Yarn production has been highly automated for decades, yet a look at the overall spinning process reveals untapped potential. Rieter has vowed to lift spinning mill automation to a new level, but this goal can only be achieved in combination with digital solutions. Processing recycled fibers also plays an increasingly important role for Rieter. In the dynamic Indian textile market in particular, Rieter technology offers customers the opportunity to strengthen their competitive ability and expand their market position.
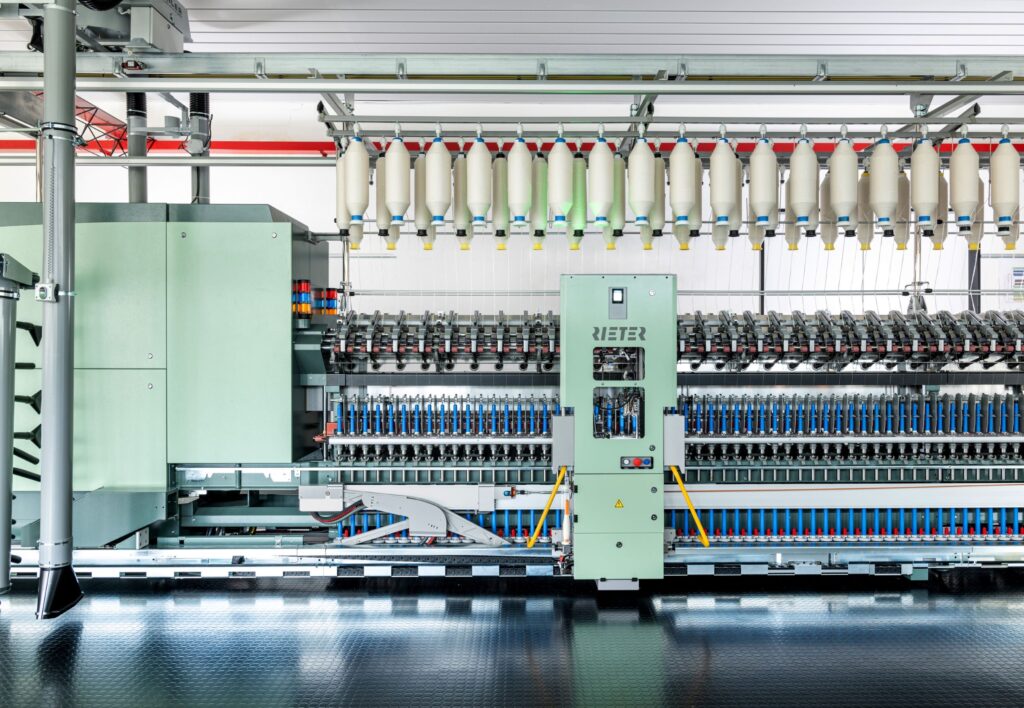
Automation and digitization open up new opportunities to optimize the spinning mill as an overall system and close automation gaps. They enable resources to be used more efficiently and at the same time, improve job quality in spinning mills. In factories around the globe, for example, the fully automated piecing robot ROBOspin repairs over 1 000 000 yarn breaks every week, receiving information about the breaks from an individual spindle monitoring system. Each spinning position is monitored by a sensor that detects whether or not the spinning position is producing yarn. If yarn production is interrupted, the sensor transmits a signal to ROBOspin, which automatically travels to the spinning position and repairs the yarn break. The repetitive work of piecing is left to machines, allowing employees to concentrate on activities that enrich their work and create added value for the company. This aspect is relevant for both large and small spinning mills and impacts markets worldwide, including India.
Increase profitability with ROBOspin
ROBOspin is revolutionizing the operations of more and more Rieter customers. By installing ROBOspin, spinning mills around the world are reducing their workforce requirements by up to 50%, as the robot reliably achieves up to 95% piecing efficiency.
The minimal contact between the robot and the yarn not only preserves yarn quality but also ensures a steady output of high-quality yarn.
“ROBOspin is the perfect automation solution to efficient workforce scheduling,” said Durai Arun, Managing Director of Poomex Clothing Company in Tirupur, India. The vertically integrated company is a manufacturer of various types of knitted garments, including underwear, for all age groups. It uses state-of-the-art spinning processes and the latest technology to produce yarn and garments. ROBOspin was installed on an existing ring spinning machine G 32 in 2020. “Compact design and consistent piecing quality are the standout features of this robot,” added Durai Arun. Since then, Poomex Clothing Company has invested in a ROBOspin for their compact-spinning machine K 42.
ESSENTIAL – New territory with digitization
Alongside automation solutions, Rieter has consistently expanded its digital portfolio over the years and launched it under the name ESSENTIAL – Rieter Digital Spinning Suite.
Rieter’s vision is the fully digitized spinning mill. ESSENTIAL is an important step in this direction. This system analyzes the data of the entire spinning mill in real-time and provides meaningful key performance indicators. ESSENTIALoptimize, one of the system’s modules, brings digital textile technology into the spinning mills, providing the data generated in the spinning and winding processes in order to optimize the entire spinning process. Sliver thick place monitoring is one example of what the module can do. The Rieter Quality Monitor system for quality monitoring simultaneously supplies data related to thick places from the card, the comber, and the regulated draw frame. ESSENTIALoptimize compares the data on a quality dashboard. The system detects deviations and generates an error message based on rules, threshold values, and evaluation of machine events along the process. This way, faults can be detected in the early stages of the spinning process and rectified by personnel before they lead to quality problems in the next process. This increases efficiency throughout the system and supports the spinning mill in producing yarn economically. With the help of artificial intelligence and data analysis, Rieter continues to expand ESSENTIAL to create a smart system that will further optimize mill efficiency.
Mastering the major challenges of recycling
Recycling poses a major challenge to the textile industry. Today, most fiber blends from recycled and raw cotton are still processed on rotor spinning machines. However, the yarns are not suitable for all the textile applications envisioned by textile producers. The EU Vision for Textiles 2030 which aims to create a more sustainable, circular, and eco-friendly textile industry by 2030, will require more and more fashion labels to make a proportion of their garments from recycled yarn.
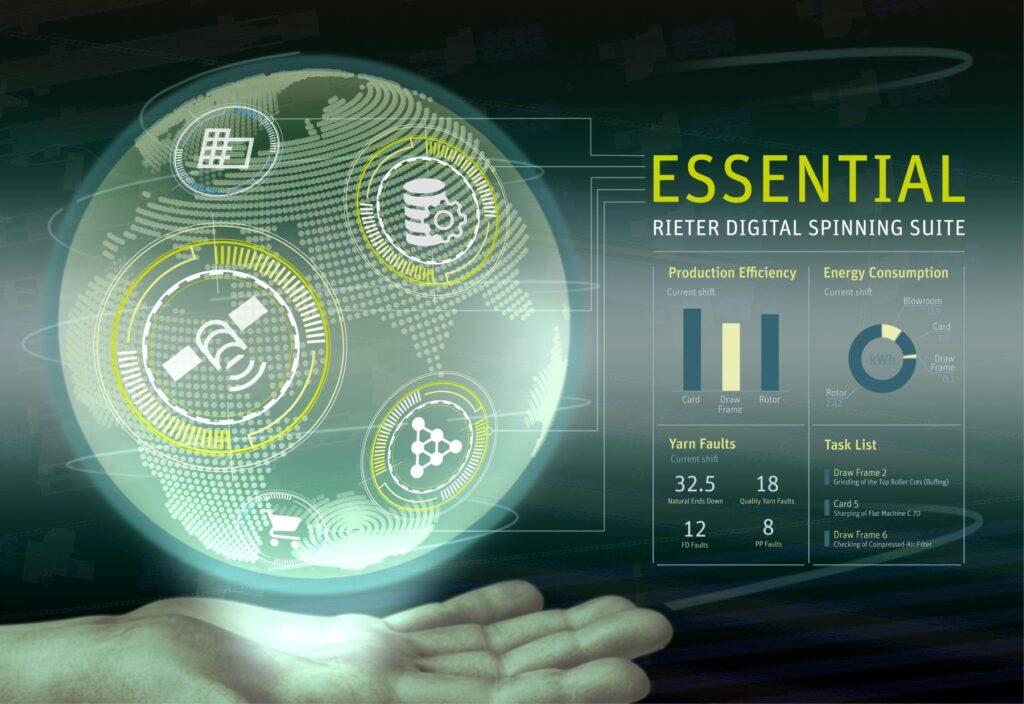
In addition to recycled rotor yarns, recycled ring yarns have so far only been available in very limited quantities and often only in coarse counts and with a maximum recycled cotton content of 20%. The reason is that producing ring and compact yarns from blends of recycled and raw cotton places the highest demands on the spinning process. For these requirements, Rieter developed Com4recycling, the Rieter recycling system. It enables customers to produce fine ring and compact yarns from the challenging raw material with just under 40% recycled fibers and high yarn quality. Rieter develops and continuously tests new technology components, processes and configurations in order to advance the spinning of recycled yarn. In India, in particular, many spinning mills rely on Rieter recycling technology to respond to the growing demand for recycled textiles.
In this context, Rieter collaborates closely with customers and fashion labels and cooperates with renowned Indian universities, external research institutes, and specialists from the textile industry. With Rieter’s technology and know-how, Indian spinning mills can increase their competitiveness and expand their market lead.
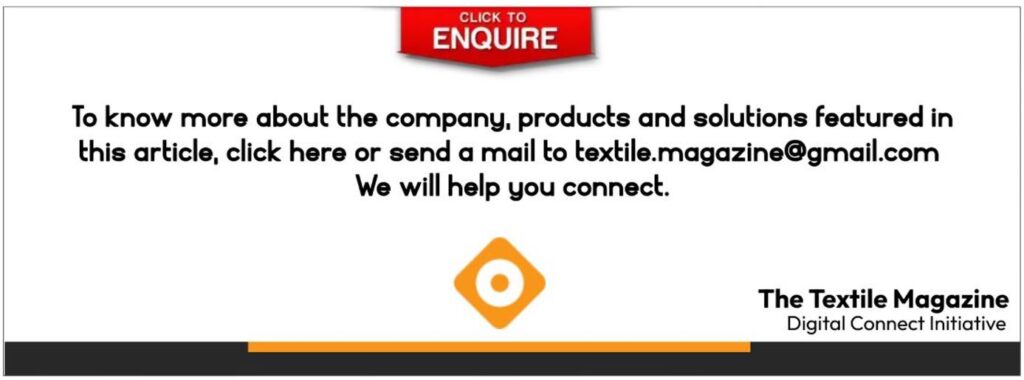