Banswara Syntex partners Rieter for ring spinning modernisation
Banswara Syntex Ltd., based in Banswara, Rajasthan, manufactures dyed, synthetic fiber blend yarns, wool and wool blend yarns, and various types of material. With 1,50,232 spindles, the company is one of the most prestigious manufacturers of dyed polyester/viscose yarn and is a front-runner in this segment. The mill, which was started by Mr. R.L. Toshniwal, is today the first port of call for buyers in the dyed polyester/viscose yarn and related textiles segment. Banswara Syntex exports products to over 50 countries across the globe.
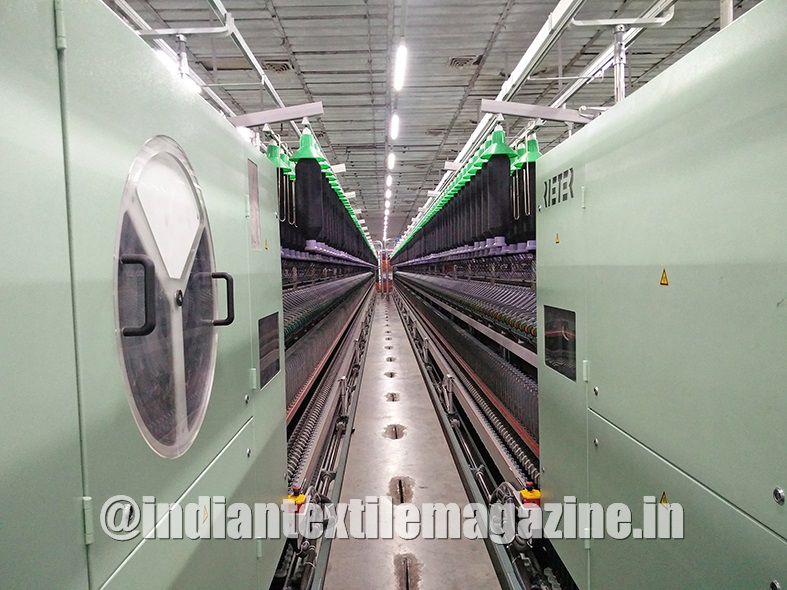
A Rieter customer, Banswara Syntex planned to modernize its ring spinning machines G 32 with the aim of reducing energy consumption and increasing productivity. To maintain the credibility of the Banswara brand in an established market, the company’s strict yarn quality requirements had to be met. The customer installed the competitor’s latest ring spinning machine adjacent to Rieter G 32, because for the customer it was important to compare the performance of the two machines before purchasing the sixth ring spinning machine G 32.
Rieter recommended replacing the existing short manual doffing ring frames with state-of-the-art automatic doffing ring frames. Once the performance comparison had been completed, which came out in favor of Rieter, Banswara Syntex decided to modernize their five ring spinning machines G 32. As replacing existing ring machines with long ring frames for the polyester/viscose dyed segment is highly complex, Rieter employed a special cross-functional team. The machines were configured with Rieter MMF package, including 30 mm bottom rollers, SERVOgrip blades and a special drafting system. The team worked collectively, enabling them to achieve the desired machine performance and meet the customer’s requirements.
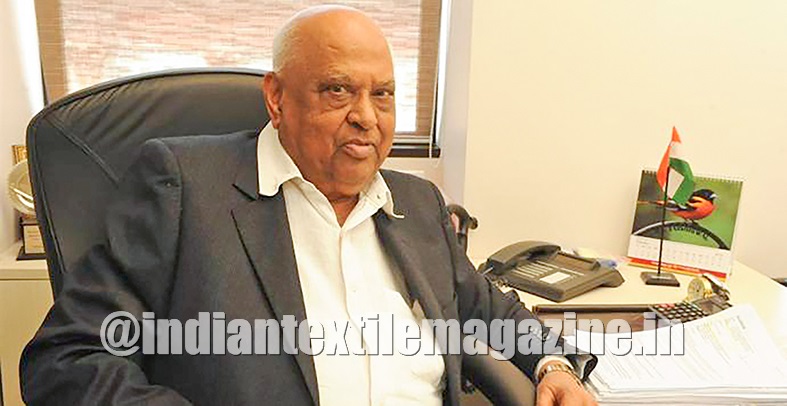
The five ring spinning machines G 32 ran perfectly from day one with an average spindle rotation speed of 20,700 rpm. The customer spins Ne 30 yarn from polyester and viscose dyed fibers and the G 32 machines are running at 5% faster speed and require comparatively less energy than competitor. In-house energy consumption readings revealed that the energy consumption of the G 32 is around 8% lower than the competitor’s latest machine. The yarn quality is consistently high and manufacturing costs have been reduced. Just one month after commissioning the five modernized G 32s, the customer decided to purchase a sixth ring-spinning machine from Rieter.
The customer’s statement
Says Mr. R.L. Toshniwal, Chairman of Banswara Syntex Ltd.: “Since they were commissioned, the Rieter machines have run at a consistently high speed and produce high-quality yarn. Thanks to the energy savings achieved, yarn manufacturing costs are remaining low. So Rieter’s ring spinning machine G 32 was the perfect solution for us. Energy savings of 8% make a considerable difference and significantly reduce operating costs for the process. We are pleased with our decision to choose machines from Rieter for this challenging project”.