InspirOn, established in 1974, set up its production facility for the manufacture of flyers. The technology for flyer was from C. Eugen Maier, Germany. From the very beginning, the flyer was adopted as standard part by all leading speed frame manufacturers in India. In 1991, the collaborator in Germany went out of business. An opportunity was thus created to supply to all European manufacturers, viz., Rieter, Saurer, Marzoli and Electro-Jet, besides continuing to supply to local OEMs. By continuously improving upon the flyer technology through its own R&D Department, it attracted sustained demand from all the OEMs.
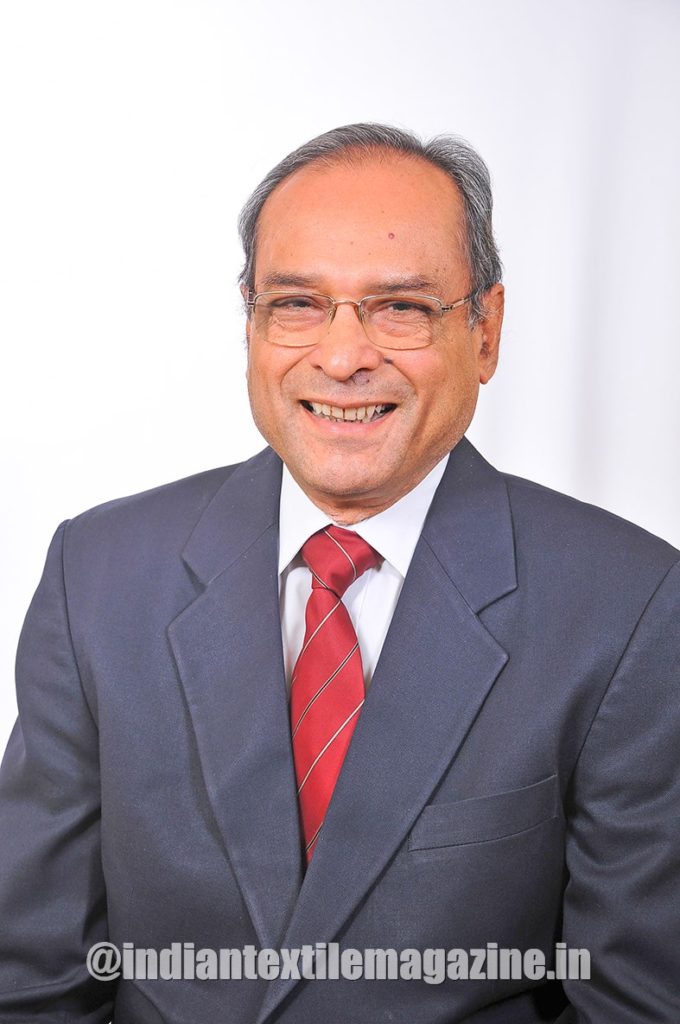
InspirOn has added to its textile engineering business another product, namely, hot air stenter. The technology for it was provided by A. Monforts. Since 2012 the InspirOn R&D centre has been approved by the Department of Scientific and Industrial Research (DSIR), Ministry of Science & Technology. A team of design professionals has been regularly working at this centre to develop new technologies which have made the indigenously manufactured machine at InspirOn comparable in performance and energy efficiency to the world’s best.
InspirOn has also strategically added non-ferrous foundry business. Engineering Services for mechanical and electrical design business, commonly known as Knowledge Process Outsourcing (KPO), are also developed where their software engineers work with European equipment manufacturers.
Mr. Prakash Bhagwati, Chairman of InspirOn Engineering, has stated that through sustainable improvement in stenter performance, Inspiron will be able to showcase at ITMA 2019 its competence to produce superior quality in a very cost-effective manner with the following features:
- Increase in drying efficiency up to 15% is achieved through patented nozzle design “UNIFLOW”. Besides considerable improvement in drying efficiency, the electrical energy, mainly consumed by driving blower fans, is also being saved to the extent of 15-20%.
- The squeezing efficiency has been improved by 10-12% with the appropriate selection of rubber technology and nip patterns. In addition, the trough design is modified to ensure minimum wastage of finishing chemicals, quick drain and fast cleaning, etc.
- The following features have been developed considering Industry 4.0 requirement at customer’s end. The standard features are:
- a) Process Automation: InspirOn has developed its own controllers for the control of process parameters like dwell time, residual moisture and exhaust moisture. This automation, as an integral part of Industry 4.0, helps in optimizing the stenter efficiency as well as improving the operator comfort.
- b) The self-developed SCADA system enables real time data monitoring and control functions for maintaining and sustaining quality of the fabric.
- c) With the help of remote access InspirOn can have quick diagnostic assessment in case of malfunction and suggest remedial action. Remote visualisation on tablet or smart phone for real time data monitoring is also possible for the stenter user.
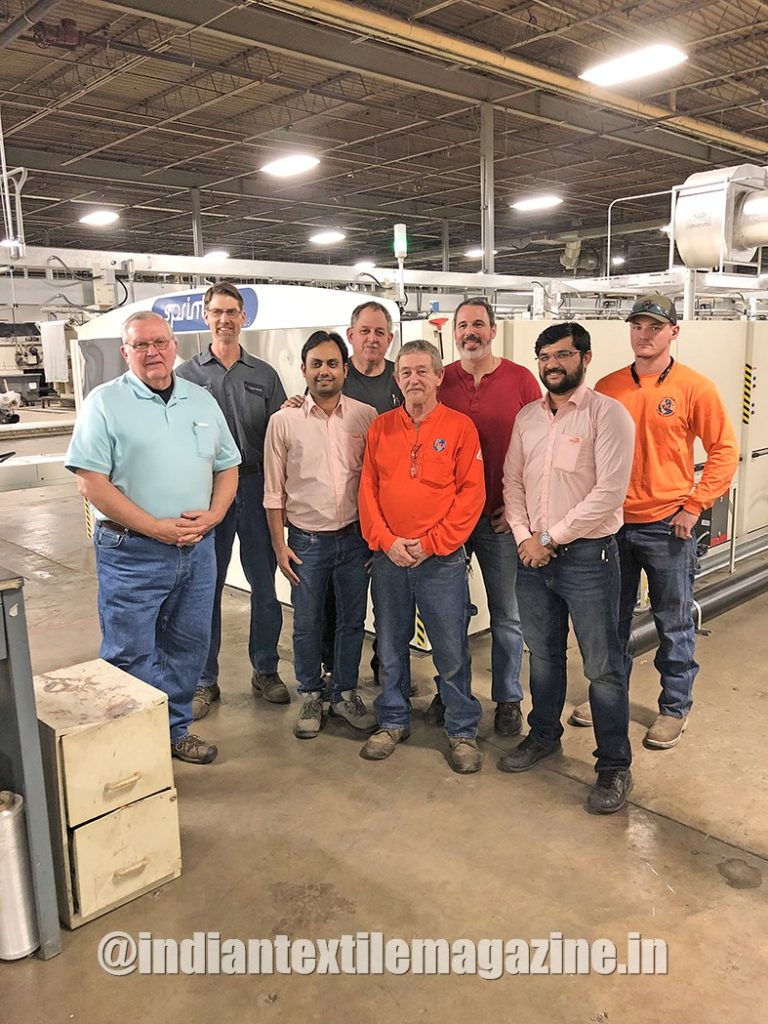
Asked how the newly developed stenter, i.e., Motex 15000, has been accepted during last financial year, Mr. Bhagwati said: “It was a brilliant year for us. We were able to get customer confidence, and hence received the maximum number of orders from corporate clients.”
The company through the Product Office, also worked on building the relationship with the customer by taking feedback periodically. This effort yielded beneficial results by fetching orders from big clients like Vardhman, Arvind and Birla Century, among others, who were more than satisfied with the product and overall service of the company.
During the last year, InspirOn Engineering also crossed Indian borders and entered the US market with unprecedented success! The recently installed stenter, branded “SprintOn”, aptly named to match the high-speed performance, at Crypton Inc., North Carolina, has set the market literally on the move!
This dream story began with the flawless shipment followed by installation in a record time, handing over the machine for production within a time frame not even envisaged by the management of Crypton Inc.
The SprintOn stenter meets with all the essential safety features which are mandatory in any US production house. The ten-chamber stenter is an integral part of an intricately designed coating line and the entire synchronisation of various components and their drives was done by the InspirOn team.
The performance levels have exceeded those which were committed, so much so that Mr. Chip King, Manufacturing Head of Crypton Inc., conceded that SprintOn has been the best thing that has happened to him in the past 25 years that he has been around in the industry. This is remarkable considering the fact that he has European set-up in his state-of-art processing plant which caters to the demanding furnishing and upholstery industry.
In a heart-warming letter addressed to Mr. Prakash Bhagwati, Mr. King has well appreciated the exemplary execution of the SprintOn stenter.
When it comes to flyer business, InspirOn has its major share in the European OEM market and has been successful in reaching out to countries like China with its flyer technology.
By the year 2024, InspirOn has plans to expand in a big way its business related to textile engineering, non-ferrous foundry and engineering services with its focus on export markets, more particularly in developed countries.