In the textile industry, compressed air is required at every level of manufacturing to power equipment and other multiple applications in the production process. Apparel manufacturers prefer oil-free screw or turbo technology due to its high productivity for the operation of air jet looms. For spinning, the preference is for low cost oil-injected screw compressors with downstream filtration to get technically oil-free air with only 0.001mg/m3 residual oil, similar to that of the oil-free compressed air generation. For the manufacture of technical fabrics, compressed air is used as an energy source.
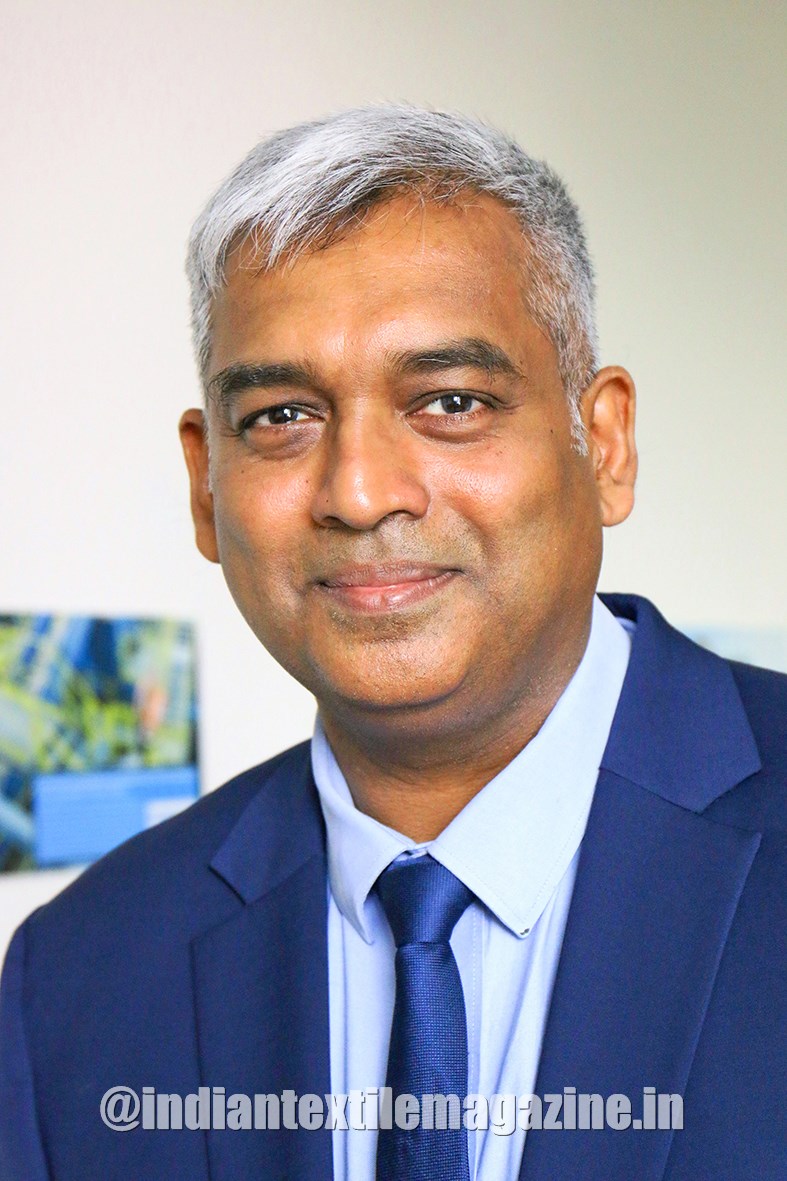
BOGE Kompressoren is a key player in this sector, providing a range of air compressors perfectly suited to textile manufacturing and its growing needs.
BOGE’s oil-free compressed air systems offer several advantages: they are clean and non-toxic and can transport large amounts of energy at the same time. The high energy density not only ensures lower weight of the pneumatic machinery, but also increases its power, speed and accuracy.
Providing intelligent system solutions
The S-3 and S-4 series of screw compressors from BOGE are the ultimate solution to cost-effective operations in the textile industry. The oil-lubricated compressed air reduces friction and prevents corrosion and wear-out of woven actuators in machinery, thereby increasing their lifespan. BOGE’s integrated compressed air treatment systems can be equipped with advanced abilities to remove oil, water and dust particles completely for clean-air production where necessary. Available up to 315kW, the smaller footprint of the S-series is ideal for manufacturing plants with space constraint.
“With the BOGE focus control 2.0, you can connect up to four compressors and access real-time information via an LCD display, or remotely via an RFID interface. The controllers come with a built-in BLS synchronising system to further optimise operating conditions and efficiently meet the demand for compressed air in the plant,” says Nalin Amunugama, General Manager of BOGE Kompressoren Asia Pacific.
Master controllers like the airtelligence plus, geared towards smaller operations, facilitate precision control and automation of six compressors simultaneously. The airtelligence provis 3.0 allows an unlimited number of compressors, compressed air networks and accessory components to be controlled and managed proactively based on consumption.
Setting new standards in pressure levels
BOGE’s turbo compressors are powering the world of compressed air into a new era of cost and energy savings. Its LPT 150 sets a new benchmark in oil-free air compression. With the LPT 150, air can be compressed up to four bar at a higher degree of efficiency than comparable screw compressors. A permanent magnet motor and air-guided drive shaft make this possible.
The design technology of the turbo compressor enables the entire drive mechanism to work without lubrication, guaranteeing low-wear operation and significant energy savings. The LPT 150 is also setting new standards for weight and noise pressure levels.
“Smart technologies in textile manufacturing are only at the beginning of their prime. BOGE’s air compressors and innovative technological solutions are already paving the way to make textile processing quicker, more flexible and sustainable,” Amunugama says.
About BOGE KOMPRESSOREN
As one of Germany’s oldest manufacturers of compressors and compressed air systems, BOGE KOMPRESSOREN has 112 years of experience. Be it high speed turbo compressors, screw compressors, piston compressors, scroll compressors, complete systems or individual devices, BOGE meets the most diverse requirements and highest standards, with precision and quality. In Asia Pacific, BOGE’s products are sold and serviced through a dedicated network of 48 distributors.