While Cubotex has been recently granted the recognition of Export Champions 2022 by Il Sole24 Ore, at the same time our business is still focused and committed to offer dye houses operating in the Italian market best in class machinery solutions, increasing textile dyeing productivity and sustainability. In fact, Cubotex has indeed recently received two new important orders from Italian dye houses – with a third one in its final fulfillment steps – witnessing a clear and strong recovery of the Italian machinery market. This is also due to the Industry 4.0 important fiscal incentives that Italian companies can rely on, getting back a share of 40 to 50% of the overall investment in new and innovative production equipments.
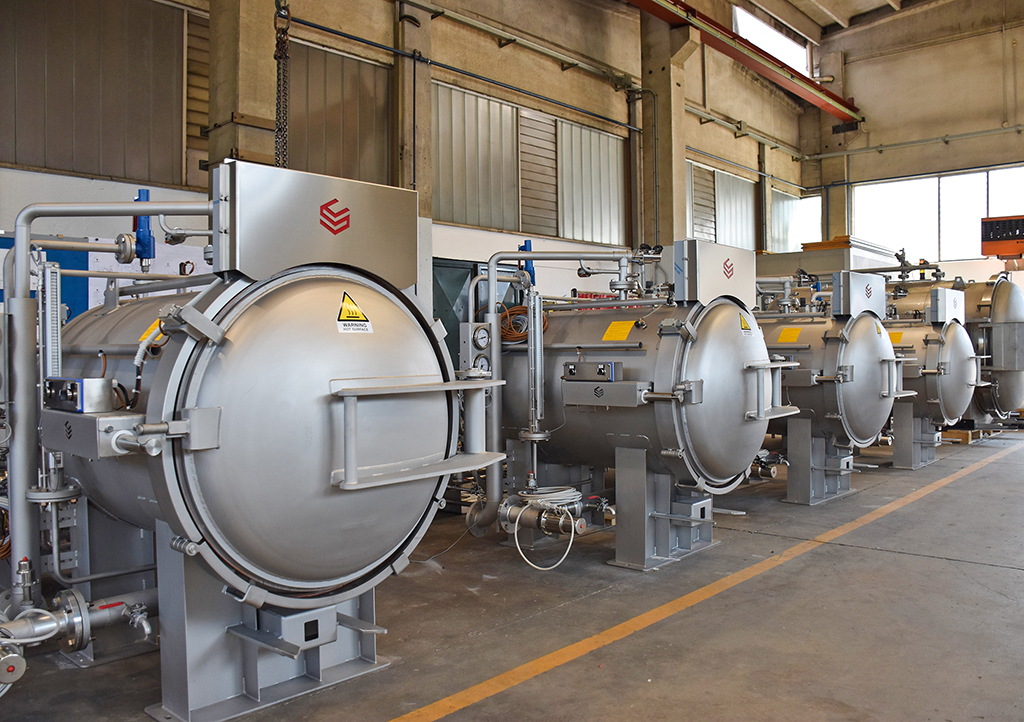
The first order came from a customer based near Mantova willing to extend its activities by entering the market of yarn dyeing, specializing in the dyeing process of synthetic fibres such as polyester and nylon. Based on a yet established partnership with Cubotex since 1993, as the customer already employs Cubotex machines for hosiery dyeing, the company decided to create a new dye house division entering the yarn dyeing market with a further investment for new Cubotex horizontal machines model TRO.
A second important order on the Italian market refers to a new customer for Cubotex, a historical dye house company based in Bergamo that decided to switch from dyeing machines of other manufacturers to Cubotex yarn dyeing solutions, following a recommendation by another Cubotex customer. The company is in fact one of the major commissional dyers in Italy, specialized mainly in cotton dyeing but with significant volumes in other fibres like wool, silk and polyester.
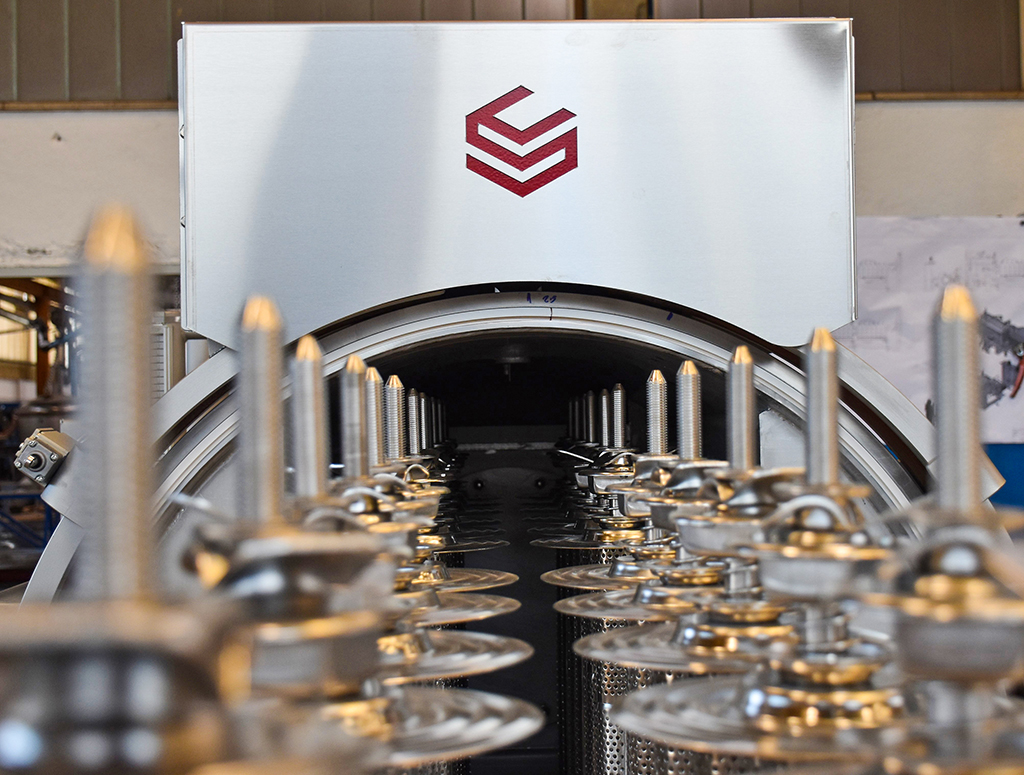
The company, with an average capacity of 10 tons/day, ordered our vertical machines model RVS, trusting Cubotex yarn dyeing machines’ high level of flexibility for the treatment of any kind of textile materials.
The proximity of the customer’s facility gave in addition the opportunity for both Cubotex and the dye house to implement a new research project, aimed to reduce water consumption within the washing cycle of the yarn dyeing process.
The washing phase is in fact the most water consuming part of the dyeing process, aimed to wash the excess dye out of yarn and ensuring that the finished dyed fiber has a solid and durable color retention, resistant to further washing cycles across the product life.
In agreement with the customer, we have therefore installed for free a series of instruments on the newly supplied Cubotex yarn dyeing machines, in order to test an innovative washing system aimed to reduce cycle times and water consumption thanks to a new concept of water circulation.
The core idea is to employ only clean water, avoiding the continued use of dirty water during the washing cycle of the dyed yarn, not only improving the efficiency of the washing process but also reducing production cycle times.
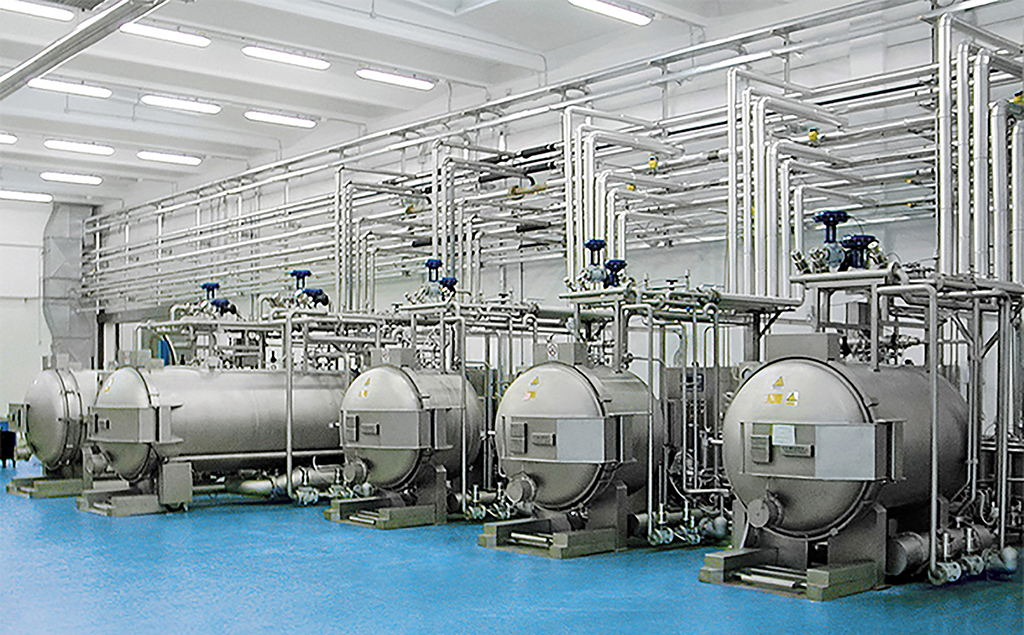
The testing results, obtained through a comparison between traditional washing cycles and the newly conceived one, in the few next weeks will provide us proper insights and parameters to evaluate the savings achieved and/or possible adjustments to investigate and maximize the benefits.
In terms of sustainability and intelligent production, all the Cubotex machines are Industry 4.0 ready, equipped with sensors and devices to capture consumption data of all the utilities required by the dyeing process, water, steam and electricity.
The controller of the machines, equipped with a proprietary Cubotex software, is then able to transfer data to upper level factory management systems such as ERP and MES, providing complete transparency on costs and consumptions of the dyeing process, making the dyeing machine an active part in the path to a more smart and sustainable textile production.