Earn more money with a Rieter compact-spinning system
The current situation caused by COVID-19 means priorities in the spinning industry have shifted. It is essential to get the best out of existing systems. But there will also come a time after COVID-19, in which investments will be made in new systems; such as in the Rieter compact-spinning system, which enables a significantly higher cash flow.

The Rieter compact-spinning system with the high-performance card C 80, comber E 90, ring spinning machine G 38 and the compacting device COMPACTdrum is known for very good yarn quality, the highest possible level of flexibility and low production costs. A complete Rieter system draws on Rieter’s expertise throughout the entire spinning process: from raw material to yarn.
What factors influence production costs? In this example, a compact-spinning system is used to produce combed cotton yarn with a count of Ne 60 for shirting fabrics (Fig. 1). A Rieter system is compared with a “mixed spinning mill” equipped with machines from different manufacturers. Rieter systems are most impressive when it comes to raw-material utilization, energy requirements as well as personnel and space requirements. The cash flow generated demonstrates the outstanding economy of the complete system, which is perfectly synchronized and is supplied from one source.
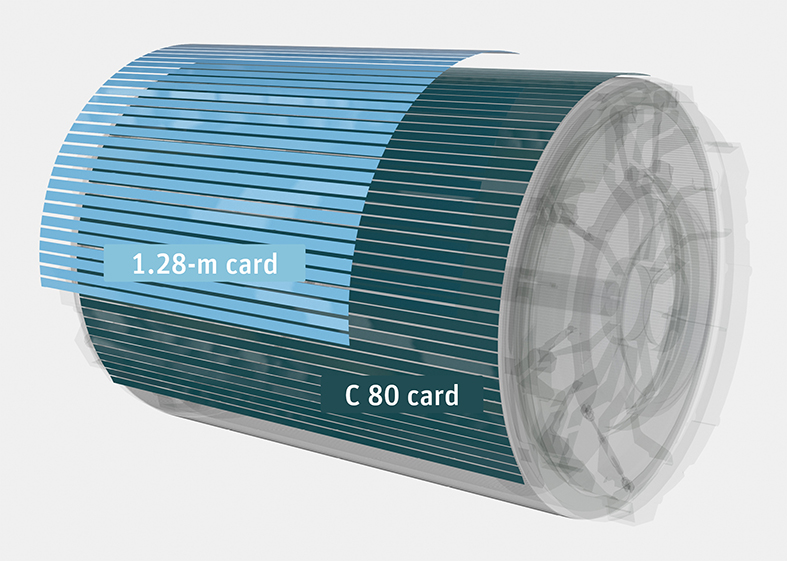
Good Raw-Material Utilization
Optimal raw-material utilization is achieved in the blowroom line VARIOline thanks to the combination of microtufts, the function VARIOset and progressive cleaning. An efficient blowroom process is dependent on the raw material being well opened from the outset. The automatic bale opener A 12 is capable of breaking down the bales into microtufts. The removal of trash and dust from small tufts in the downstream blowroom process is considerably more efficient and gentle. On the high-performance cards C 80, the maximum technological carding area with 40 active flats and a working width of 1.5 meters as well as the pre- and post-carding zones that can be equipped individually ensure reduced loss of good fibers while retaining the same sliver and yarn quality (Fig. 2). High-quality technology components and optimally coordinated combing movements on the comber E 90 (Fig. 3) allow reduced noil extraction while retaining the same yarn quality. Over the entire spinning process, this results in a raw material saving of 1%.
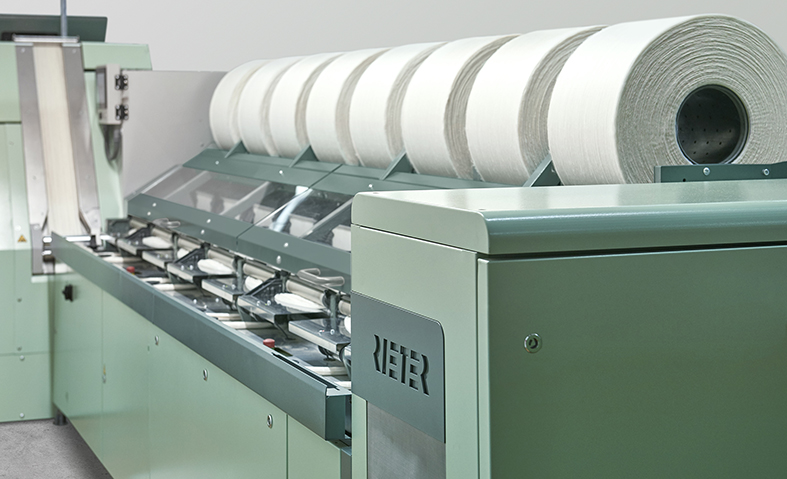
The Energy Saver
Rieter compact-spinning machines save energy. This also applies to Rieter ring spinning machines combined with compacting device COMPACTdrum (Fig. 4). The sieve drum of the compacting device that compresses (i.e. compacts) the fibers has been optimized and the compacting zone reduced to the necessary minimum. The energy required for compression is therefore very low, at around five to eight watts lower per spindle than that of compacting solutions from other suppliers. With energy-efficient drive concepts and innovative machine components throughout the process, the Rieter system is capable of offering 10% energy savings – all the while maintaining the highest possible levels of productivity.

Reduced Personnel and Space Requirements
The high productivity of Rieter machines allows a reduction in the number of machines, thus saving a lot of space compared to a process using a “mixed system.” In the case study mentioned above, the Rieter spinning mill requires one compact-spinning machine, one autoleveler draw frame, one comber and two cards fewer than the “mixed system.” Space-saving machine concepts, such as for draw frames, also lead to a more compact spinning mill layout. This allows space savings of approximately 7% (750 m2) – and therefore lower building investment and maintenance costs.
Thanks to the reduced number of machines and therefore a reduced operator workload, the automatic roving bobbin transport system SERVOtrail and user-friendly machines with a uniform design, 6% fewer personnel are required and can therefore be used for more efficient tasks.
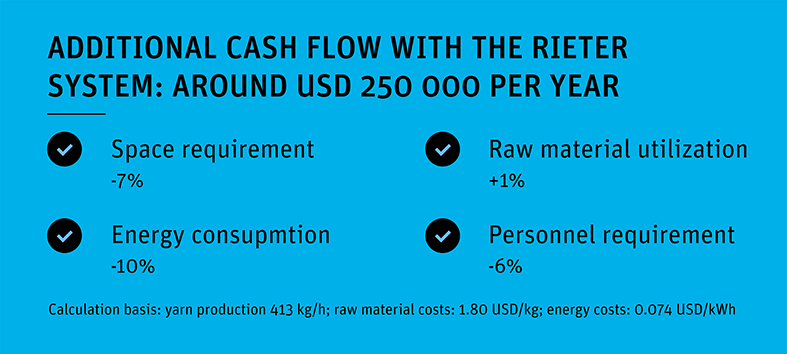
Higher Cash Flow Thanks To Lower Production Costs
Taking raw-material utilization, energy and labor costs, interest rates, yarn and noil sales and ongoing operating costs into consideration, the total production costs calculated for the Rieter system for the combed compact-spinning process are lower than for a solution from different suppliers. This means that customers who invest in the Rieter compact-spinning system as per the example shown generate a cash flow that is around USD 250 000 per year higher than that of customers who opt for a “mixed spinning mill” (Fig. 5).
Maximum Flexibility as an Additional Advantage The combination of the ring spinning machine G 38 with the compacting device COMPACTdrum is ideal for customers who appreciate flexibility in yarn production. COMPACTdrum makes it easy to change between ring and compact yarn, because the compacting device can be easily attached and removed from the ring spinning machine. COMPACTdrum can be supplied with a new ring spinning machine, and existing Rieter ring spinning machines can be retrofitted. In addition, the G 38 is capable of producing high-quality special yarns. Thanks to the integrated VARIOspin system for slub yarns, which is integrated in every G 38, the customer can change between standard and slub yarns simply at the touch of a button. The G 38 with COMPACTdrum is suitable for all raw materials and yarn counts.