“The world faces an invisible crisis of water quality that is eliminating one-third of potential economic growth in heavily polluted areas and threatening human and environmental wellbeing”, according to a World Bank report released in August 2019.
And the situation hasn’t changed much with the beginning of 2021.
The pandemic has definitely changed the way the world operates while consumers are getting more conscious towards the environment than ever before. Sustainability has become a serious emerging trend focusing on the concept of ‘circularity’ and the way goods are produced – more sustainably. A McKinsey survey suggested that 66% of U.S. consumers now consider sustainability when making a purchase, with younger generations increasingly willing to pay more for products which have a proven minimized negative environmental impact leading to usage of sustainable materials, processes and transparency in the value chain.
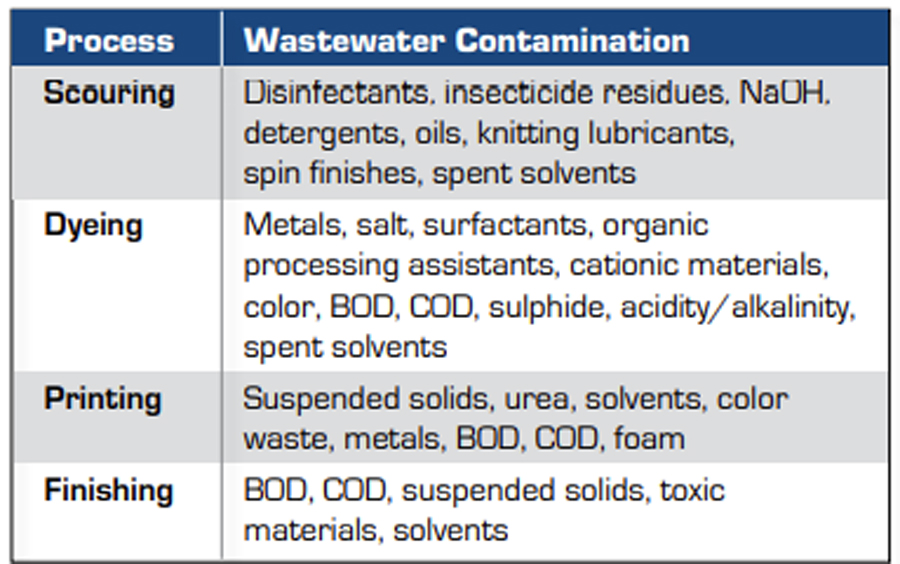
The fashion & textile industry is among the major polluter of water at various stages of its value chain – growing cotton in the fields to its processing, releasing a mix of toxic chemicals and micro-plastics during home laundering of clothes. In 2015 alone, the sector used 79 billion cubic metres of water as per the estimates.
Leading fashion brands are setting up goals to source products only from units which have zero liquid discharge facilities and have adopted new technologies to reduce water consumption during the process.
Water is majorly consumed and contaminated during the processing stage of textile materials including scouring, dyeing, printing and finishing which varies with textile substrate and end product requirements.
The entire textile industry including suppliers of technology and chemicals are incessantly working together to reduce water consumption during textile processes. Among these, waterless dyeing, digital printing, etc. have already been commercialised, however with slower adoption rate due to high investment and running costs.
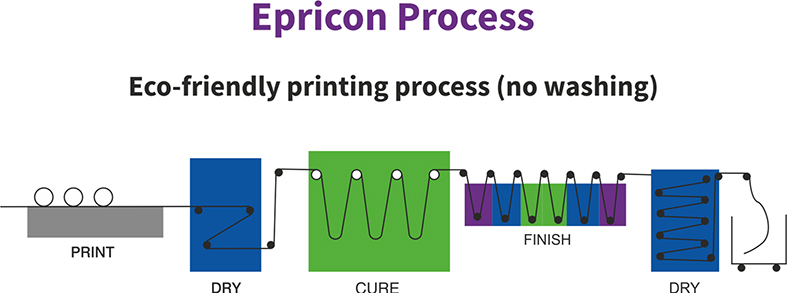
The textile printing industry majorly comprises of conventional processes while digital printing has less than 10% share but growing fast. The printing effects on fabrics are largely achieved through conventional printing processes of reactive, vat, disperse and pigment based on textile substrate. However, these processes particularly used in reactive, disperse and vat, require washing post printing to remove unfixed dyes generating effluent to be discharged for mandatory treatment. Besides this, it consumes high amount of energy and steam during dye-fixation process.
Comparatively pigment printing is an easier process, but has limitations in terms of colour depth, feel and fastness when compared to reactive, vat and disperse prints. Due to these limitations it was never considered as a first choice prints for the up market.
ERPICON – Eco-friendly printing solution
Zydex Industries, a speciality chemical manufacturer, has come up with an innovative sustainable printing solution based on next generation polymer. Continuing with its vision to innovate for a sustainable world, Zydex Industries has introduced EPRICON, an eco-friendly textile printing solution and an alternate to traditional reactive, vat and disperse printing, saving water, energy and process time while keeping the desired depth, brilliancy, feel and fastness intact. The major features are explained below:
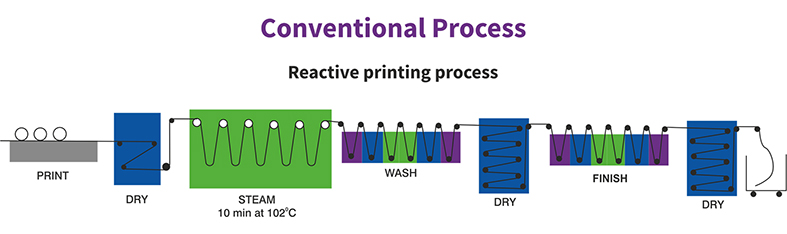
Eco-friendly sustainable process
The GOTS and ZDHC certified package – Epricon is a direct print and dry technique. This eliminates washing and steaming processes and the effluent treatment hassles associated with reactive and disperse printing.
Higher productivity
Epricon is a simple print, dry and cure process, eliminates steaming and washing processes resulting in more productivity. The drying process is also shorter due thin layer of deposition.
Reduced rejection & shorter lead time
Epricon printed fabrics are not prone to colour variation post curing unlike in reactive printing where shade and toner changes are usually observed post printing processes (washing & drying), leading to higher fabric wastages. This eventually results in reduced rejections, faster deliveries and higher customer satisfaction.
Sharper digital like printing
The package is designed to run with higher mesh rotary screens and allows to produce finer designs and sharper prints similar to digital prints but at much reduced cost.
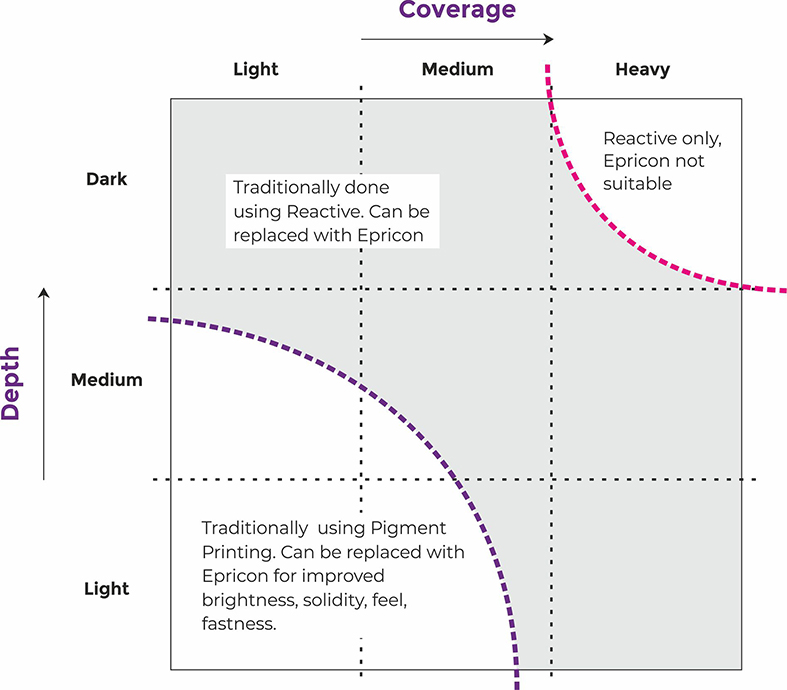
Higher brilliancy
Epricon with the combination of nano-technology chemistry, surface active agents and cross-linking polymers produces brilliant colours and clean prints when compared to conventional prints.
However, it has some limitations which are illustrated in the below graph. Epricon performance is exceptionally good in the areas highlighted in grey and are traditionally printed with reactive, except in the top right corner area representing high depth and high coverage prints.
Zydex is a specialty chemical company with the purpose of innovating to create a sustainable world through conservation of resources. For more information, please write to amirsheikh@zydexindustries.com or log in to www.zydexindustries.com