To meet rising demand for its fully automated and digitised fabric and part handling solutions, Eton Systems – a member of TMAS, the Swedish textile machinery association – has just moved into modernised new premises in Borås.
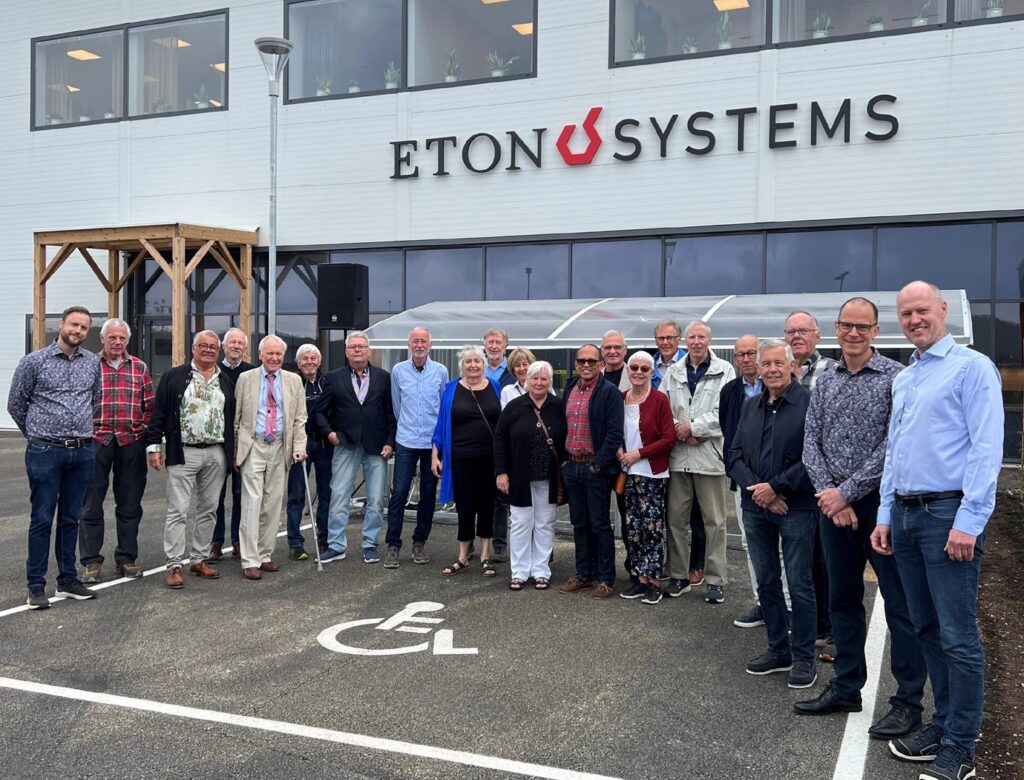
The company was founded in 1967 in Borås – widely known as Sweden’s textile city and home to worldwide brands and companies, as well as the prestigious Swedish School of Textiles – as a result of future-looking research and development at shirt maker Eton Shirts.
Eton Shirts, founded in 1928 and still also headquartered in Borås, was very early to realise the benefits of streamlining its production processes, minimising downtime and better utilising factory space. Its internal R&D led to the world’s first overhead unit production system (UPS).
Today, Eton Systems UPS technologies have a positive impact on the productivity of thousands of production lines for a range of industries. Designed to increase value-added time in production by eliminating manual transportation and minimising handling, the individually addressable product carriers are now fully managed and controlled by the company’s advanced software.
Roots and heritage
“We’re very happy that we have been able to realise our plans and site our new premises with advanced technologies here in Borås, staying true to our roots and heritage,” says Eton Systems CEO Jerker Krabbe. “Digitalisation and the push for more sustainable, shorter and less expensive supply chains are currently making manufacturing in high-cost countries within Europe more attractive and our technologies are very much a part of making reshoring a feasible option for our customers. It’s fantastic that we can still undertake projects like this in Sweden in order to grow for the future.”
10,000 pieces daily
Kinnarps, one of the largest providers of high quality workspace solutions in Europe, has retained all of its production in Sweden, and is thriving with the assistance of Eton Systems.
At the Kinnarps fabric upholstery plant for office chairs in Skillingaryd, customers are able to choose from over 250 different fabrics for their designs and collections, or to provide their own, in addition to selecting from a range of bases, springs and wheels.
With the installation of a full Eton UPS system, the lead-time from order to finished product from the Skillingaryd plant was cut from nine-to-ten days to just five days, due to a reduction in set-up times and other preparatory operations at individual work stations – a distinct competitive advantage.
On a daily basis, the Eton overhead system is loaded with more than 10,000 pieces, each with their own identification codes, enabling them to be fully tracked as they move sequentially through the phases of production. An automatic buffering system enables all products to be moved to each stage of the production process easily and just in time.
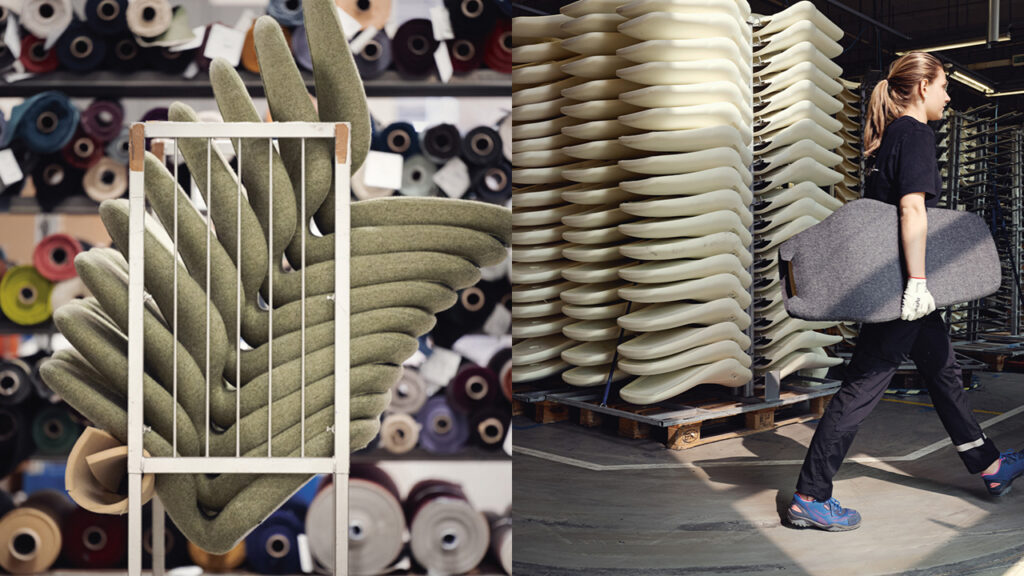
Kinnarps also appreciates Eton’s latest software, which provides an overview of every single unit produced and has led to a significant reduction in waste.
Full control
With annual sales of SEK 4.5 billion and a workforce of 1,700 people, Kinnarps is operational in over 40 countries and the concentration of its production in Sweden enables it to retain full control over its entire manufacturing chain, as well as ensuring decent working conditions for all of its employees.
“The advantage of this were particularly evident during the pandemic, when the transport chains caused major problems for companies with production in distant countries,” says Thomas Wilsson, manager at the Skillingaryd plant. “In addition, we don’t need to take a gamble on getting a big order and if our order intake increases, we can scale up our own manufacturing process relatively quickly. It also gives us great flexibility. If a product needs to be changed, we just do it and don’t need to wait until existing stock has sold out. If we want to make updates, improvements or efficiencies, we can react much faster.”
Life cycle
Sustainability is naturally high on the Kinnarps agenda but the company stresses that it is essential to create interior design solutions and furniture that are suitable for use over a long period of time.
“Sustainable interior design is as much about the present as the future,” says Kinnarps Global Range Director Jenny Hörberg. “When choosing interior design and furniture, it is important to take the entire life cycle into account. It’s also about choosing furniture with carefully selected materials that are designed and prepared for renewal, to maximise the life span and create conditions for sustainable circularity.”
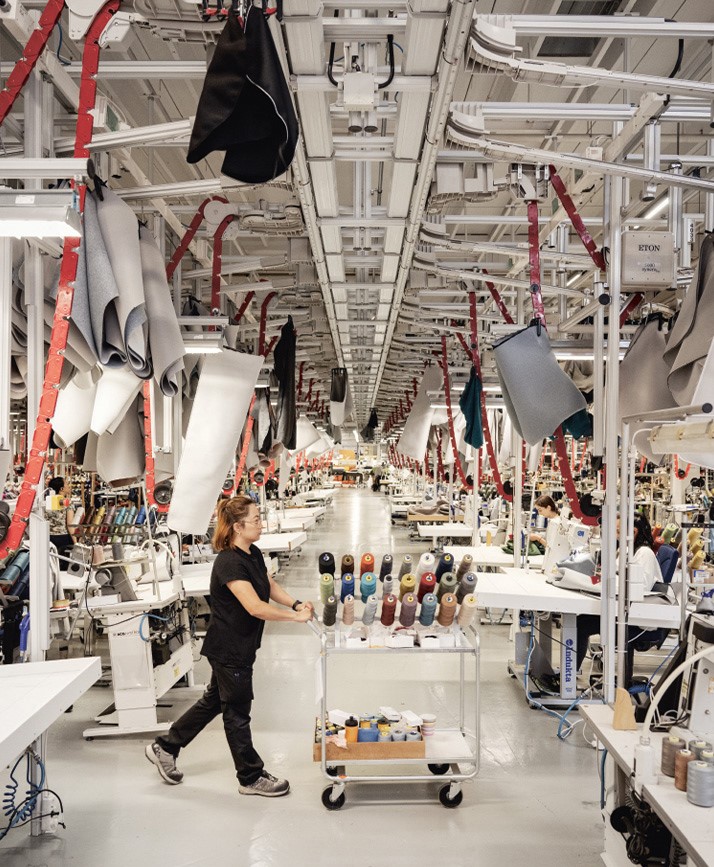
“We help our customers make sustainable and circular choices from the beginning that provide the conditions for futureproof environments,” adds Global Sales Director Dan Molander. “Based on needs analysis, we create customer-unique, ergonomic and flexible solutions, designed for today’s individuals and activities, but which are also ready to meet future needs and challenges. Through furniture and concepts that can be updated, renewed and renovated, we enable adaptable interior design solutions that can be developed to meet changing needs and last for a long time.”
Blueprint
“Every year, more than ten million tons of furniture is thrown away in Europe and smart companies like Kinnarps are at the forefront of pushing the furniture industry to take responsibility for how it is designed, manufactured and transported to create the conditions for sustainable interior design,” says TMAS Secretary General Therese Premler-Andersson. “Working with our member Eton Systems, Kinnarps has created a blueprint for how things should be done at its operation in Skillingaryd. Like Kinnarps, Eton Systems, in opening its new Borås HQ, is also committed to expanding sustainable manufacturing here in Europe.”
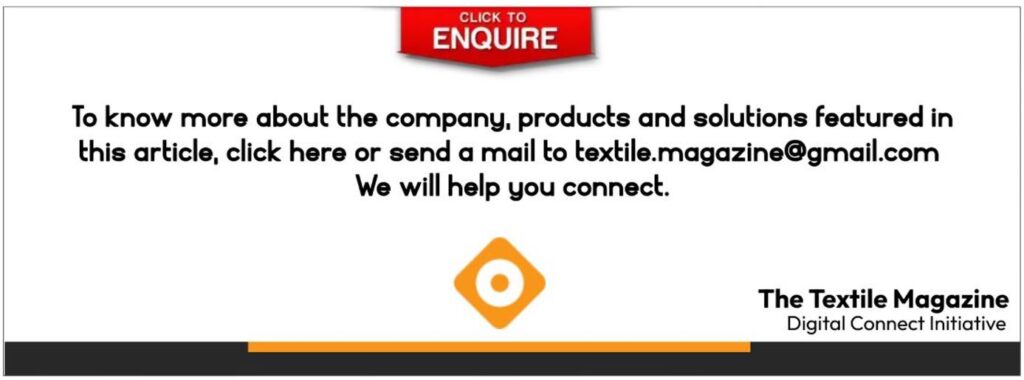