The textile industry in India is currently besieged by rising energy cost which in turn has led to a surge in the overall production cost. In such a scenario, the need for energy conservation has assumed paramount importance in the industry. Manufacturing efficiency and agility to make the process more cost efficient is now the goal of the textile industry.
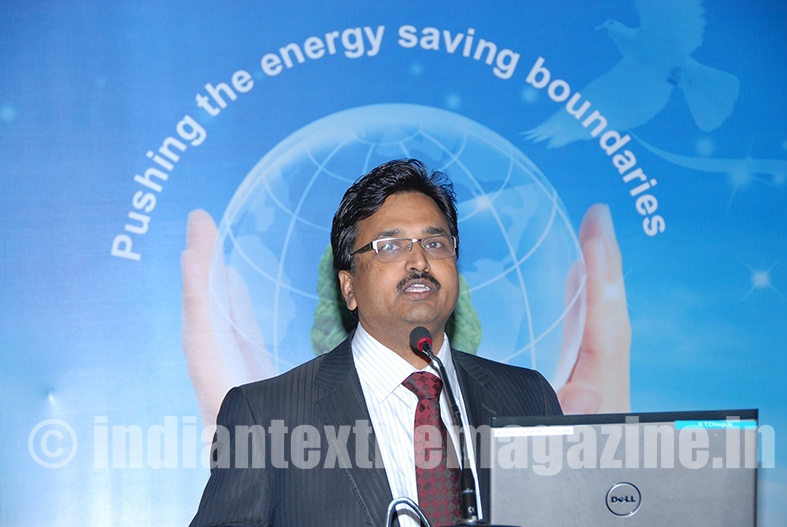
Generally, in close succession of the material cost comes the energy cost which is around 15-20 per cent of the total production cost in the textile industry. A major key to deal with the quandary of rising costs and cost competitiveness is automation. Gone are the days when one could see a labour-intensive, factory-based textile industry in which men and women toiled over looms and spinning jacks. Today, automation has made an all-pervasive impact on the textile industry which includes reducing the cost and saving energy.
Role of automation
The main objectives of automating a textile plant is to hone every section of the plant for the efficient management of the various stages of production, to provide facilities for planning and control at strategic points, to have compatible sophisticated technology systems and creating additional work stations as the business grows.
Automation mainly aids applications where synchronisation is required, helps where speed and logic are involved to perform a task and also gives visibility to see the performance of a machine.
We at Mitsubishi Electric have been continually working in providing energy conservation techniques and improved operational and maintenance practices. For instance, we offer energy efficient controls to deliver efficient solution for complex mechanisation processes using our variable frequency drives (VFDs) and servos for synchronisation, programmable logic controllers (PLCs) for logic and human machine interfaces (HMIs) for visibility.
New features like optimum excitation control will give 3 to 4% energy saving than the standard variable frequency drive. Also features like KWH display on the drive which will help to Increase the visibility of the Energy consummation.
Now it is possible to communicate HMI directly to drives of different application and machine, which will add more flexibility in the system and will increase the visibility of different machine in one location.
With an increasingly competitive global business environment, most manufacturers are seeking opportunities to reduce production costs without negatively affecting the product yield or even its quality. But with the rising energy prices, costs are hitting a zenith and decreasing value that is added at the plant. To deal with this, successful, cost-effective investment into energy-efficiency state-of-the-art technologies and practices is important to maintain the quality of the product while reducing production costs.
This is especially important in the current age, as energy-efficient technologies often include additional benefits such as increasing the productivity of the company or reducing materials consumption. Even on this level, companies like Mitsubishi Electric India offer a vast range of automation and processing technologies, including controllers, drive products, etc. All of the company’s technology offerings come with advantages like optimisation of speed and downtime of the machinery, improving the quality of the product, reducing the recycle time and enabling more production in less time. VFDs and servos has features like auto tuning along the load; which will help to optimise the parameter setting according to the application and load condition of the machine.
Modern features like winder control & droop control and traverse function in drive which will help increase the flexibility and speed of the machine and will lead to decrease production cost with higher quality of production.
Increasing demand for energy saving and speed
Most companies today look for cost-effective solutions to improve output as well as save energy. Their demands range from asking for energy saving VFDs and servos to products that offer smooth speed variations.
Mitsubishi Electric is offering VFDs which run up to 590 HZ (12 time of base speed) and servo with max speed up to 6000 RPM, which will help to increase the speed of the machine.
One of the likely emerging trends in the textile industry is use of IPM (permanent magnet) instead of induction motor as it offers high efficiency at no load, which will help in energy saving.
The company’s latest FR-A800 series VFD is designed to drive IPM motor, thereby offering energy-efficient solution to the textile industry.
Flexible solutions for the industry
An important factor in the success of an automated textile mill is the flexibility of the automation process. Mitsubishi Electric India helps organisations succeed with customized solutions and proven products that are innovative, flexible and high performing, yet cost-effective. The company provides flexible solutions as per the automation requirement of the machinery.
In a nutshell, recent advances in automation for the textile industry have resulted in a major cut in costs due to skyrocketing energy bills. In order to mitigate this, Mitsubishi Electric has several cost-effective automation solution, designed for the industry.
Automation has now become a determining factor in whether or not a company will remain competitive within the textile industry. Investing in automated equipment is creating a valuable resource for large production volumes, which, in turn, are increasing profitability while reducing energy-costs.
By KT Chougule, A.G.M., Product Marketing (Inverters), Factory Automation and Industrial Division,
Mitsubishi Electric India Pvt. Ltd.