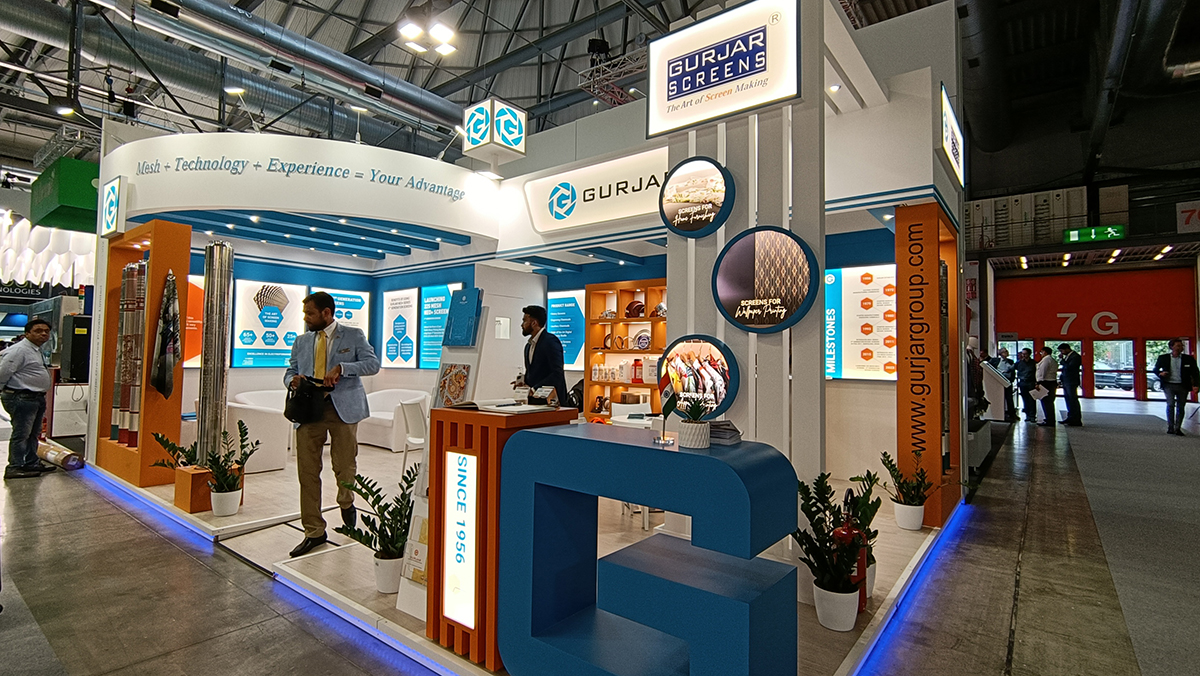
While digital printing has become popular, Gurjar’s Rotary Screens remain a more economical option that delivers its own unique kind of quality. Their commitment to innovation has allowed them to achieve results that are comparable to digital printing, which is a significant achievement.
The Gurjar Group’s 67-year long journey began in 1956 as pioneers in photo engraving of copper rollers to print textiles, a unique technique for printing on fabrics. The design pattern in the market was limited to pantograph engraving at that time, which resulted in a flat and solid effect on the fabric. Innovating in sync with the times with the advent of Rotary Screen Printing Machines, Gurjar’s pursuit of progress led them to be the first manufacturers of Galvano Designer’s Screens in 1972 which revolutionised the way people saw textile printing in India. Thereafter in 1979 they entered into a technical collaboration with Erstwhile Consolidated Engravers Corporation USA to introduce Nickel Perforated Rotary Screens under the brand name of Rotel Rotary Screens which are still the market benchmark for quality.
Today, while digital printing has become popular, Gurjar’s rotary screens remain a more economical option that delivers its own unique kind of quality. Their commitment to innovation has allowed them to achieve results that are comparable to digital printing, which is a significant achievement. As a leading textile company, Gurjar has always been committed to meeting the evolving needs of its customers. Today’s customers demand high-quality products at an affordable price, and Gurjar has responded by constantly innovating and improving its product line. By focusing on customer education and awareness, Gurjar has been able to stay ahead of the curve and incorporate customer feedback into its product’s.
New Technologies
One of the ways the company has improved its efficiency and performance is by increasing the fineness of its prints through the use of higher mesh count screens. Recently, Gurjar has launched a 225-mesh screen, which falls under the 4th generation screen technology, allowing for even finer designs and improved aesthetic appeal. The use of 4th generation screens also brings greater efficiency in the production process, with reduced dye stuffs usage, lesser requirement of manpower and increased automation. In addition, Gurjar has also invested in advanced machinery and technology to ensure consistent and efficient production.
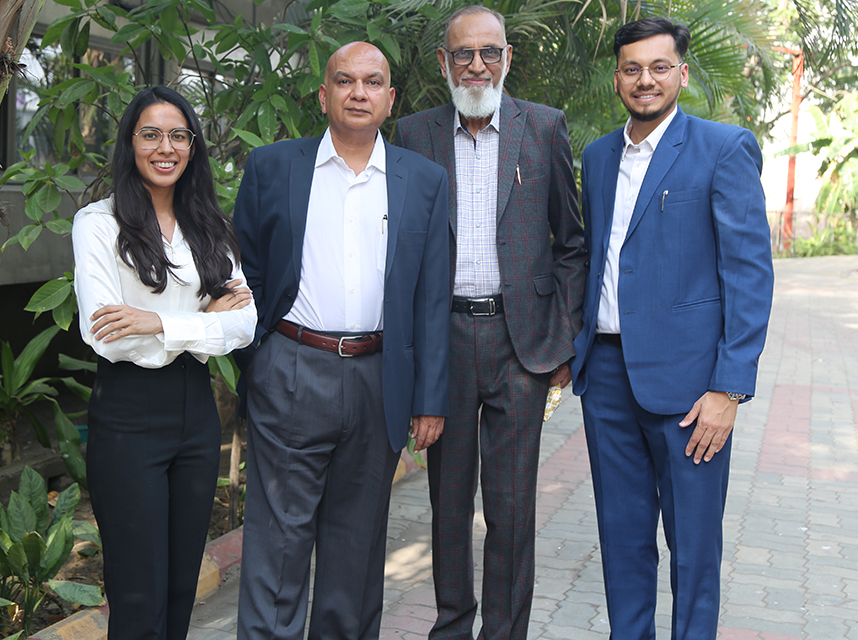
For example, they use high-speed machines to ensure faster production and reduce lead times for their customers. Their commitment to quality and customer satisfaction has helped them maintain a strong reputation in the industry and establish long-term relationships with their clients. They are constantly striving to improve their processes and offerings to provide the best possible value added solutions to their customers. The benefits of incorporating 3rd and 4th generation screens into rotary printing setups are indeed numerous.
One of the most significant advantages is the ability to perform surface printing, which requires less pressure and results in higher printing speeds and less consumption of dyestuffs. In comparison to a second-generation screen, which typically uses around 5% of dyestuff concentration, a 3rd or 4th gen screen uses only 3%, without any noticeable drop in print quality. This reduction in dye consumption amounts to savings of around 30%, which is a substantial amount when you consider the volume of fabric that is printed every day. One of the most remarkable advantages of using 4th generation screens is their ability to produce output of the same quality as that of digital printing setups.
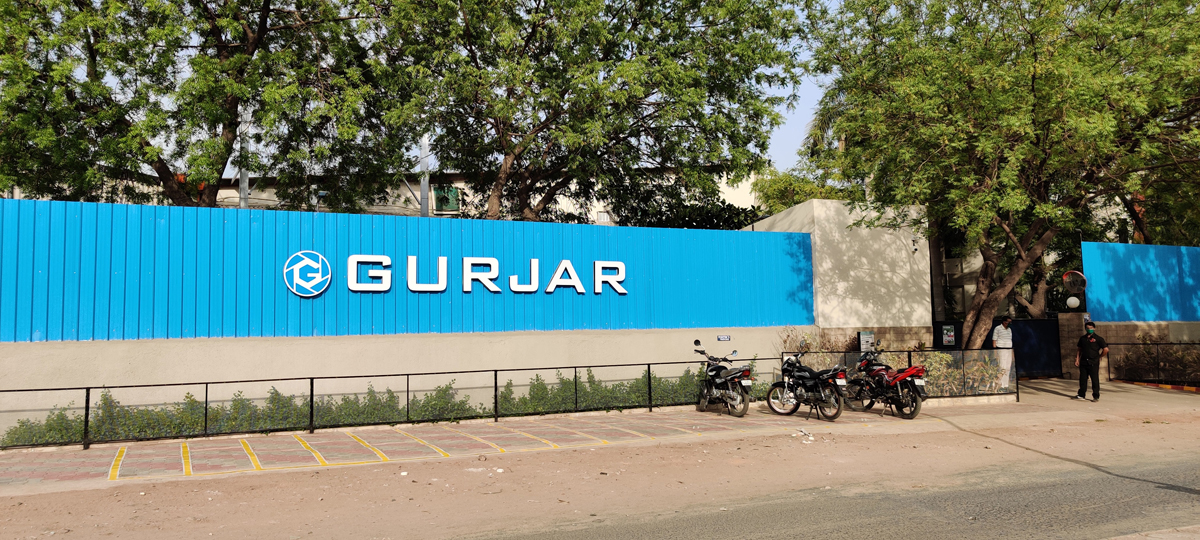
Although the initial cost of purchasing a 4th generation screen is higher than that of older generation screens, the return on investment is very high due to the phenomenal performance. By switching to these screens, businesses can save around 30% on print costs, which is a considerable amount that can be reinvested elsewhere. Moreover, Gurjar has also mastered the art of providing more to its buyers. The company possesses a range of engraving chemicals that help them give an excellent and sharp image to transfer on to the fabric. The photo emulsion they have made use of is very precise and cohesive, which allows for the creation of intricate designs that are difficult to reproduce using traditional printing methods.
By incorporating these additional services into their business model, the company is offering their customers an even greater value proposition. Under their product range, Gurjar Screens is the only manufacturer of the 4th generation rotary screen printing technology. With this advanced technology and their more than 50 years of experience in the screen making industry has allowed them to manufacture top-quality screens that have become the benchmark in the market.
Pioneering Efforts Pay Rich Dividends
However, screen making by design is a very precisely engineered product and reaching this level of expertise comes from decades of experience and our inhouse R&D cell. We have walked through the entire technical advancement of our industry from 1st generation rotary screens to the revolutionary 4th generation rotary screens. In 2015, during the International Textile Machinery Exhibition (ITMA) at Milan, Gurjar recognised the growing popularity of digital printing, which was considered expensive at the time. This realisation led them to explore how they could compete with digital printing using rotary printing technology. Their hard work and determination resulted in the creation of the 4th generation screens, which has allowed them to establish themselves as an apex player in the textile printing market.
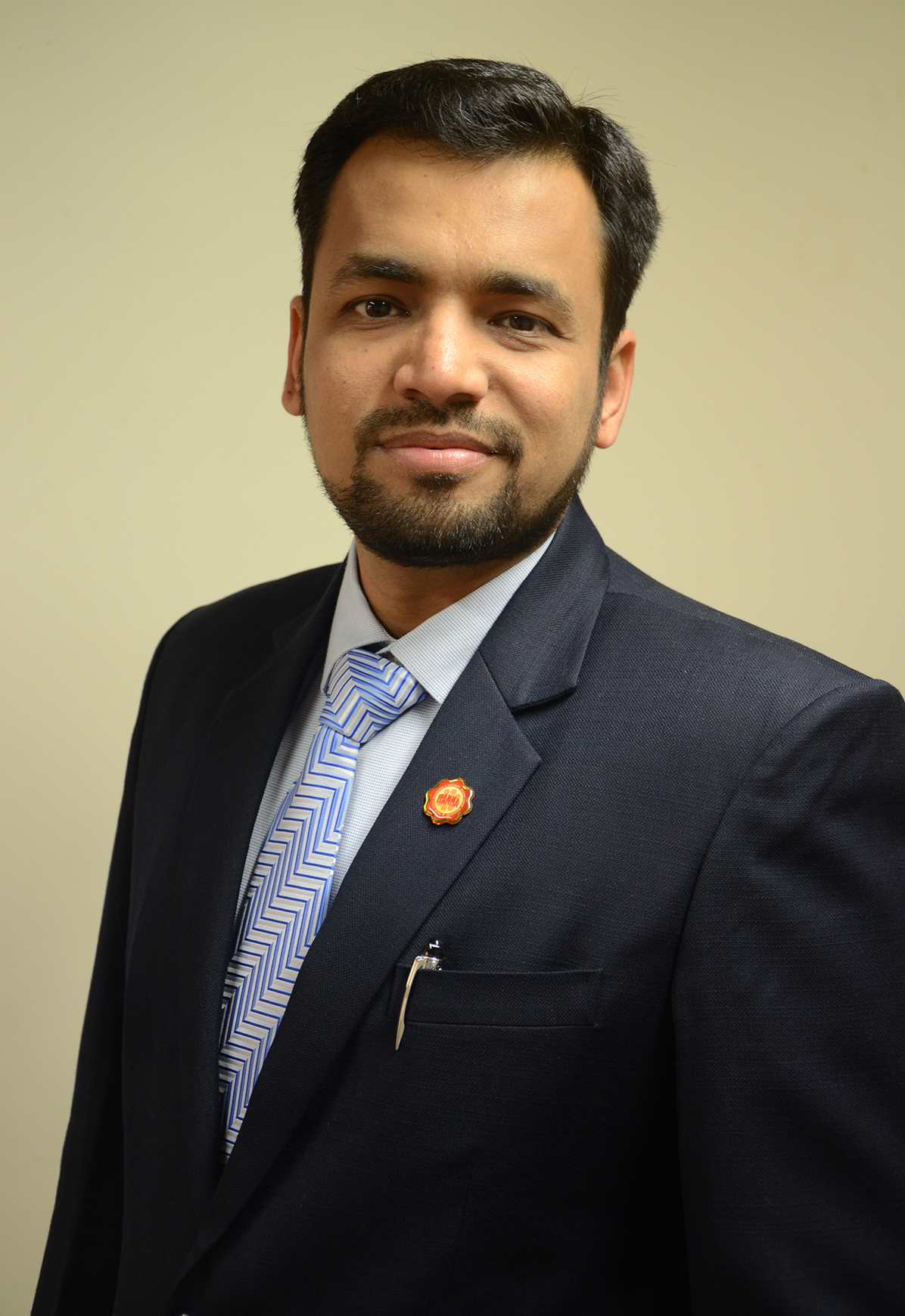
The Gurjar Group is proud to offer a comprehensive range of products to their customers. Their product range in 2023 includes a wide variety of offerings such as complete and comprehensive range of screens, chemicals and all the necessary components for rotary machines. Their in-house engraving studio is fully equipped with advanced engraving machines and staffed by skilled technicians who can handle all aspects of the engraving process, including coating, designing, and screen stripping. Regarding their sales split, Gurjar has a longstanding presence in the global market and has been exporting to over 30 countries for more than three decades. While their current domestic market is experiencing significant growth, they remain agile and responsive to market trends and opportunities. Therefore, the company’s domestic-to-international sales split is not fixed and varies according to market conditions.
Participation at ITMA 2023
At the ITMA 2023 event slated to be held at Milan, Gurjar has wasted no time in setting up its stall in Hall 7, Stand D, Stall No. 302. They have designed a two-side open stall that is visually appealing and easy to navigate and are expecting clients from Asian to African to South American countries. Their focus at the event is to educate the printers on how they can unlock the full potential of their rotary screen printing machines using Gurjar’s 3rd and 4th generation screens. The company’s primary objective is to showcase the significant difference between a 2nd generation screen and their advanced screens in terms of efficiency, dyestuff savings and overall quality of print. Gurjar is confident that by using their screens their customers will be able to challenge the most delicate & complex print designs in the future with these higher mesh screens.
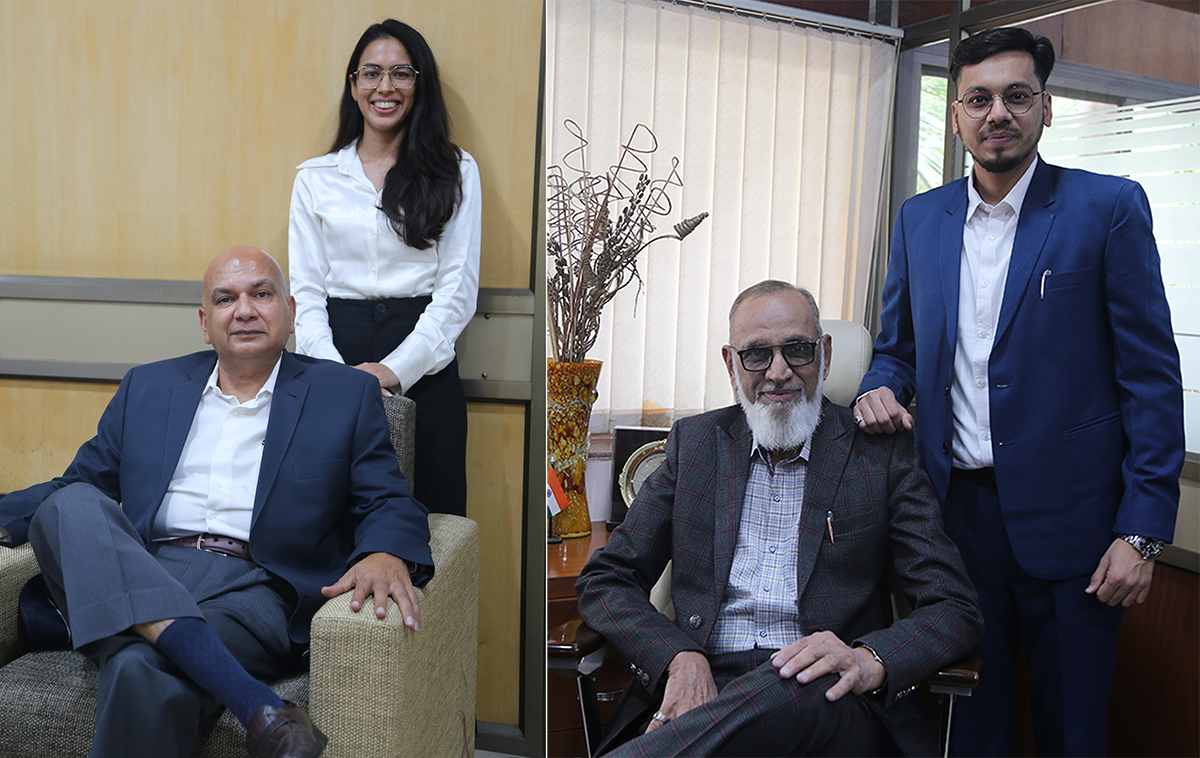
Gurjar’s more than 50 years of experience in screen making and constant innovation through in-house research and development has put them ahead in the game. Gurjar is officially launching their 225 mesh screens at the ITMA 2023 Milan event. They are also introducing certain engraving chemicals and a special high definition photo emulsions chemicals that can be used for laser machines, enabling the finest printing with accuracy down to one pixel. Customers can expect to see and experience the latest innovations and advancements in screen making technology at this event.
The Way Ahead
Gurjar’s commitment to innovation and excellence has positioned them as a leader in the textile printing industry for the past 67 years. Looking towards the future, Gurjar is focused on expanding into new markets such as paper, food and home furnishing, by utilising their current and investing in new technology. The brand’s reputation for value and quality is what has made them successful thus far, and it is their dedication to pushing the industry forward that will continue to drive their growth. With this mindset, Gurjar is on track to achieve a centenary milestone and continue to be a driving force in the world of printing.
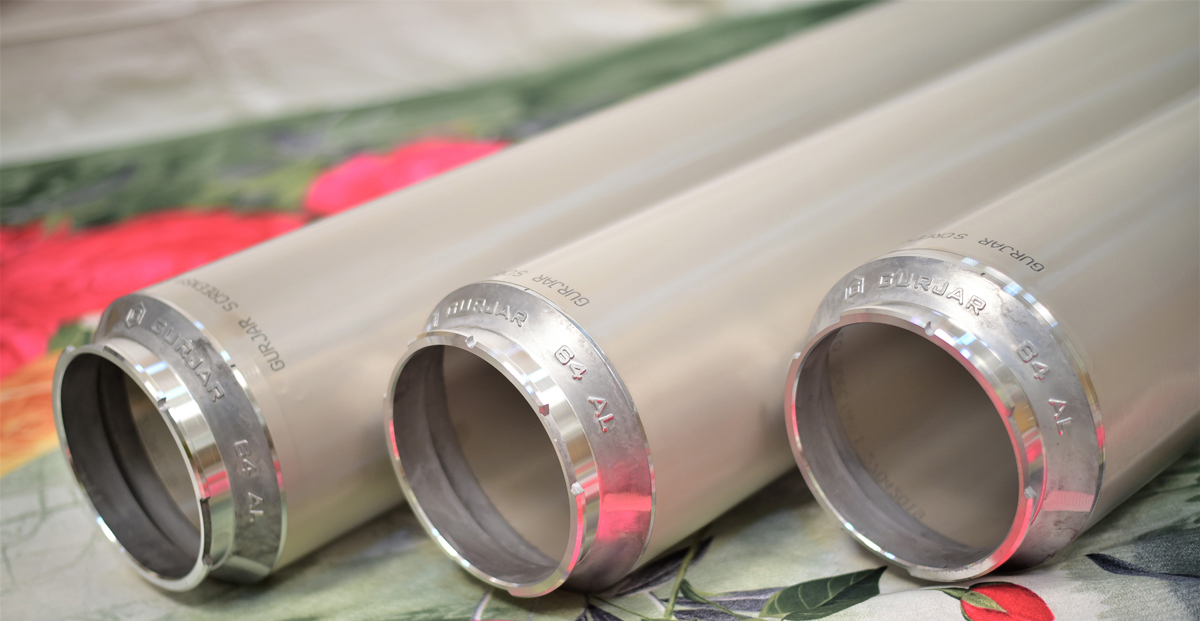
Gurjar’s unwavering pursuit of progress and excellence has established them as a symbol of innovation in the textile industry. Their journey serves as a reminder that with hard work, perseverance and an unwavering commitment to innovation, anything is possible. At Gurjar, the priority is always to provide high-quality products at affordable prices rather than focusing solely on maximising profits. This commitment to quality has earned them the trust and loyalty of their customers, who appreciate this dedication to delivering superior products and services.
The company is excited about the potential opportunities that ITMA Milan 2023 will bring for them. Their participation in the event will allow them to showcase the latest innovations and educate the industry on how to unlock the true potential of textile rotary screen printing machines with their screens. “We are confident that our products and expertise will make a significant impact on the textile printing industry, and we look forward to exploring new partnerships and expanding into newer markets. Our commitment to innovation through our in-house research and development has been one of the key drivers of our success over the years. We take pride in our ability to develop cutting-edge technologies and processes that not only meet but exceed the evolving needs of our customers in the textile printing industry,” the management said.