By Johann Philipp Dilo
At ITMA 23 DiloGroup has launched its MicroPunch pilot line including fiber preparation, web forming and needling consisting of a special pre-needler for intense needling and two finish needlers type “MicroPunch”.
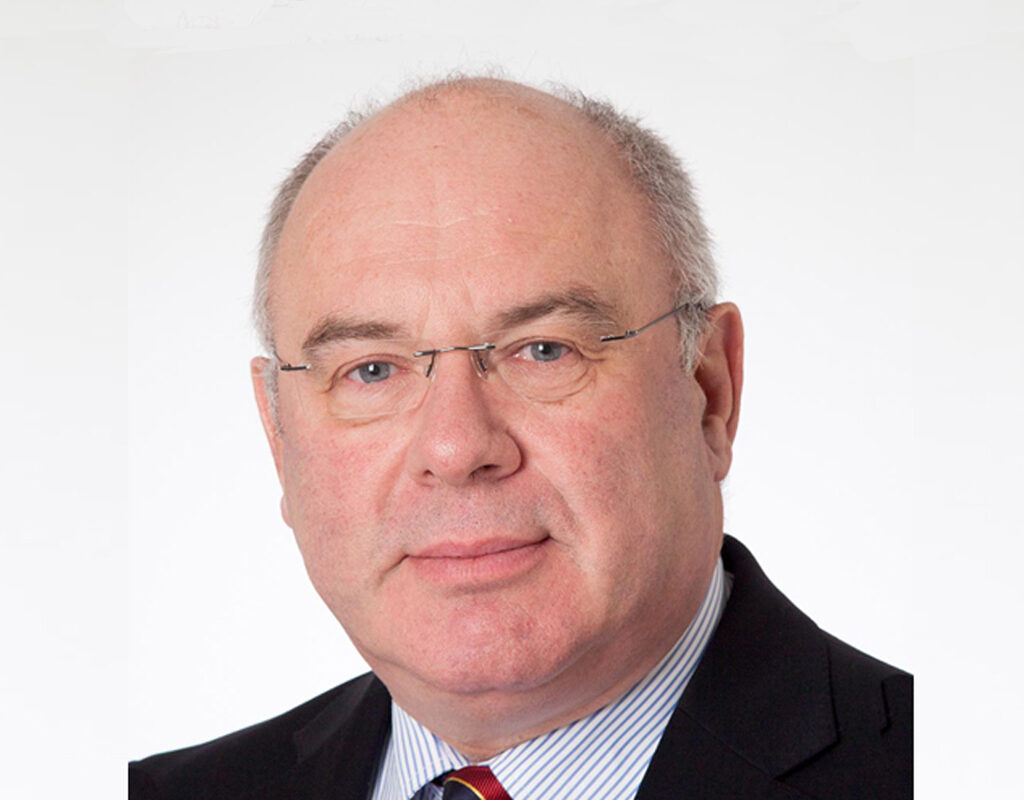
During ITMA this line was on demonstration to prove its basic capabilities as an alternative to other consolidation techniques through needling lightweight material in a range of approx. 30 to 120 g/m2 . The pre-needler featured a needle density of 20,000 needles/m/board on 4 needle boards in a working width of 2.5 m. This classical intense needling includes slotted stitching plates and alpa-flex needle boards with individual drillings to accommodate the needles. The two finish needle looms of the MicroPunch S series mark the step to an advanced stage of intense needling. Instead of slotted stitching plates so called wire plates are used applying tensioned wire in a parallel array to create long slots for the needles on the board in a needle density of 45,000 needles/m/board. This massive increase of needle density was only possible through an arrangement of needle modules positioned side by side accommodated within C shaped cassettes/containers on the board. Thus, a total of 8 needle boards in the 2 finish needle looms are designed to create stitching arrays in the product’s, surface, similar to those of the water-entangling process. The line at ITMA has fulfilled this purpose of demonstrating the advanced capabilities of intense needling through it’s MicroPunch design features.
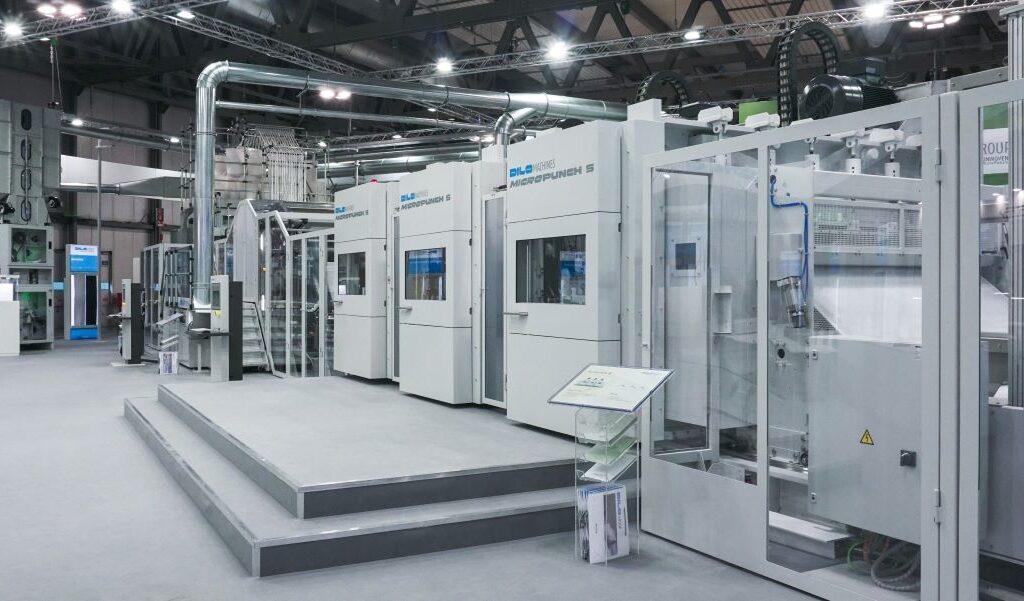
The demonstration and pilot line from ITMA has then been reinstalled at DiloGroup’sheadquarters in Eberbach in the DILO Nonwoven Research & Demonstration Center.
The new design approach of the advanced MicroPunch needle looms is considered “phase I” in order to prove the concept. Earlier this year phase II has been commencing in order to carry out nonwoven product development for the areas of hygiene, cosmetical and medical products, not excluding technical areas to widen also the range of applications and products. Together with interested parties and a number of customers this product development is carried out first in order to prove the individual application capabilities of products within their related market segments, typically for example a 40 g wipe for hygiene personal use. During this phase II the quality features of the related product ranges are not only investigated but also tested. Sometimes with the intent to duplicate features of products of other technological processes yet also for new and different applications as well as to allow a different market approach with new features for an existing application segment. One example of this development direction would be a wipe of the hygiene sector featuring an improved thickness, softness, absorption capacity, air permeability and wear resistance.
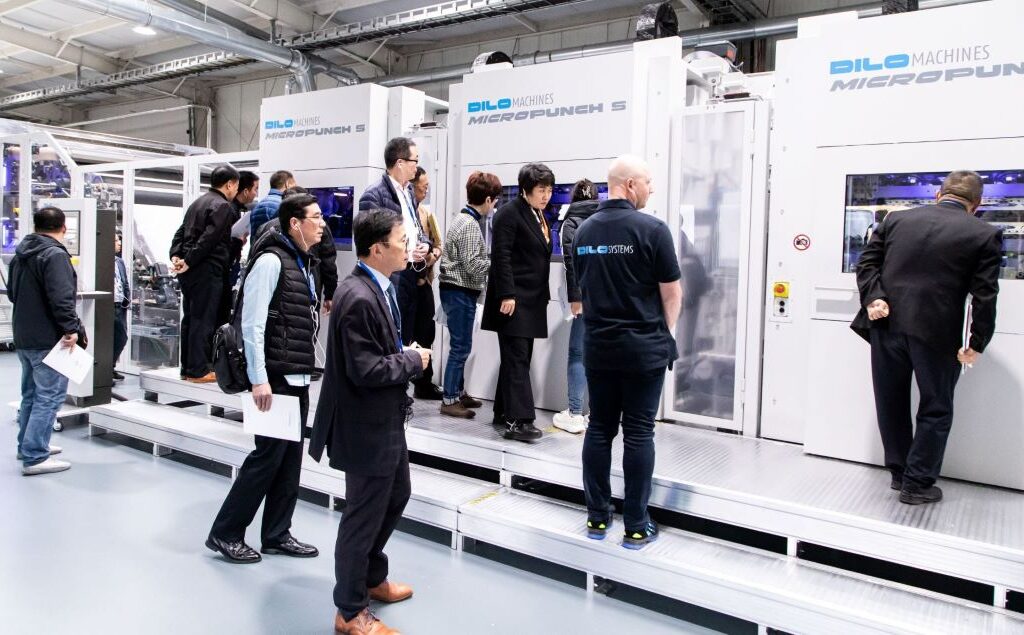
Parallel to the above, last year as Phase III DILO has started the design of a new MicroPunch needle loom series as an industrial solution for a 24/7 operation going beyond the capabilities of the pilotline machines. This MicroPunch series SC is capable to run at stroke frequencies of up to 2,500 strokes per minute and to provide an enlarged capacity for through-put speed and production rate for lightweights like wipes of 40 g/m2 to be run at a speed range of up to appr. 170 meter per minute and more at the winder. Some of the latest mechanical design features which include carbon fiber reinforced needle beams and boards will provide the necessary safety in continuous operation which requires additionally features for cleaning needling zones from fiber dust, and also to provide measures to detect particles within the fleece as well as foreign matter on the surface through inductive, radiometric and optical detection systems. Blower fans are installed for the cooling of the high-speed main shaft modules within the needle beam drive mechanism as well as those for dust removal and cleaning.
Additionally, to the development of features of an industrial series, in the mechanical, electrical and technological area, an array of test stands have been created to study needle wear and behavior, maintenance and cleaning, high-speed performance of mechanical elements as well as for the research of fiber behavior apt to quality hygiene materials. In that context DiloGroup is aiming to provide an environmentally sustainable range of product qualities made of bio-degradable fibers like Viscose and natural fibers as well as out of biopolymers.
All in all, the new MicroPunch series are designed to offer a consolidation technology working at a largely reduced energy consumption level along with the elimination of water consumption when manufacturing lightweights for a large range of purposes.
General Background of MicroPunch – Intense Needling
During the past decades, a lot of progress has been possible in the development of needling technology on the basis of staple fibre. Machine builders have been successful with web forming and consolidation to give a considerable increase in product quality, foremost homogeneity, production capacity and efficiency. The awareness in the public of the importance of needling according to statistical production data of an abundance of applications was not always present. For years, there was a head-to-head race of nonwovens from staple fibre and endless filaments reflected in the respective production data. A similar competition took place among the consolidation technologies of hydroentanglement and needling. The market was divided in the applications of needled and hydroentangled products. Needling because of its applications to any fibre material which spreads over a very large range of weights and fibre finesses controlled the higher weight range mostly over 100 g/m2 . Only in the low weight range between 30 g/m2 and 100 g/m2 of products out of fine fibre water entangling has been extremely successful also fuelled by the growth rate of the consumption of hygiene materials where hydroentangling dominates and has surpassed the production volume of needled products recently. For a long period it appeared as if intensive needling could not penetrate this important sector of lightweights by the application of highest needle densities, finest needle barbs and very high stitching densities in the weight range of 30 g/m2 to 100 g/m2 . The restriction of needling was the lower productivity which created a big hurdle to achieve an economical production when comparing the cost per kg nonwoven material of needled or hydroentangled lightweights.
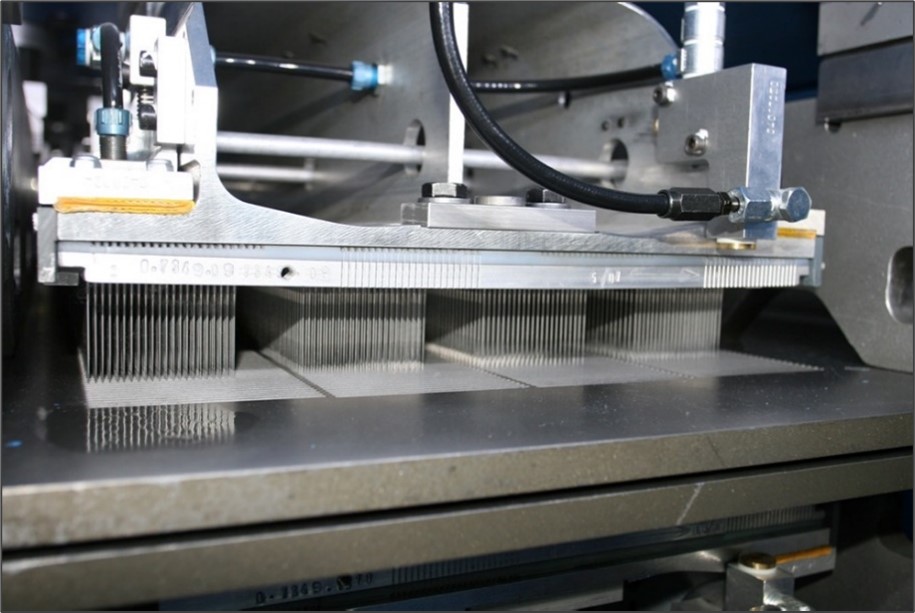
New Requirements for Sustainability
More recently, the development of prices for energy, foremost electricity and gas, together with the increasing shortage of water, a re-evaluation has started where economics are not solely considered but rather are related to environmental consequences caused by the production industry. For Dilo as a needling specialist it was therefore motivating to reconsider the potential of needling to better penetrate the fine and lightweight sector. The individual elements of intensive needling have been analysed and partly revised.
Engineering Tasks
It was clear that the high production efficiency needed was only possible through the two-dimensional kinematics of the needle beam be it HyperPunch or CycloPunch. The necessary high advance per stroke of approx. 50 mm per stroke requires nevertheless very high stitching densities in order to gain enough abrasion resistance of the product, which calls for an extreme increase of the number of needles in the boards. Textile technological simulations showed that an increase from about 20,000 needles/m/board up to 45m000 needles/m/board would be necessary. At the same time, it was clear that the Dilo needle modules had to be loaded into a specialty needle board in order to fulfil a precise arrangement and a quick exchange when necessary.
The complete needling zone had to be modified through “wire plates” which replaced drilled or slotted stitching plates. Just in time to be presented at ITMA 23 in Milan these design elements could prove that intensive needling using high needle densities at high advances per stroke could be applied.
The economics, of course, are greatly influenced, by the current high costs of electricity to drive the high pressure pumps and for gas which is needed to dry water out of the entangled fleece. It is obvious that also an increasing water shortage worldwide will influence the economics of needling versus hydroentangling.
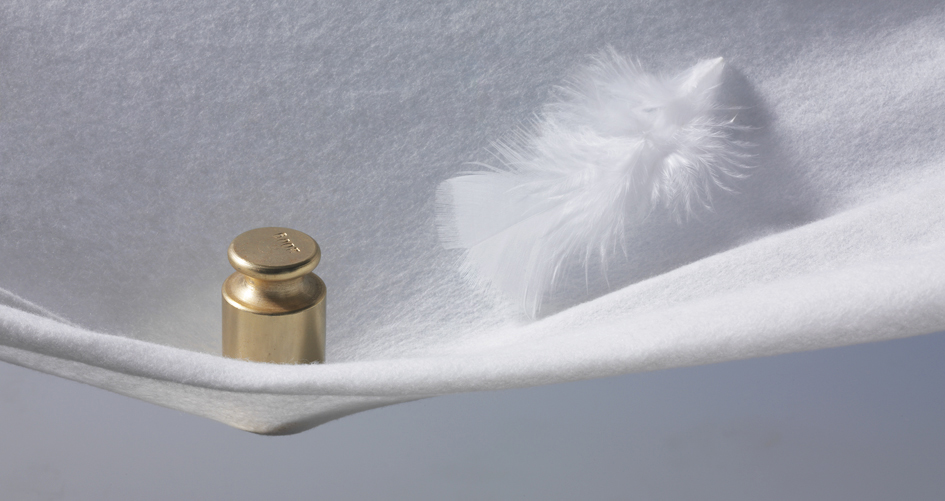
Environmental Aspects for Single Use Hygiene Products
It is also obvious that hygiene wipes should consist of biodegradable fibre in order to release them after a single use to a decomposing process in an environmentally friendly manner. Therefore, it should be a goal to eliminate polyester fibre or polypropylene in single use lightweights and rather apply viscose, cotton, other natural fibre or biopolymer materials instead. A side effect of the use of viscose and natural fibres is their capacity to store moisture and hold water. This capability is particularly important in hygiene applications and is negative when hydroentangled nonwovens have to be dried in ovens. At the same time, it is a fact that in carding viscose and natural fibres, the throughput-rate is considerably lower when comparing it with processing polyester or polypropylene fibres. Consequently, questions of economics in the field of hydroentangling and needling have to be evaluated by ecological and economic criteria.
Considerable Cost Reductions through “MicroPunch”
Simulations and calculations of production costs show that cost reductions mainly depend on product weight and are to be expected in a range of up to ca. 50 % when needling instead of hydroentangling is applied. These numbers, of course, have to be verified case by case while considering all fibre and production parameters through production tests possible on the Dilo R&D and demonstration line. Typically, for the production of wipes complete nonwoven lines are used in a working width of approximately 3.6 – 3.8 m. When water entangling is applied in such lines, the electric power is more than twice the power used for needling, needed for the high pressure pumps, for filtering the circulated water and for vacuuming the soaked fleece. Water and heating gas for drying is not used in the mechanical needling process. Also, the consumption of fibre material is less in a needling line because its fibre waste is easy to recycle. The high pressure pumps are needed in hydroentangling lines in order to create a stable jet to penetrate the fleece. In contrast to a needle made from steel which is useful for several hundred millions of strokes, the water jet loses its complete kinetic energy after it has penetrated the fleece once.
Technological Aspects
Staple fibre opening, blending, dosing and card feeding need to be adapted to inline web forming, crossline or combinations of inline and crossline web forming. At the beginning of hydroentangling technology the preferred line configuration was inline and crossline web forming through direct cards and card cross lapper combinations whereas during the last two decades mostly the standard of two inline-cards was applied in working widths of approx 3.8m. More recently, in Asia requirements shifted to better CD strength or an even MD and CD strength ratio in the sector of hygiene and medical products.
“MicroPunch” intensive needling technology should include random carding preferably applying random and condenser rollers available from Spinnbau for decades. Depending on the choice of the type of line with or without cross lapper, fibre throughput is heavily influenced since lines including cross lappers naturally have a reduced maximum line speed, therefore only state-of-the-art cross lapping including high layering precision and highest web infeed speeds should be chosen, particularly when the lines have a rather low layering width of normally below 4 m. This requirement is best fulfilled with the DILO HYPERLAYER technology were the web is processed between two screen aprons which carry the web from infeed to the layering point almost without dimensional change, MD draft and CD shrinkage. Therefore, layering precision and lapper joints are optimum when hyperlaying is considered which allows maximum nominal speeds of up to approx 200 m/min, however related to larger layering widths. The line design normally includes lap drafting which is improving the throughput and to some extent fibre orientation. CycloPunch kinematics realize advances of approx. 50 up to 65 mm per stroke resulting in 50 to 65 m/min throughput speed in the needling line at 1000 strokes/min. Without regard to the draft during needling and in end-of-line components, including configurations of drafting units, nominal throughput speed range of approx. 125 up to approy.160 m/min at 2500 strokes/min can be expected. Additionally, draft ratios however increase that speed before winding. Longitudinal draft of approx. 15 to 30 % can be chosen and may raise the throughput speed to approx. 180 to approx. 200 m/min at a capacity of one card to provide approx. 30 to approx.. 40 g/m2 web mass or more when two cards are applied in line.
Of course, the economics of such a complete line depend on the production per hour which is crucial to define the fixed costs per one kg fibre mass in the end product. While calculating the economics it is important to know that different fibre types also influence fibre throughput in the carding units. Viscose and natural fibre only allow lower production rates when polyester is left out of the blend. At the same time, it is clear that the more viscose or natural fibre is applied in a blend the higher is the retention of water in the fleece which influences considerably the amount of gas needed to dry it after hydroentanglement.
The increase of entropy in a blend is making it difficult and expensive to separate the fibre components later for recycling since polyester cannot be biodegraded. Expected end of line speeds when using 100 % viscose fibre are limited to approx. 210 to 230 m/min at the winder. This basic relation explains the limitation of economics of hydroentangling lines with their respective production capacity and makes obvious that the production capacity of “MicroPunch” needling at around 170 to approx. 200 m/min has come very close to the production speeds of approx. 220 m/min of hydroentanglement lines when running viscose only. Therefore, the total costs per kg of nonwoven material from a needling line is considerably lower compared to a hydro-line because of the advantage of the dramatic savings in electricity and the complete elimination of water and gas consumption.
Through the possibility of technological research at the DILO Textile Research Centre by carrying out product development for the various applications of “MicroPunch” needling, specific questions of the economics using different fibre materials and combinations can be answered. “MicroPunch” does offer an advantageous alternative to other consolidation techniques. After verification of those results and their influence on the investment, engineering can provide alternative line concepts from fibre opening up to end-of-line functions, cutting, winding, converting and packing. Depending on the required throughput of fibre per year and the nature of fibre orientation web forming technology, production capacity of the needling line is defined.
Efficient fibre suction and filtration for the needle looms is necessary and is realized through a suction filter station TFS of DiloTemafa designed by the Air Systems Engineering department. An additional cleaning system is attached for continuous operation of these specialty needle looms. The variety of ”MicroPunch” nonwovens is large and maybe chosen in a weight range between 30 or 100 g maybe including up to 120 to approx.150 g/sqm. Specifics to be verified by tests and trials. Of course, other consolidation techniques may be added in order to provide different product characteristics, physical properties and features, for example by calendering, where calenders are included by DiloSystems engineering and general contracting. Together with our partners DILO offers development, tests and trials including different finishing technologies in the framework of comprehensive development work. The outlook of producing light and fine fleece material based on staple fibre through the intense needling technology “MicroPunch” will offer economic as well as ecological solutions.
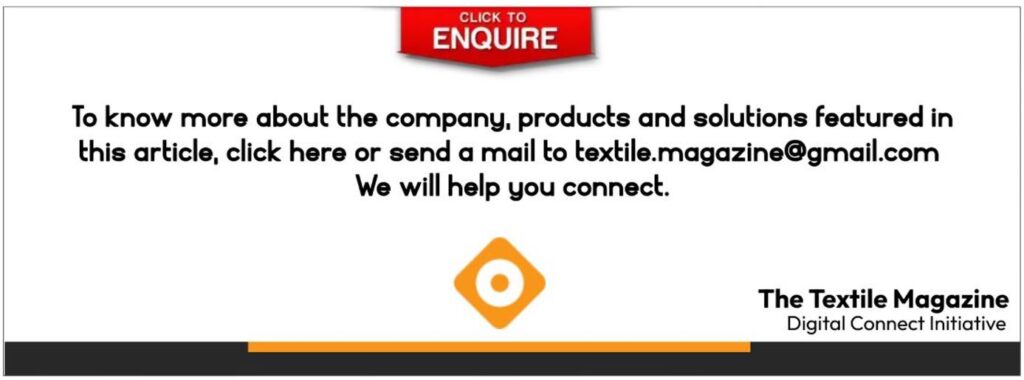