By Arvind Maurya, Business Head and Chief Executive – Knits Fabric Business, RSWM Ltd
The Knitting Industry: Driving Growth
The knitting sector, an essential pillar of textile and garment manufacturing, has undergone significant transformation in recent years. With the growing demand for knitted fabrics in sectors like fashion, sportswear, athleisure, and technical textiles, the industry is enhancing its technological capabilities while addressing key sustainability challenges. Set for robust growth, the sector is driven by innovations and shifting consumer preferences. As one of the largest cotton producers globally, India enjoys the advantages of its rich textile heritage, skilled workforce, and large-scale production capacities, making it a prominent player in the international market. However, the shift toward sustainable and efficient production techniques has become indispensable for ensuring long-term viability and success in the sector.
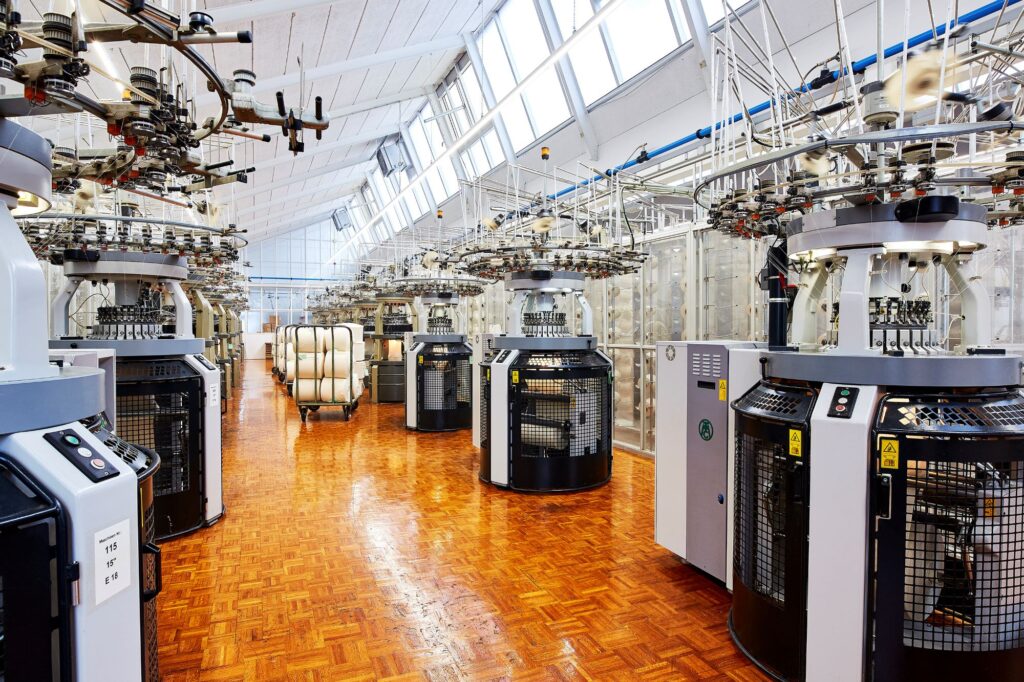
Be it circular knitting, flat knitting, warp knitting, or Jacquard knitting, each segment is experiencing increased global demand, with machines designed for specific applications. Circular knitting machines, for example, are ideal for manufacturing garments in fashion, sportswear, and smooth socks, while flat knitting machines produce flat fabric panels perfect for items like scarves, sweaters, and collars. Warp knitting machines excel in creating tricots and lace fabrics, commonly used in lingerie, automotive, and other technical textiles. Jacquard machines enable the production of intricate designs and patterns, including motifs, logos, and textures.
As the knitting industry continues to evolve with these innovations and sustainable practices, it is poised to redefine the future of textiles and garment manufacturing across the globe.
Knitting Market Overview
As per estimates, India’s knitwear market is pegged at around $9.1 billion. This is slated to reach about $21.5 billion by 2027, recording 9% growth. Renowned for their quality and delicate techniques, knitting mills – especially in places such as Tirupur, Ludhiana, Bengaluru, Mumbai and Delhi – have made India one of the world’s largest textile-exporting nations. Tirupur accounts for a major chunk of the country’s overall knitwear exports. Primary knitwear exports comprise ladies’ tops, men’s t-shirts, sportswear, boxer sets, jogging suits, etc.
Large circular knitting machines are gaining growing popularity in producing knitted fabrics on a mass scale. The Circular Knitting Machine market is poised for significant growth, projected to achieve a CAGR of 11.4% from 2024 to 2031. Appropriate for high-speed manufacturing, these machines are used to produce numerous knitted items such as clothing, home textiles, and accessories.
Designers now create elaborate patterns seamlessly through advanced software in computerised machines. Simultaneously, waste is reduced with automated production processes.
Knitted fabrics are more popular in India since they permit better breathability and have a soft texture, which is suitable in hot and humid conditions. High waterproofing characteristics also allow air and moisture to pass through its breathable fabric. The comfort, flexibility and stretchability of knitted fabrics also add to their allure.
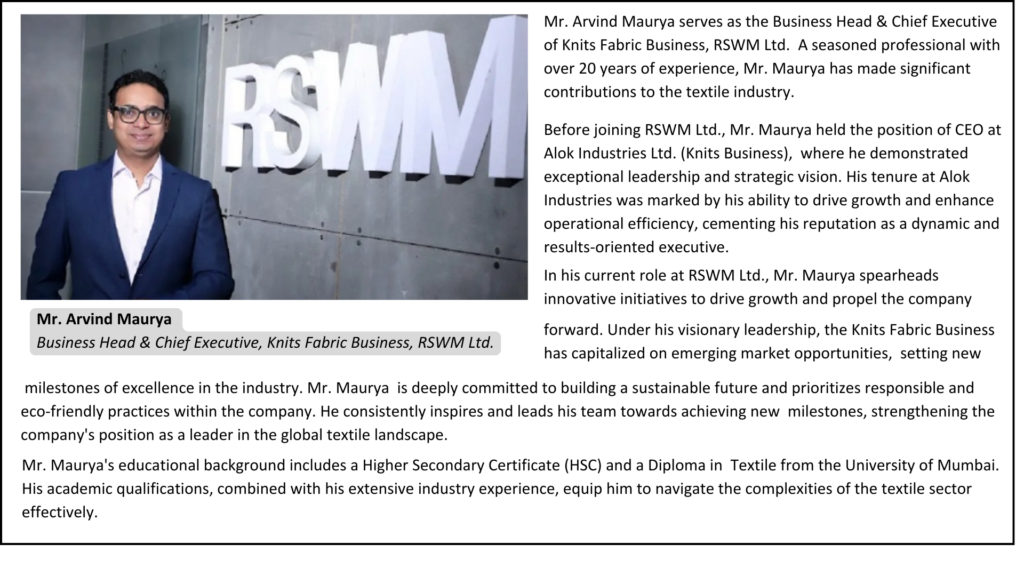
In recent years, both the circular and flat knitting markets have seen significant growth due to evolving consumer preferences and global socio-economic drivers. Economic issues in conventional textile hubs such as Bangladesh and Sri Lanka have nudged many global customers to expand sourcing to regions like India, Turkey, Uzbekistan and Vietnam. Among these, India has become the preferred destination because of its stable political and economic environment.
Ongoing Tech Trends and Innovations
Meanwhile, technological innovations are reshaping the future of the domestic knitwear industry. While circular knitting machines revolutionised the production of seamless garments, saving time and limiting fabric waste, the use of 3D knitting machines is leading to the creation of complex, customised designs without any need for cutting and sewing. Automated machines and 3D knitting are also facilitating faster, more precise production while creating complex designs with low waste.

Similarly, smart knitting with the integration of IoT (Internet of Things) and AI-driven technologies for automated quality checks, optimised production workflows and predictive maintenance is enhancing overall efficiency and productivity. Advanced knitting technologies are also augmenting India’s capabilities in competing with Asian manufacturing hubs such as China, Vietnam and Bangladesh.
Therefore, it has boosted the quality of domestic craftsmanship and garments, increasing its demand in international markets and making the country a first-choice destination for exports of value-added items. These factors have enhanced India’s competitive edge in the world knitwear market, thereby positioning it as a leading knitwear exporter, particularly in the US, Europe and the Middle East.
Sustainable innovations are also being driven by the introduction of eco-friendly machines designed to curb energy consumption, water usage and waste in the knitting process. Additionally, the use of recyclable materials and sustainable yarns produced with advanced machines is reducing the sector’s carbon footprint. Furthermore, manufacturers are embracing eco-friendly practices by using organic fibres and recycled fabrics in catering to customer demand for green products.
Primary Challenges in the Domestic Market
However, the knitwear industry is facing some challenges like unpredictable market conditions and demand fluctuations. Although demand soared in the post-pandemic period, geopolitical flashpoints such as the Russia-Ukraine and Israel-Hamas wars have affected demand in the knitting industry as it is an export-oriented sector.
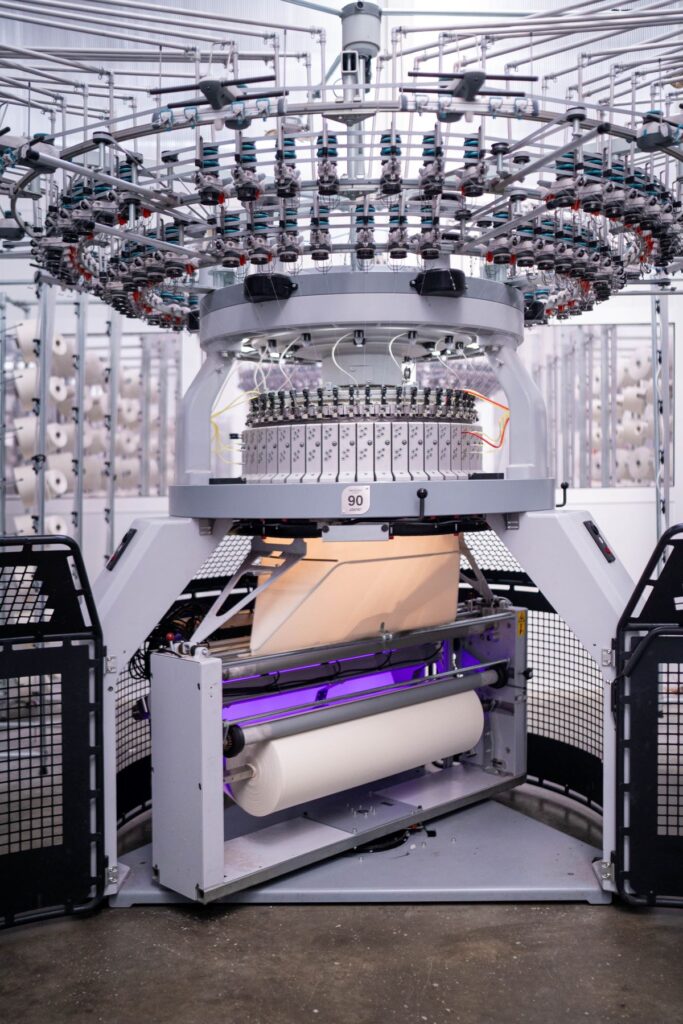
An unorganised and decentralised industry alongside the multiplicity of regulations in diverse regions across India only exacerbates the problems. To elaborate, while a zero-discharge mandate prevails in some part of India, only primary treatment is required in other regions. Dissimilar regulations then lead to varying costs of production throughout India.
The skills gap represents another major issue. Almost all companies struggle to hire skilled workers who are competent enough to operate and maintain their advanced knitting machinery. For small-scale units, upgrading traditional machines to state-of-the-art machinery is a big barrier because of the high capital investments involved.
Some Select Opportunities
Nonetheless, several opportunities exist that Indian manufacturers could tap into. Organised players with modern machinery can leverage the increasing consumer preference for wearable technology and smart fabrics in the knitwear segment that is aligned with universal trends in athleisure wear and performance. Moreover, eligible units could opt for relevant government programmes – such as the Production-Linked Incentive scheme – encouraging technological upgrades in the textile segment.
Along with other conducive policies, the possibility of FTAs (Free Trade Agreements) being signed in the coming months could help foster an enabling environment for the knitting industry. As a result, the overall outlook for the industry augurs well. Together with institutional support, all the above opportunities can help India emerge as the knitwear capital of the world, sooner rather than later.
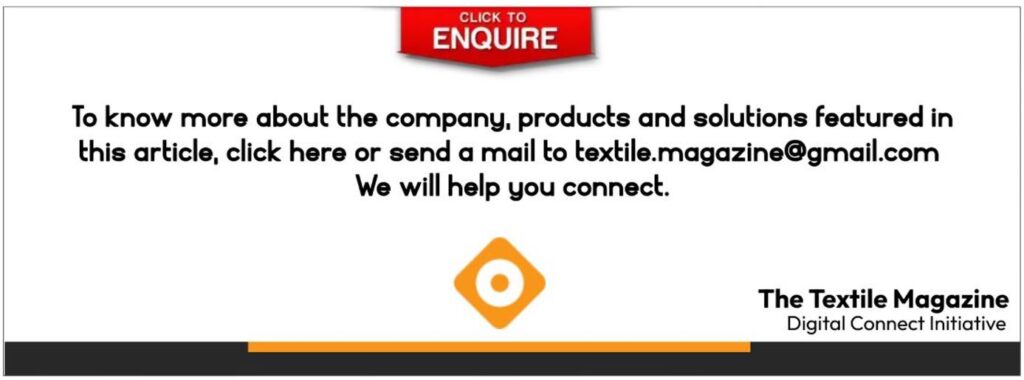