The group is a one-point source to get ring spun, open end, vortex, blended, fancy, mélange, recycled yarns and is a volume producer
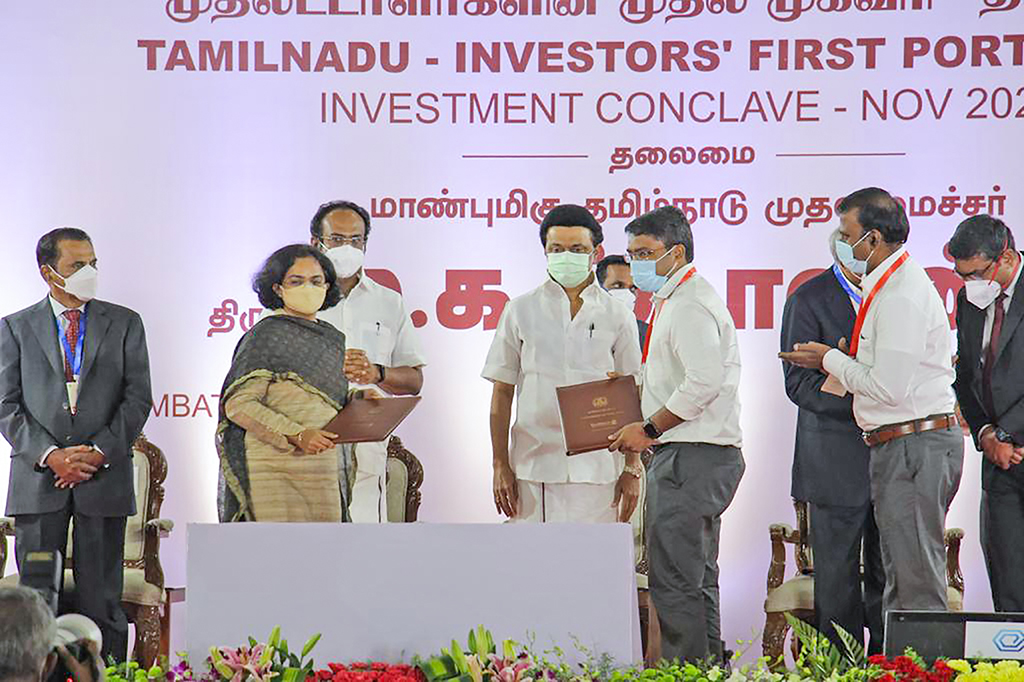
Started in 1988 with 3,000 spindles in Kottaiyur, Tamil Nadu, Eveready Spinning Mills Group now has five spinning units with about 1,79,000 ring spindles, 3,020 rotors, 29 vortex spinning machines, 55 high-speed knitting machines and six TPD yarn and fibre dyeing units. The production capacity now is 63 million kilograms of yarn and 4 million kilograms of knitted fabric per annum. “The vision is to produce products with consistent quality to win and retain customer confidence and loyalty by using good quality raw material, state-of-the-art machines and scientific management systems,” says Managing Director S Saravanakumar.
The products and solutions offered by the group include:
• Carded compact and combed compact
• Siro or slub
• Cotton (imported or Indian)
• Viscose, modal, tencel, micromodal
• Blended yarns using cotton, viscose, modal, tencel, micromodal, polyester, dyed fibres, dope dyed fibres.
• Ring spun or open end or vortex
• Knitting or weaving
• Melange yarns (grey melange, colour melange, injected slub, grindle, neppy, snow, etc).
• Dyed fibre or dyed yarn
• Organic (GOTS, OCS, GRS)
• BCI
• Contamination controlled with Jossi and Uster quantum clearer 3 or 4 with PP cleaning.
When asked about any recent and planned investments Saravanakumar listed out the following initiatives:
• Work is just started to establish a brand new 51,702 spindle Rieter ring spinning project with latest model machines and this is expected to start production within another 8-10 months.
• Installation of additional 25 MW capacity solar power plants is going on.
• A new fibre and yarn testing laboratory with latest Uster instruments will become functional with the new spinning unit.
• Discussions are underway to put a process house for knitted fabrics with 25 TPD capacity within the next 8-10 months.
• Knitting capacity addition to increase the production further by 10 TPD.
Saravanakumar points out nine key reasons that give the group its competitive edge:
- The group is a one-point source to get ring spun, open end, vortex, blended, fancy, mélange, recycled yarns and is a volume producer.
- Good quality raw material procurement is the specific skill of the top management.
- High-end Usterized laboratory, online monitoring systems like Ultimo, Visual Manager, Uster Expert, V Labo and T-Data give real time and long time data to fine tune and continuously monitor key quality parameters.
- Rieter Uniblend results in a very high blend uniformity matching or exceeding the international standard of ± 0.75%.
- Religious adherence to quality assurance and preventive maintenance schedules are the other hallmarks of the group which result in very high consistency in quality.
- Established shade development department and in-house dying capacity means matching any shade with high accuracy.
- ISO certification, Com 4 license, Usterized certification are the indicators of quality systems and levels maintained.
- Uster Jessi in combination with Uster Quantum clearers enables the supply of contamination-controlled yarn.
- Knitting machines fitted with fabric scanners result in first grade fabrics of long lengths.
The group’s domestic and export market share are 90% and 10%, respectively. “Turnover in 2020-21 is Rs 850 crore. It will be Rs 1,200 crore in 2021-22,” says Saravanakumar. The total number of employees in the group is around 3,000, out which about 60% are female. Bus facility, help towards higher education, free medical facility, residential hostel with subsidised food are some of the good HR practices followed, apart from complying with the government norms.
Speaking on Eveready Spinning Mills Group’s focus on sustainability, he says: “We focus on reducing environment spoiling, reduce power consumption and to use the input to the maximum extent with low wastage.
Some of the steps undertaken are:
• Rainwater harvesting, having own windmill and solar plant, planting trees using efficient filters.
• Using energy-efficient machines including compressor, H plants, AWES and using vortex spinning technology.
• Taking continuous trials and using quality enhancing kits to improve yarn realisation, continuous training to use manpower fully and proper preventive maintenance to improve machine utilisation.”
Saravanakumar highlighted the automation and Industry 4.0 capabilities of the group in its manufacturing process. These include:
Automation:
• 80% of the total ring spinning spindleage is equipped with auto doffers and this will become 100% within six months.
• 30% of the total ring spinning spindleadge is connected to link winding and this will become 50% very shortly.
• Within the next six months 80% of the ring spinning spindles will be covered by bobbin transport system.
• Old simplexes are replaced with autodoffer simplexes connected to BTS.
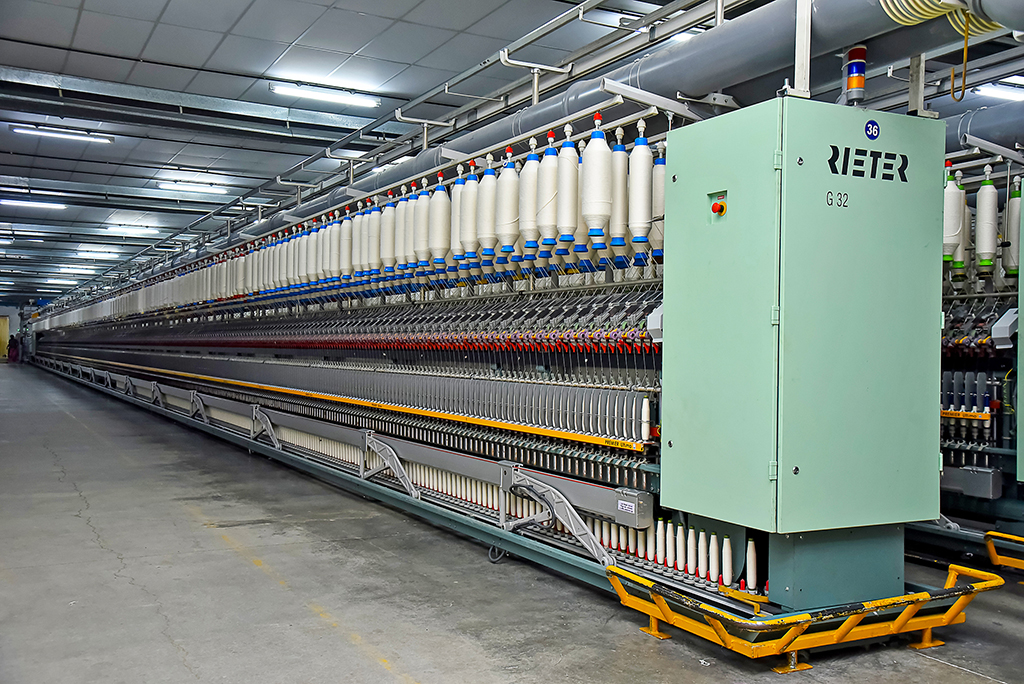
Industry 4.0:
• A matured ERP is in place for the past eight years covering all areas.
• Online monitoring and data collection systems like Ultimo (individual spindle monitoring in ring spinning), Visual Manager (individual drum monitoring in winding), V-Labo (individual spinning position monitoring in vortex), Digicontrol (automatic humidification plant monitoring), Uster Expert (quality monitoring system for yarn clearers) and T-Data (monitoring system for latest Truetzschler blow room, card and draw frame).
• Planning is underway to install online production, power and air monitoring system in all the machines in all units very shortly.
“Doubling the current capacity and entering strongly into the garments sector,” is how Saravanakumar puts across the group’s vision and plans for 2025 and beyond.