Hyosung TNC announced that it had recently completed the installation of the smart factory system at its Spandex factories in Quzhou City, Jiaxing City, Guangdong Province and Zhuhai City in China and in Dong Nai in Vietnam.
The new system is composed of a process monitoring system, a quality control system, and smart IoT (Internet of Things) among other elements.
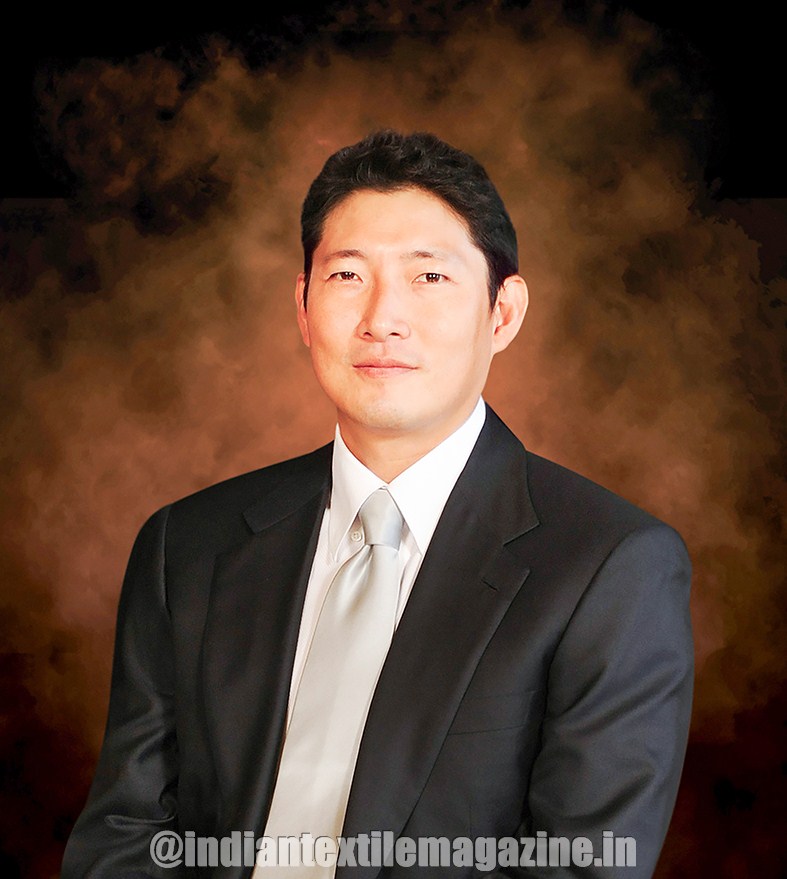
With the establishment of the next-generation production environment, Hyosung TNC is now able to manufacture products of identical quality at each of its global factories by monitoring their status in real time for enhanced quality control. In addition, the company’s manufacturing competitiveness can be further improved through the collection and analysis of data and control management in every area of the manufacturing process from the import of materials to actual production and shipping.
The establishment of the smart factory system was driven forward at the insistence of Hyosung Chairman Hyun-Joon Cho, who has repeatedly called for innovation in the area of production and management since he took office last year. Chairman Cho has also emphasized that it will be necessary for Hyosung TNC to respond proactively to the changing industrial trend in the upcoming era of The Fourth Industrial Revolution by establishing a flexible and optimal production environment based on a combination of ICT and the company’s own proprietary technologies if it is to maintain its global No. 1 status.
Realizing optimum production processes and solutions based on big data
Hyosung TNC accelerated the establishment of the smart factory system in the latter half of last year using the know-how of Hyosung ITX, a professional IT company. After conducting the actual inspection of each factory, Hyosung ITX carried out the project by establishing a standard data collection and data management system, followed by a data analysis and monitoring system, and then an automatic production process control system.
Hyosung ITX developed the optimized BOT+ solution for Hyosung TNC’s Spandex factories and completed its delivery in August. The BOT+ system makes it possible to promptly detect and deal with quality problems in the production process via the application of various ICT technologies including the analysis of big data with machine vision, IoT, and smart sensors.
Machine vision can identify defective products or problems in the production process by analyzing data obtained from a super-high- speed camera using AI. What used to be monitored by the naked eye is now treated by AI, thereby improving accuracy to a remarkable degree.
Chairman Hyun-Joon Cho is committed to “strengthening global No. 1 status by further improving quality and boosting capacity with the smart factory system”
Hyosung ITX developed the inspection equipment using “machine vision” technology to diagnose the production process at each stage. Hyosung TNC plans to raise its production efficiency by improving the production process with an optimal quality algorithm, which will be prepared by analyzing the data of each machine vision.
Hyosung Chairman Hyun-Joon Cho said, “It is essential for manufacturers to install smart factory systems in the face of the powerful, irreversible trend of the Fourth Industrial Revolution. Hyosung will solidify its status as the world’s No. 1 Spandex manufacturer by improving its world-class quality and developing new technologies based on the smart factory system.”
Hyosung ITX launches ?XTRM FACTORY?, a smart factory solution brand.
Meanwhile, Hyosung ITX plans to enter the smart factory system markets in Korea and overseas by using its experience of establishing smart factories for Hyosung TNC. To that end, the company recently launched ?XTRM FACTORY?, a solutions brand optimized for smart factory systems. Hyosung ITX has implemented a strategy aimed at positioning itself as a provider of one-stop total solutions, offering a road map for the step-by-step establishment of systems optimized for customers on the basis of production process and data analysis and organic cooperation among experts in the establishment of IT systems.