The Lindauer DORNIER GmbH will display at ITMA in Milan a multitude of innovations and new machine concepts for particularly sophisticated fabrics. Under the motto “The Green Machine”, this family enterprise from Lake Constance, which produces all its machines only in Germany, presents comprehensive solutions for sustainable technologies.
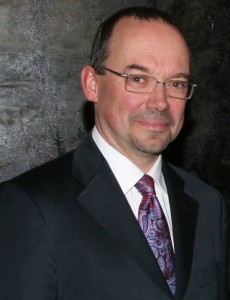
With this guiding principle, DORNIER is not just hinting at the well-known green varnish of the weaving machines but at the “green effect” of the fabrics they produce. These fabrics are vital for many “green technologies” in almost all sectors with products such as filters to purify water or air, airbags and anti-ballistic structures for protection of life and limb, and glass or carbon fibre composites to reduce moving masses and CO2 emissions. In all these sectors the DORNIER “Green Machines” are indispensable for production of high-precision fabrics. Especially in these areas, where the main focus is on quality, DORNIER weaving machines make their mark. This is possible thanks to quality manufacturing, the inventive approach and engineers the culture of closer relations with customers.
In addition to the focus placed on the production of technical textiles to improve sustainability, the German machine manufacturer will also present its newest developments in areas like home textiles, clothing and technical textiles.
The highlight of the 400 m2 DORNIER exhibition stand is a new generation of rapier weaving machines, the P2. The other exhibits are the air-jet weaving machine A1 and two rapier weaving machines P1 in their respectively latest version. At the Stäubli stand an air-jet weaving machine A1 in the Jacquard version and at the Bonas stand a rapier weaving machine P1 with a directly mounted Jacquard system will be displayed.
Referring to the ITMA slogan “Master the Art of Sustainability”, Peter D. Dornier, Chairman of the Executive Board, says: “For our company sustainability has been a philosophy for more than 65 years, not just a fashionable trend. At our site, we respect and support eco-systems and nature. As a family enterprise we cherish values such as confidence and respect. Against the background of claims for more sustainability in textile production, we feel it is important to point out what enormous contribution modern technical textiles do make to the environment. Woven high performance filters, due to their importance for pure air and clean water, cannot be appreciated highly enough. In this aspect, our customers with their DORNIER weaving machines make an excellent contribution to environmental protection. There is much room for improvement as we will show with the help of our ‘Green Machines’ and, above all, with the new rapier weaving machine P2. Together with our customers we want to unlock this potential. Furthermore, DORNIER weaving machines also offer numerous innovations in conventional areas such as home textiles and clothing”.
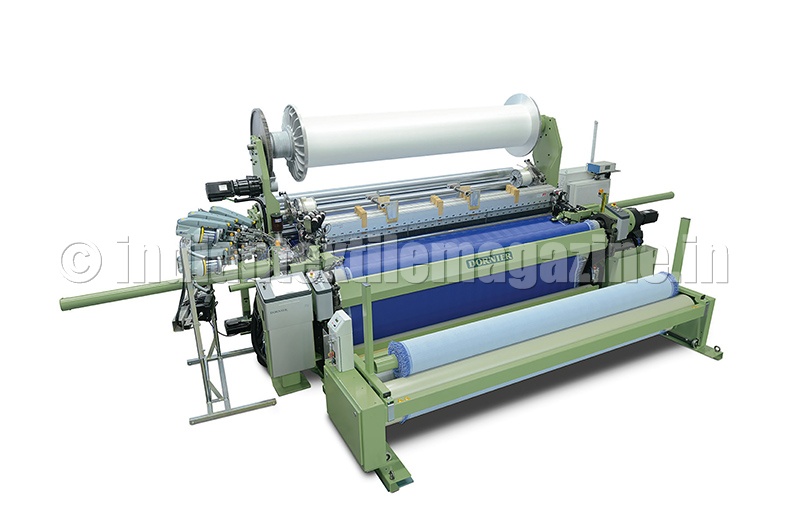
The P2 is a further development of the DORNIER rapier weaving P1 machine with positive controlled center transfer. At the ITMA stand this machine will produce a high density filter fabric in super heavy design with a nominal width of 320 cm and two warp beams. For this width, this kind of fabric could till now be produced with special machines.
The extremely high density is achieved by a specially developed cloth take-up, an absolute uniformity of the filling density and a reed impact force of 5 tons. Such a high reed impact force requires regulation of warp tension with the warp let-off and cloth take-up at a constant value.
In order to master this warp tension, the DORNIER SyncroDrive, with its stable speed, is crucial for shedding. The load peaks in the whole shedding motion are minimized, and the uniform fabric produced has always the same mesh number per cm2. In addition to density, this is another requirement for high quality filter fabric.
This new rapier weaving machine P2 provides for weavers a multitude of new areas of application as well as the chance to open up new markets. As a real “Green Machine” it will prove its special strength and sturdiness in fields that require more efficient, heavier and denser fabrics with highest regularity. This applies, e.g., for filter fabrics for wet, fluid and solid matter filtration or for soot particle separation.
The rapier weaving machine P1 of the latest version produces a sophisticated functional fabric out of different materials, e.g., upholstery fabrics for office chairs. Monofilaments and different flock yarns are used in the filling. The colour of the fabric can be chosen individually according to the customer needs. This challenging elastic material of high quality can only be woven using a very precise warp regulation. The regulation must ensure a predefined tension curve from full to empty warp beam. For this purpose, the rapier weaving machine P1 is equipped with a warp tension measuring system whose sensors control the actuators by means of the warp let-off control, thus ensuring a constant warp tension.
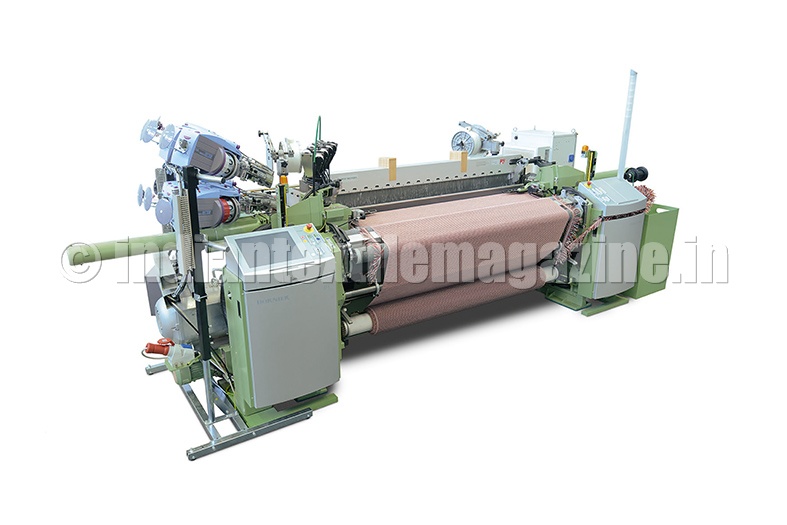
For sophisticated ladies outerwear the rapier weaving machine P1 produces a very exceptional fabric that was recently presented at the Première Vision in Paris. The special feature of this fabric is that it is woven with 16 filling colours and different materials at up to 600 fillings/minute. The basis for weaving such a multi-faceted blended fabric is the well-tried DORNIER filling insertion with positive controlled center transfer ensuring a precise and reliable insertion of different filling yarns. A multitude of in-part patented machine functions and components such as DORNIER MotoLeno for selvedge creation or DORNIER AirGuide for precise rapier guidance in the shed guarantee topmost process reliability.
The air-jet weaving machine A1 of the latest version produces a suit fabric out of worsted yarn as fabricated by the leading textile factories worldwide. Weaving a high-quality fabric out of finest wool yarns with high productivity poses a major challenge. The DORNIER air-jet weaving machine succeeds here with its gentle filling insertion (“senza pelosità”, which means no hairiness of the fabrics) in combination with the automatic filling break repair.
Nowadays, the air-jet weaving machine A1 is used at more than 1,000 picks/minute in industrial applications. The newly developed nozzle concept accelerates the filling thread gently and inserts therefore sensitive yarns even more smoothly.
DORNIER SyncroDrive
At the Bonas stand a DORNIER rapier weaving machine P1 in Jacquard version produces alternately a medium weight carpet fabric and a gobelin. The remarkable thing is the machine itself. Conceptually first created in 2014, this machine will now be presented at ITMA. The Jacquard machine is directly mounted and screw connected to the weaving machine. Here 14,000 hooks are used. A standard feature of this machine is the DORNIER SyncroDrive. By eliminating the cardan shaft, the weaving machine runs more smoothly due to markedly reduced vibrations.
At the Stäubli stand a DORNIER air-jet weaving machine A1 will produce airbag fabrics that is “one piece woven” (OPW). The combination of Jacquard weaving machine and A1 is the optimum solution for this special production technique. Here 12,228 hooks are used. A standard feature of this machine is the DORNIER SyncroDrive. This type of airbag is used for instance for lateral impact protection. Protection of human life is a central aspect of sustainability. A lot more can be done for passenger protection in lower and middle vehicle classes even in Europe and the US. Airbags therefore continue to be a growing market.
The A1 in Jacquard version with its high productivity and extreme reliability offers optimum possibilities. Airbags of top quality are produced in series while meeting the economic and ecological criteria.
The patented DORNIER SyncroDrive is a particularly low maintenance drive, based on servomotors with direct controlling but without a clutch/brake unit. This drive concept permits to change the close of shed timepoint during weaving. The very rigid and low vibration drive concept reduces mechanical load as well as attrition in the whole shedding motion and in this way ensures fewer warp breaks.
Systems equipped with DORNIER SyncroDrive insert the yarns very gently. Service life is prolonged and operating costs reduced. Lower costs, highest functional reliability and an outstanding fabric quality raise weaving with DORNIER SyncroDrive to a high level.
DORNIER Technology Days
Within the framework of the DORNIER Technology Days taking place from October to December in Lindau, customers and interested persons have the opportunity to see weaving machines and innovative processes at the company factory and to discuss customised solutions and specific applications.
On display at the company will be Jacquard weaving line for 3D structures, tape weaving machine, and a tape production line for the application-specific production of thermoplastically fixed or consolidated tapes. The new terry air-jet weaving machine DORNIER ServoTerry and special applications of the DORNIER Open Reed Weave (ORW) technology for the clothing and technical textile sector will be revealed to the public in Lindau for the first time.