In view of India’s deteriorating water crisis, there is an urgent need to explore alternative means of water management. Industrial water treatment can help us to tide over this situation by retrieving the processed water and making it usable for other purposes.
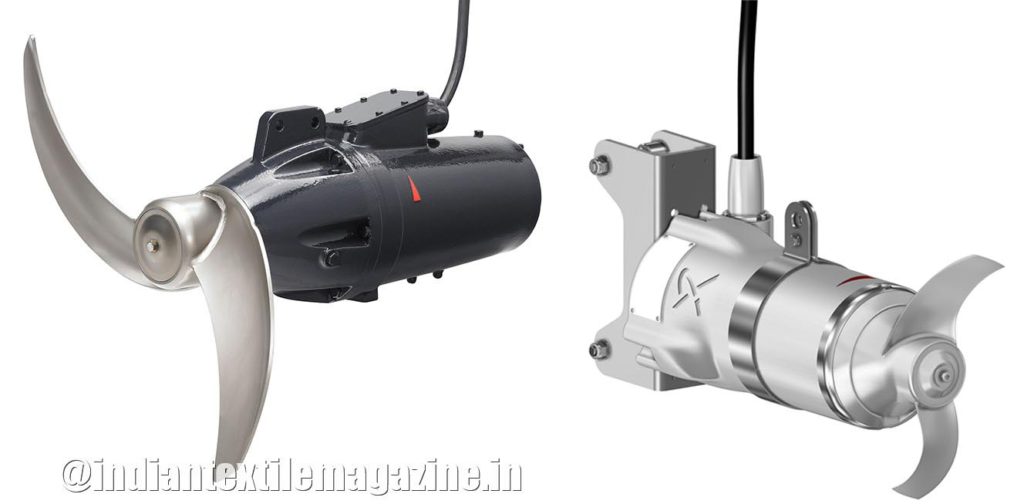
Textile effluents are one among the complex wastewater which undergoes intense treatment through various processes like chemical, biological & membrane separation. Because of the complexity & the characteristics of the effluent, the treatment scheme is envisaged with anoxic zones, anaerobic zones, oxidation ditch & sludge holding tanks, which requires submersible mixers & flow makers for homogenization.
What is homogenization?
Suspended solids, biomass & sludge in the effluent must be kept in suspension and if the masses settle, the operation of the equipment & the process will be hindered. Therefore, various stages of wastewater treatment use submersible mixers & flow makers as a preferred equipment to retain the solids in suspension, which is otherwise called as homogenization. This is made possible with the help of the thrust exerted by these equipments in to the liquid medium.
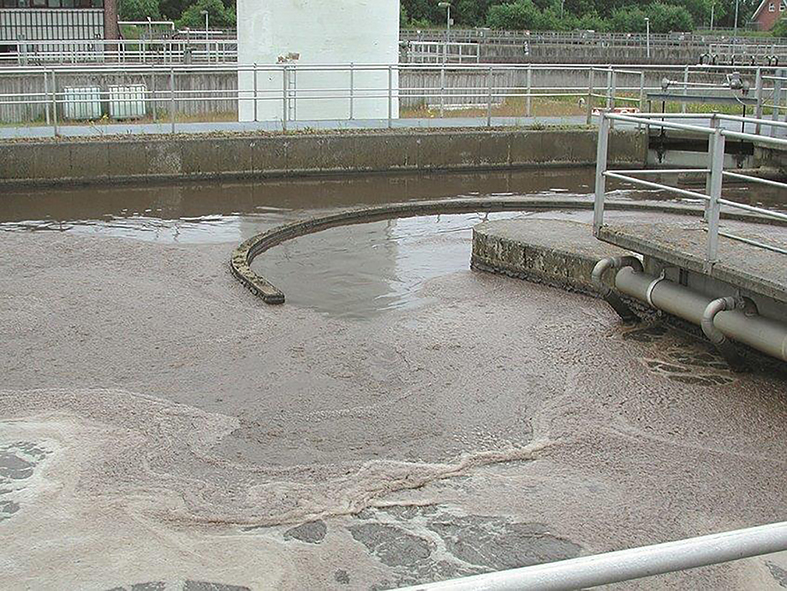
This process of homogenization is particularly useful in all treatment plants that undergo major variations in maximum and minimum flow rates. Homogenization of liquids in large volumes is usually a voluminous task and requires large amounts of energy consumption to get the final treated effluent.
Out of all the other methods of homogenization, hydraulic is the most cost effective and energy efficient method, used widely in wastewater treatment.
Mixers and flow makers are used to homogenize suspended solids in both CETP and ETP, explicitly in pumping stations, treatment plants, sludge processing systems, and biogas generation. The efficiency of hydraulic homogenization is decided by “Thrust to power ratio (T/P)”, based on which the submersible mixers are designed.
These mixers can be either direct driven or gear driven. The gear driven mixers provide more thrust when compared to direct driven mixers, and that is the reason gear driven mixers are used in huge / lengthy tanks
The mixing velocity in the tank is governed by influence zones / velocity profiles provided by the manufacturers.
What is the role of submersible mixers and flow makers in the treatment process ?
Mixers:
Once the initial screening and processing of the textile effluent is completed at the inlet of CETP’s, the liquid is homogenized in effluent collection/ Equalization & neutralization tanks to ensure that incoming pollutants are evenly distributed, so that it simplifies the next process.
Grundfos Submersible mixers “SMG” shall be put in to operation, these mixers are gear driven & range between 0.9 kW to 18 kW.
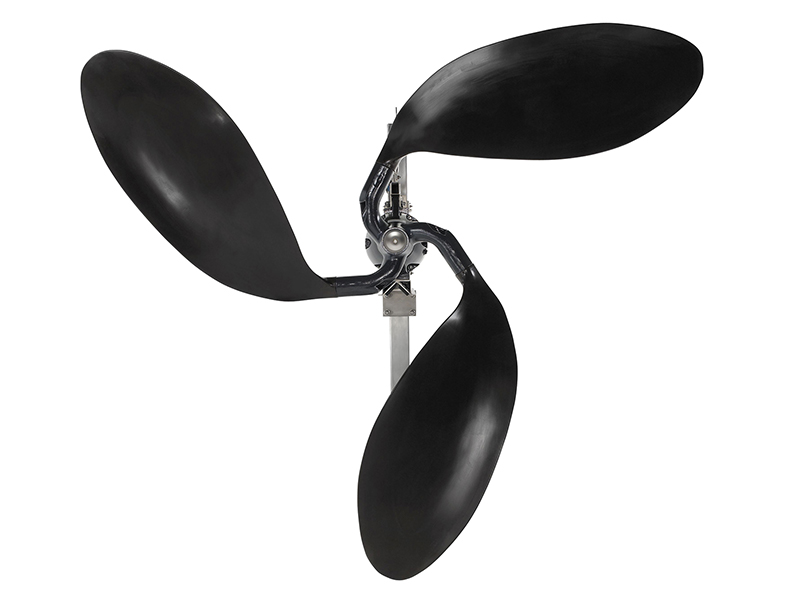
Flow makers:
Oxidation ditch is a kind of biological treatment which is classified as an activated sludge process & it’s a type of extended aeration. These are lengthy tanks in the treatment plant one can come across in textile CETP’s. The Oxidation ditch is a closed loop system, which increases the retention time of effluent with subsequent aeration & anoxic zones, in other words nitrification & de-nitrification.
There are certain challenges in the process like:
• Floating sludge
• Sludge bulking
• Settling
• Improper mixing
Installation of “Flow Makers” would largely facilitate the process by limiting these challenges.
These Flow makers convert the power into thrust, which keeps the bio-mass in suspension & makes the bulk move in the oxidation ditch.
The number of flow makers, its positioning are critical to avoid dead zones in the tanks and to prevent sludge settling
Grundfos supplies flow makers, which are gear driven, the model is referred to as SFG (Submersible flow makers, gear driven). SFG flow makers range between 0.7 kW to 8.0 kW, the thrust generated range from 665 N to 6570 N.