by Arun Rao
Partners DRD Weaving for the Indian market
The Covid-19 pandemic disrupted global supply chains, creating significant challenges for businesses reliant on imports. For Surat-based weavers, weaving machine and spare parts importers, this disruption posed a severe problem. However, Mr. Ujwal Balar, Director of Emmtek Machines Pvt Ltd, saw an opportunity in this crisis. Emmtek Machines pivoted from import reliance to manufacturing high-quality weaving machine spare parts, transforming the company’s operations and contributing to the local economy.
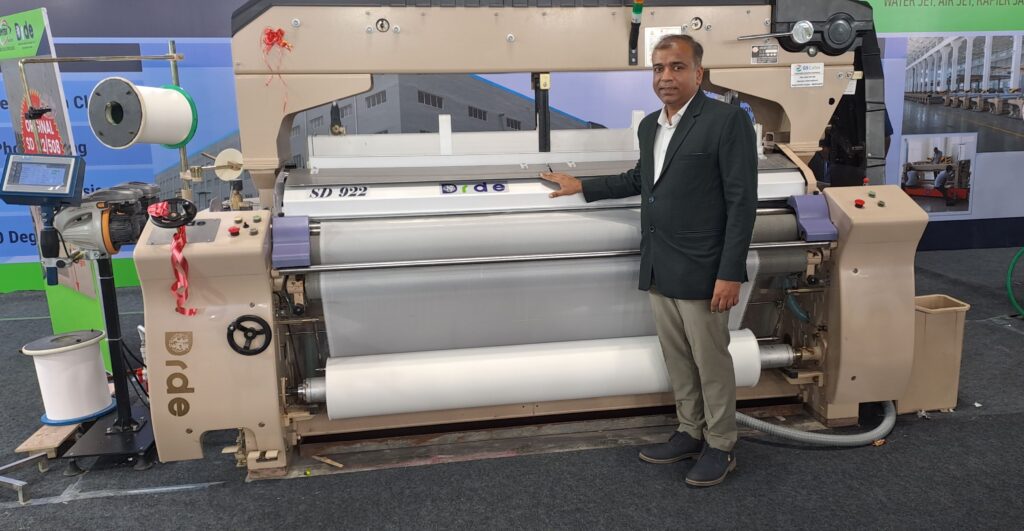
During the Covid-19 pandemic, China’s extended closure made importing weaving machine spares a significant challenge. Recognizing the need for a reliable domestic supply, Mr. Ujjwal Balar took a bold step to begin manufacturing these spares locally. Emmtek Machines started with the production of Cam Plates for Waterjet looms and gradually expanded their product range.
Expansion and Innovation
Initially, Emmtek Machines operated their production plant for just six hours a day. Today, the plant runs 24 hours, reflecting their growth and increased demand. A notable innovation by Emmtek is the production of India’s first plastic heald wire, which has become a game-changer in the industry. Mr. Balar explains, “Eighty percent of plastic heald wires bought in Surat are supplied by our company. These wires, unlike traditional SS wires, reduce the load on the loom, thus saving electricity.”
Plastic heald wires offer significant advantages, especially for weaving fabrics from bright and lustrous polyester yarns. They are not only easier to operate but also cost-effective, being supplied at half the price of SS wire healds. Mr. Balar highlights that the entire Waterjet looms industry in Surat now relies on these plastic heald wires.
Meeting Industry Needs
Emmtek Machines produces 40 percent of the consumable spares used in Waterjet looms, with their parts fitting any make or model of these looms. Mr. Balar notes, “Our parts are designed to have a longer lifespan than those imported from China, yet we offer them at competitive prices.” Emmtek’s commitment to quality is evident in their production of shedding pins from SS, which last three to four times longer than the MS pins imported from China.
Emmtek Machines stands out for its dedicated R&D and testing facilities. Unlike other Indian manufacturers, Emmtek designs, develops, and tests all spares in their own weaving unit before commercial production. This rigorous process ensures that their products meet the highest standards of quality and durability.
Transition to Local Manufacturing
Mr. Balar, originally a weaver with 450 machines, observed the challenges faced by weavers in sourcing spare parts. This led him to enter the spare parts import business in 2009 and later, in 2010, bulk import of Chinese Waterjet weaving machines.
Partnership with DRD Weaving Brand
In April 2024, Emmtek began importing Waterjet machines from DRD Weaving Brand, one of China’s top three weaving machine manufacturers. Mr. Balar emphasizes, “DRD Waterjet looms are user-friendly, easy to set up, and known for their longevity and efficiency. These looms have a lifespan of 15 years if properly maintained.”
Emmtek Machines has successfully turned a global crisis into an opportunity for innovation and growth. By shifting from import reliance to local manufacturing, they have set new standards in the weaving machine spares industry. With their commitment to quality, continuous innovation, and robust support system, Emmtek Machines is poised to lead the way in the Indian textile industry, ensuring reliability and excellence in every product they produce.
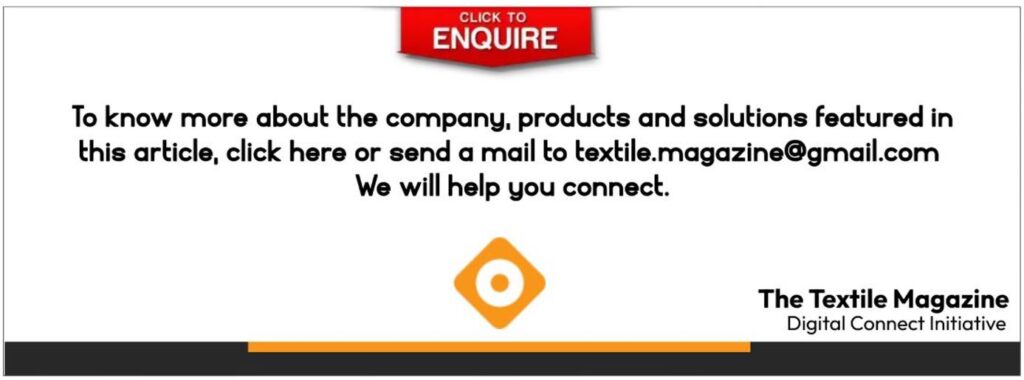