From its modest origins more than three decades ago, KPR Mill has indeed come a long way and is now recognised as a leading manufacturer in the Indian textile industry. In fact, it has further strengthened its portfolio with diversification into other segments, including its most recent foray into garment retail. What applies here are the words of Chinese philosopher Lao Tzu who said, “The journey of a thousand miles begins with a small step”
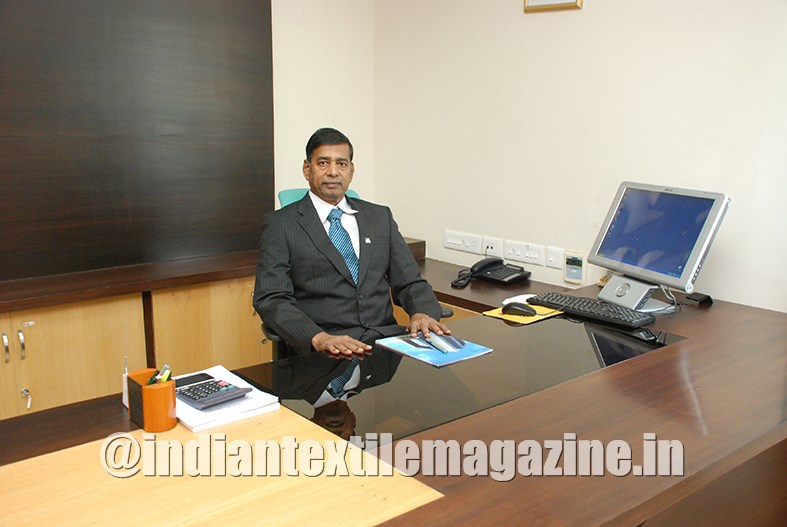
The year was 1984. An enterprising young man in a small town in South India decided to set course on a new journey. He ventured into unchartered waters and set up a small textile company. He was none other than K P Ramasamy, Founder and Chairman of KPR Mill Ltd. Following him, his brothers, K P D Sigamani and P Nataraj joined the venture, and toiled with sweat on their brows and passion in their hearts. Their combined efforts bore fruit. In 1989, the company started manufacturing fashion apparel and carved a niche in the buzzing export market. The company then expanded its frontiers to encompass spinning and processing and set up state-of-the-art manufacturing facilities.
These are located at Coimbatore, Sathyamangalam, Perundurai and Tirupur in Tamil Nadu. In 1995, it set up its first spinning unit at Sathyamangalam with 6,000 spindles to produce cotton hosiery yarn. This was expanded to 30,240 spindles in 2000. The following year it set up a spinning mill at Karumathampatti with 30,240 spindles along with a knitting facility and a green power wind mill for captive use. In 2003, another spinning unit was established at Neelambur with 50,784 spindles along with a knitting facility and a wind mill.
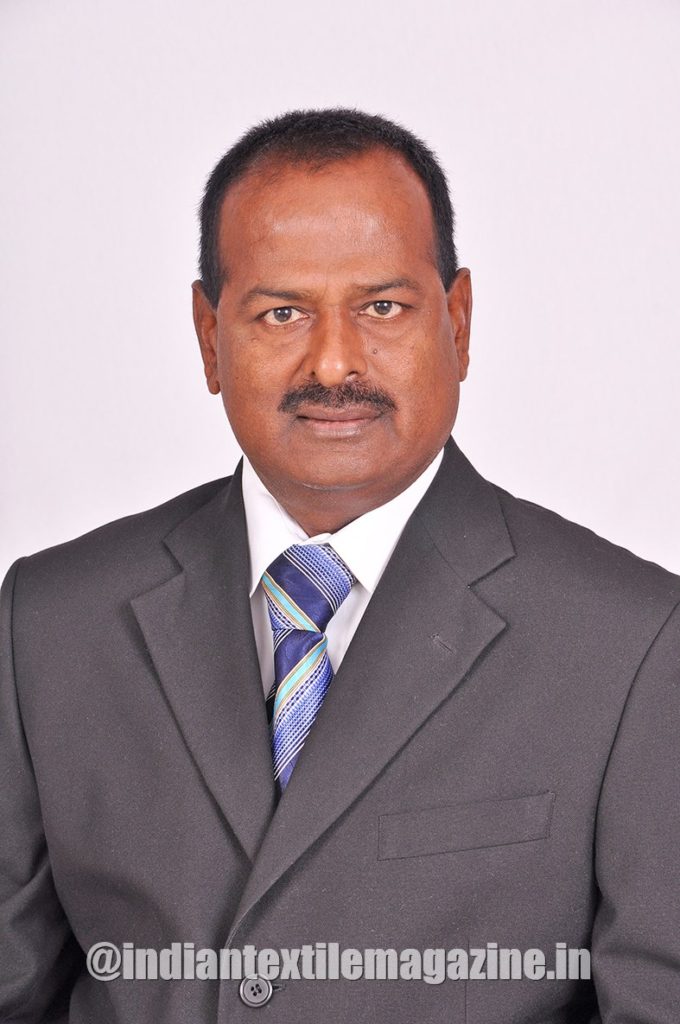
The facility at Arasur was set up in 2005 with a spinning unit of 1,00,800 spindles and a garment manufacturing unit. KPR Mill is now a formidable group of companies that has earned it the title of being one of the top 500 listed corporates while the company’s CEO has been counted among the top 100 corporate leaders of India. Today, KPR Mill manufactures and markets cotton yarn, compact and melange yarn, knitted fabrics, readymade knitted garments and sugar. Meanwhile, wind power coupled with co-gen power boasts of a healthy bottom-line.
The KPR Brotherhood
Chairman K P Ramasamy is a pioneer with more than four decades’ experience in the apparel business. He is a hands-on leader formulating innovative ideas towards HR and new business avenues. He spearheads strategic expansion initiatives with grit and gumption, but addresses employee needs with a personal touch. Managing Director K P D Sigamani is a dynamic entrepreneur with over three decades’ experience in the apparel industry. He currently heads the apparel division of the company and its export business.
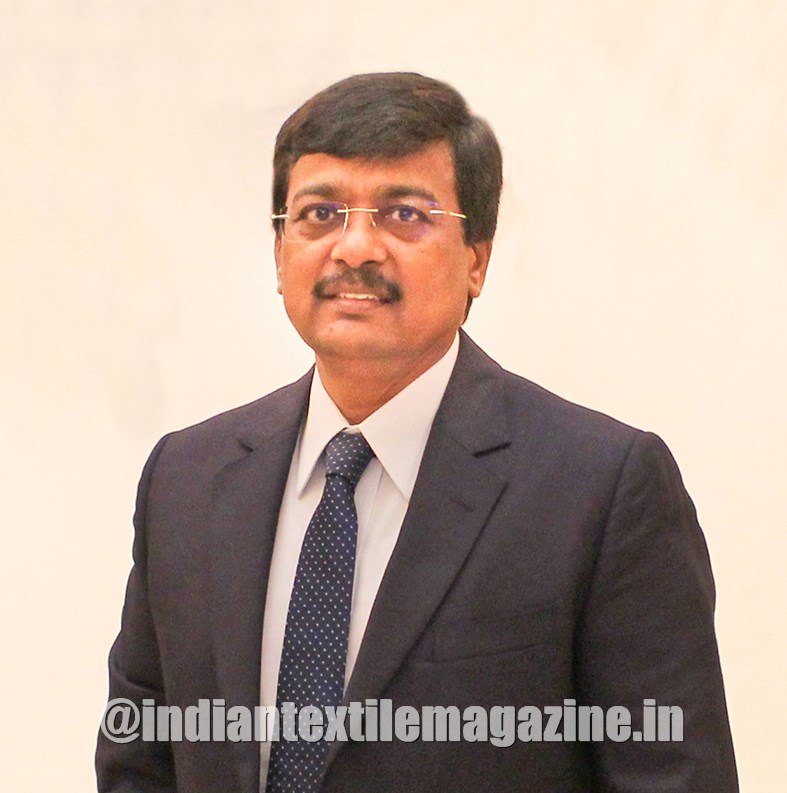
His strong leadership skills and immense focus on customer satisfaction has ensured KPR Mill an enviable position in the apparel exports market. Managing Director P Nataraj, who is also a Chartered Accountant, manages the financial aspects of the business, cotton procurement and yarn marketing. Armed with two decades’ industry experience, strong interpersonal skills and sharp analytical skills, Nataraj has managed to create a strong rapport with clients and has helped the company sustain and succeed in a globally competitive market.
Consistent Growth
KPR Mill has witnessed steady growth in business over the last four decades. The company’s attempt to export knitted garments from Coimbatore has now established KPR Mill as a leading business conglomerate in India, engaged in textiles, sugar, ethanol, automobiles, power generation and education. The brothers’ determination, untiring hard work, perseverance and team efforts have crossed miles to be where they are today. The Indian apparel sector with a history of fine craftsmanship and global appeal has emerged as the most preferred destination for international brands. The strong raw material base and availability of skilled labour carries huge opportunities for Indian textile players. The current market situation and global scenario offers a lot of opportunities favouring the Indian garment sector.
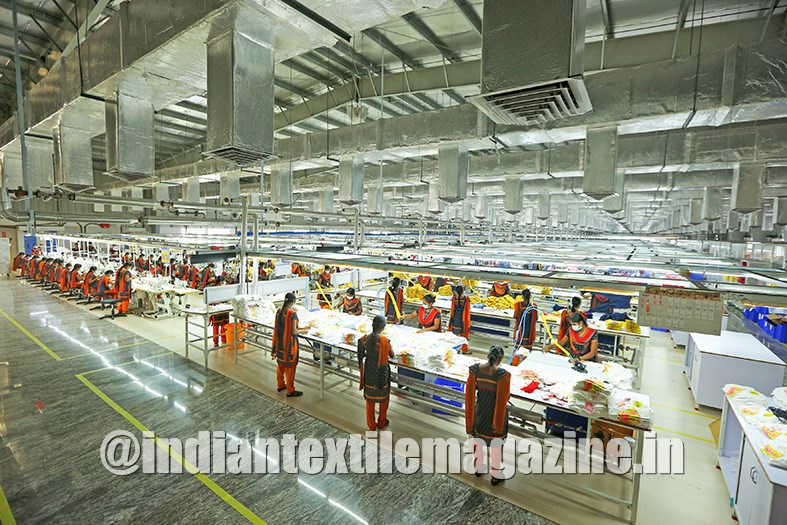
In such a scenario, KPR Mill has demonstrated high level of quality consistency, commitment, best sustainable practices, deployment of green manufacturing practices and the empowerment of rural workforce, more particularly the women fraternity, all of which has helped garner trust and reputation among the international buyers. As the management puts it, the enquiries from the current clientele as well as from the new markets are encouraging and there exist bright prospects to be explored aggressively while focusing on the US and other potential markets.
Driven by Technology
KPR Mill has 12 manufacturing units equipped with advanced technology and over 22,000 dedicated personnel. It has the capacity to produce 1,00,000 MT of yarn per annum, 40,000 MT fabrics per annum and 115 million ready-made knitted apparel per annum, thus making it one of the largest garment producers in India. It also has a garment facility in Ethiopia, not to forget industry-acclaimed ETP embedded fabric processing capacity of 22,000 MT per annum equipped with advanced cold processing technology and sophisticated printing division with the capacity to print 7,500 MT per annum (1,00,000 high-fashion garments per day). It also has 66 wind mills with a total green power generation capacity of 61.92 MW, co-gen cum sugar plant with a capacity of 30 MW and 5,000 TCD and an ethanol plant with 90 KLPD capacity. Recently it has also ventured into the retail sector under its own brand ‘FASO’, producing first-of-its-kind 100% organic cotton men’s wear.
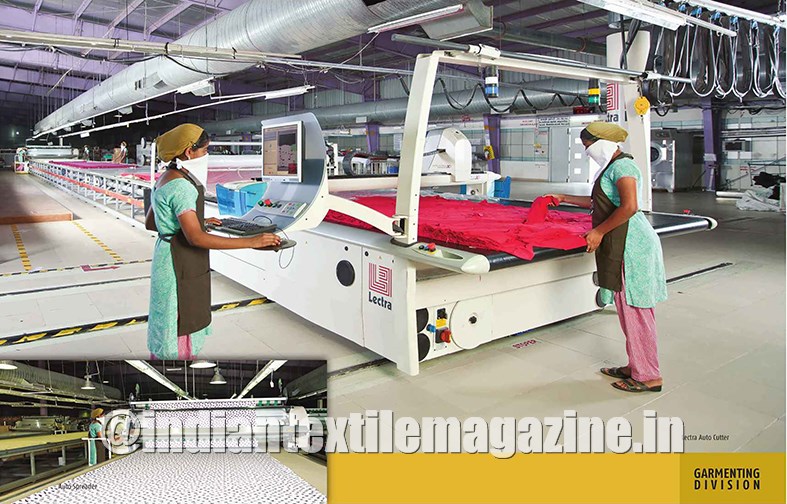
Outstanding Performance
In FY 2019-20, KPR Mill clocked total revenue of Rs 3,389.09 crore with profit after tax (PAT) of Rs 376.68 crore. Despite the ongoing pandemic, KPR Mill has clocked turnover of Rs 952 crore during the second quarter of FY 2020-21. Commenting on this performance, K P Ramaswamy, Chairman, KPR Group, says, “The entire world is passing through an uncertainty it has never seen before due to the pandemic. Like many other sectors of the economy, the textile industry has been hit hard due to closure of business during the lockdown periods. During these challenging times, our priority has been the wellbeing of all of us.”
“Our entire focus has been on supporting the government’s public health initiatives and instructions regarding social distancing. I would like to assure you that we remain operational and continue to serve all our stakeholders. In the face of this pandemic, KPR Mill has implemented systematic procedures to safeguard its employees while continuing to best serve our clients. Our executives have successfully re-positioned to ensure that our work progresses,” he adds.
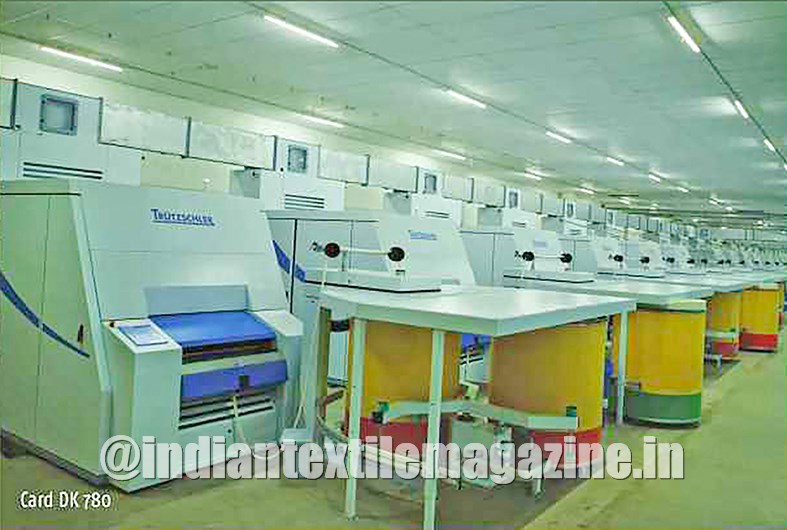
Expansion Plans
In order to cater to the growing market demand and taking a step towards increasing the efforts of tapping potential markets, KPR Mill is investing in garment manufacturing by establishing a new factory with a capacity to manufacture 42 million garments per annum at an estimated project cost of Rs 250 crore. The factory is currently under construction near Coimbatore, within the proximity of existing facilities so as to avail the benefits of integrated activities. As stated earlier, in totality, KPR Mill currently has the capacity to manufacture 1,00,000 MT of cotton yarn, 4,000 MT of viscose yarn and 40,000 MT of fabric along with 22,000 MT of fabric processing capacity, 7,500 MT of fabric printing and 115 million units of garment manufacturing. In FY 2019-20 the company erected the latest technology-aided vortex spinning machine which produces various blends and range of viscose yarns, creating a new wave of world fashion at its Neelambur unit.
It eliminates two major processes, thereby saving labour and power, besides producing an ideal structure of yarn. KPR Mill has also established a new advanced technology knitting factory housing contemporary imported knitting machines of Mayer and Cie at its Karumathampatti unit. The company has also added another most effective and technically advanced effluent treatment system at its processing unit in SIPCOT Perundurai, thus enlarging its wastewater treatment capacity. It has successfully established an ethanol plant with the capacity of 90 KLPD at its sugar factory in Karnataka. The ethanol plant has commenced production and its full-fledged commercial operation is expected during the current financial year.
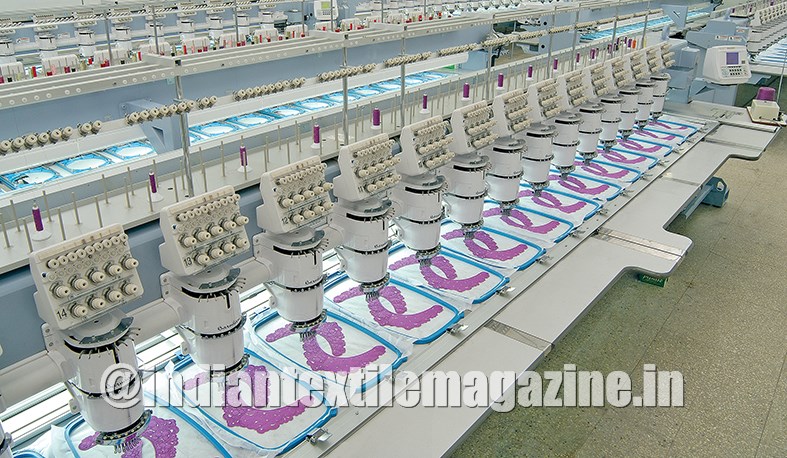
Ethiopia Venture
KPR Mill has established a new plant in Ethiopia which has received approval from leading global buyers. The company is now ramping up its production capacity with the setting up of a garment unit with the production capacity of 10 million garments per annum. Employees were recruited and trained at its unit at Arasur. The required capital equipment and materials were imported and commercial production has already commenced while trial consignments have been shipped. In order to cater to the growing demands of international buyers, KPR Mill established an entity at Singapore, KPR Mill Pte. Limited. Singapore has substantial international brands and retailers well-connected to the international garment industry.
Retail Business: FASO
KPR Mill has introduced first-of-its-kind 100% organic cotton men’s innerwear and athleisure products under its newly launched ‘FASO’ brand, catering to three different premium ranges – comfort, style and supreme. This is in recognition of the fact that the need of the hour is nature-oriented fashion that is toxic-free. FASO as a brand has been curated after doing extensive research on customers’ needs and comfort. FASO innerwear is ‘Italian at heart’ which means slick designs in trending colours and meticulous craftsmanship. FASO offers a collection of innerwear and athleisure wear designed with greater ecological integrity.
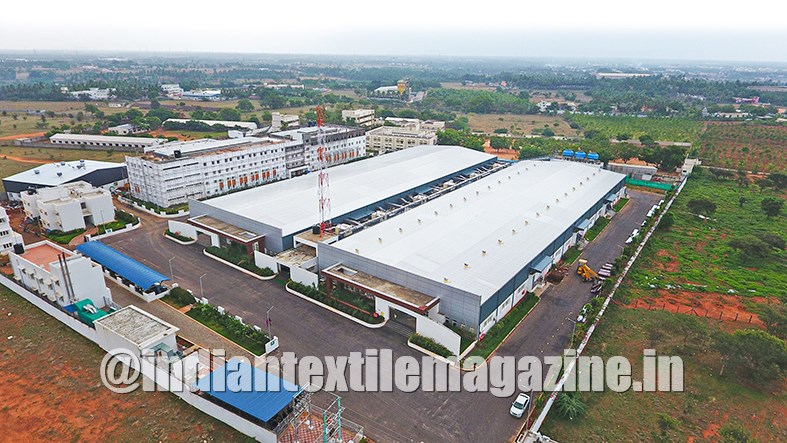
Organic cotton of the highest quality is used in a manner that is good for the environment. In addition to providing a stylish collection with bright trendy colours, the 100% superfine combed organic cotton products offer ultra-soft comfort that naturally makes it very skin-friendly. “Our major strength is the vertically integrated operations where we have end-to-end in-house manufacturing facilities for yarn, fabrics, processing, printing, embroidery and garment. This helps us to keep a check on the quality and enables producing organic cotton products that are skin-friendly and breathable. With these eco-friendly products, KPR Group hopes to make a stride in the retail segment. Our launch in South India has met with success,” the management states.
Human Resources
Safe, healthy and happy workplace creates positive business culture. It drives employee engagement, job satisfaction and staff retention, and in turn defines business success. Good HR practice plays a key role in developing, reinforcing and changing the culture of an organisation. Having recognised the importance of human resources right from the beginning, KPR Mill has been concentrating on adding value to the employees by extending the best facilities for its work force. And in the current scenario of the pandemic, it is the ‘feel at home facilities’ provided by the company that has helped it retain its manpower at a time when the industry witnessed the return of migrated employees in large numbers to their hometowns.
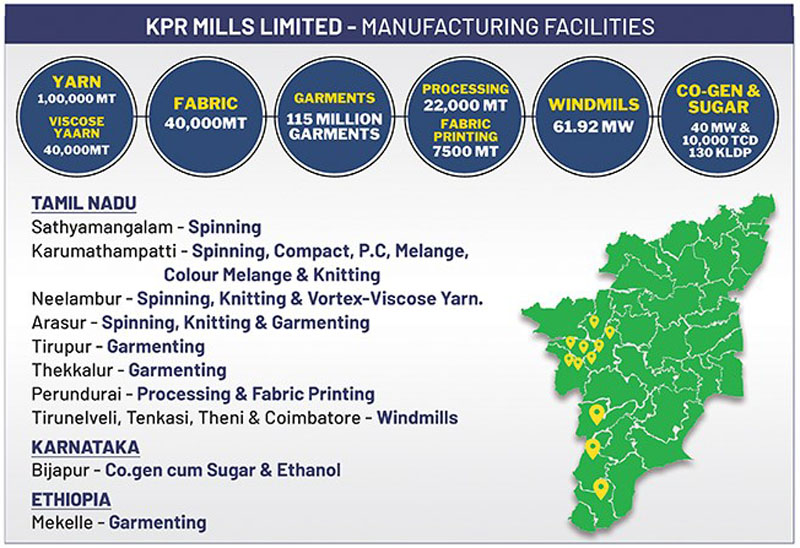
“At KPR Mill, employees chose to stay back on the factory premises where they continued to enjoy comfortable accommodation, nutritious food and recreation and education facilities besides best health and safety measures. Higher education facility, an important aspect of the company’s HR policy, continues to add bright prospects to the employees at large. So far over 27,000 employees of KPR Mill have benefited through higher education. The best educational facilities extended by KPR Mill can be manifested by the employees’ continuous remarkable achievement in government examinations, securing medals, ranks and certifications every year,” the management informs.
“The whole world is battling to curb the impact of the corona virus but all of us should try our best to overcome this challenge in solidarity. We should convert this threat into a new opportunity available to the nation to progress as regards its ‘Make in India’ aspirations and enhance its exports to the world. Business conditions must be conducive to position India as a viable competitive alternative to China which the Indian industry is fully capable of. The Indian textile industry possesses inherent and unique strength such as abundance of raw material, presence of entire value chains, competitive manufacturing costs and availability of skilled manpower,” the management states.
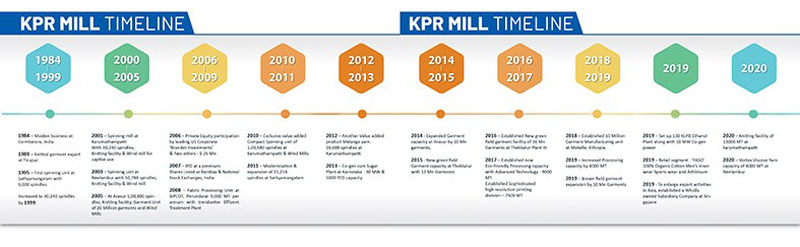
“A large and growing domestic market, higher youth population, rising per capita income, higher disposable incomes and preferences for brands and increase in organised retail landscape and e-commerce are the other contributing factors. Besides, various governmental flagship programs are expected to further drive growth,” the management adds. The success of KPR Mill is an example of a business that started from a humble beginning and eventually grew into a force to be reckoned with. The journey, however, has had its fair share of challenges but has also been one of dedicated and diligent efforts along with employing the right strategies to be able to survive and also grow in as competitive a sector as textiles.
—
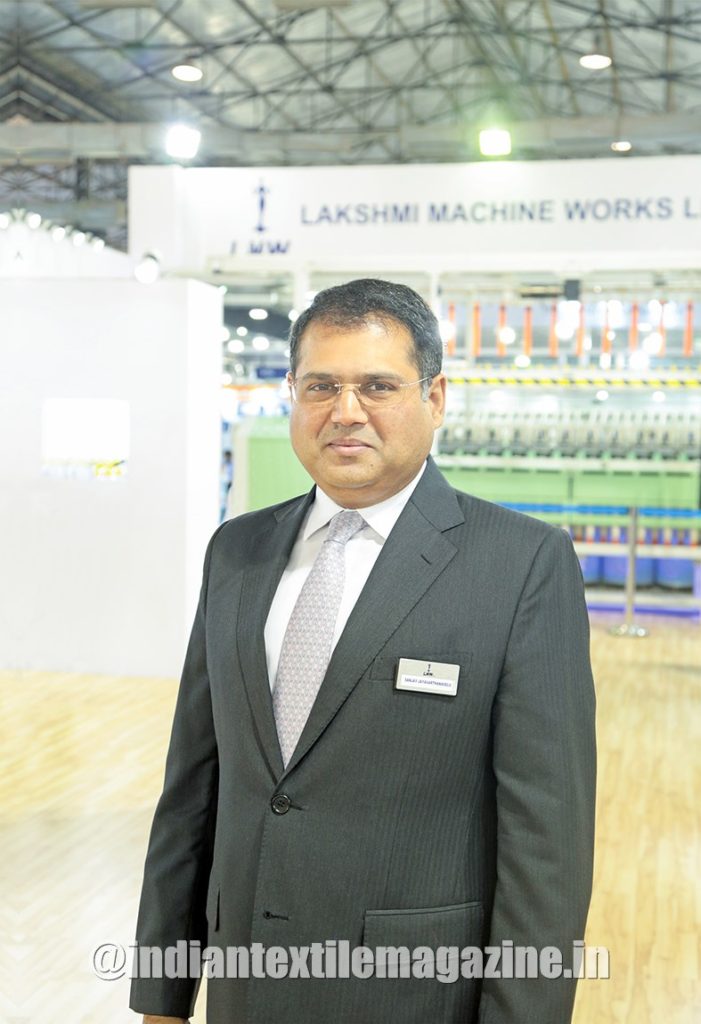
LMW draws immense pleasure in continuing a long-term association with KPR Group for over three decades. The group is one of the largest vertically integrated business conglomerates globally and is a frontrunner in quality and operational excellence. Under the dynamic leadership of Chairman K P Ramasamy and the Board of Directors the group has grown from strength to strength and has set many standards for the textile industry. LMW through supply of advanced technological and innovative products has been a strategic partner in KPR Group’s journey of excellence. We congratulate KPR Group and wish it the very best in their journey. We look forward to the company expanding their business activities.
– Sanjay Jayavarthanavelu, Chairman and Managing Director, LMW
—
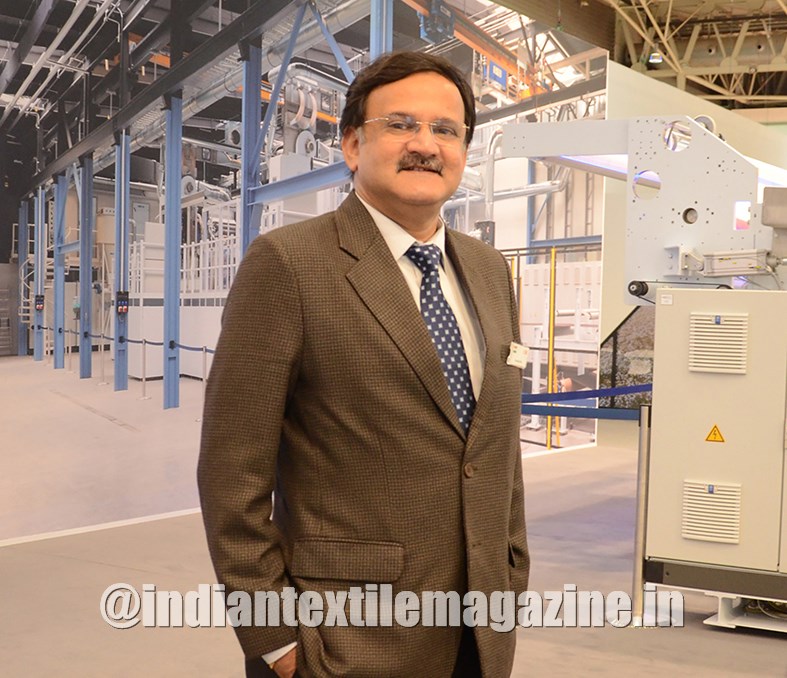
KPR Mill is one of the largest vertically integrated manufacturers of high-quality yarn, fabrics and garments. It also is a large manufacturer and exporter of knit garments in India and has been equally successful in its foray into retail with its own FASO brand of innerwear and athleisure wear and also has spread its wings to Ethiopia with its first international operation. We, at A.T.E. Enterprises, are very closely associated with the KPR Group since more than a decade as a technology supplier. We have so far supplied 20 blow room lines, automatic blending installations and 240 high-production cards from Truetzschler Germany and India apart from 64 speed frames from Zinser India.
A.T.E. Enterprises has also participated in their knit processing project by supplying rotary printing machine from Zimmer (Austria), slitting machine from Corino (Italy) and fully automated dyes and chemicals dispensing system from Color Service (Italy). We are extremely proud to be a technology partner to KPR Group for a long time. KPR Mill always invests in the latest and best technology without any compromise. It has one of the best manufacturing facilities and it maintains a high compliance standard towards quality and housekeeping.
One of the biggest success factors for KPR Group’s strong position is the foresight of its Chairman K P Ramasamy. Today, KPR Group has one of the best facilities and excellent team of technicians on account of which they produce the best quality products on a consistent basis due to which many of the major global brands are their loyal customers. We wish all the best to the management and team of KPR Mill for its future endeavours and look forward to the continuation of an enduring relationship for decades to come.
– G V Aras, Director (Textile Engineering Group), A.T.E Enterprises Ltd.
—
Quality is in their DNA
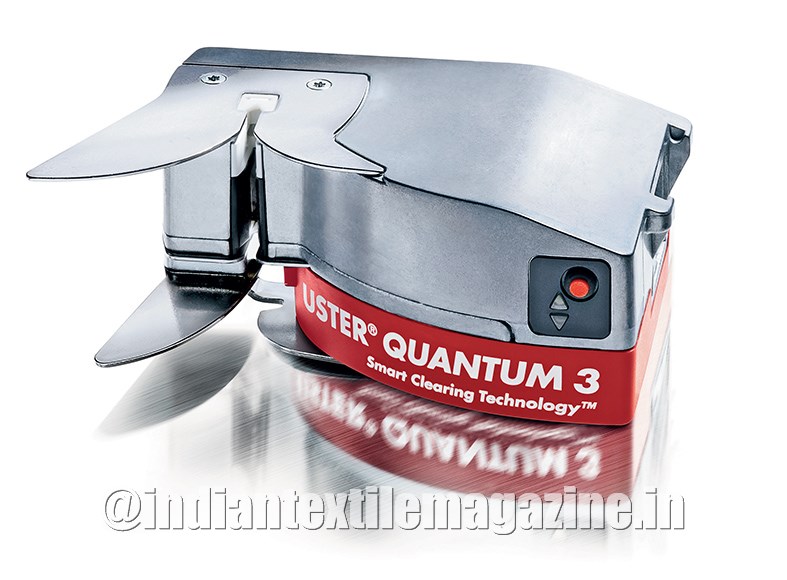
With a focus on innovation, quality and service and by combining latest technology and modernisation, KPR Group is one of the largest conglomerates in the Indian textile industry. With its futuristic thinking and rich experience in the textile industry for many decades, the group has successfully managed to acquire a prominent position under the visionary leadership of Chairman K P Ramaswamy. Uster Technologies is very proud to have had a strong business relationship with KPR Group for more than two decades. With quality as core in their DNA, they have established state-of-the-art quality labs from their emergence, and they have constantly driven their quality-testing efforts by equipping their lab with Uster Technologies’ equipment in every spinning location.
Consistency and quality are the prima facie of KPR Group. With highly set benchmarks, they have continuously strived to meet top-standards, providing quality products to their customers. Uster Technologies takes pride in shouldering this responsibility with USTER®QUANTUM clearers installed in every winding room and USTER®JOSSI VISION SHIELD in blow rooms to deliver the required quality. With various departments like sales, marketing, after-sales support, training and electronic repair station, we are glad to provide comprehensive support to enable KPR Group deliver the right products made with the right quality every time. We thank KPR Group for their continuous patronage of our products. We wish to grow along with KPR Group by supplying quality management solutions.
—
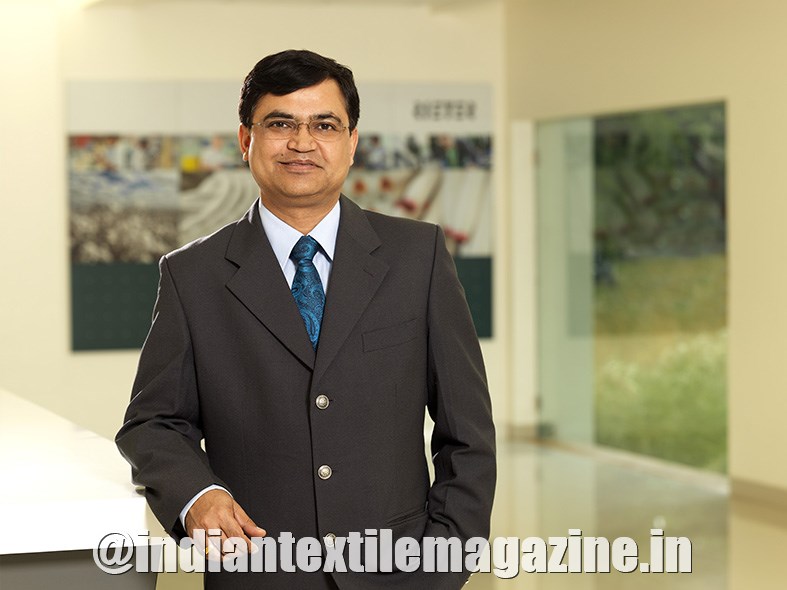
Current challenging times demand textile companies to be highly competitive in order to adapt to the changing manufacturing scenarios in terms of Planning, Efficiency and Sustainability. KPR’s intensive experience over last few decades to overcome these aspects in the textile landscape has proved to be useful in today’s difficult market situations.
It is pride to be in partner with KPR group, one of the benchmarks in the textile sector for their quality, operational efficiency and consistency. Rieter with its wide range of offerings has been a trusted supplier across all our Business Groups – Machines and Systems, After Sales Services and Components for two decades. This association goes back to 2001 with the initial supply of 3 Draw Frames D 30.
KPR entrusted Rieter for the entire range of Fiber preparation machines such as UNIfloc, UNIClean, UNIblend and Card C 70, and remains exclusive supplier for complete Spinning preparation machines like Draw Frames and Combing sets, and in End spinning with 72 Ring Frames equipped with Elite Compacting devices. Rieter After Sales Services with OEM parts ensures the trouble-free performance in sync with Rieter Components which provides key technological parts like Rings, Spindles, Card Clothing and Elite.
Overall, our engagement with KPR ensured the swift results thus strengthening the mutual confidence of being successful as a premium textile supplier.
– Prasanta Deka, Market Head India, Rieter
—
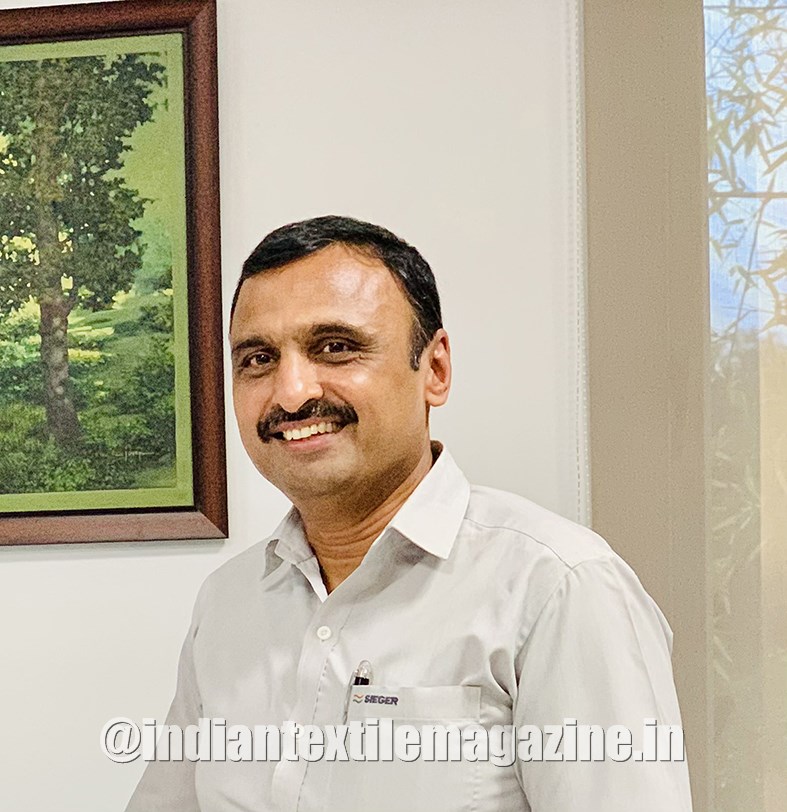
KPR is one of India’s largest integrated textile player who has presence across value chains from fiber to fashion. Having our origins from the same city, it has been a great opportunity to watch them grow and expand across different verticals of the textile industry through uncompromising quality. They have been one of the most dynamic companies that we have been associated with over the last 15 years.
SIEGER has supplied a wide range of machines right from our Yarn Conditioning Plant, Auto-Doffer retrofit for ring frames and many automation solutions for their spinning division to our latest Automatic Fabric Storage and Retrieval Systems for their garment division. It has been a great learning experience for us to be integrated with them at a process level and be a part of their growth.
Under one of the most charismatic leaders in the form of Mr. K.P. Ramasamy, they have truly evolved into a company which has raised the bar of manufacturing excellence and quality across the textile industry. We truly wish the Board of Directors success in all their endeavors and looking forward to a very exciting relationship over decades to come
– G. Radhakrishnan, Managing Director, Sieger Spintech
—
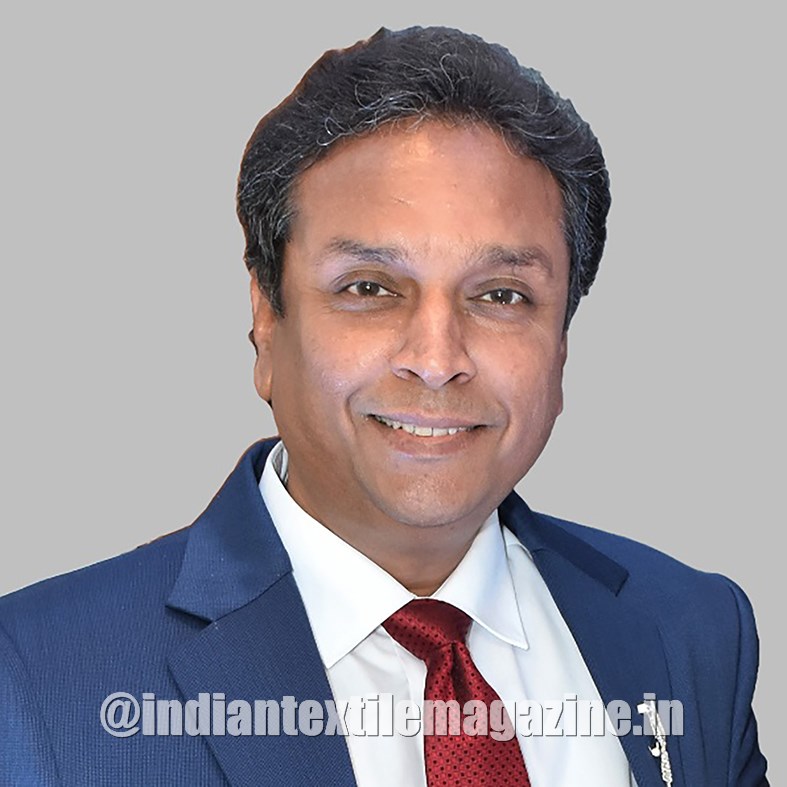
It is our privilege to be associated with the KPR Group since the last more than two decades. Today KPR is one of the largest vertically integrated groups in the textile domain. Their expertise across the textile value chain is quite unparalleled and unique.
Saurer started its business relationship with KPR Group during mid 1990s and we sold our first Autoconer to them in 1997. From a humble spinning capacity in the beginning, the group soon gathered momentum and with continuous focus on the market and expansions in steps of 50,000 to 100,000 spindles, today they stand tall at an overall spinning capacity of 370,000 spindles producing 100,000 metric tonnes of cotton yarn per annum with a count range between 10s – 40s Ne. In all major expansion projects of KPR since 1997, the have opted for our winding models from AC338 up to the current ones in various categories totalling to 9420 drums, thereby reposing their confidence in Saurer as their preferred supplier for the winding machines. Apart from winding, they also have 50 nos. roving machines from us.
The relationship between KPR Group and Saurer is a time tested one of mutual respect and admiration. For any trials that Saurer wishes to undertake, we always turn to KPR where their technical teams support us in all aspects and offer value added inputs aimed towards improving the machines. We wish KPR Group all the very best!
– Vikas Sharan, Director – India Operations, Saurer
—
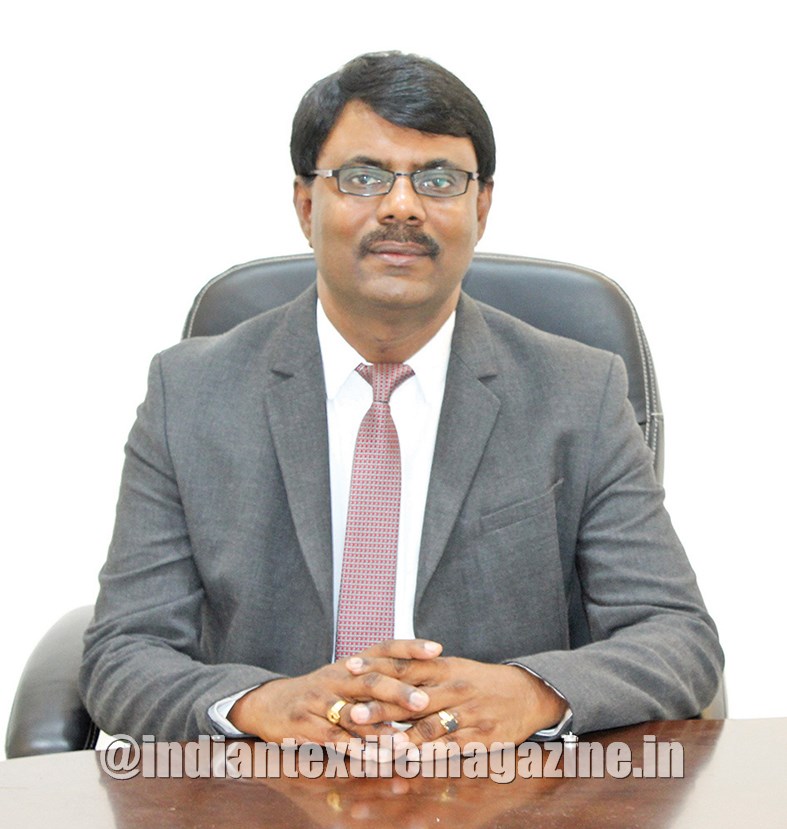
We got an opportunity to present a brief seminar about our products to KPR Group’s technical team in 2014. Before the seminar, the team analysed and compared us with our competitor’s product. Finally, the technical department raised a pattern and gave a sample test on Slub over Slub parameters with SKAAT Slub machine. We took it up as a challenge and satisfied them with amazing results. A technical team from the group visited us and got trained at our customer training centre. After a week’s time, we got an order for one machine. From that moment, our order for machines has been increasing year by year.
We are happy to state here that we have also developed a project on Lycra Colour Slub for their requirement. We are having a very good relationship with their entire team. They provide equal opportunity to all textile machine manufacturers and are open if there is any issue so that we can arrive at a positive solution. We admire the discipline and process followed by the KPR Mill team. We want to cite here a small example: Normally, we send an instruction manual with our machine. After four years, we found that the same instruction manual was pasted on the right side of the machine with a different maintenance person. The highly disciplined approach of their team, from bottom to top, is the same. My best wishes for all their upcoming projects.
– G Radhakrishnan, Managing Director, SKAAT
—
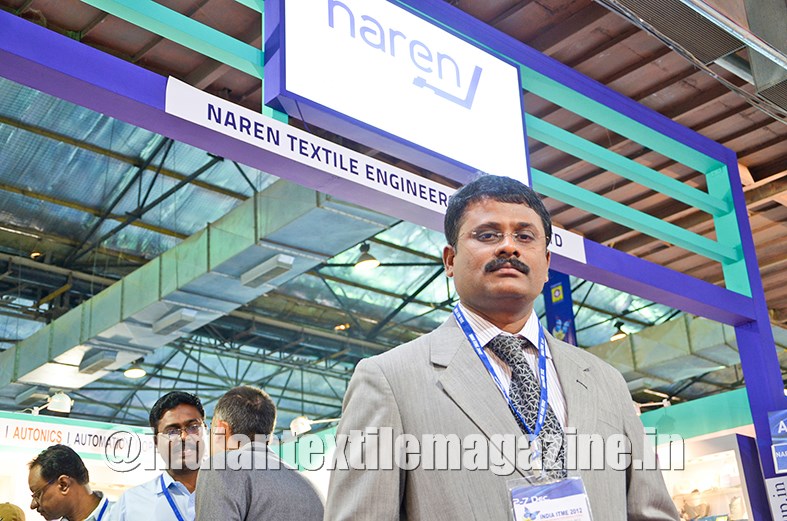
Our journey with KPR Group is almost two decades old and it has been a pleasant experience working with them. The teams across all units are very professional, well-equipped and planned. They are always on the lookout for new technologies to improve. They clearly explain their requirements and understand our difficulties as a supplier and provide us enough space to cater to their needs. We take pride as their prominent vendor of electrical and mechanical accessories for all kinds of machines from blow room to automatic cone winding machines. Their cooperation is excellent in evaluating components for new developments with proper and focussed feedback. One can experience the ease of doing business with KPR Mill provided you give good quality products and cost-effective solutions.
Their immense support and cooperation during the uncharted times of the pandemic-triggered lockdown phase has improved our relationship, going from strength to strength and it definitely has been one of the highest points in our relationship. Our experience in doing business with KPR Mill will not be complete without mentioning their responsibility on executing their commitments on commercial terms which is vital for sustainability of any enterprise and a long-standing relationship between us, built on the platforms of mutual trust and commitment. We feel content to be associated with them and wish them greater success in the journey ahead.
– R Sundarraj, Managing Director, Naren Group
—
Circular knitting machines from Mayer & Cie.
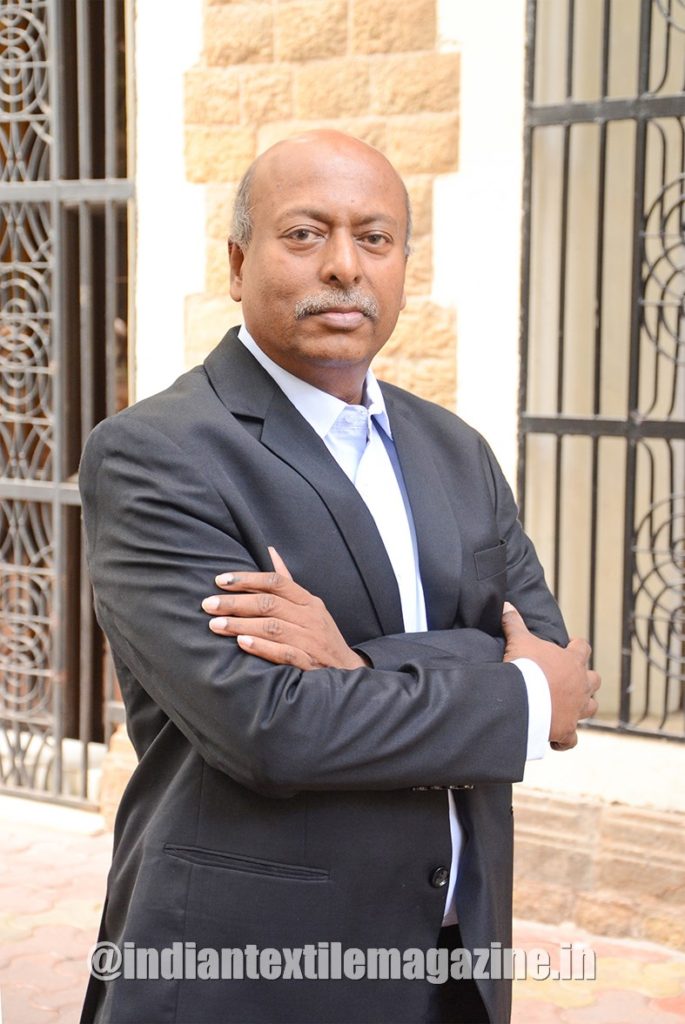
Foundation of a lasting partnership
Mayer & Cie., the German manufacturer of circular knitting machines has become a key supplier of KPR Mill Limited in Coimbatore. The Indian textile company unites spinning, knitting, processing and confecting under one company roof. With its knitting mill comprising several hundred machines, it is one of the largest entities in the area.
KPR mills and Mayer & Cie. revived an existing relationship starting in 2018. In 2019, the premium supplier and their Indian sales representation Batliboi were able to convince KPR of the benefits of Mayer & Cie.’s Relanit machines. They are the manufacturer’s signature products offering outstanding productivity and reliability with a wide range of yarn qualities. Since their market launch in 1987, the Relanit machines have remained unsurpassed in these respects.
Relative technology: gentle on the yarn
Relanit machines take their name from Mayer & Cie.’s relative technology. In contrast to conventional technology with its horizontal sinkers, relative technology knits by means of a contrary movement of needle and sinker. This movement has given the technology its name: contrary or relative technology. It is a technical refinement resulting in a gentler stitch formation process. Relative technology works with half the number of deflection points compared to conventional technology which results in considerably lower stress on the yarn.
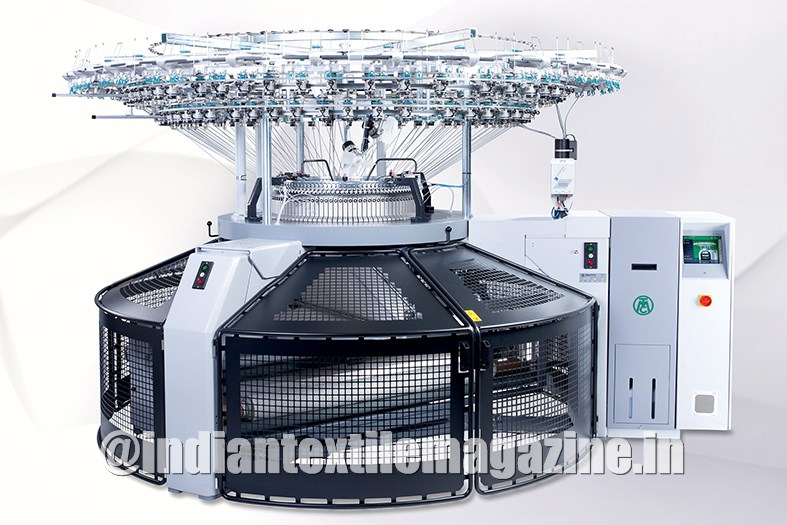
Relative technology: tangible benefits
The benefits of this technology are tangible: they include less yarn breakage and fewer machine downtimes. Even when processing inferior yarn qualities, the machines maintain their high operating speed and still deliver the desired quality. For the most recent member of the Relanit family, this fact manifests itself when working with elastomeric yarn. The Relanit 3.2 HS features extraordinary reliability and productivity in this realm.
“It were those well-known benefits that convinced KPR mills of our Relanit machines”, says Abhay Sidham, CEO of Batliboi. When extending their production facilities, KPR mills invested in a substantial number of Relanit 3.2 HS and Relanit 4.0. The latter is a league of their own in terms of productivity for cotton single jersey fabric, while the Relanit 3.2 HS is often used for knitting fabrics with elastomeric yarns.
Increased productivity pays off quickly
“KPR very quickly realised that increased productivity is far from being an end in itself”, Batliboi CEO Sidham states. “Increased productivity indeed has an impact on the entire production.” His reasoning is easy to follow: “If I can use fewer machines to produce a certain output, this means less space, less personnel, less wear and tear and less consumables. Therefore, a premium machine by Mayer & Cie. is prone to pay off very quickly.”
—
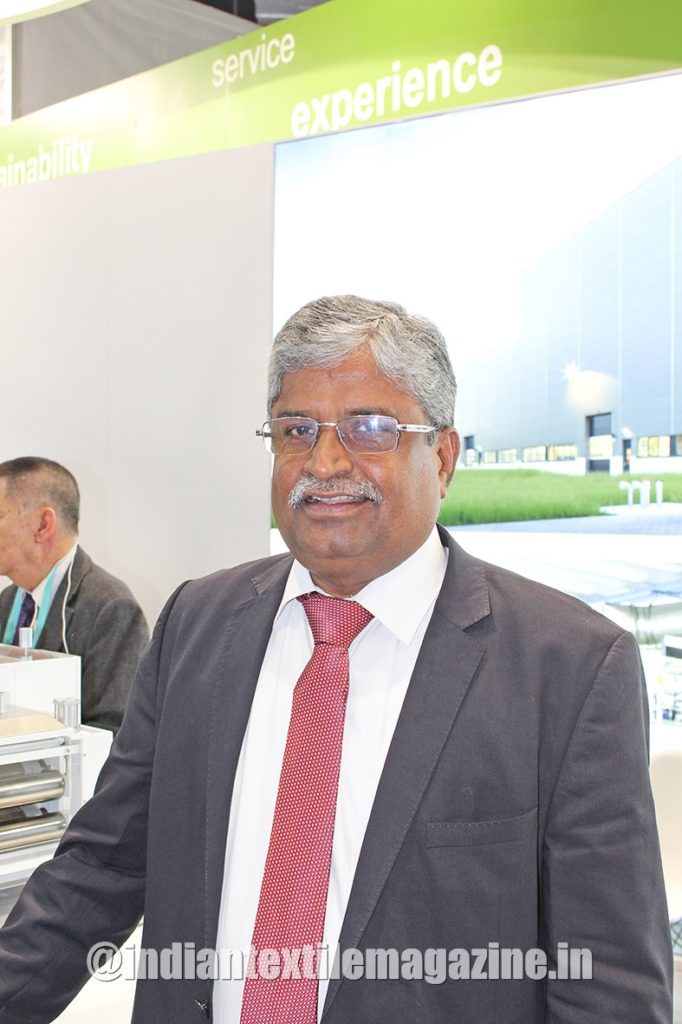
Voltas strong partnership with KPR Mill
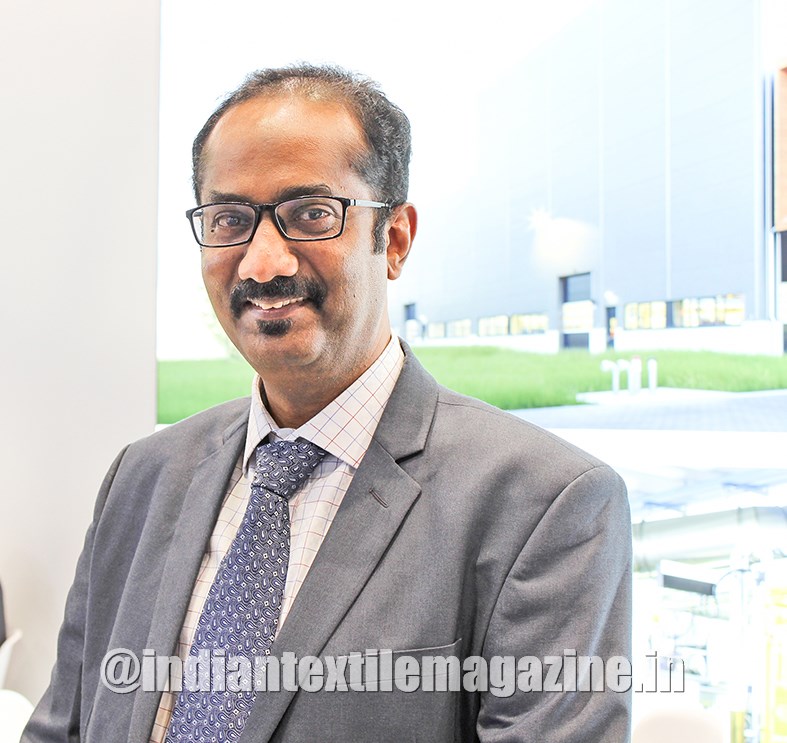
KPR Mill is a reputed and progressive organisation in the textile industry with its focus spanning across yarn, fabrics and garments. FASO is a leading brand of KPR Mill through which the group has also forayed into the retail space and created brand identity. Voltas TMD has always been a trustworthy business partner in the textile industry and our long-lasting association with KPR Group stands testimony to this fact. Our focus is on continuously enhancing this relationship not only by offering the right products and solutions but also by providing end-to-end service support throughout the lifecycle of the products. Voltas TMD has been a preferred partner to KPR Group since inception for capital machinery as well as after-sales products. The details given below are some of the examples where we have been a valued partner to the KPR Group for the past two decades.
—
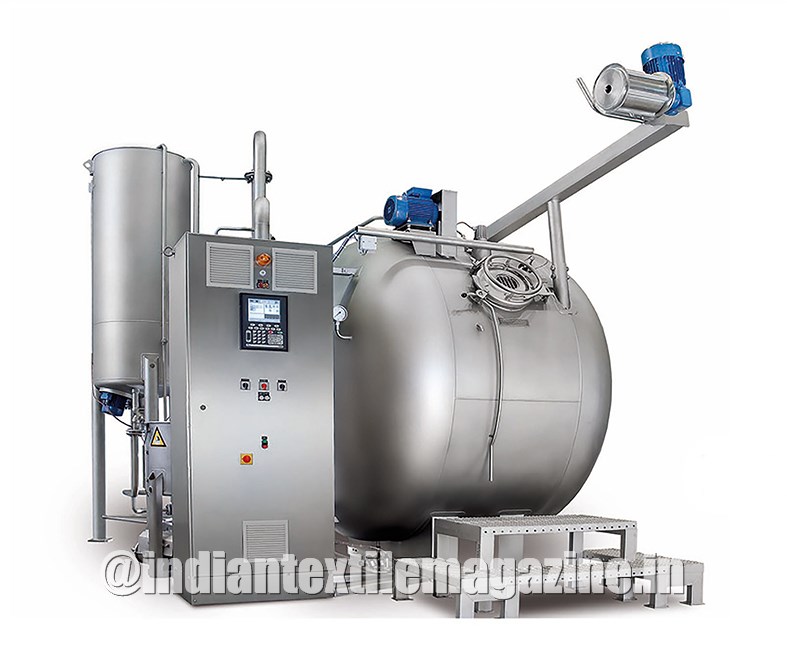
Fabric Dyeing Machine from Thies: We are privileged to be a partner to KPR Group in their dyeing project with a capacity of more than 30 tons per day by supplying a set of 10 Ecomaster machines with automatic dispensing MPS units from our principals, Thies of Germany. Subsequently we had also supplied a further set of two Minisoft machines in the year 2018. Excellent dyeing results with high reproducibility are continuously achieved in these machines for almost every type of fabric by KPR Group. Thies GmbH, Germany is a global leader in soft flow dyeing machines.
The current range of iMaster dyeing machines have a series of unique value propositions which include dyeing quality, consistency, repeatability, low liquor consumption and high level of user-friendliness. Exceptionally reliable fabric transport is guaranteed by innovative features, including internal winch, nozzle and plaiter delivery pipe in one unit and a two-dimensional adjustable fabric chamber. The amount of free liquor in the machine is reduced to a minimum, improving water consumption.
—
Finishing Machine from Brueckner: We are also privileged to be chosen by KPR Group for their finishing project through the finishing machines from our principals, Brueckner of Germany. Initially, we supplied one six-chamber and one eight-chamber stenters. Delighted with the performance of the machine, KPR Group favoured us for the supply of four more stenters, which were supplied in 2016. Brueckner has always been a preferred supplier of KPR Group when it comes to finishing and it demonstrates the confidence bestowed on our relationship and our deliverables.
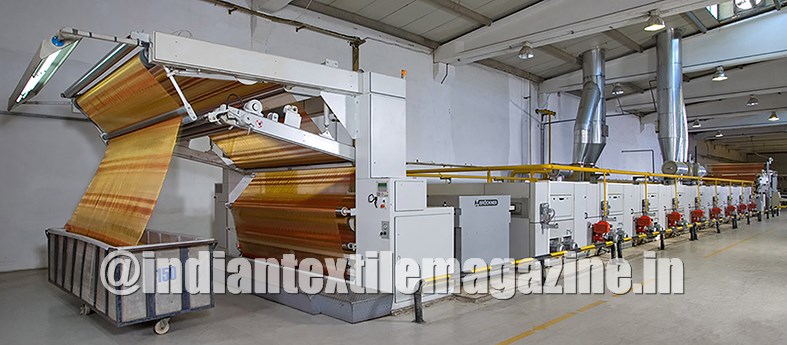
The stenter is the heart of textile finishing. It develops more and more into a multi-purpose line for the production of technical textiles and other web-shaped materials. Several thousands of Brueckner stenters are in use all around the globe. Every day they are stentering, drying, heat-setting, functionalising and coating uncountable metres of the most different fabric types. Since many decades Brueckner stenters stand for highest quality and performance and ensure production with sustainability and energy-efficiency.
—
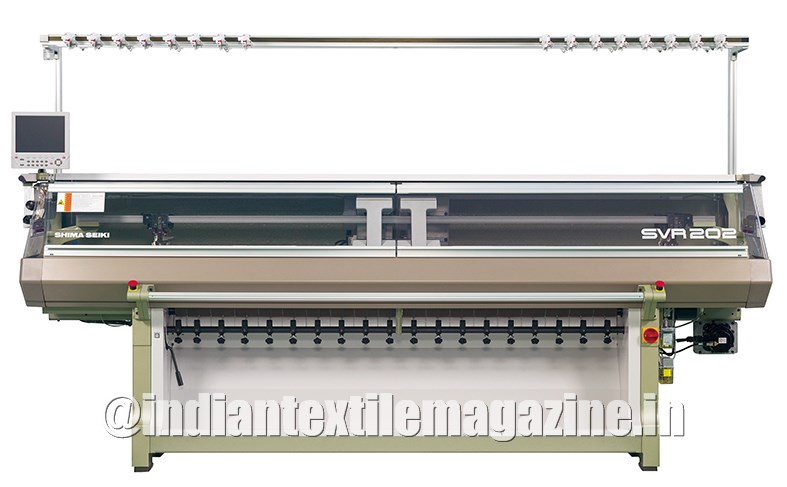
Flat Knitting Machine from Shima Seiki: Our partnership with KPR Group got strengthened further by participating in their project for making flat-knitted fabrics. We were favoured for the supply of 20 SVR202® flat-knitting machines from our principals, Shima Seiki of Japan. By using this high-class latest technology in flat-knitting, KPR Mill is in a position to deliver the best-in-class finer garments to its buyers. SVR202 supports a variety of production needs with its wide 80-inch knitting width and tandem knitting capability. High productivity is achieved with a maximum knitting speed of 1.4 metres per second and the R2CARRIAGE® system that permits quicker carriage returns.
It also carries over established Shima Seiki technology such as the renowned digital stitch control system (DSCS®), spring-loaded full-time sinker system and stitch presser. Proven technology along with ‘Made in Japan’ quality, reliability, productivity, user-friendliness and cost-performance all combine to satisfy the high expectations of the world’s fashion industry.
—
Apart from capital machinery arena, we have also been serving KPR Group for a range of after-sales products including: a) ring travellers from our principals, Lakshmi Ring Travellers, b) card clothing from our principals, Lakshmi Card ClothinG, and c) speciality lubricants from our principals, Klueber Lubrication India Ltd.
—
“We value KPR team’s feedback”
– Senthil Raja, JMD, MEC Growths Texmach P Ltd
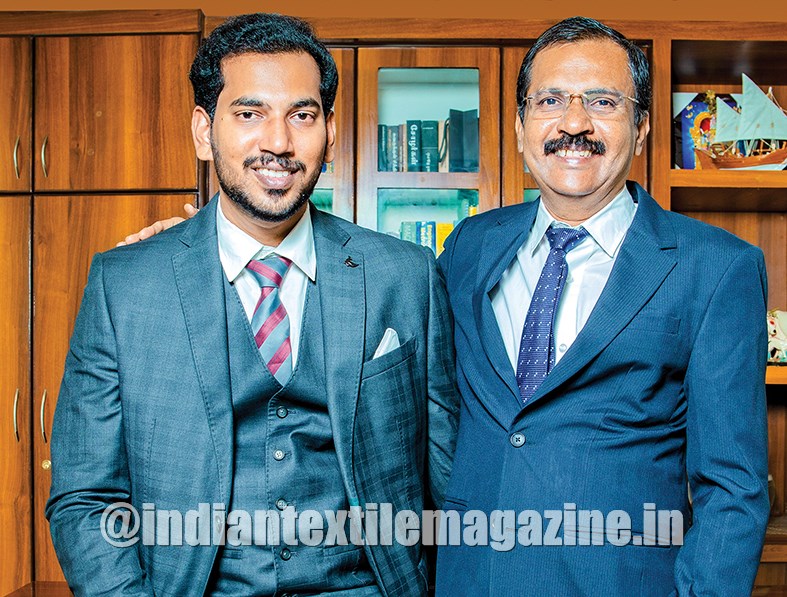
KPR is amongst the most discerning clients that you can meet. The company has set exceedingly high standards in performance, quality, service and the entire vendor selection process. Once you meet their requirement, best rest assured of a long and mutually enriching association.
At MEC Growth, when our initial top arm trial was successful, it all looked so easy. But subsequently we realized that we had taken only the baby steps towards climbing Mount Everest! After the initial trial, then started the product analysis, technical clarifications, price negotiation, etc.
Though we supply to other OEMs, it is only KPR that has thrown light on our product. We value KPR team’s feedback, which can help further improvements on our product. This has boosted our confidence level to promote our product fearlessly throughout the world.
We started with two machines in October 2018, with the KPR Group, which further went to 0.2million spindle top arms by the beginning of 2019. We received another order in 2020. We can now say that our product is perfectly alright. Thanks to the entire KPR team and management for such fabulous support and advice. We truly cherish this relationship.
—
SETEX software to handle manufacturing performance.
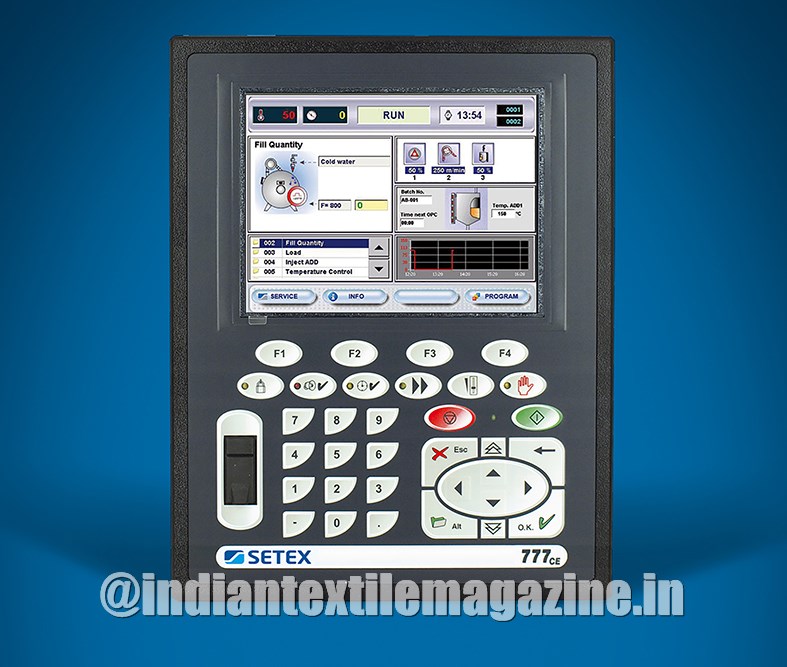
To be sustainable, a textile production facility project typically demands a high level of both excitement and interest from all parties. For the automation part of the dyeing department, SETEX was involved in the turnkey project from the start in 2008 as a technology partner of the machine supplier THIES.
While the majority of textile finishing mills increased the efficiency of systems in small steps with embedded software in controllers, for KPR Mill it was about the whole factory. The OrgaTEX MES software is linking therefore operational and information technology by integrating multiple machines on a single platform.
With the goal of production excellence, KPR Mill wanted to use less chemicals and colorants from the start and run optimized dyeing cycles with the best possible “right first time”.
This was achieved with the synergistic effects of:
– Machine controllers with identical user interface and intelligent processing
– “Look ahead” functions for integration of dissolving and dosing systems to achieve the most efficient possible utilization and precisely fitting injection on the dye-machine process-step.
– Combining the recipe and process management information in a software module with dynamic optimization of standard treatments.
This system provides the relevant information on production order cost, consumption, and energy, including performance KPIs to make the manufacturing smart, streamlined and efficient.
Regular on-site inspections with equipment or software upgrades make KPR Mill´s focus on customer satisfaction intricately connected to the requirements for the systems up-to-date status, high availability, and fail-safe operation possible. With full commitment from the customer´s staff and being always on the most recent software version, KPR Mill gains more meaningful information from the increasing flood of data in order to get even more out of the production and conserve important knowhow all at the same time.