India-based Geratex Machinery Pvt. Ltd. is introducing a new revolutionary and sustainable technology at ITMA 2015 that is set to change the way fabrics are processed while desizing, bleaching, mercerising and washing.
For the first time in the textile sector worldwide, Geratex Machinery is using the Ultra Sonic technology on industrial size machines in its fabric processing for desized chemical impregnation, bleaching chemical application, mercerising, dyeing or washing, which offers higher efficiency in terms of space, energy usage and also chemicals and water consumption.
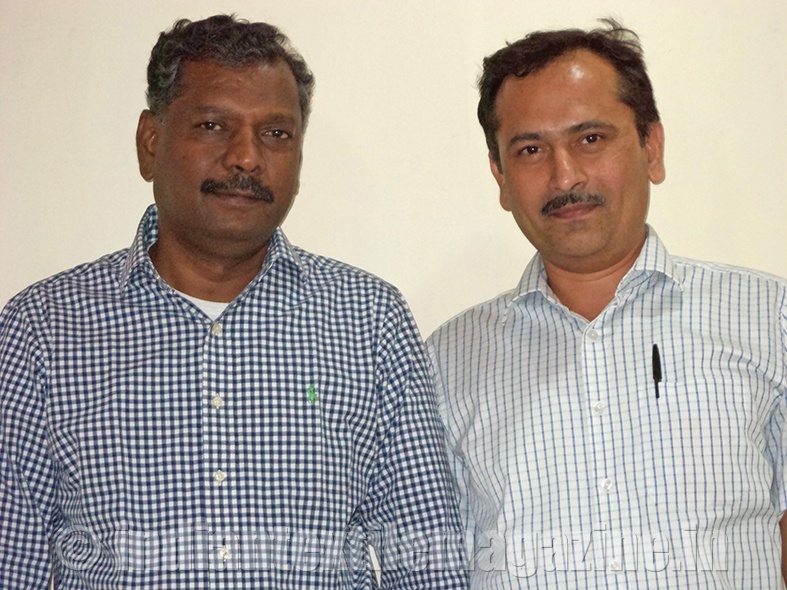
The Ultra Sonic waves accelerate the water molecules in the bath and move practically at the speed of sound or several thousand times in a second, which create a turbulent effect in the machine and achieves the whole process in half the time taken by conventional machines, due to the speed of the waves.
The company has sourced the Ultra Sonic technology from Germany and integrated into newly developed machines. The beauty of the design of the Ultra Sonic technology of Geratex is that it can even be integrated or retrofitted into the existing and conventional fabric processing machines.
According to the Managing Director of Geratex Machinery, Mr. K. Venkat Reddy, while newer technologies have been introduced in spinning and weaving in the last 3-4 decades, there has been absolutely no change in fabric processing technology in the same period.
Explaining the technology, Mr. Keyur Vyas, who integrated the Ultra Sonic technology and co-inventor of this technology along with Mr. Reddy, says: “The amount of chemicals added while washing these fabrics is less than 100 milliliters, but the amount of water needed to wash out these chemicals is five litres per kg of fabric.”
“The Ultra Sonic technology which has been successfully applied in other industrial applications till date was tried and tested for processing textile fabrics for the first time on an industrial size machine of 2 metre width and gave great results in terms of saving in chemicals, washing consistency, water used, energy efficiency and the space utilised by the machine itself,” he adds.
Mr. Vyas further observes that with their innovation they are providing a solution for a major pain area of the fabric processing industry.
Beginning with the desizing process, since the fabric has a good amount of sized material, it does not absorb water or chemicals, as high-concentration of chemicals are used to first loosen the size and then wash off the sizing, utilising high amounts of water.
On the other hand, the Ultra Sonic washing technology completely does away with wetting agents, while the amount of chemicals used is less by 30 per cent and so consequently, the volume of water used is also reduced considerably.
On the Tegewa scale of 1-10, a measurement tool to calculate the efficiency of washing, the conventional technology scores between 4 and 6 points after desize washing, while the Ultra Sonic technology achieves between 7 and 8 points.
“In bleaching too, the Geratex Ultra Sonic technology consumes 30 per cent less chemicals and achieves the desired bleaching effect in 50 per cent of time when compared with conventional machines, while for post-dyeing washing also, the results were equally good,” Mr. Reddy says.
In mercerising also, conventional machines use 300-320 gms per litre of caustic soda, while the new technology uses just 200-220 gram per litre and delivers the same results.
In conventional technologies, water is heated to temperature of 95 degree centigrade, before washing, while in the Ultra Sonic washer, the water needs to be heated up to just 65 degree centigrade, which results in high energy savings.
However, Mr. Reddy says the new technology is not suitable for printed fabrics washing, as the washing efficiency is so high that the prints get smudged. At the same time it is suitable for all kinds of fabrics, whether made from cotton, man-made, blends or even wool fabrics.
Mr. Vyas also shares that this technology is also useful when treating functional fabrics with anti-bacterial or flame-resistant fabrics properties, as the Ultra Sonic technology helps functional chemicals penetrate deeper into the fabric, thereby helping the functionalities last longer, even after repeated washes.
Further, even though it is a newly introduced technology, the cost of installing it will be down by 40 per cent when compared with conventional fabric washers as the cost of the new technology is slightly less. It takes less space and requires smaller related ancillaries like boilers, electrical power, water, etc.
In a nutshell, as per the test results, the technology helps save around 20-30 per cent of chemicals, achieves 30-50 per cent in water savings and 30-35 per cent in energy savings, with the biggest advantage being the size of the machine which is compact and helps save space to the extent of 60 per cent.