RMP Bearings Co. at Ranpur in Gujarat was started by CM Makwana. Initially RMP started off by producing thrust bearings for the automotive industry in 1978. In 1983, it began by producing bearings for the textile sector, and within the first year notched up Lakshmi Machine Works Ltd. (LMW), Coimbatore, as its first OEM customer.
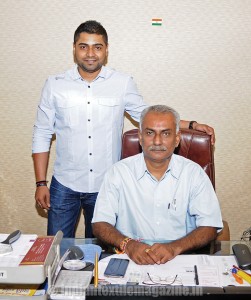
With passage of time, RMP, which is an ISO:TS:16949 certified company, increased its capacity and is an OEM to other renowned Indian and global textile machinery companies like Trutzschler, Kirloskar Toyoda Textile Machinery (KTTM), Zinser Textile Systems Ltd., Marzolli, etc., while LMW still remains the biggest buyer of its bearings. RMP has recently also concluded talks with Rieter to provide bearings for its spinning machinery range.
Bearings produced by RMP are equally distributed between the automobile and textile sectors and its SR-60 make of bearings are extensively used by LMW and KTTM in their spinning technologies.
One particular bearing, the 45-NPPB, which in its earlier model had a lifespan of seven years, is now guaranteed a lifespan of 17 years by RMP after extensive research and development. The original bearing which was not supposed to be lubricated in its earlier model was provided a hole to lubricate it. It also changed the size of the ball and also changed the RAV value of the bearing from 0.08 to 0.02, which reduced the friction between the ball and the track and extended the lifespan.
Miten Makwana, Operations Director at RMP Bearings and the third generation of the Makwana family, proudly shares with The Textile Magazine that the company is also supplying bearings to the textile machinery industry in China, which itself has a huge number of bearings producers, and is of the view that RMP is probably the only Indian bearings producer to export to China.
The main products turned out by the textile industry include GE, GRAE, RAE, RALE and BT Series, line shaft bearings, pillow block bearings, pulley spindle tape tensioner, SRO Series, tensioner pulleys and thrust bearings.
The RMP Bearings plant, spread over 27 acres, has a built-up area of around 18 acres and employs around 800 people. It uses the highly-automated German technology to produce bearings of the highest quality and efficiency.
RMP Bearings’ current daily production is 53,000 pieces, and according to Miten, 30 per cent of its products are import substitutive. It also exports its products to the US, the UK, France, Brazil, Italy, China, Turkey, Sri Lanka, Nepal, Bangladesh, Vietnam and Indonesia.
RMP has its own R&D department and a tool room to develop new versions of bearings, which includes a material lab testing facility. Each and every raw material which goes in to production is first tested on various parameters before it goes on the production line and goes through seven stages of production and has recently placed an order for the latest Taiwanese technology, which will give productivity of 1,000 pieces per hour.
Miten who joined RMP Bearings two years ago began by developing the replacement market serving the automobile sector and is now busy developing the same for the textile industry. Nearly half of its business comes from the textile industry. Hence the sector is very important for the company.
Currently RMP is serving the aftersales market for the textile industry, by directly supplying its bearings to textile mills which directly approach them. As part of creating a replacement market business for the textile sector, RMP will be appointing distributors across India. Miten feels that although the after sales market may not be as big as direct sales to machinery manufacturers; it however is important.
On why a textile machinery manufacturer should buy RMP Bearings, Miten says: “There are very few Indian bearing producers who have R&D and testing facilities in-house, which gives the textile machine manufacturer the confidence that RMP Bearings would be able to develop a bearing as per their requirement. Secondly, our bearings have a longer lifespan, and the biggest factor is our business ethics, which we will never compromise for the sake of bagging an order.”
RMP is focused on incessantly advancing energy – efficient, resilient performance in practically every type of machinery. It develops pioneering solutions with customers to help their applications function safely, efficiently and smoothly. While the notion of “innovation” may have numerous dissimilar descriptions, at RMP it could be very simply described as using ingenuity to add value in the whole lot of things it does.
This idea of added value through innovation is verified in every facet of its business from progressions geared to generate better products and solutions, to providing its customers with outstanding services worldwide. RMP’s passion for innovation is replicated on three pillars, ‘People, Technologies and Processes’.
Quality, according to Miten, is in the DNA of RMP Bearings and a basic prerequisite to attain global competitiveness. “Our quality processes are deeply entrenched to make certain that customers receive reliable and brilliant quality in all RMP products and services across the world,” he observes.
Following the economic crisis of 2008-09, which saw sales of new textile machines tumble, sales of RMP Bearings too took a hit in the period. However, in the last few years, following favourable policies including subsidies, textile machine manufacturers have been able to sell more machines, which in turn has also helped RMP garner better business.
Miten sees a bright future for the Indian textile industry following the announcement of the Make-in-India program of the Government. He expects that investments will go up in the next 2-3 years, which will also help perk up RMP Bearings’ sales.