“Our Machines are known for Robustness and Long Service Life”
In an exclusive interview, Hans Wroblowski, Head of Denim and Area Sales Director SEA, Monforts, elaborates about the products of the company, their management philosophy, marketing strategies and the constant integration of new technologies to deliver better products and solutions
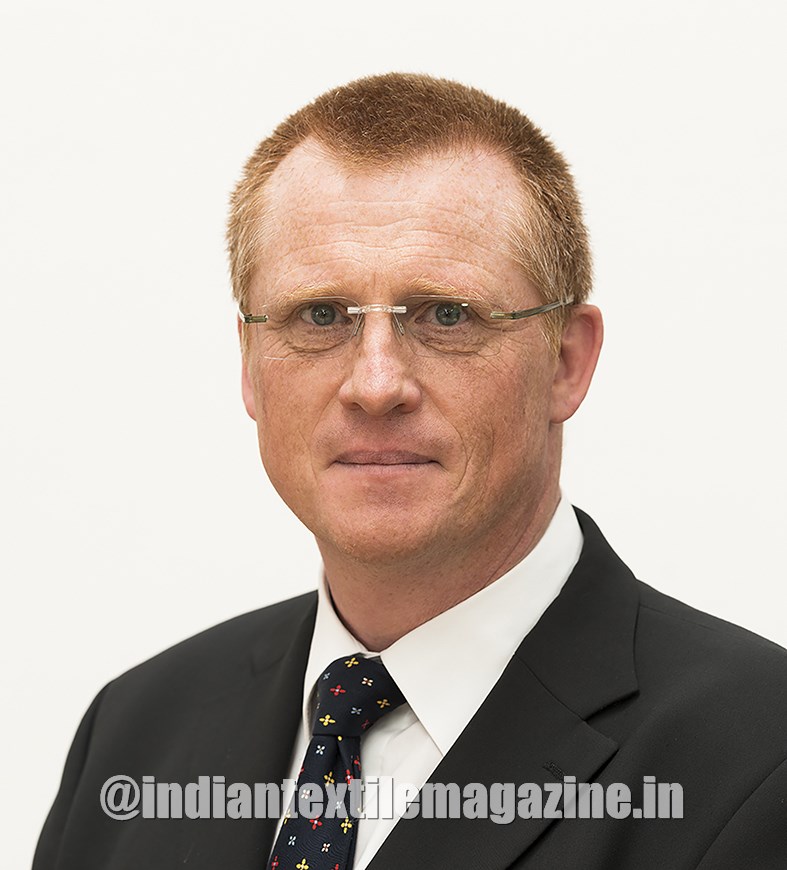
How has the ongoing pandemic period been for Monforts?
There is a growing appetite now for making progress in the textile industry and many investment decisions that were put on hold as a result of the uncertainty in 2020 are now being made. As a result, I am happy to say that we have a healthy order situation which we are responding to, despite the ongoing difficulties related to the pandemic, with the assistance of our local representatives in all markets. This includes, of course the A.T.E. Group, which has played a crucial role in the success of Monforts in India for many years.
As our representative in India, A.T.E. has enjoyed considerable success in installing and commissioning Monforts’ machines, with its service team working side by side with our own engineers to ensure the machines fully meet every customer expectation. A.T.E. has also invested in the training of sales and service staff on Monforts’ technology. Among recent installations in India, we have provided new lines to companies like Arvind Textiles, Auro Textiles, Birla Century, Himatsingka Seide, Nahar Group, Nitin Spinners, Premier Fine Linens and Vardhman Textiles.
The pandemic has put more focus on sustainability and care for our environment. How is Monforts adapting to the post-pandemic world in terms of products and technology?
The Montex machinery range is constantly being upgraded to meet evolving customer needs for greater automation, ease of operation and, of course, energy optimisation and waste reduction. With the latest Montex stenters for processes such as drying, stretching, heat setting and coating, the overall energy savings of up to 40% can now be achieved compared to a conventional stenter. The energy-optimised stenter offers different features to help save energy, including better insulation of the treatment chambers, a reduction of cold air intake at the inlet and outlet of the stenter chambers with the help of the ‘bionic fin’ slot cover, as well as new optimised gas burners and the use of preheated combustion air in combination with the MonforClean™ integrated heat recovery module.
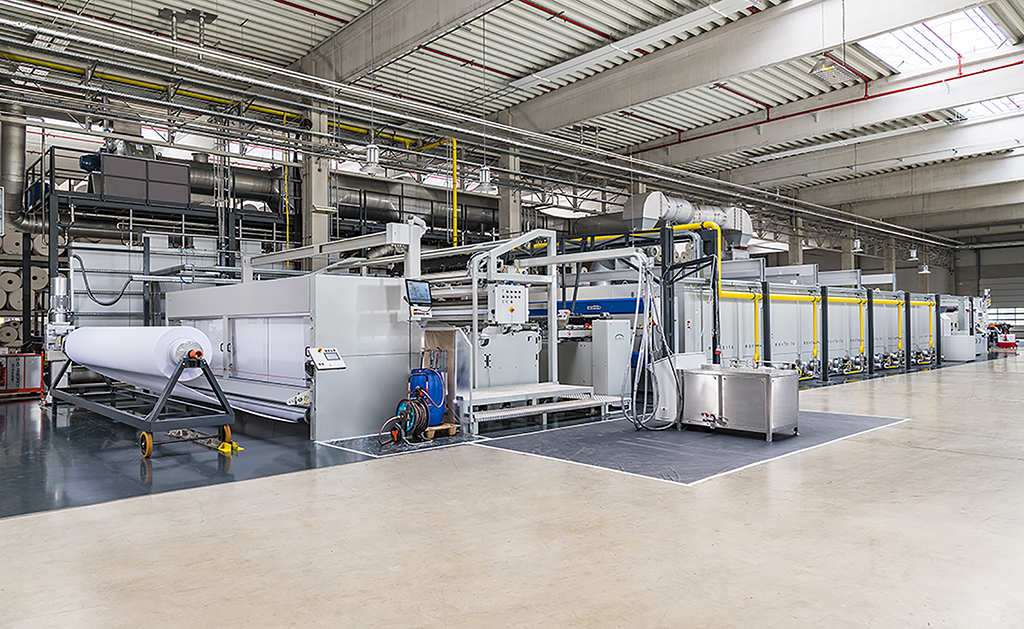
The waste heat from the drying process is used to pre-heat the drying air, resulting in a radical reduction in the conventional heat supply required compared to gas and thermal oil heating. The modular system for heat recovery can also be extended for exhaust air cleaning and odour elimination. As an alternative to conventional padding – where fabrics are immersed in a bath of the required finishing chemicals – the Monforts EcoApplicator™ can significantly further reduce the energy and water required for achieving perfect finishes via a precise direct application system. Finishes can be applied on just one side of the fabric, or both, and even separately on each side, and sealed in place via different heating zones in the stenter.
This allows endless differentiation possibilities. We have also enjoyed particular success with our Eco Line™ concept for denim in India and have recently introduced the CYD continuous yarn dyeing range based on the Econtrol® technique (a registered trademark of Dystar Colours Distribution GmbH) – the most effective and established dyeing process. Econtrol® is a pad-dry process employed in Monforts’ continuous dyeing in which the reactive dyestuff is fixed to the cellulose fibres during drying. The fixing medium is controlled by a steam or air mixture within the Monforts’ Thermex® unit.
With sulphur and reactive dyes in particular, the improvement in both dyed fabric quality and dye fixation is considerable, and with significant savings in energy and time due to the combined bleaching and padder fixation. The CYD system also integrates new functions and processes into the weaving preparation processes – spinning, direct beaming, warping and assembly beaming, followed by sizing and dyeing – in order to increase quality, flexibility, economic viability and productivity. It is also possible to process short batches of yarn in order to produce minimum runs of finished fabrics in a single continuous process. By comparing the usual processing sequences within the denim industry with the new CYD system, the advantages become immediately clear.
The pandemic has also increased focus on automation and digitisation. Industry 4.0 is getting adopted faster than it was expected. How is your company enhancing automation and digitisation technologies in its products and solutions?
The latest Qualitex® visualisation software offers the operator reliability and ease of operation with its full HD monitor and slider function, dashboard function with individual adaptation to the operating states and faster access to the comprehensive recipe data management. The Monforts’ WebUI application provides live streaming of machine data and actual and historical alarms as well as network camera feeds. Since the software is based on HTML5, it can be used on any kind of mobile device.
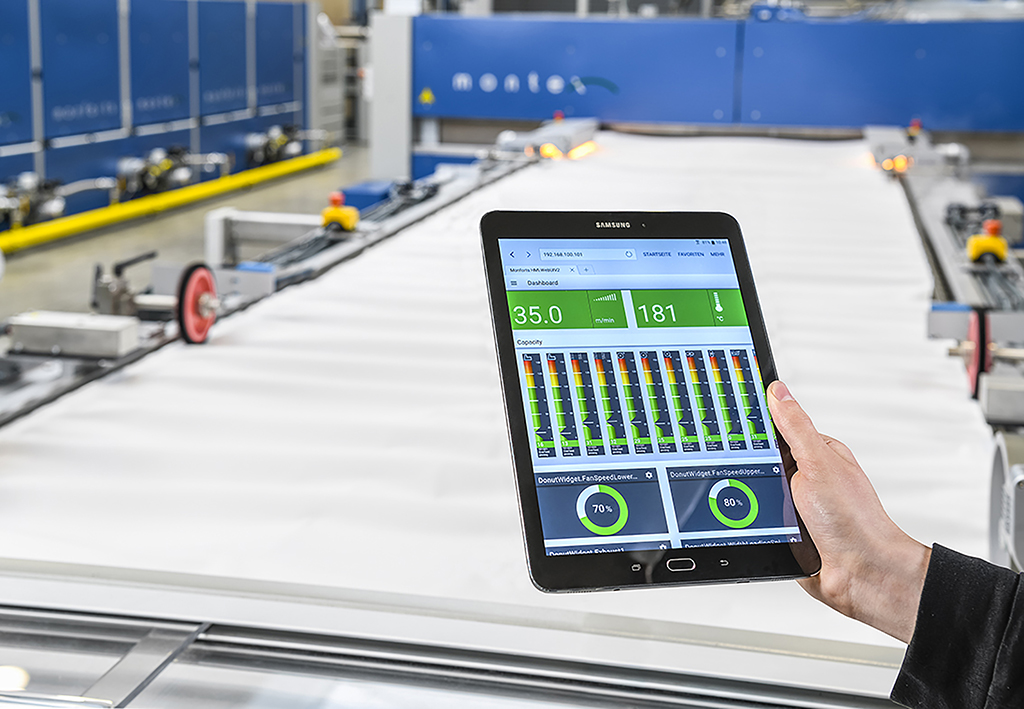
With the Monformatic™ control system, the exact maintenance of the dwell time in combined treatment processes i.e. drying and heat setting is monitored. When the heat setting point is reached the fan speed is automatically adjusted, keeping energy consumption fully under control. The Q-soft database is a central control system for production planning and documentation with a central interface. All process data can be stored in a standardised database where all set points and actual values are filed with read and write access for set points. Several machines can be connected simultaneously.
In combination with the Q-soft database, the customer can use additional systems including:
• Monforlogic® for the planning and management of batches and parameters or recipes with scheduling for up to nine machines.
• Operating cost overview for enhanced analysis of the machine processes by aggregating, analysing and displaying operational and process data, continuous monitoring and recording of meter data.
• Maintenance manager which generates machine alarms at regular intervals to remind the operator to carry out necessary working steps.
Monforts has traditionally been a leader in segments like denim and home textiles, to name a few. Are there any new product segments that the company is focussing on and developing solutions, as for example, technical textiles?
Monforts partners with technical textile manufacturers for the value-added finishing of many products using the latest Montex®Coat multi-head coating system. Coated technical textiles are extremely diverse in their end-use applications and products already manufactured by Monforts’ customers range from substrates for digitally printed soft signage to those for high-performance composites. Others include airbags, automotive interior components, flame-retardant barriers, filter media, geotextiles, heavy-duty membranes, mattresses, and even base liners for sensor-packed dye sensitive solar cells. All of these very different materials require expert coating and finishing for maximum efficiency using Monforts’ technologies which provide the ultimate in flexibility.
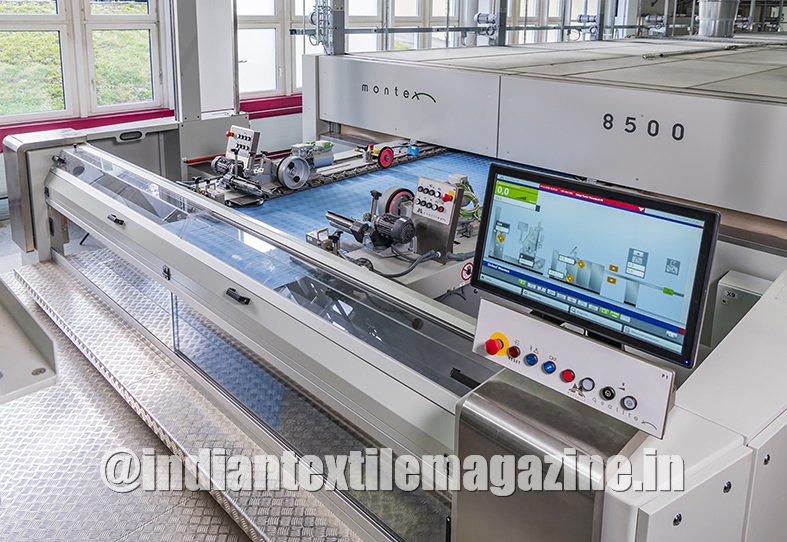
They also offer the ability to switch quickly from one fabric run to the next without compromising on the economical use of energy or raw materials. Ever since we acquired the technology that our coating units are based on in 2015, we have made a lot of refinements. All of these developments are reflected in higher coating accuracy and the resulting quality of the treated fabrics. At the same time, our latest multi-functional coating heads offer an unprecedented range of options with a wide range of modules available. Globally, technical textiles account for more than one-third of all textile consumption and currently India accounts for only a small proportion, but producers are investing in this sector and projections are that it will grow substantially in the coming years.
After-sales service and availability of spares is a very important aspect that determines the success or failure of a company in a given market. How does Monforts ensure efficient after-sales service and are you offering remote diagnostic or monitoring services and preventive maintenance services to ensure lesser downtime for your customers?
The Monforts’ commitment to customer service is based on four principles – helpful, accurate, fast and reliable. The company has established a reputation for quickly and efficiently dispatching spares and components, and online support is always available when needed. Monforts’ machines are known for their robustness and long service life, but major advances in digital technology mean that there are now significant gains to be made in the retrofitting of the latest automatic drives and control systems to machines, going far beyond the basic replacement of spare parts.