Ideal is a major player in the Gujarat market with its presence across the entire region. More than three million spindles have been added in Gujarat in the past few years.
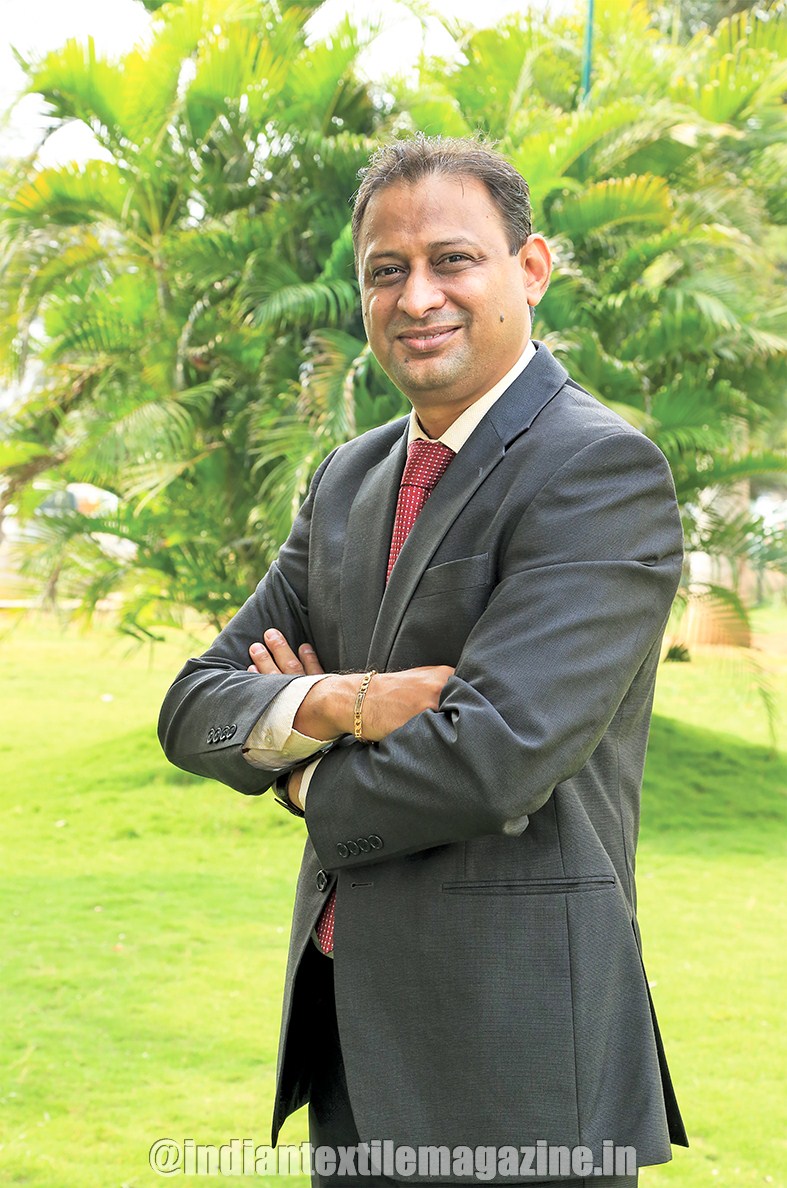
The company manufactures about 100,000 tubes per day and a huge quantity of simplex bobbins, dye cheese and cones. It has a wide range of yarn carriers for all brands (LMW, Rieter, Saurer, Electrojet, Marzoli and KTTM), which are manufactured from high grade engineering polymers.
Ideal is an innovation-driven company with a strong R&D team. Its “SureLock” tubes are ideal for centrifugal spindles. The new “HCC” tubes are developed to increase operational efficiency of ring spinning and winding machines.
The weight of HCC tubes is reduced by 35% and the wall thickness from 2.75mm to 1.8mm, without compromising on strength and durability. The cop content is increased by 10% to 15%, and there is power saving of about 3%, which has encouraged customers to replace their existing tubes with the new HCC tubes.
Ideal has also introduced special grade engineering polymer for steaming / dyeing at 135°C and have acquired prominent space in this segment too. The company is moving forward with the best-in-class innovation, quality and service. In its six decade journey, it has emerged a power to reckon with, catering to major textile mills across the globe.
Mr. Laxmikant Rathi, President – Sales & Marketing, said: “We provide quality products and customer-specific solutions through a detailed analysis which enables customers to achieve their specific requirements.”
Raja Industries
“Ideal has supported us to solve all our spinning-related problems” – Dilip Patel
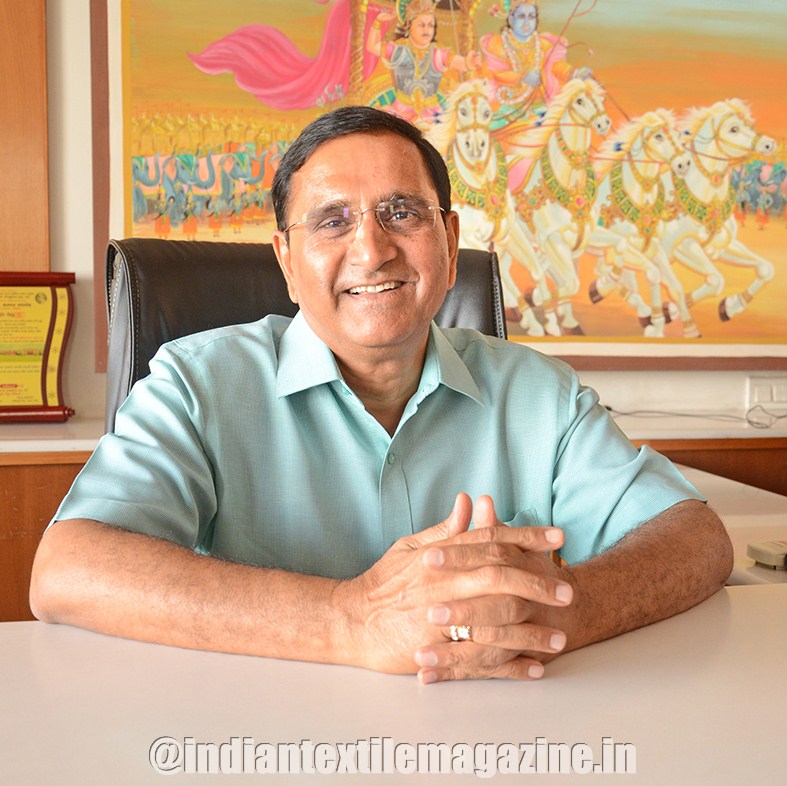
Raja Industries has proved a significant player in the ginning industry and ventured into spinning in 2010 with 13,000 spindles. The company currently has a huge annual production capacity of 5.5 lakh bales, with 97,000 spindles across its three mills.
The company has state-of-the-art LMW and Rieter ring frames equipped with auto doffer and link coner. Mr. Dilip Patel is a great visionary and has taken many critical decisions for its successful functioning. He started his ginning business with his elder brother. Using the best of raw materials and skills they slowly expanded the business. The company, with 1,800 employees, generated a turnover of approximately Rs. 900 crores in the last financial year.
D. Raja has been associated with Ideal since it ventured into the spinning industry. The common problem with regular bobbins is that the tubes have a loose grip that reduces the production efficiency. Ideal has solved this problem with its new technology. Mr. Dilip said: “Ideal has maintained good relations with us and has solved all our problems. They have supported us and their products have proved ideal for us.”
In the company’s phase 4, Ideal’s Surelock tubes are being used for better grip and performance on centrifugal spindles.
According to Mr. Dilip, the leaders at Raja Industries think big and seize all the new opportunities offered under the textile policy. The company is witnessing a steady growth in terms of production and has also plans to venture into garmenting as it is the future of the Indian industry. With Government support for garmenting, the Indian firms can very well compete in the world market with their skills and competence.
Samosaran Yarns
“Ideal’s customer-centric approach and timely deliveries are their biggest plus points” – Mahendra Jain
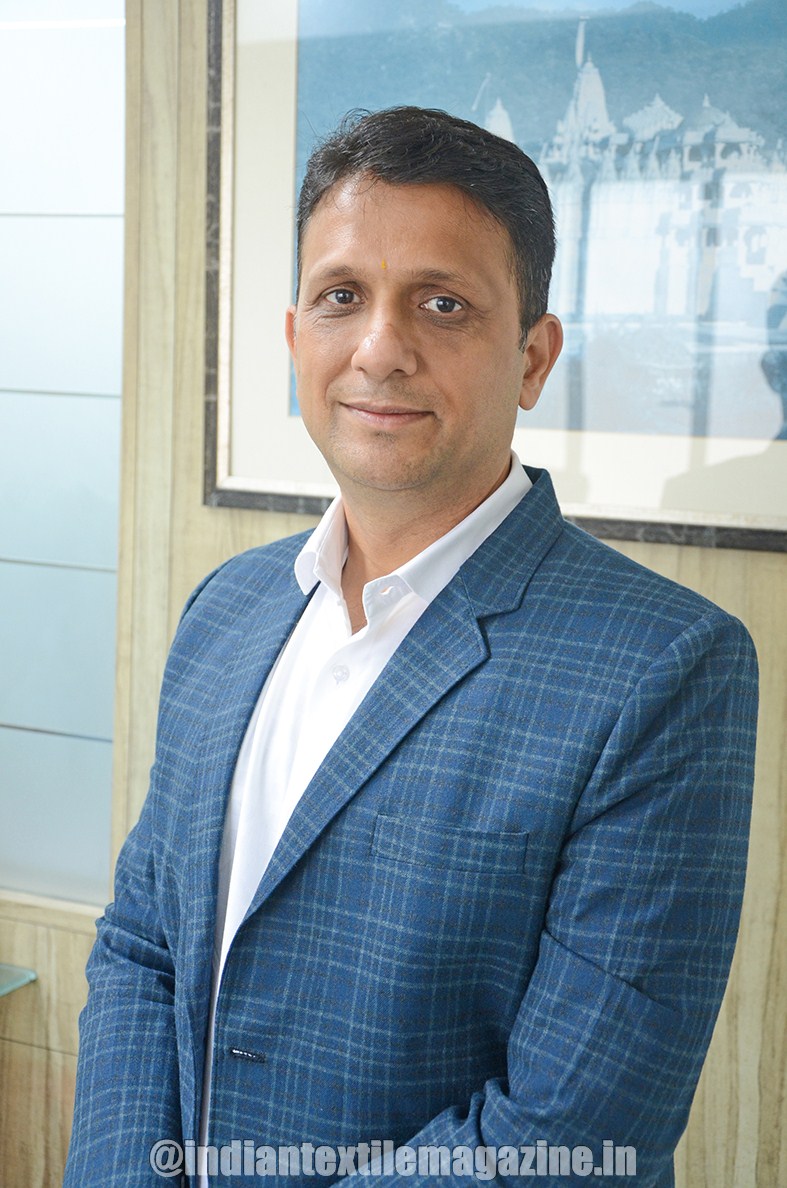
A subsidiary of the Pukhraj Group, Samosaran Yarns was established in 2007 as a manufacturing unit. It currently has 80,000 spindles and is located in Silvassa, Gujarat. The company also has a partnership unit at Pallipalayam with a capacity of 18,000 spindles. The company plans to expand the Gujarat unit capacity to 1 lakh spindles by March next.
Mr. Mahendra Jain was previously involved in the manufacturing of traditional yarns for which the Pukhraj Group was known. Looking at the market demand they decided to diversify into production of specialised yarns. The other yarn manufacturers were not trying any unique blends which Samosaran took as an opportunity and started focusing on producing of fancy yarns. They manufacture synthetic fibers ranging from 16 to 120 counts to cater to the domestic market. They are now witnessing a consistent growth of 20% per annum.
The company has facilities from blowroom to auto doffing. It has its weaving unit with a production capacity of 25 lakh meters per month. The company employs 1,500 people and is progressing at a commendable rate.
Samosaran has been associated with Ideal for 5 years and has been using its bobbins on the new ring frame spindles that run at a speed of 22,000 rpm. Mr. Jain said: “We have had no problems since our association with Ideal. We have Ideal’s SURELOCK tubes on our new machinery and they are running successfully.”
“Mr. Rathi has been an excellent technical advisor to Samosaran. He has also provided great assistance to the company to improve its overall efficiency. We are proud to be associated with Ideal,” added Mr. Jain.
His future vision for Samosaran is to maintain the current growth rate. He also aims to increase the unit’s production capacity to 10 lakh spindles in the 10 years.
JP Modatex
“Ideal HCC tubes have enhanced our operational efficiency and its plastic cones have added value to our products” – Jindas Jain
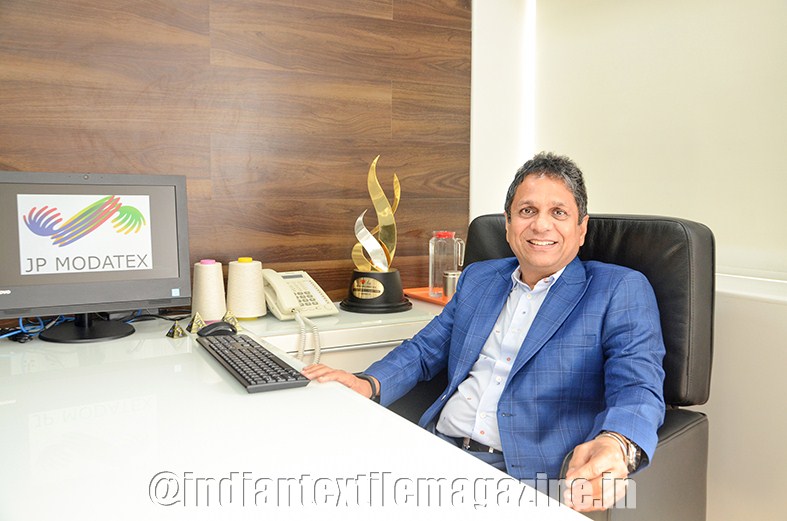
JP Modatex was set up by Mr. Jindas Jain for the ring spun yarns business in 2015. With a strong marketing strategy and Mr. Jain’s long experience in the industry, the company products are receiving positive customer response.
Mr. Jindas Jain has been a part of the textile industry since 1983. His experience has made him aware of what the customers require. The current market is witnessing peak demand for specialised and premium yarns from JP.
The company focuses on production of linen blends with cotton, viscose, bamboo, etc., and faces no competition in this field, thanks to its expertise in manufacturing quality yarn. Mr. Jain said, “100% linen is the best fabric on earth. It is skin-friendly, durable and fashionable when blended with other fibres. We bring to the market a quality standard that was lacking in this domain”.
The company mainly focuses on cellulosic and synthetic cellulosic fibres. To maintain a certain quality, the raw materials are selectively chosen from various locations. The linen is imported from Europe, Tencel from Austria and bamboo from China and cotton is locally acquired. The production unit is equipped with its latest LMW machines. It started with 18,000 spindles, and the plan is to take this capacity to 45,000 spindles. An experts team works on the development of special fibres.
Mr. Jain stated: “The HCC tubes are of lightweight and have a very unique design, hence are able to carry more yarn. Also, as the ring frames are linked with auto motors, there has been 15% increase in efficiency”.
JP also uses Ideal plastic cones which have helped the company weavers to reduce the damage cost during transportation. Ideal has been a trusted partner of JP Modatex since its inception and Ideal’s innovation-driven technology has helped it to reduce production cost.
Mr. Jain’s vision is to keep increasing the market share by providing customers with quality yarn at most competitive rates.
Pashupati Cotspin
“Ideal is a better choice when it comes to reliability” – Saurin Parikh
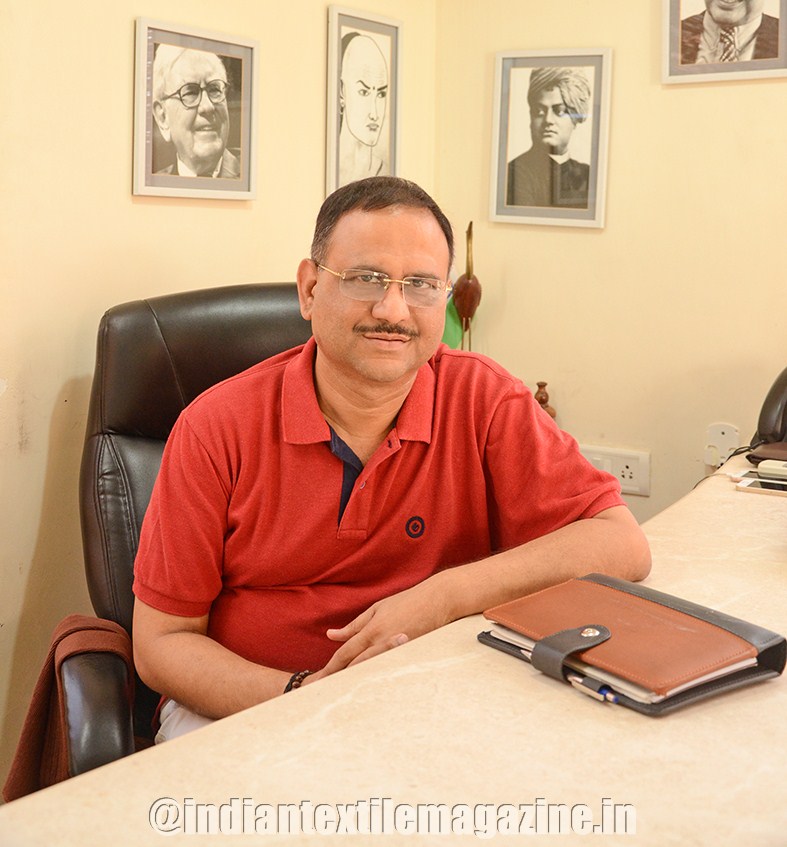
Pashupati Cotspin gradually developed as a ginning unit since 1997 and ventured into spinning in 2012. Today the company owns 112 double roller Bajaj gins. Having produced 1.5 lakh bales last year, it stands amongst the top five in Gujarat.
Mr. Saurin Parikh, a first generation entrepreneur, had a vision to start forward integration after the success of the ginning unit. He set up a spinning unit with 25,000 spindles to which 12,000 spindles were added in 2015, along with sizing warping and weaving unit with 48 Toyota looms and 18 machines of TFO.
The company is the first to provide the customers with a “yarn beam”, meaning a consistent quality of yarn produced and finished in the same unit. This would provide consistency and supreme quality to the weavers, and the company would earn a fortune on the transportation and packaging cost.
The company is focused on manufacturing of grey fabrics. It has introduced the ‘SOOVESH’ brand for retail fabric. The idea behind SOOVESH is of having an in-house brand that can generate good profit margins for the company and can present its ideology in the market. The company has a production facility spread over in 40 acres, including an oil mill and a cotton delinting (seed cleaning) unit.
Ideal has been a great partner to Pashupati. In Mr. Parikh’s words, “Ideal has provided us with the right quality, they have a remarkable work culture and a very customer-friendly approach, and we plan to be associated with them in all our future ventures as well”.
Mr. Tushar, who heads the company’s spinning vertical, said that the new plant uses Ideal’s latest HCC tubes which are lighter in weight and help to reduce power consumption. The tubes have perfect locking on centrifugal spindles, thus tube lifting is prevented.
The vision of the Pashupati team is to develop SOOVESH as a brand and work on online retail facilities. Mr. Parikh said: “Sky is the limit for our development, and branding is the best way to reach that stage. The company is also involved in warehousing and has a role in renewable energy with its rooftop solar energy plant of 2.5 mw. Future aim is to establish a wind energy plant that could generate 2.6 mw energy.”