KTTM to double ring spinning frame output capacity
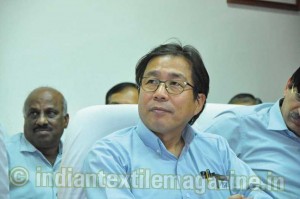
Toyota Industries Corporation (TICO) of Japan has announced its plan to double ring spinning frame production capacity at its Indian subsidiary Kirloskar Toyota Textile Machinery Pvt. Ltd. (KTTM), Bangalore. Production of ring spinning frames at the TICO Kariya plant in Japan will be transferred to KTTM by synergizing production facilities of ring spinning frames.
KTTM, the joint venture, was established in 1995. It commenced commercial production in 1997 for manufacturing of high-speed ring frames of world class technology, primarily for the Indian market. KTTM is currently manufacturing the RXI 240 model and has delivered three million spindles till date. In due course Toyota Industries plans to have the global model RX 300 produced at this plant in India. The R&D in spinning technologies and the designing aspects of the machine will be given more importance at the headquarters in Japan.
Since inception, KTTM has been a pioneer in developing and introducing the latest technologies in ring spinning frames with the support of TICO. The introduction of highly successful SCD (Auto Doffer), e-lift, longer versions of ring frame, namely, 1440 & 1824, are the few unique features which set the trend for the Indian spinning industry. There is a steady order inflow to KTTM in the current fiscal, and the order book is full for the next 12 to 14 months. With its well-established sales and service network countrywide, KTTM is poised to step up its steady growth rate in tandem with the capacity increase.
The company will be expanding its production capacity in a phased manner to meet the growing demand for the RX300 model the world over. This strategic move by Toyota Industries is believed to provide a major thrust to its sales and huge advantage to its customers worldwide.
3 millionth ring spinning spindle delivered
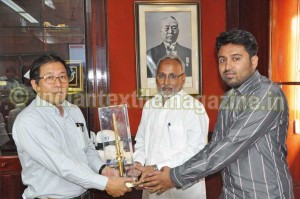
KTTM recently achieved another milestone by delivering the three millionth ring spinning spindle to K.A.S. Industries Private Ltd. of Erode. This momentous occasion was marked by a grand felicitation ceremony held at KTTM’s factory premises. On a symbolic note, Mr. Masafumi Kunito, Managing Director, KTTM, presented a golden spindle to Mr. Shameem, Managing Director, K.A.S. Industries.
Going down the memory lane, KTTM’s maiden machine produced indigenously at its Jigani plant was handed over to Mr. S.P. Oswal, Chairman & Managing Director, coinciding with the plant inauguration held on June 1, 1997. Subsequently, the one-millionth spindle in 2005 and two millionth spindle in 2010 were delivered to Mr. Sachit Jain, Executive Director of the Vardhman Group, and Mr. Manikam Ramswami, Chairman & Managing Director, Loyal Group respectively.
The K.A.S. Group, a leading player in the leather business supplying to many global brands, diversified into the textile industry in 2007. The company has established a modern, state-of-the-art spinning unit in Erode. KAS Industries currently has 45,000 spindles, which are predominantly supplied by KTTM. The company plans to further increase the capacity to 70,000 spindles, most of which will be supplied by KTTM.
KAS Industries manufactures 40s to 60s yarns which are supplied to fabric manufacturers in Indian and overseas markets. The company is witnessing increased demand in overseas market, thanks to its investment on high quality machines and infrastructure.
KTTM is steadily building a strong customer base and a good population of its machines in the Indian market. In fact, it took 10 years for the company to sell the first million spindles, five years for the second million and three years for the third million. The next million is expected to happen much faster.
TICO’s decision to move the manufacturing base for spinning machineries from Japan to India is a big boost to Indian operations. This further reinforces TICO’s confidence and commitment to the Indian market.
Saurer Group’s successful relationship with KTTM
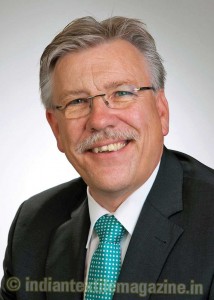
The Saurer Group has been having direct association with KTTM in India since 2008, but in general the Saurer Group with the Texparts brand has been a long-term supplier to KTTM for years. Texparts branded products manufactured from Halol, Gujarat, provide complete package solutions for excellent quality drafting systems and high speed spindles. “As a key supplier we take pride in having a close relationship with KTTM. We congratulate KTTM on this historical milestone and also feel proud for our association. We look forward to continuous close cooperation with KTTM and wish them all the best for their future growth and prosperity under the leadership of Mr. Kunito.”, says Mr. Spahlinger, CEO, Components Business, Saurer AG.
“For Saurer Texparts, KTTM symbolises the perfectionist, always craving for quality. Our plant unit in Halol has been audited by KTTM/Toyota many times. During every such audit, they walked us thru our Quality Systems with such minute details resulting in continuous improvements. We never felt at any time that our relation is customer-supplier or auditor-auditee but that of equal partners always looking for those finer contours of quality management and prevention of likely defects. Transparency at KTTM gave us ample opportunity to feel and learn high quality standards maintained in their shop from Traceability to 4M Conditions to Work Standardization with focus on continuous monitoring of Process Controls and Preventive measures”, adds Mr. Spahlinger.
With Innovative and high quality Toyota machines now being manufactured in India by KTTM, Saurer sees a huge opportunity for its components business. “We feel this will help KTTM in further penetrating the Indian as well as overseas markets and improving their market share. With TICO’s involvement in Indian operations, we the supplier’s of KTTM will be further enriched with Toyota Production and Quality Systems”, Mr. Spahlinger says.
Precitex’ high-performance cots & aprons
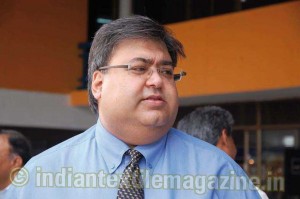
Precitex supplies high performance series aprons and cots to KTTM for its conventional ring frame as well as for ring frame equipped with compact spinning systems. The company meets KTTM’s requirement for both its domestic and overseas supplies. It has been a learning experience for Precitex and has benefited largely out of this wonderful association.
Precitex has been working together with KTTM right from the day of the latter’s inception in India. KTTM has introduced certain unique concepts in the drafting system of the machinery that calls for products with greater precision and longevity. Precitex received excellent support from KTTM for product development. The manufacturer, with repeated visits to Precitex, helped in developing the product to meet its rigid standards. Their contribution in developing suitable quality control systems is worth mentioning.
Precitex products have been in use by customers having Toyota machinery located in countries like Indonesia, Thailand, Vietnam, Bangladesh, Pakistan and Turkey. With Toyota deciding to shift its global manufacturing base for spinning machines from Japan to India and further expanding its capacity, Precitex foresees a lot of business opportunity. It has been gearing up and is confident that it can meet Toyota’s technical requirements.
In the recent past Precitex has invested heavily in expanding its manufacturing capacity to meet the increasing demand in the domestic and global markets. The company has also invested in acquiring new technologies to meet the technological challenges posed by the new generation machinery that essentially operate at high speeds and deliver high quality output.
Precitex has maintained the market leadership in India and continues to be the largest exporter of cots and aprons from India and has won several awards for export excellence.
Mallya gearing up to meet future opportunities
Mallya Steel Industries has been associated with KTTM since their inception. The company is supplying bright, peeled and ground Bars in various sizes and shapes. Mr. Rajesh Mallya, Managing Director of Mallya Steel Industries, says: “It has been an enriching experience, to say the least. We have been in this line since 1985 and without a doubt KTTM remains our best customer to date”.
“Being a global company with a great lineage, KTTM has brought in a lot of professionalism to the approach of vendor development. We were able to understand and experience the ‘Toyota Way’ first hand with many visits by their engineers and overseas experts for every new part development. We are forever indebted to them for the way they helped and guided us weather many a storm like the recessions of the late nineties and 2008-09”, says Mr. Mallya.
“KTTM considers its vendors as partners. As and when any new part or additional capacities are planned they always inform and guide us in preparing for the expanding capacities. We at Mallya Steel Industries are investing in improving our existing methods, machines and manpower and if necessary adding further to meet the future opportunities”, Mr. Mallya adds.
A.B. Carter supplies quality spinning rings
A.B. Carter India Pvt. Ltd., a joint venture with A. B. Carter U.S.A., was established in 2005 with the sole objective of offering superior rings and ring traveller solutions for the Indian sub-continent. The company is associated with KTTM since 2009 for supplying spinning rings and accessories such as traveller clearers, etc., for various ring frame models and is proud of its relationship.
A.B. Carter has so far supplied over five lakh rings to KTTM whose purchasing process has been extremely fair and transparent. The manufacturer treats its suppliers as strategic partners and this results in a win-win situation for both.
Working closely with a world class Japanese company has helped A.B. Carter to improve its quality, efficiency, service levels and also to continuously improve its product offerings. With Toyota deciding to shift its global manufacturing base for spinning machines to KTTM and further expand its capacity in India, A.B. Carter has a great opportunity to increase its business share with the manufacturer in the near future. With KTTM already indicating its ramp up plan for the next year, A.B. Carter is in a comfortable position with necessary resources to meet the growing demands of KTTM.
Inarco’s unmatched technology
Inarco, a leading manufacturer of cots and aprons has been associated with KTTM right from the inception. The company is supplying for KTTM spinning machines, including the NEW Compact Spinning System and the EXTRA LONG RING FRAMES (1824 spindles). “It’s an extremely satisfying experience working with KTTM. More importantly we are in complete sync as both our companies follow similar Kaizen practices like ‘Lean Manufacturing Techniques’, ‘TPS’ (Toyota Production System), ‘KanBan System’, etc. We have learnt a lot about ‘Inventory Management’ and ‘Vendor Management’ systems from KTTM and have successfully implemented some of them in our own factory”, says Mr. Pradipto Bera, General Manager – Sales and Marketing, Inarco Ltd.
“We have recently introduced a few niche products which are comparable to the ‘best in the world’ in quality and performance like the I-series Cots and Aprons. We certainly hope we can help Toyota completely ‘indigenize’ the cots and aprons components for their machines and still maintain the high quality standard for their global customers”, adds Mr. Bera.
KTTM-SKF, partners in progress…
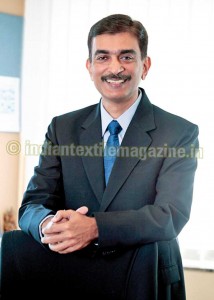
SKF’s association with KTTM stretches beyond two decades. SKF has been associated with KTTM on their various ringframe models. Currently the company is working on the latest model RXI240e-1824. SKF has been a supplier of various textile machine components like top arms, top rollers, cradles, spindle inserts in addition to the various types of bearings.
On the recent announcement of KTTM doubling capacity and moving spinning machine manufacturing to India, Mr. Sudhir Rege, Director – South Asia, Regional Sales and Services, SKF India, says: “We at SKF were very excited about the development when it was declared at the vendor meet recently. With the textile industry growing rapidly in the Asian continent, we were looking forward to this declaration to happen sooner. With every forward step that KTTM takes, their vendors are bound to grow. It has been a tradition at KTTM, that a vendor is treated as an “Insider who is sitting Outside”. We are confident to be a part of it and supporting them in all possible means in this growth story. SKF has foreseen the potential of the textile industry and have a textile segment developed specially in Asia to address the requirements of this segment. This segment is continuously striving towards all possible developmental activities and offering the best products and solutions to the textile OEMs, so that they maintain a competitive edge”.
“KTTM has high focus to deliver high quality and technology products to their customers. For SKF as a Knowledge Engineering company, customers like KTTM are preferred partners to work with. We share lot of application knowledge between us”, says Mr. Rege.
“All emerging markets, as they mature, will realize they should measure all suppliers based on how they can help them achieve the lowest TCO (Total Cost of Ownership), not through the lowest purchase price but through adding more value. While trying to add value, it is critical to note that value needs to be monetized for customers to be able/willing to pay for it. At SKF, we have a concept called Life Cycle Management (LCM) that gives an insight right from the design stage to the end of the product service life. At every stage of this cycle, we add value which in terms of understanding the application, specification, design analysis, validation, failure analysis, modification/up – gradation. Product is just a reflection of our all our activities but what needs to be realized is the amount of investment we make during each stage of the life cycle that brings the ultimate benefit to the OEM and the end-user too. We have demonstrated this repeatedly to various customers/partners and are sure to utilize this experience at KTTM also. In terms of manufacturing readiness/deliveries, KTTM has always enjoyed a ‘special’ status and we will always value this long-standing relationship”, observes Mr. Rege.