Taking strong steps towards growth in export markets with its rich sewing and embroidery thread product portfolio, Durak Tekstil supports the growth of the Turkish textile industry with the added value it creates. Durak Tekstil has a monthly production capacity of 250 tons. The company brings the sector together with new products through R&D.
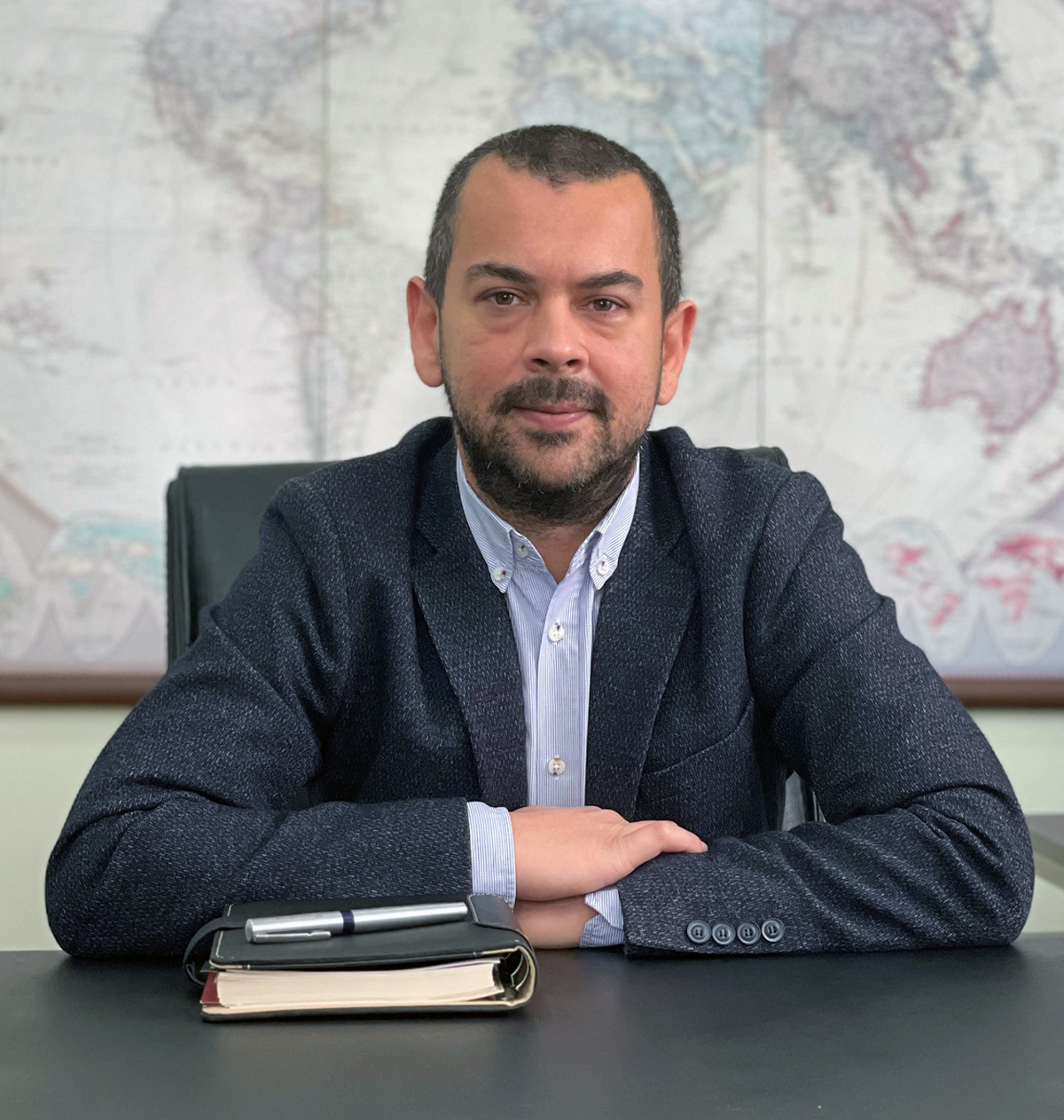
Turkey’s leading manufacturer of industrial sewing and embroidery thread, Durak Tekstil continue to provide added value to the Turkish textile sector with nearly 50 years of industry experience and innovative manufacturing principles. The company meets the high quality and qualified thread demand of the global textile industry with its continuous innovation concept and has managed to grow both itself and the Turkish textile industry with its investments. Focusing on threads with improved technical and application properties, Durak Tekstil has become one of the demanded brands in the global market with their solutions.
Durak Tekstil makes a difference by investing in innovation ever since 1972 as Turkey’s first manufacturer of polyester embroidery thread. The company grows every year with its strong vision, solid production, and sales strategy, and today exports the majority of its production to more than 70 countries spread over 5 continents. Durak Tekstil Board Member and Marketing Manager Yiğit Durak said that this is the result of a successfully managed process. Noting that Durak Tekstil has focused on innovations since the day it was founded, Yiğit Durak provided information about the company’s development and innovative work.
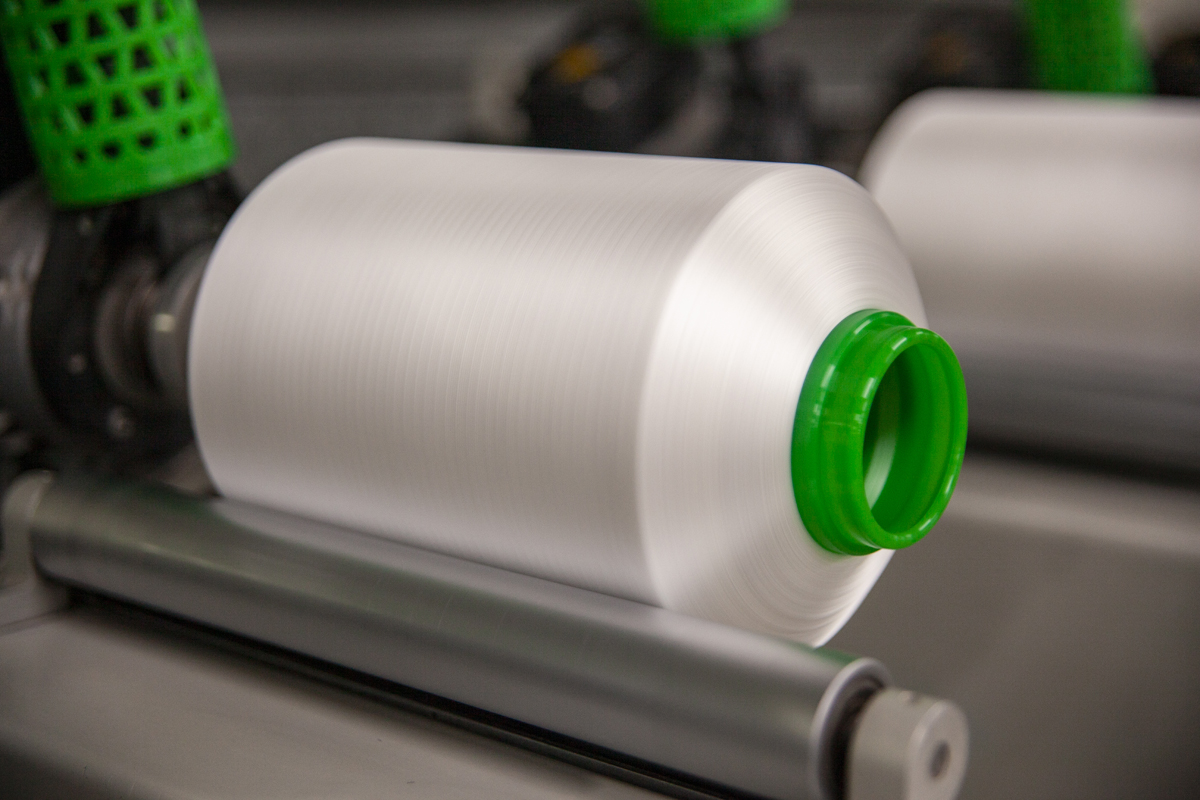
Saying that Durak Tekstil is working nowadays with a monthly average of 250 tons of production capacity at production facilities in Bursa and China, Yiğit Durak announced that they have a sales network spread around Turkey’s 81 provinces as well as, sales offices in Istanbul, Austria and Poland and more than 25 network of distributors. Yiğit Durak stated the following: “The production process, which starts with the supply of raw materials, is carried out by meeting 100% quality control and product safety criteria. The raw material we supply is carefully evaluated by our team and it is reported whether it meets the criteria. Approved raw materials are allowed into our production process. In addition, our POY facility also gives us confidence in raw materials. The folding, twisting, dyeing, and finishing processes of these raw materials are carried out in our facility with new technology machines. In the final stage, the threads we produce are winded on plastic cones and packaged for use in machines. With more than 350 employees, we continue to work with great devotion so that our products reach more than 70 countries”.
Continuing its investment strategy in 2020, when the pandemic was experienced with all its intensity, Durak Tekstil updated its machinery. Yiğit Durak stated that thanks to this investment, the production capacity increased by approximately 50% and that they reached the opportunity to provide better delivery times to the customers.
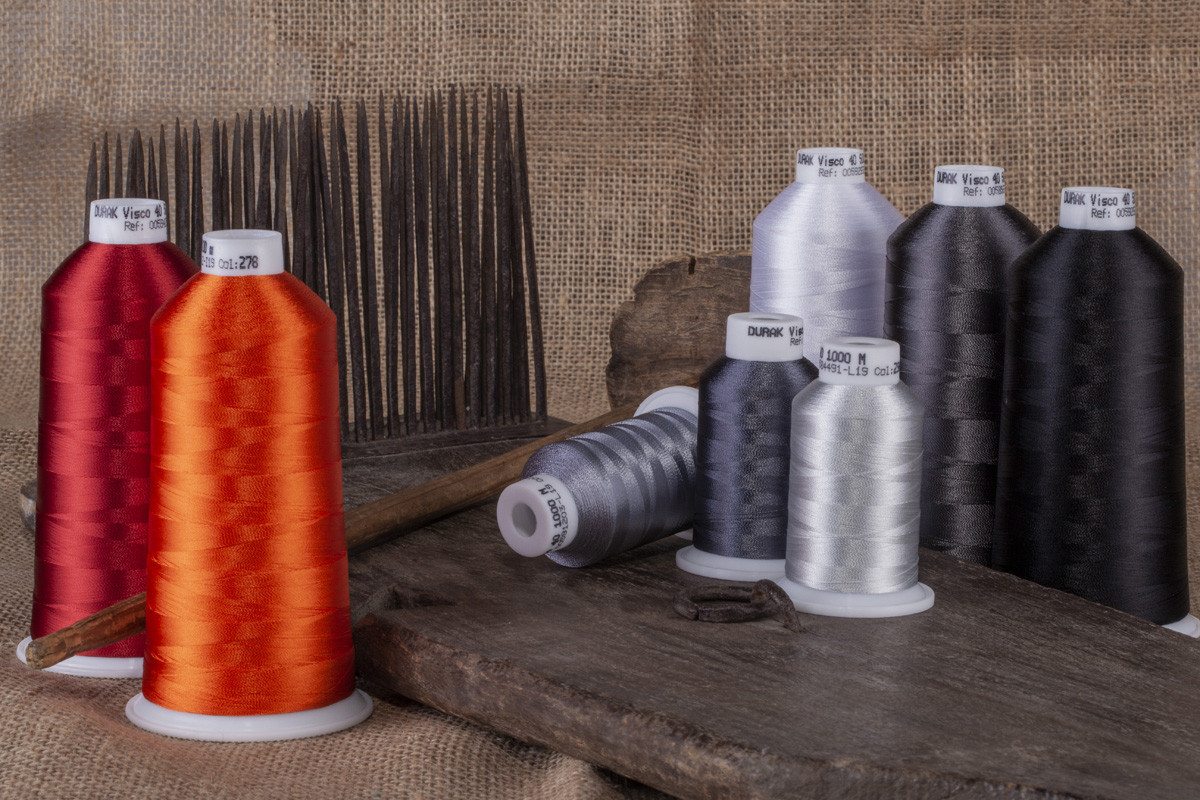
POY investment increased production flexibility of Durak Tekstil
One of the most important milestones in the growth process of Durak Tekstil is the POY (filament) facility established in the 90’s. Saying that they got rid of dependency on raw material suppliers with the POY investment, Yiğit Durak continued his words as follows: “At that time, supply networks were not that advanced and there was a serious dependence on suppliers in terms of production. Periodically experienced raw material supply difficulties prevented our growth and production targets. The POY facility that we have installed gave us the ability to produce the threads we want by using the raw material we want, while saving us from dependence on raw material suppliers. Especially, we eliminated the issues that can be encountered in fine thread supply. With the POY investment, we have turned an important bend on the road to growth”.
Durak Tekstil is also one of the first textile companies to run its own R&D department. Yiğit Durak said: “We are always proud of being an innovative company” and emphasized that the development and improvement of innovative products is in the company culture. Stating that the R&D department also functions as a ‘business technical library’, Mr. Durak explained that they obtained great benefits from the R&D department in the processes of new product development and certification of innovations. Noting that 19 of their R&D projects have received state support so far, Mr. Durak said that they both closely follow the developments in the global textile machinery market and cooperate closely with universities. Mr. Durak: “For example, we follow developments in military applications. Especially the demand for products made with technical threads is increasing. Developments in many points from products that change colour with heat to products suitable for filtration systems, from the food to the health sector inspire our R&D studies. We have even achieved great success in working with aramid fibres”.
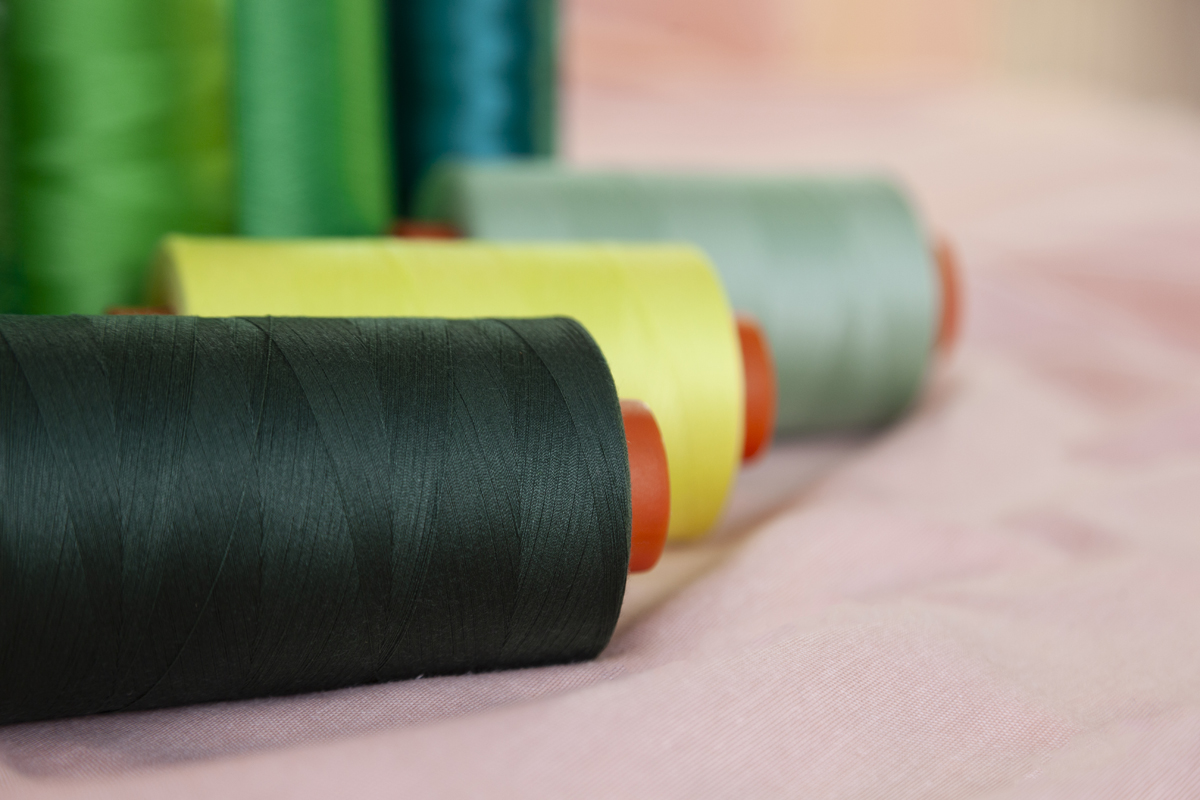
The share of value-added products in the portfolio is increasing
Durak Tekstil, having a wide product portfolio in the field of sewing and embroidery threads, continues to develop special threads that meet customer requests. The main market for sewing and embroidery threads is the ready-to-wear and apparel industry. However, especially the bed and furniture industry has shown a rapid development in recent years. Yiğit Durak said that the share and amount of high value-added products in the portfolio increased: “For instance, our efficiency-enhancing and security products, developed through intense R&D studies, have achieved a rapid rise in the market. These threads can be used in many different application areas with their late incineration and cut resistance properties”.
Noting that they believe that the way to be a successful brand passes through the category of technical products, Yiğit Durak explained their work on this subject as follows: “Almost all of our products are able to apply various technical finishing properties. We give our sewing and embroidery threads features such as water repellence, static electricity conductivity, resistance to UV rays, and special dyeing. In this way, water-proof technical textiles such as air balloons, sails and similar can be produced with our threads. This production contributes not only to us, but also to the Turkish textile industry to be competitive in the global market”.
Yiğit Durak shared that they have innovated products to increase production efficiency in both embroidery and sewing machines. Mr. Durak said that their Duma and Duraless products brought a different perspective to the lower thread system used in sewing machines and hooks: “These products take about 3 times more thread than conventional hooks. In this way, it provides longer working time, extends uninterrupted production time and increases operational efficiency”.
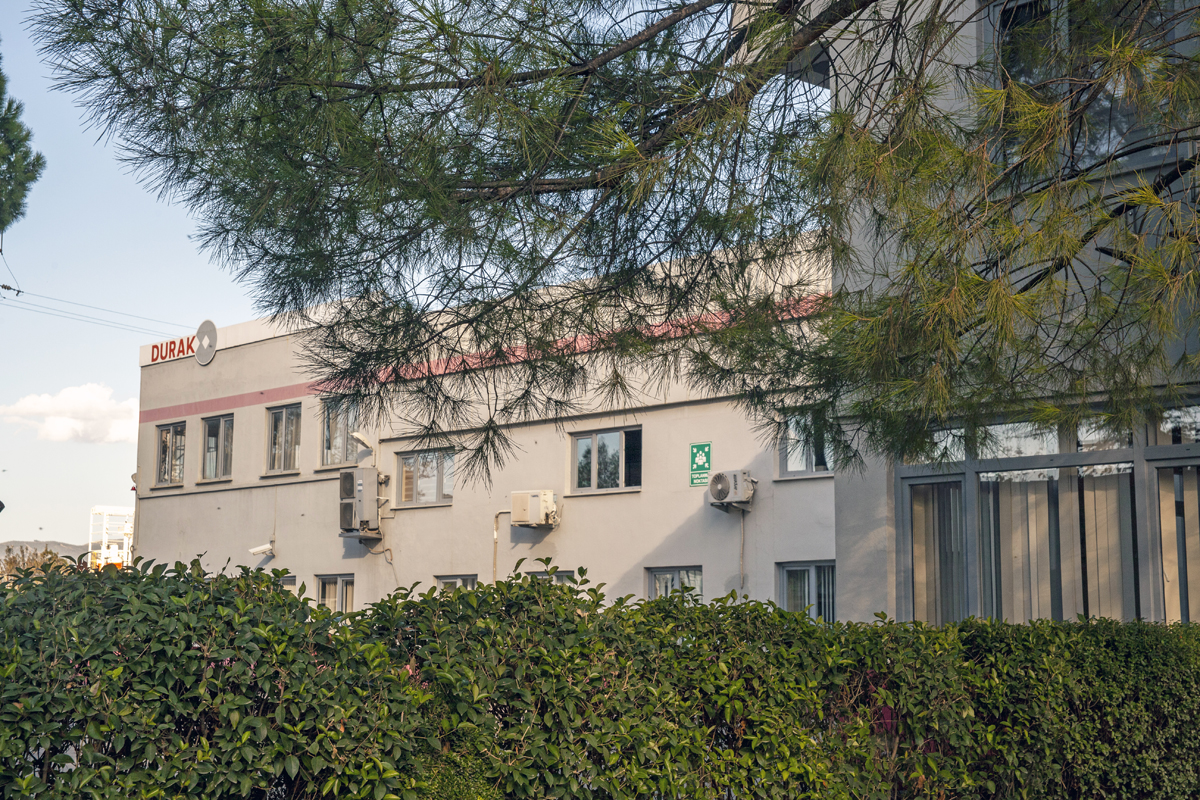
100% renewable energy is used in the Bursa facility
Saying that Durak Tekstil’s efforts on environment and sustainability were going on for a long time, Yiğit Durak noted that they have a comprehensive program. Underlining that they use completely renewable energy in their Bursa facility, Mr. Durak: “In addition, we supply our recycled raw materials from 100% reliable sources, fully certified. We offer our entire polyester and nylon product range with recycled alternatives. This shows the importance we attach to the protection of the environment and resources by using 30 plastic bottles for 1 kg of thread. Our ISO Quality Certificate and the Oeko-Tex certificate prove that we comply with international labour standards”.
Speaking about the short- and medium-term targets, Yiğit Durak concluded his words as follows: “As Durak Tekstil, we aim to increase our share in exports. We plan to increase our domestic market and export sales to 70% in favour of exports in 2021 and to 80% in 2022. In the next 5 years, we aim to grow more in the market and become a globally known and accessible brand”.