The ring spinning machine G 37 meets all requirements for an efficient yarn production. The machine with improved reliability produces high-quality yarns with highest production rates and lowest energy consumption. Also in terms of flexibility, the G 37 ensures optimum preparation for the ever-changing market conditions.
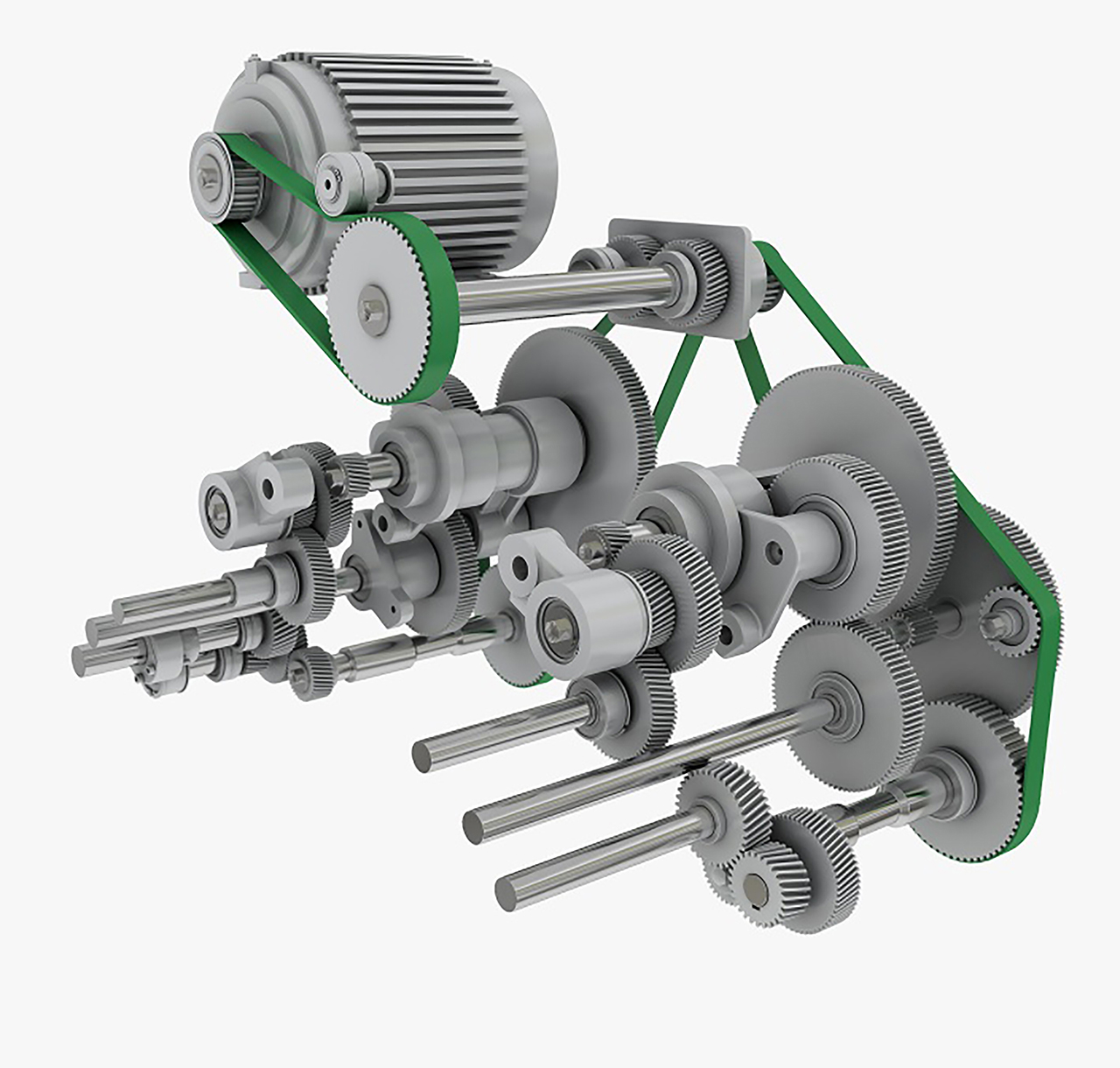
With the G 37 customers profit from a top-quality machine, efficient energy utilization with LENA spindles and IE4 main motors as well as an optimized suction system. The semi-electronic drafting system allows a fast change of yarn parameters. As a result, only little time is required for a machine changeover. The integrated individual spindle monitoring system ISM premium reduces personnel costs significantly and opens the door to the world of digitization. Besides efficiency, the G 37 is also very flexible. With the new generation of compacting devices for compact yarn production and systems for slub and core yarns, customers are optimally prepared to easily adapt to new market conditions.
Energy-Efficient Drives and Spindles
In ring yarn production, 50-60% of the energy costs of the whole spinning process are caused by the end spinning machine. For this reason, Rieter is particularly investing in energy-efficient and reliable technologies for the most important components like motors, inverters and drive systems.
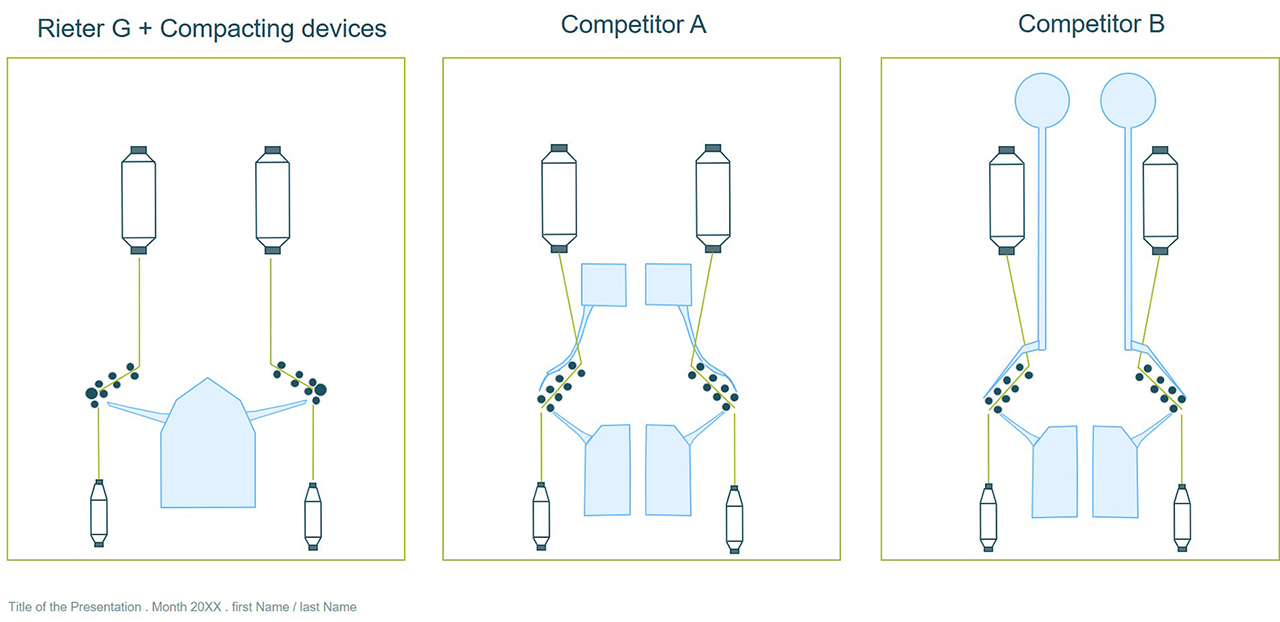
More than 80% of the energy of the end spinning machine is used for the spindle drive. Here, energy savings can be achieved with the extremely efficient permanent magnetic IE4 main motor which is developed for high spindle speeds. The motor can also be used profitably on machines with fewer spindles and low speeds due to its permanent magnetic functioning.
In addition, the proven Rieter 4-spindle tape drive with only one large drive motor shows great advantages. This drive is energy-efficient, easy to handle and operates without failure. The low contact pressure due to only 90° enlacement guarantees low energy consumption. Furthermore, the LENA spindle reduces the overall energy consumption of the machine by up to 4% and is recommended for yarn counts Ne 28 and finer.
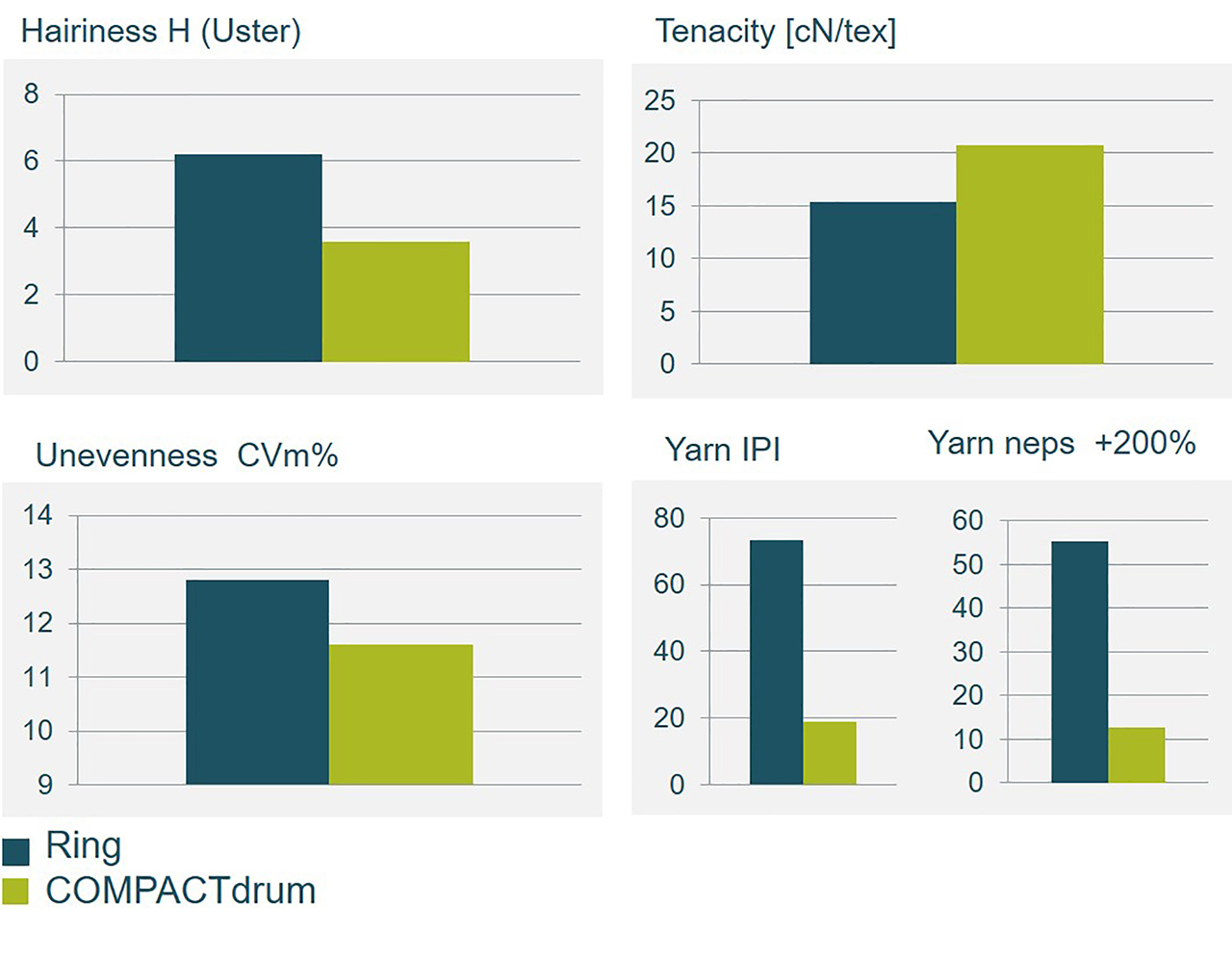
Short Machine Changeover Time
In terms of efficiency, an outstanding advantage of the G 37 machine is the easy yarn setting. The semi-electronic drafting system allows quick gear change for yarn count settings (Fig. 1). Parameters such as yarn twist and twist direction can be simply set by fingertip on the operating unit. There is no need to change gears or make any other mechanical adjustments which leads to less work for operating personnel. The machine changeover time for a complete yarn parameter change including yarn count, twist and Z or S twist direction is reduced to 65 minutes, compared to 145 minutes for a competitor’s mechanical system. The spinning of small batches becomes much more economical.
Unique Suction System
The suction system of the G 37 is an outstanding advantage compared to competition. The large cross-section of the suction duct lowers the air speed and reduces the air resistance (Fig. 2). This advantage is particularly apparent when the G 37 is equipped with the compacting device COMPACTdrum. The double-sided suction on long machines creates additional energy savings by further reducing the energy required to generate the necessary vacuum. Compared to a single-sided suction system, the same air volume can be transported using less energy.
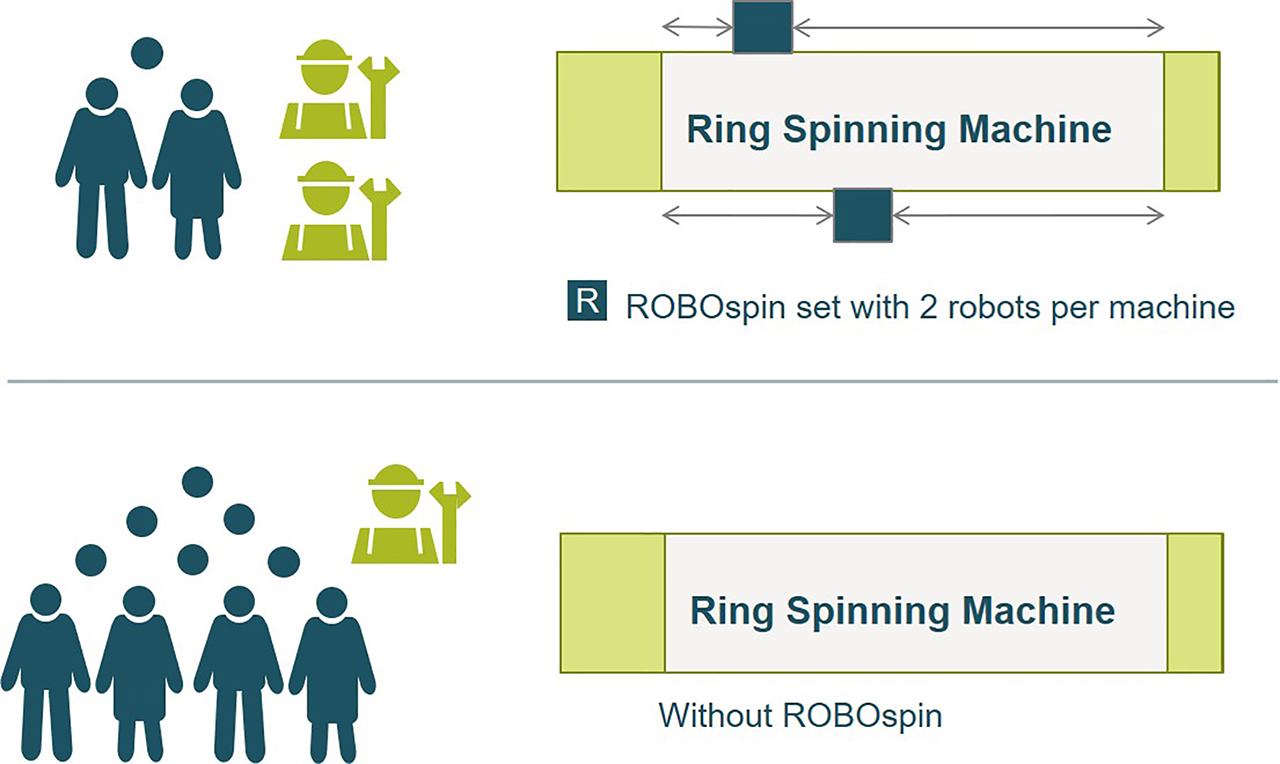
High Flexibility with Devices for Compact and Special Yarn Production
The compacting device COMPACTdrum for the G 37 enables a quick changeover from conventional ring yarn to compact yarn with simple installation. COMPACTdrum performs with extraordinary yarn quality results. Significantly less yarn hairiness as well as a better yarn tenacity and unevenness improve the running properties in further processing. In the end product this leads to an enhancement of the appearance (Fig. 3). With low energy requirements, very high productivity and long-life technology components, production costs are kept low. No periodic wearing of compacting elements like aprons are necessary.
The production of fancy yarns is also possible at any time. This flexibility is made possible by the Rieter one-duct system that has incorporated such adaptations in its concept. Whether you choose the highest yarn quality, the fastest spindle speeds, or a cheaper raw material – with the G 37, maximum plant efficiency is achieved anytime.
Efficient Personnel Deployment with ROBOspin
ROBOspin is the first fully automated piecing robot for ring spinning machines and increases productivity significantly. One robot per machine side repairs ends down that occur during doffing or while the machine is running. The robot travels directly to the affected spinning position and repairs ends down in the shortest time possible (Fig. 4). As a result, the complete piecing cycle runs fully automatically – from finding the yarn on the cops to placing the yarn in the traveler, in the yarn guide element and behind the delivery roller. The robot receives the required information from the integrated individual spinning monitoring system ISM premium.
Reduced number of operators simplifies mill planning and organization:
• Highest mill efficiency with ROBOspin
• Reduction of human error impact
• Reduction of staff absence impact (no illness, no holidays, no quitting)
ESSENTIAL – The All-In-One Mill Management System
ESSENTIAL is a modular system to gradually digitize the spinning mill while meeting the highest security standards. The Rieter Digital Spinning Suite creates values from data by providing key indicators of spinning mill performance. This system connects all machines, auxiliaries, and business management systems in one or several spinning mills. Customized to the requirements of the spinning mill, ESSENTIAL displays user-specific information. As a result, owners, managers, and operators can manage, monitor, and maintain spinning mills with one click.
These and many other features make the new Rieter ring spinning machine G 37 the perfect fit for spinners who count on high efficiency while saving costs through low energy consumption.