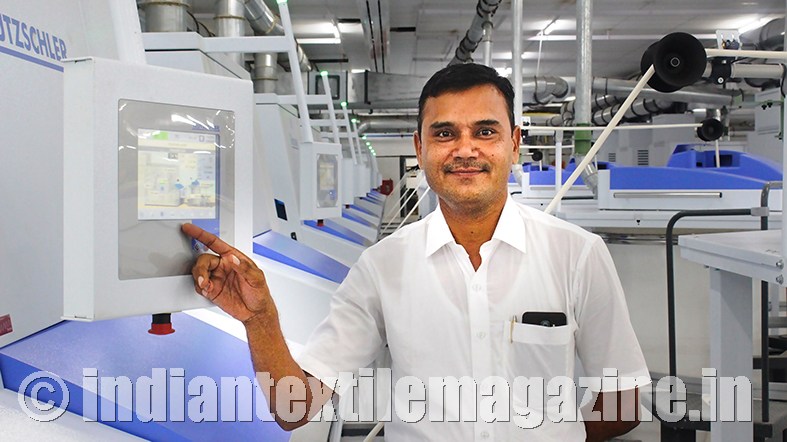
Until recently, the mill used to capture basic production data manually in shift diaries and registers. These data form the basis for all further calculations related to production, such as machine efficiency, and hence any human error in noting down any production data would throw the entire calculation haywire. Further, capturing such data was a time-consuming process.
To overcome this major handicap, Jay Jay opted for Truetzschler T-DATA, a web-based monitoring system, for analysing the performance of the machines. T-DATA monitors and tracks a whole range of machine performance parameters such as production, efficiencies, breakdowns and maintenance schedules on a real time basis.
Expressing his satisfaction with the performance of T-DATA, Mr. Jaichand, Managing Director of Jay Jay Mills, said: “In this era of Industry 4.0, we wanted an automated solution to monitor and optimise the machine performance that will give us an edge in the market over competitors. The T-DATA offered by Truetzschler along with its blowroom and cards precisely meets this requirement, and I find it excellent and highly beneficial”.
The T-DATA system can be accessed by a central PC kept in the office. To make it even more user- friendly, Truetzschler has created a new “My Production” app which can be accessed 24×7 from anywhere in the world on a smart phone with an internet connection. The app makes it possible to see at a glance if the machines are running smoothly – it uses a simple colour coding system: green indicator means “everything is OK”, while a red indicator means “act now”.
Mr. Ekanath, Asst. General Manager at Jay Jay Mills, said: “We now optimise settings and reduce downtimes by monitoring trends in production and malfunctions using the T-DATA. These production data are further analysed for a specific period of time. We can either choose between one of the ready-to-use standard profiles for production, maintenance and quality or easily create individual charts and tables with data of interest to us”.
Mr. Ekanath is very excited that he can now remain in touch with his department wherever he is, even when he is travelling. He is particularly happy with the T-DATA’s unique feature that enables sending e-mail or SMS alerts to staff members for maintenance, machine malfunction or in case of any variation in quality compared to the set points.
The mill is planning to have all its meetings with the top management, henceforth using the real time information from T-DATA which also allows users to send information to the user’s ERP system through an interface for further processing, if required.