iNTERSPARE of Germany, a textile finishing machine manufacturer, is looking back very positively at ITMA 2015 in Milan at the end of the first quarter 2016. This relates to both the number of visitors to the exhibition stand and the successful follow-up business. The shrink dryer, exhibited as the main showpiece at the world’s largest textile machinery fair, was successfully sold shortly after the fair to a customer in India. And there are numerous other order inquiries for Syncro and other systems.
At ITMA, iNTERSPARE showcased itself at a large exhibition stand and with a new CI as a manufacturer of textile finishing machines for fitting the Artos and Krantz product lines. The group had acquired the relevant trademarks, designs and patents in 2007 and in recent years has developed gradually from a supplier of spare parts to a manufacturer of textile finishing machines. Many company decision-makers who have been using Krantz und Artos machines for years visited the booth and were very happy that they could continue acquiring new machinery of the Artos and Krantz product lines with the proven quality of iNTERSPARE.
“The ITMA and above all the feedback on our stand and our presentation as a textile finishing machine manufacturer was simply overwhelming”, said iNTERSPARE Director Dirk Polchow. “For us it was really an enormous recognition of our work just to see so many happy faces. All visitors to our stand were full of praise on how we tie in with the tradition of Artos and Krantz and can offer these high-quality machines in quantities again. And they were also surprised at how we have now established ourselves as a machinery manufacturer”, he added.
iNTERSPARE had used ITMA as the showcasing platform for the textile machinery industry, to present the latest version of the legendary Krantz Syncro. The shrink dryer – as a further development of the Haas Aerovar shrink dryer – has always been an excellent example of German engineering talent. In particular, the extraordinary results and the high production rate based on the optimal interplay of many sophisticated and patented components make the Syncro the best shrink dryer in the world.
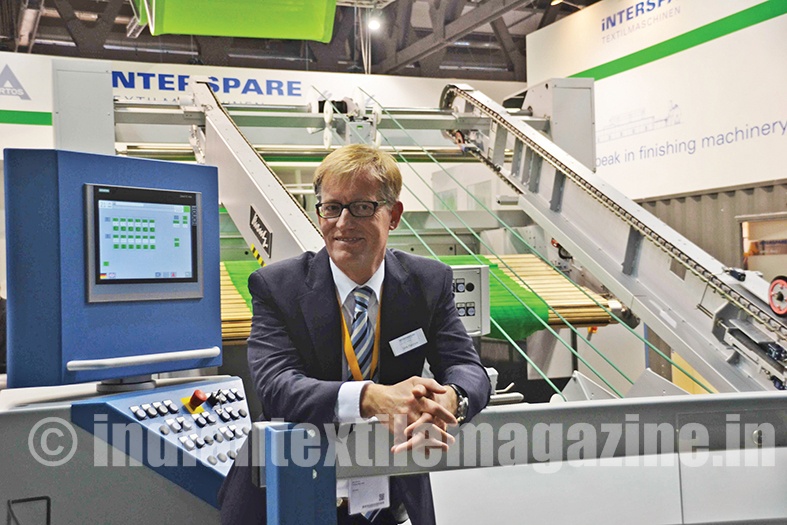
The interest in iNTERSPARE and the iNTERSPARE Krantz Syncro that was exhibited was also very intense at the first-ever press conference held at the show. Around 20 journalists from key media in the global textile industry attended the conference and wanted to know how the company had developed from a successful supplier of spare parts to an established manufacturer of textile finishing machines in recent years as well as its vision for the future. In response, director Polchow announced, among other things, the new construction of an assembly hall at the iNTERSPARE premises in Reinbek (Germany) in which the machines shall be manufactured in the future as the available space no longer suffices.
Current machinery range
The machinery range of iNTERSPARE Textilmaschinen includes the Krantz Syncro shrink dryer and the Krantz K30 stenter, both of the Krantz product line. In the Artos product line, iNTERSPARE Textilmaschinen offers the Artos Unistar stenter, the Artos Vari-Flex dyeing padder and the Artos Uni-Flex impregnation padder.
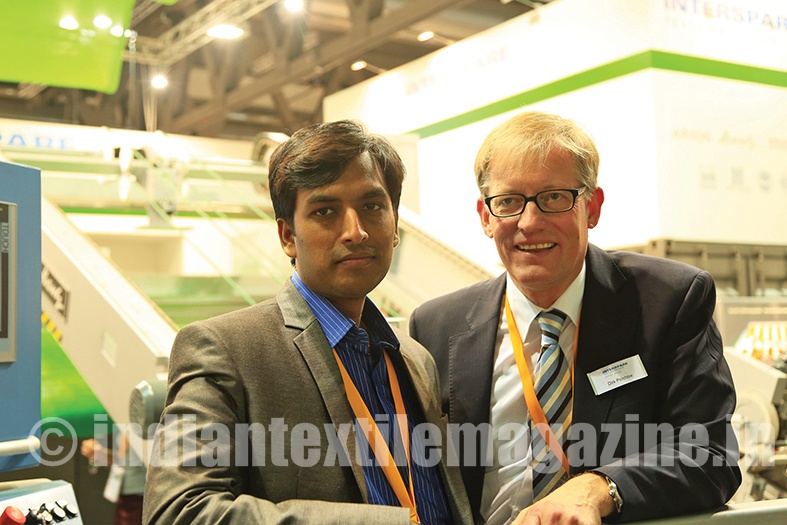
Another major topic for discussion at the IMTA stand was the modification, upgrade and modernisation of existing installations of the product lines Artos und Krantz. There is a 5-digit number of existing systems from the Artos, Babcock Krantz, Stentex, Hacoba, Müller und Famatex product lines at textile companies in 116 countries. A lot of these systems, installed by Artos, Krantz, Deutsche Babcock Textilmaschinen and Moenus over the past 50 years, are still used for drying and finishing textiles. Based on a growing need for productivity as well as sustainability, modifications and upgrades offer textile companies an excellent alternative to jumping to the current state-of-the-art with manageable investments.
iNTERSPARE has already carried out upgrades successfully in recent years, for example a tenter frame in the iNTERSPARE product line Artos for Dutch textile company Vlisco Group.
A consequence of a modification may be improved energy efficiency. Not only is greater economy attained but also an improved ecological performance – very important for sustainability strategies of textile producers and for meeting the demand of larger brands and retailers. Other modifications include for example the extension of the machine for enlarging production capacity. Alternatively, supplementary component sets increase flexibility and economic efficiency.
Equally interesting are conversions enabling installations to be adjusted to the changed specifications. Examples of these are conversions of heaters from oil circulation systems to gas heating or exchanging lubricated tension chains for modern lubrication-free chain systems. More extensive alterations such as the conversion of stenter frames for woven goods for the use of knitted fabrics are also possible.
Updating can also prove economically advisable. This can be achieved by converting from S5 to S7 controls or replacing a PIV transmission with individual drives.
INTERSPARE has all the technical drawings of the machines available and is thus able to submit constructive and well-informed proposals.
Visitors to the company stand were also delighted to see the new version of the “Smart Order System” smartphone app and were impressed by how easy it is to use. The app liberates customers from all research for the correct spare part allowing the customer to save time and money. The only thing the customer has to do is to install the app and to send a picture of the part which needs to be replaced.