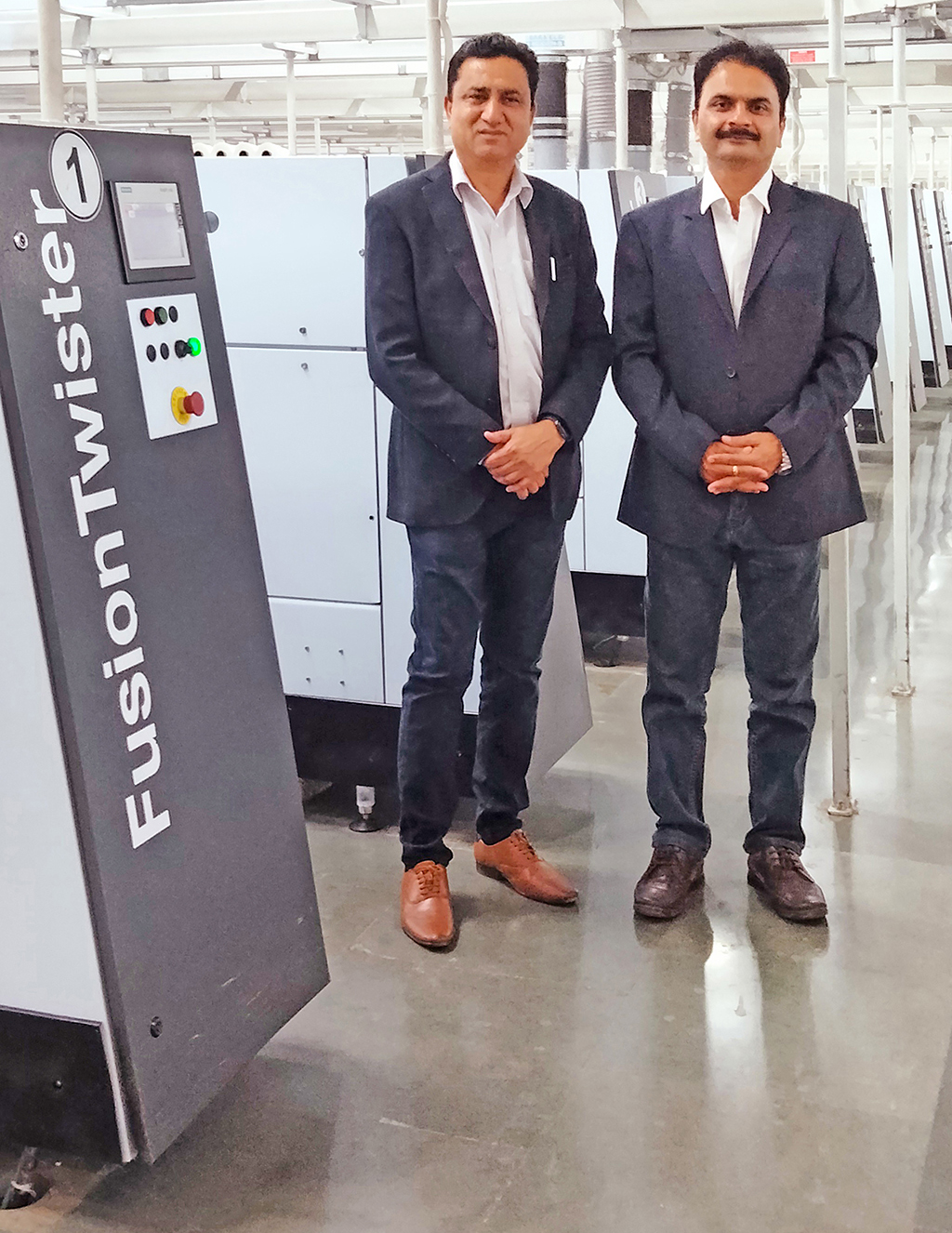
GRG Cotspin Ltd of the Anjar-based GRG Group in western India was established in 2013 and is one of the fastest-growing textile companies in the country. The state-of-the-art spinning mill produces 85 tonnes of carded and combed yarns daily on 24 ring spinning machines with nearly 35,000 spindles. A large proportion of the yarns is processed in the twisting mill into twisted yarns with very low twist as well as so-called zero twist yarns for high-quality terry fabrics.
Energy is the biggest cost factor in the twisting process. Energy efficiency was therefore a top priority when setting up the twisting mill of GRG Cotspin Ltd. Since 2016, 43 Saurer FusionTwisters have been producing superior quality twisted yarns with unrivalled energy efficiency. The FusionTwister’s low energy consumption and high winding speeds increased the company’s profitability and competitiveness.
10% faster, 15% more economical
GRG has never regretted its decision to purchase the FusionTwister. “Saurer promised the lowest energy consumption in its field, which has been proven time and again in our production since then,” says Dr. Rakesh Sharma, the Group CFO of GRG Cotspin Ltd. The energy consumption of the FusionTwister is 15% lower than comparable machines from competitors.
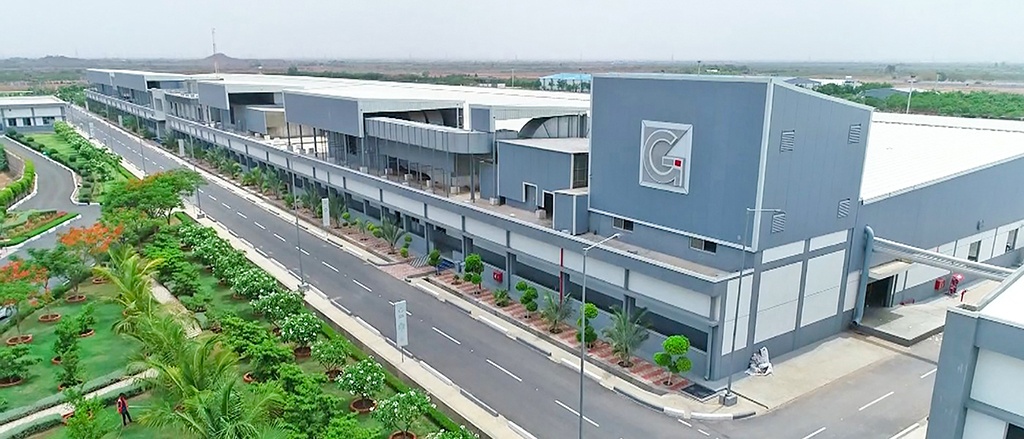
Twisted yarns with very low twists, such as those produced by GRG, at high winding speeds. This requires particular robustness from the twisting machine. The winding and traversing mechanism of the Saurer FusionTwister enables maximum speeds even with very low twist insertion in the yarn. For GRG this means a speed gain of 10 % in production.
GRG therefore decided to purchase a further 53 twisting machines from Saurer in 2021 in order to drive forward its ambitious expansion plans in an energy-efficient manner. “The cost-efficient production processes far outweigh the investment costs,” explains Dr. Rakesh Sharma of GRG.
Mr. Dilip Kulkarni, Vice President Operations elaborates the key points, which made the Saurer FusionTwister as their only choice:
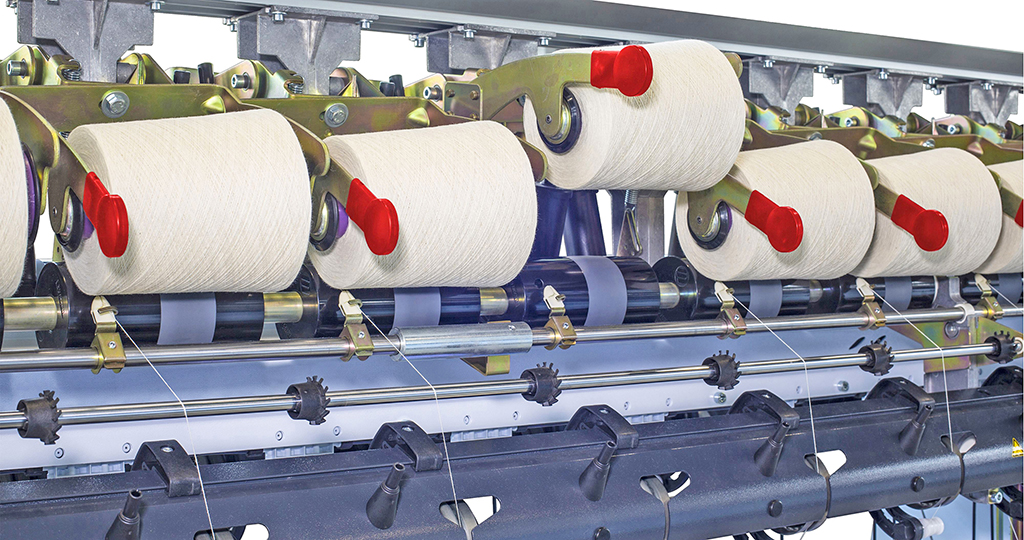
Design to perform
“In GRG we produce versatile yarns with very low twist as well as so called Zero Twist yarn for high value terry fabrics. This demands robustness of the machine for very high winding speed. Saurer’s design of winding and traverse mechanism allows us to run the FusionTwister at higher r.p.m even at low twist level,” says Mr. Dilip Kulkarni.
Benchmark for best quality
However, the FusionTwister is not the only benchmark for economy in the twisting process. The yarn quality achieved is also outstanding. The yarn contact points in the yarn path consist of yarn-friendly ceramic elements and plasma-coated surfaces. This ensures quality-assured processing of the yarn. The new traversing geometry ensures uniform package density from the centre to the edges.
Special design for a larger bobbin weight
Saurer has developed a spindle, which on the one hand allows a larger bobbin weight for more efficiency in the downstream process, and on the other hand keeps the energy requirement at a low level. Saurer found the solution in a 7” package with a larger pot and a highly efficient spindle.
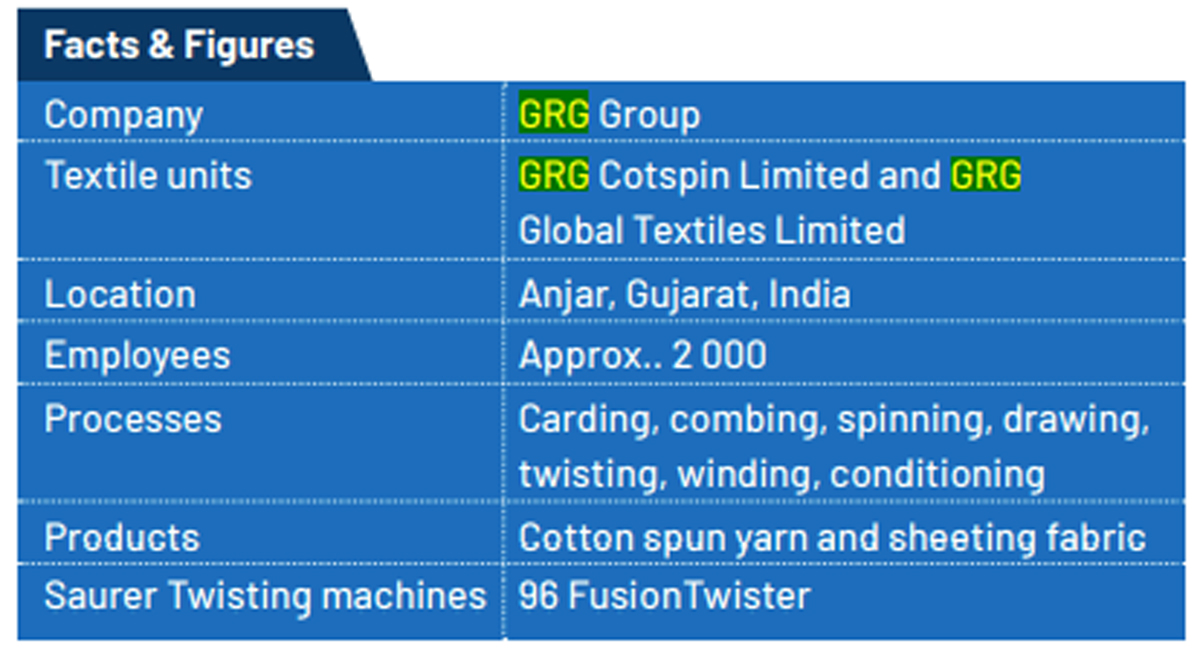
The new mill GRG Global Textiles Ltd can respond even more flexibly to all customer requirements with the new Saurer FusionTwister. The cost-effectiveness of the Saurer FusionTwister is GRG’s guarantee that they will be able to successfully implement their ambitious expansion plans with the enlarged twisting mill.