In addition to celebrating the company’s own 140th anniversary this year, Monforts can look back on 30 years in successful partnership with Bengal Technology and Engineering in serving the Bangladesh market.
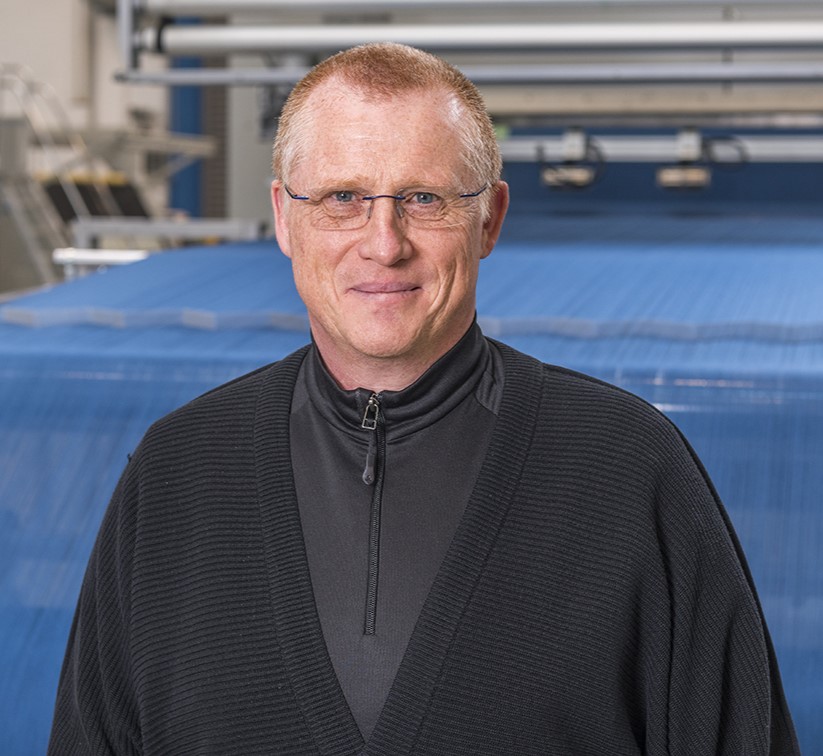
These past three decades have seen the rapid rise of the nation’s textiles and apparel sector from just a handful of manufacturers to over 6,000 factories today, and in particular, the growth of Bangladesh into the world’s second largest exporter of readymade garments (RMGs).
Many of the world’s leading fashion brands have chosen to establish operations in Bangladesh, including Abercrombie & Fitch, Gap, H&M, Levi’s, Puma and Zara, drawn to the country’s efficiencies and highly integrated network of rapidly responding suppliers. The Bangladesh government has now initiated plans to achieve exports of RMGs worth $50 billion by 2025 and approaching $100 billion by 2030.
To realise this, the reinforcement of a textile manufacturing backbone will become increasingly crucial, and Monforts has much to contribute to ensuring the Bangladesh industry continues to grow sustainably.
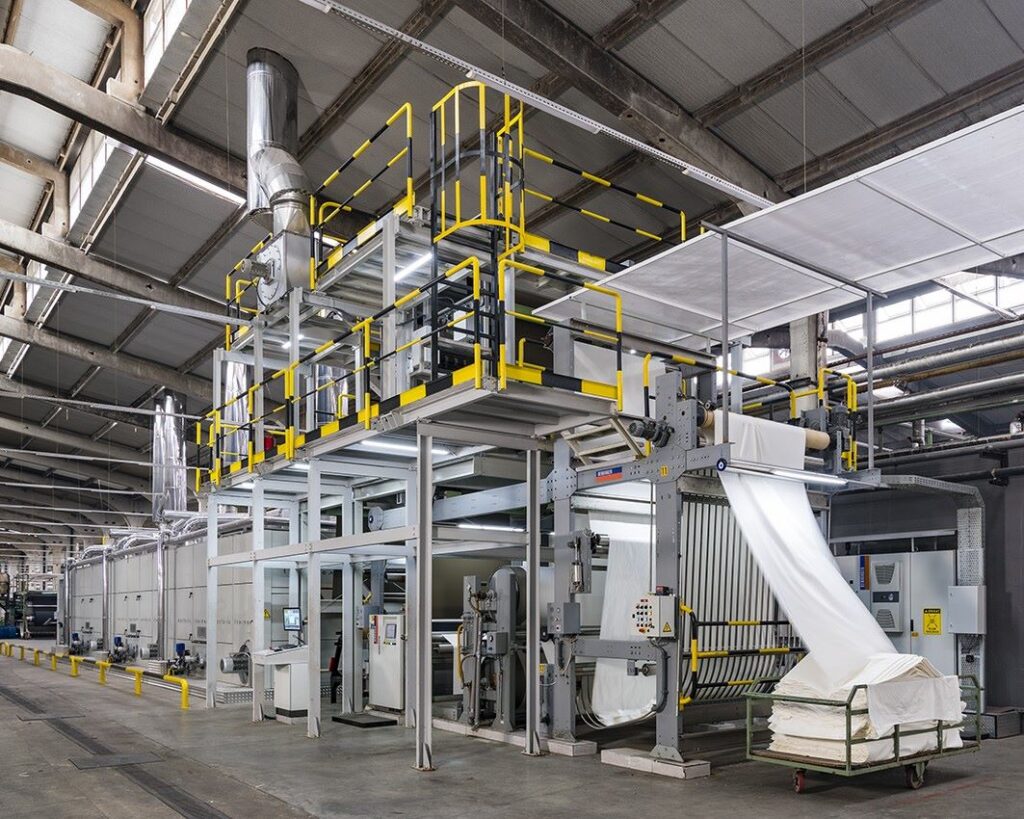
Monforts is 140
“We have always specialised in advanced technology for fabric finishing based on successive industry developments over many decades,” says Monforts Head of Denim Hans Wroblowski. “Our company was founded in 1884 in Mönchengladbach in Germany, where it is still headquartered and our Advanced Technology Centre (ATC) is also situated. All of our machines are manufactured in Europe, at our engineering and fabrication plant in Austria.
“Monforts Montex stenters – for processes such as drying, stretching, heat-setting and coating – are the industry standard for the fabric finishing industry, particularly in the sectors of denim and home textiles, providing a number of advantages in terms of production throughput and especially in energy efficiency and savings. These machines remain unmatched in terms of their robustness and long service life, as well as resource-efficient productivity.
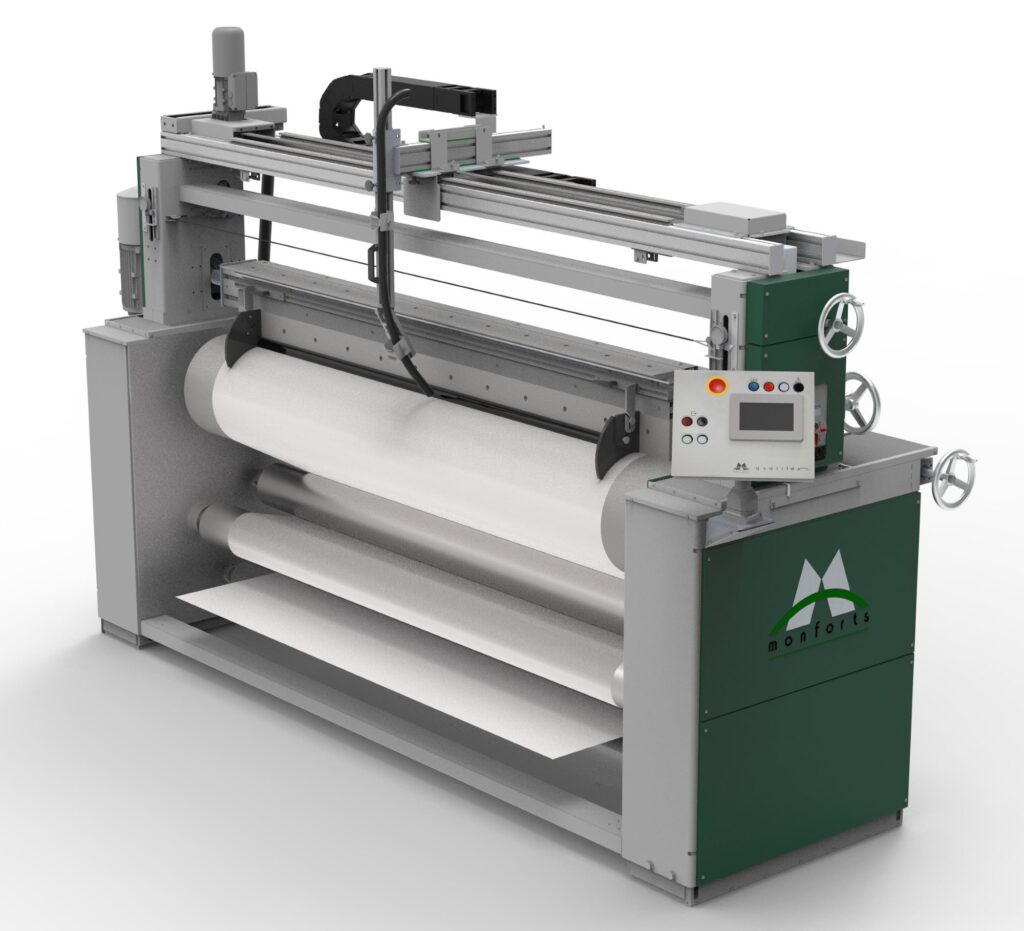
Energy savings
“CO2 footprint is our new responsibility and major challenge and because finishing is a particularly energy-intensive part of the textile production chain, it is exactly where convincing results can be achieved,” he adds. “We have developed a wide range of energy-saving measures and a notable innovation here is our VarioMatex padder, which can be quickly adjusted to suit the fabric being processed. Mechanically squeezing out water with a padder is much more energy efficient than thermal drying, but synthetics and natural fibres, as well as knits and wovens, require differing roll hardnesees for maximum effect. Our EcoApplicator, based on kiss-roll application, is the right choice for functional sportswear.”
For Thermex hotflue and Montex stenter solutions, Monforts has also developed a range of heat recovery and energy optimisation options enabling overall energy savings, up to 40% compared to conventional stenters.
These include the Universal Energy Tower, a free-standing air/air heat exchanger that achieves energy savings of up to 25%. The ECO Booster heat recovery system with integrated automatic cleaning is meanwhile directly integrated into the chamber design of the Montex stenter and enables energy savings of up to 35% depending on the application. One ECO Booster module is sufficient for stenter ranges with up to eight chambers.
Retrofits
All of the above solutions, the VarioMatex, EcoApplicator, ECO Booster and Energy Tower can also be retrofitted to existing ranges without having to invest in a new machine.
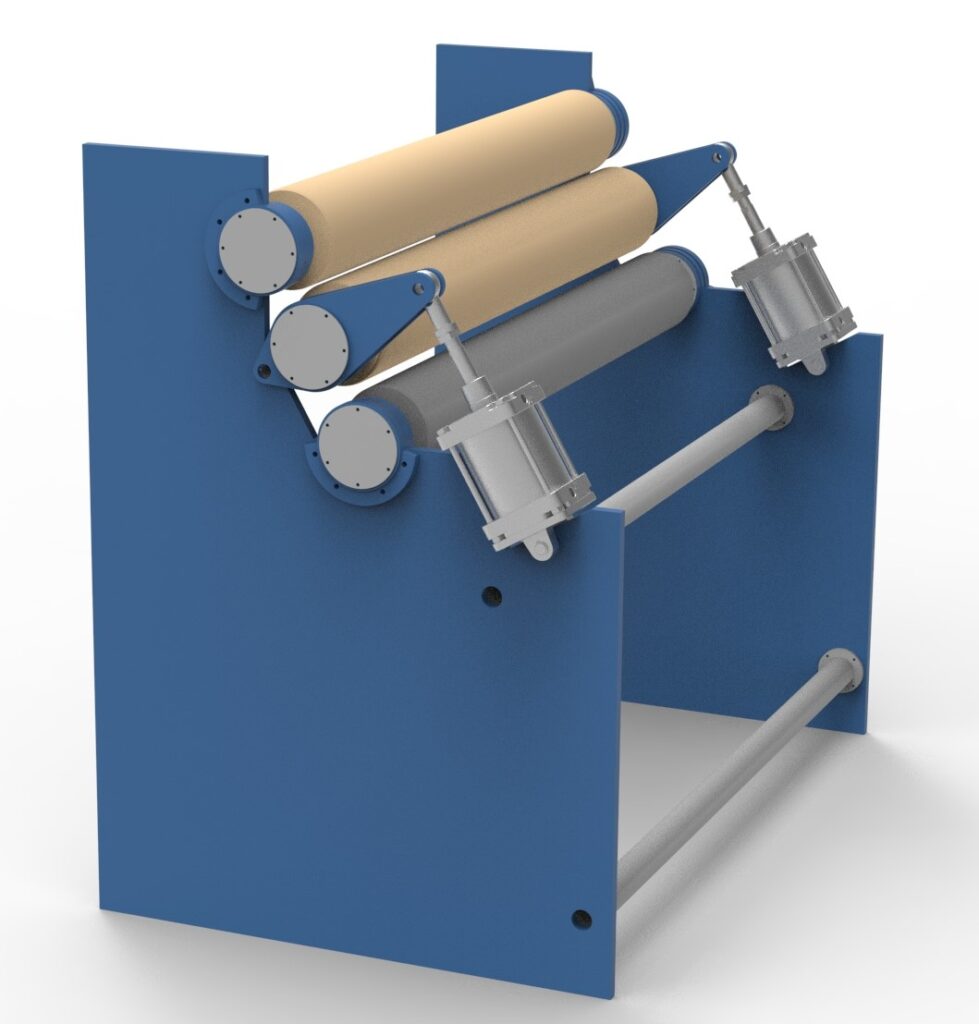
“If anything, today’s high energy prices are only encouraging investment, because for our customers, energy costs can account for up to 70% of production costs, so there is great demand for ways of saving money,” Wroblowski observes. “This also helps in terms of global warming and reducing carbon footprint, of course. We see the energy crisis of the past few years as an opportunity because it is leading to an energy consumption rethink in the textile industry.”
Thermex
Another major area of specialism for Monforts is in denim production and over 900 Monforts Thermex hotflue dyeing systems are now operational in the main textile producing countries, including Bangladesh, with around 150 of them already reaping the benefits of the Econtrol® and Econtrol®T-CA processes.
Econtrol® is a continuous process for the dyeing of woven cotton and cellulosic fabrics in which reactive dyestuffs are fixed into the fabric in a one-step dyeing and drying process with a controlled combination of steam and air. The entire pad-dry process takes just two-to-three minutes at a temperature of between 120-130°C and a relative humidity volume of 25-30%.
The latest innovation for denim manufacturers is the CYD yarn dyeing system which integrates new functions and processes into the weaving preparatory processes – spinning, direct beaming, warping and assembly beaming, followed by sizing and dyeing – in order to increase quality, flexibility, economic viability and productivity.
Qualitex800
With the highly intuitive Qualitex 800 visualization software, all article-specific settings can be stored and the formulations for thousands of treatment processes called up again at any time. Individual operators can also personalise their dashboards with the most important machine functions and process parameters.
Montex®Coat
The Montex®Coat coating unit is one of the latest additions to the Monforts portfolio and the first of these systems in Bangladesh has recently been installed at a plant belonging to leading conglomerate DBL Group.
The Montex®Coat can serve a very diverse number of markets and enables full PVC coatings, pigment dyeing or minimal application surface and low penetration treatments, as well as solvent coatings. Knife coating, roller coating or screen printing can also all be accommodated with this system.
As such, it provides the ultimate in flexibility and the ability to switch quickly from one fabric run to
the next, without compromising on the economical use of energy or raw materials.
As a more specific coater, Monforts has just introduced the coaTTex, which exclusively dedicated to air knife and knife-over-roller coating. For single-sided application with paste or foam, the versatile coaTTex is suitable for both incorporation into existing finishing ranges as well as installation with new Monforts lines, notably the industry-leading Montex stenter systems.
“We are now experiencing high interest in both the Montex®Coat and coaTTex units from the Bangladesh market,” Hans Wroblowski concludes. “We are here to offer full assistance in the supply of advanced dyeing and finishing technology, with full service support, assisted by Bengal Technology and Engineering which has been the perfect partner to us in Bangladesh, in realising over 100 fully integrated line installations over this last thirty years.”
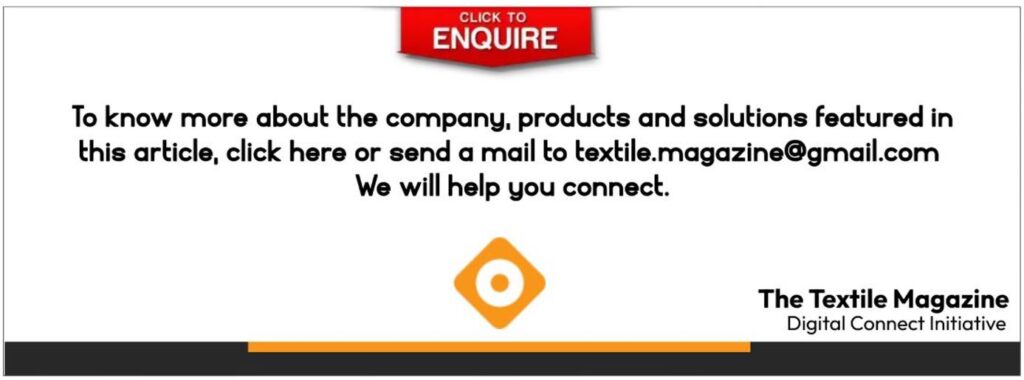