Faster than a formula 1 car: During cabling, a mechanical yarn finishing process in carpet manufacturing, the yarn in the “CarpetCabler”, built by Saurer Volkmann in Krefeld, reaches top speeds of up to 420 km/h (261 mph). With a few decisive innovations the Saurer Group, with seven locations in Germany, is making a significant contribution in the effort to reduce energy consumption and therewith also the CO2 emissions associated with industrial carpet manufacturing. Why can their solutions save up to 40 percent energy and how does Saurer keep the customers’ machines up-to-date? We asked Dr. Martin Folini, CEO of both, the Saurer Group and its largest business unit, Schlafhorst Zinser (leading in the production of roving frames, ring and rotor spinning and winding machines).
Which Saurer highlights will you be offering to visitors at your booth at the ITMA in Milan in November?
One of the biggest highlights is undoubtedly our latest winding machine, the Autoconer 6, which Saurer Schlafhorst launched into the market in 2015. This will be the trade fair début for the winder and its increased productivity combined with lower consumption of energy is sure to impress.
Carpet yarn manufacturing is very energy-intensive. During take-up, the outer yarn is wrapped around the inner yarn at very high speed. This is where the innovation starts.
Our engineers have succeeded reducing the rotating mass of the spindle significantly by decreasing its dimensions. At the same time they have reduced the yarn balloon size and shape with the aid of a patented outer yarn delivery system in a controlled manner. By harmonising the spindle diameter and the balloon geometry, energy consumption compared to conventional technology is reduced by as much as 40 percent. Special drives and bearings are also needed to deal with the high speeds involved. These are practically frictionless and operate extremely quietly.
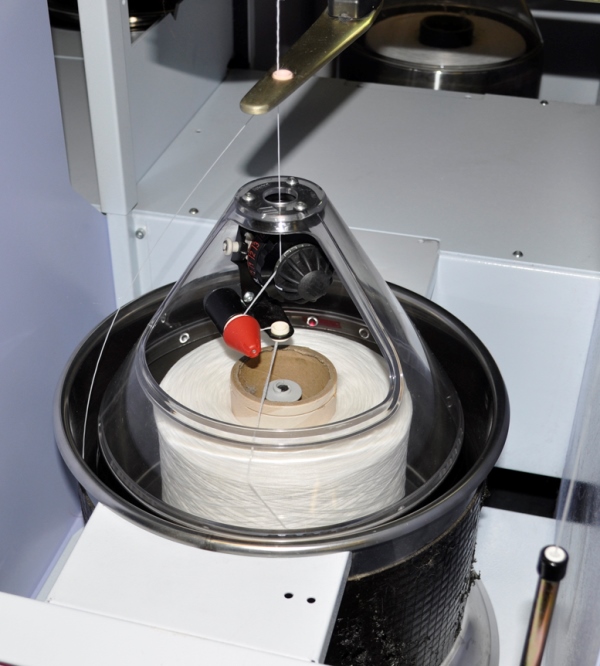
What is the significance of the balloon geometry in energy consumption?
When a strand of yarn is wound very fast around something, it is subject to centrifugal force and air resistance. It is like rope skipping, as the rope turns, it forms an arc that simulates the contour of a balloon. So the faster the yarn turns the harder it pushes outwards, like the skipping rope. This tends to increase its aerodynamic drag. So we need more force to drive the spindle and to control this balloon. If we can keep the balloon relatively small, the aerodynamic drag is also less powerful and our energy requirement is reduced correspondingly. After all, it takes much more force to turn a 20 metre long skipping rope than a very short one.
Can these energy savings be quantified?
The energy savings can be measured very precisely. Consequently, the investor can use a reliable tool to compare machines of older generations with the new ones. The benefit to the buyer is twofold. Certainly, he can count on using much less energy to produce the yarn, but one must also consider that most textile manufacturing machines are running in air conditioned plants. If less energy is consumed, less waste heat is generated, therefore the customer again saves energy, because the system does not have to be cooled as intensively to maintain its operating temperature.
Aftersales is an important sustainability tool for Saurer. You offer your customers a lifecycle partnership …
… because we want our customers to remain competitive, we offer them a lifecycle guarantee on their machines, which also covers innovation growth. They have access to the latest technologies developed by us in their respective field. Wherever possible, these are then retrofitted in the existing system so that it reflects the most up-to-date state of the art, which can also prolong the service life by several years. This enables the customer’s existing machine park to be updated inexpensively and without long production downtimes. You might be interested to know that the oldest machine Saurer maintains in this way has been in production for more than 40 years.
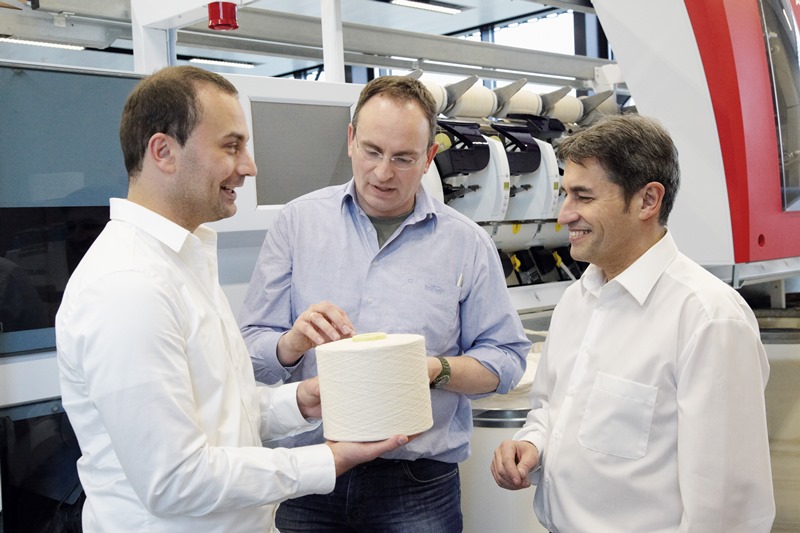
Please give us an example of the innovation growth you mentioned.
One example is the improved aerodynamics of a fan wheel, which is even more economical in terms of energy. The customer does not just receive a duplicate of the old component. We send a replacement fan wheel incorporating the new geometry that is compatible with the existing equipment. So the operator knows that his machine always reflects the latest state of our technical development.
Saurer introduced the E3 logo into the market to draw attention to customer benefits. What is the essence of the guiding principles behind the E³ philosophy?
These are the guiding principles that mark the design of every Saurer product and ensure that it will meet the challenges of the future. Energy is a huge topic, which will only loom larger in future. Every new machine launched into the market has a smaller specific energy footprint than its predecessor. This means that we are constantly reducing the amount of energy required to produce a kilogramme of yarn. Secondly, Economics represents increased productivity of the manufacturing process, which is the most important consideration in the customer’s purchasing decisions. And finally, Ergonomics, Time is money for our customers. A machine software has to be designed enabling the operator to learn to use it in a quick and intuitive manner. The great art of ergonomics consists in configuring the human-machine interface in such a way that the equipment can be managed safely and without difficulty by all workers on the factory floor. This includes self-explanatory menu structures, largely centralised control and monitoring so that the machine does not have to be configured and adjusted at numerous different locations. In short, E3 represents our ongoing efforts to reduce consumption in the yarn production processes still further, make them more economical and improve the ergonomic environment for the operator.
Schlafhorst and Allma Volkmann are also partners in the Blue Competence initiative and thus actively involved in the VDMA sustainability initiative.
Dr.-Ing. Jürgen Meyer, General Manager Schlafhorst Winding, a product line of the Business Unit Schlafhorst Zinser, has been a committed supporter of Blue Competence since its inception, working to incorporate sustainable textile production as a general principle in the German textile machine building industry and so increase its effectiveness. Blue Competence is the international brand name for sustainable solutions in machine and plant building, and it identifies those companies that align their development and production efforts with this criterion. Nowadays, users expect nothing less than productivity enhancing machines with automation options tailored to their specific needs, as well as optimised energy consumption while also satisfying the highest ergonomic standards.
“With our innovations we strive to continually reduce consumption in energy-intensive yarn production processes, thus making them more economical and further enhance the ergonomics for the machine operation in the future as well” says Dr. Folini.